Author: Inspector. Jose Lopez. 02 September 2023.
Introduction
Gas desulfurization is a fundamental process in the control of sulfur emissions from industrial processes, power generation, and transportation. Significant emissions of sulfur dioxide (SO 2 ) lead to the formation of acid rain, deterioration of air quality and adverse effects on human health.
Strict compliance with environmental regulations is essential to reduce polluting emissions and to minimize the associated environmental impact. The flue gas desulfurization (FGD) plant process uses a suite of technologies to remove sulfur dioxide (SO 2 ) from flue gas emissions from coal-fired power plants.
Flue gas desulfurization systems were developed in response to flue gases from fossil fuel power plants, primarily coal-fired, which posed a hazard to both the environment and human health.
S0 2 can be removed from flue gases by various methods. In the case of a typical coal-fired power plant, Flue Gas Desulfurization (FGD) systems, or scrubber systems, remove approximately 95% of SO 2 from flue gases.
Technological strategies for gas desulfurization
These strategies are designed to mitigate sulfur emissions from industrial processes and power generation, aligning with rigorous environmental standards. Here, we will discuss how various technology strategies for gas desulfurization address regulatory challenges and contribute to regulatory compliance.
Wet Scrubbing: The technique involves conducting exhaust gases through a liquid solution, typically an alkaline slurry. The liquid selectively absorbs the sulfur compounds present, resulting in a noticeable reduction in sulfur dioxide (SO2) emissions. Wet scrubbing systems are especially effective in large-scale industrial applications, although they require the use of water and generate liquid by-products.
Dry Cleaning: The method is based on the use of dry sorbents, such as limestone or hydrated lime, to react with the sulfur compounds present in the exhaust gases. This chemical interaction allows the capture of sulfur and the consequent reduction of SO 2 emissions. Unlike wet cleaning, dry cleaning creates solid waste rather than liquid by-products.
Fluidized Bed Combustion: The technique involves burning sulfur-rich fuels in a bed of inert material in a fluid state. During the combustion process, sulfur compounds are captured and retained in the bed material, leading to a significant reduction in SO 2 emissions.
Catalytic Conversion : It is based on the use of catalysts to facilitate chemical reactions between the sulfur compounds present in the exhaust gases and the conversion agents.
The presence of catalysts favors the transformation of sulfur compounds into forms that are less harmful to the environment. The high temperature facilitates the reaction between the sorbent and sulfur compounds, resulting in the formation of solid by-products that can be captured by particulate control devices.
A sorbent is a material that has the ability to adsorb or absorb substances from gases, liquids, or solutions. The term “sorbent” is a general term that encompasses both adsorbents and absorbents, although they have slightly different mechanisms.
FGD flue gas desulfurization processes
The FGD process is designed to absorb sulfur dioxide from flue gases before it is released. This is achieved by a wet or dry process.
dry FGD
In the process of dry cleaning injection systems (Figure 1), lime is used as a reagent to react and remove gaseous contaminants. There are two common dry methods, the dry injection system and the spray drying systems. Each process injects lime into the flue gases to remove SO 2 . A dry injection process injects dry hydrated lime directly into the flue gas duct, while the spray drying system injects atomized milk of lime into a separate vessel. Both methods produce a dry end product, which is collected in particle control devices for further treatment.
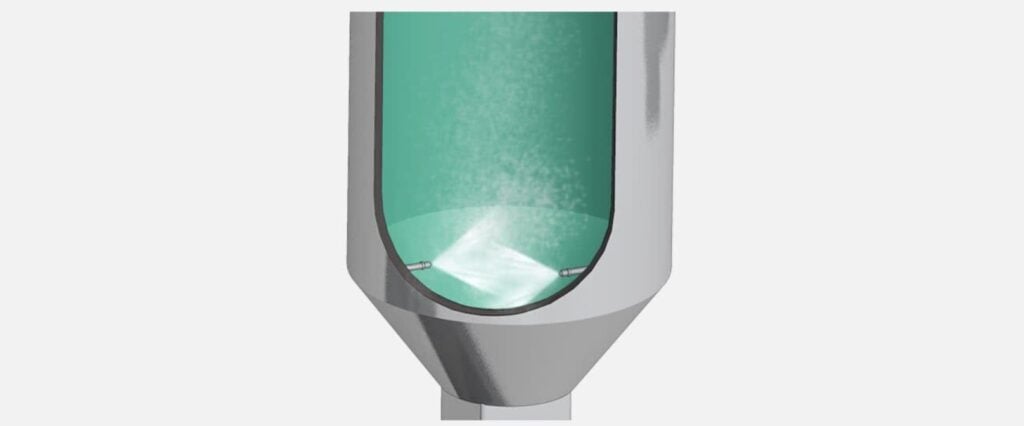
wet FGD
The wet scrubbing process (Figure 2), typically uses an alkali-based milk of lime to scrub the gases. A shower of lime milk is then sprayed into a flue gas scrubber, where the SO2 is absorbed in the spray and converted to a wet calcium sulphite. A byproduct of that sulfite is that it can be made into marketable plaster. Wet scrubbing provides highly efficient sulfur dioxide removal capability, as well as reducing any scaling potential.
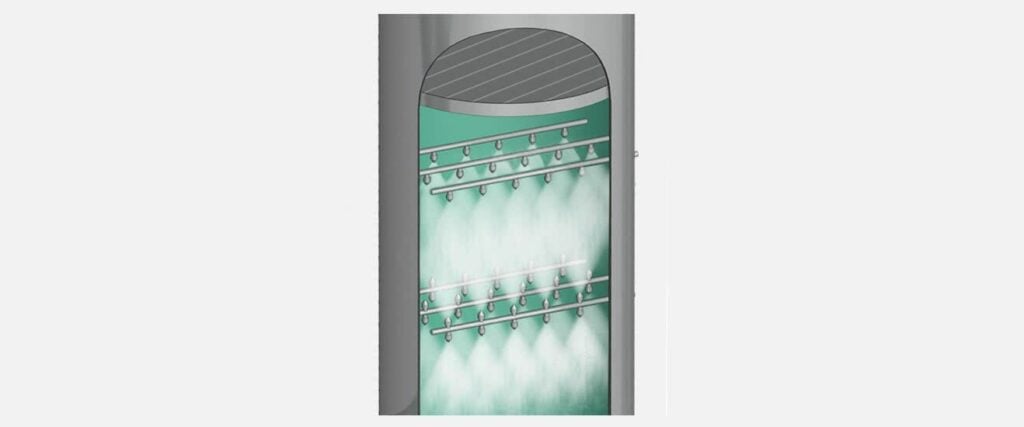
Reduced Acid Rain Formation
Acid rain is a significant environmental concern caused by sulfur dioxide emissions that react with atmospheric moisture. Gas desulfurization aims to minimize these emissions and, subsequently, reduce the formation of acid rain.
The combustion of fossil fuels to power manufacturing and refining facilities occurs in a wide range of industrial sectors.
Hydrocarbon plants feed chemical and petroleum refineries, as well as facilities that produce cement, paper, glass, steel, iron, copper, and other metals.
The SO 2 gases emitted as a result of these processes are a major contributor to acid rain and have long been regulated by every industrialized nation in the world due to their harmful effects on human health and the environment.
Facing the challenges dictated by regulations
Technological tactics offer the means to achieve and maintain compliance with emission limits. Industries can select the most appropriate method based on specific emission requirements outlined in regulatory standards, avoiding penalties, legal action and operational disruptions due to non-compliance.
In this context, the industries that allocate resources to research and development with the aim of improving their criteria for gas desulfurization demonstrate a solid commitment in terms of complying with and exceeding established regulatory requirements. This approach reflects a mindset oriented towards excellence and the constant search for advanced solutions for the control of sulfur emissions.
As regulations continue to evolve and become increasingly stringent, industries find themselves in need of constant innovation in their gas desulfurization technologies. This process involves the continuous improvement of the efficiency of existing methods, the exploration of new techniques and the development of advanced monitoring systems.
Sulfur emissions play a significant role in the formation of particulates and in the degradation of air quality.
By implementing gas desulfurization methods, it is possible to achieve an effective reduction of sulfur compounds, which leads to a substantial improvement in air quality and a reduction in the associated risk to public health.
In this way, it seeks to mitigate the negative effects derived from these emissions, promoting a healthier and more sustainable environment.
The Effluent Limitation Guidelines (ELG) regulate wastewater discharges from Coal Power Plants and Combined Cycle Power Plants (IGCC). They are used in control systems for atmospheric pollution by combustion gases or in solid waste handling systems.
Environmental impacts
Using scrubbers to clean flue gases before they leave the stacks has a drastic and beneficial impact on the environment. By collecting particles and acid gases, the amount of different pollutants that can leave industrial plants and contaminate the environment is drastically reduced, which increases air quality and reduces the health risks of people who could come into contact with it. with different contaminants.
The implementation of advanced technologies in the desulphurization of gases in industrial plants has acquired a fundamental importance to address regulatory challenges and contribute significantly to the mitigation of industrial air pollution.
The application of this knowledge, based on advanced catalytic hydrodesulfurization and sulfur capture, allows an efficient reduction of sulfur levels in petroleum products, thus ensuring compliance with environmental regulations.
The key to the success of these applied sciences lies in the convergence of various technological advances, such as the incorporation of real-time monitoring systems powered by artificial intelligence and machine learning. These systems improve operational efficiency and ensure consistent regulatory compliance, adapting to changing environmental regulations and standards.
Conclusions
In a global context where sulfur emission limits continue to decrease, it is essential to continue researching and developing cutting-edge solutions that are economically viable and environmentally friendly. Adaptability and technological innovation are crucial to achieving a cleaner and more sustainable oil industry.
In summary, gas desulfurization technology strategies have shown that innovation and cutting-edge engineering play an important role in preserving air quality, human health, and protecting the environment.
References
https://www.routledge.com/Handbook-of-Refinery-Desulfurization
https://www.metso.com/metals-refining/solutions/gas-cleaning