Table of Contents
- Summary
- Situation Analysis .
- From the point of view of the operation - production
- From the point of view of process control .
- From the point of view of reliability and maintenance
- What do operational integrity windows pose?
- Operating conditions – Not considered in the operational routine
- Boiler hearth walls
- Overheater Manifolds
- Discussion and Conclusions
- References
Summary
This article considers the convenience of identifying the variables, operating limits, which must be established to permanently monitor and control the operational conditions, efficiency and integrity – reliability of process equipment, which in this case will focus on boilers. . Managing this under the methodology of Operational Integrity Windows (IOW) according to the Recommended Practice of API 584. The IOWs allow correct and immediate corrective actions to be generated, during the operation of boilers in real time, in line with the trend of moving towards an Industry 4.0, to optimize operational safety and efficiency, in addition to identifying the conditions that promote the generation of Probable and credible damage mechanisms in each component of the boiler, with the consequent loss of reliability in case of not controlling the process sufficiently and in a timely manner. Under this methodology, immediate corrective measures can and should be taken and fed day by day to the next Inspection and Maintenance Plan in the short and medium term of the boiler.
Situation Analysis .
From the point of view of the operation – production
In the Chemical and Process Industry, one of the main plant services is steam. A lack of steam supply, due to boiler failures, implies unplanned shutdowns and production losses. From the point of view of the operation, the operators typically attend as the most important parameters the control of the flow, pressure and temperature of the steam product, flow of the feed water, flow of fuel, that the water level is within a specified range. To prevent the boiler from going offline and with a certain frequency, chemical analyzes are made of the feed water and the boiler.
To maintain the required load to the boiler by the process, fuel combustion is increased without the operator in most cases analyzing possible imbalances in the temperatures of the various steps of the combustion gases, the inlet and outlet of water and/or steam by the exchange components of the boiler (superheaters, superheaters, tube banks, economizers), and even of the metallic elements of the main components of the boiler.
During normal operating conditions and out-of-control events (contingencies or out of critical operating limits), even knowing what is happening, in order to meet the steam requirements of the process, rarely is a comparative analysis with the original design conditions and the possible effect on the promotion and generation of probable and credible damage mechanisms in each component of the boiler. Although the values of the parameters are being observed and recorded under these conditions, this “condition monitoring in real time” does not always imply taking correct and immediate corrective actions to sufficiently and timely control these operating limits, because the required steam comes first. per plant.
From the point of view of the field operation, it is observed that the verification of the combustion conditions and if the flame hits the walls or ceiling of the hearth, is not part of the operator’s routine or it is not possible to verify for the closing of the inspection windows. Burner adjustment skills are not often found among boiler operators or maintainers. These are all conditions that can be observed during inspections.
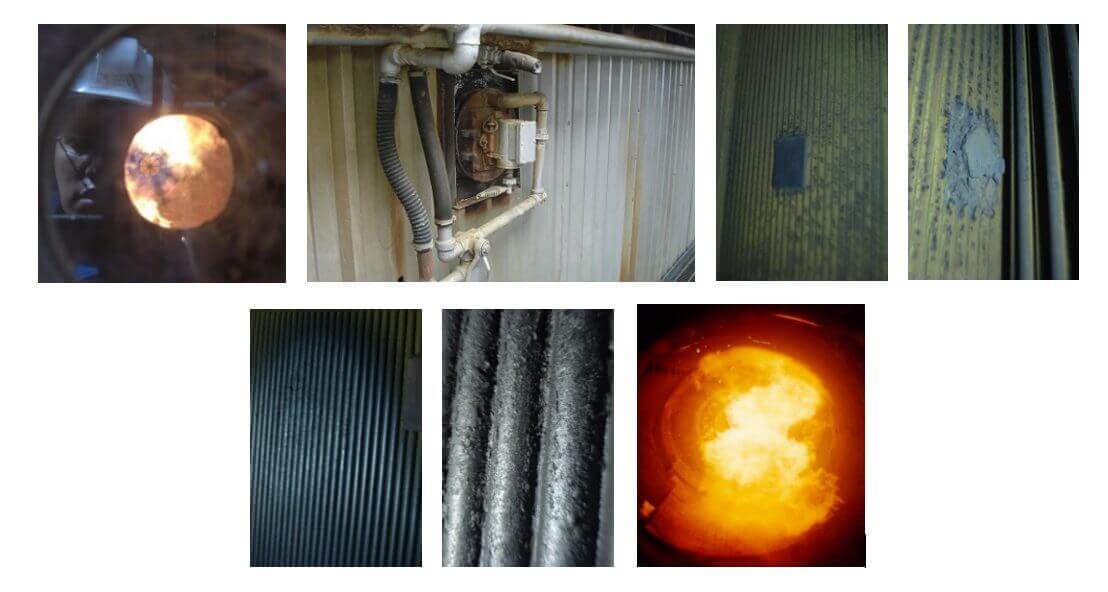
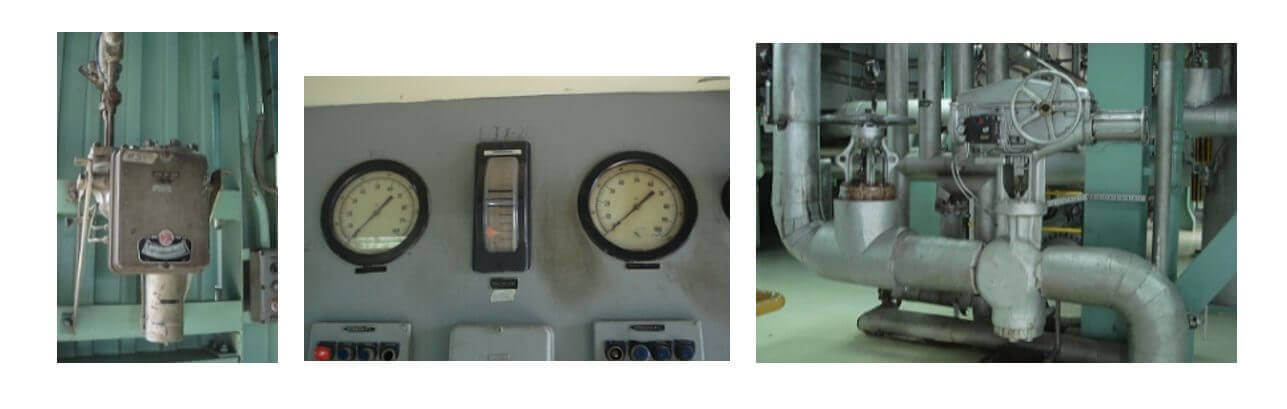
From the point of view of process control .
At the level of the boiler control and safety system, resources are available on the market that allow permanent monitoring of variations in parameters, which are established as operating limits and operating conditions, for, in real time, , in order to effectively and timely govern the efficiency and safety, as well as the integrity-reliability of the boilers (2).
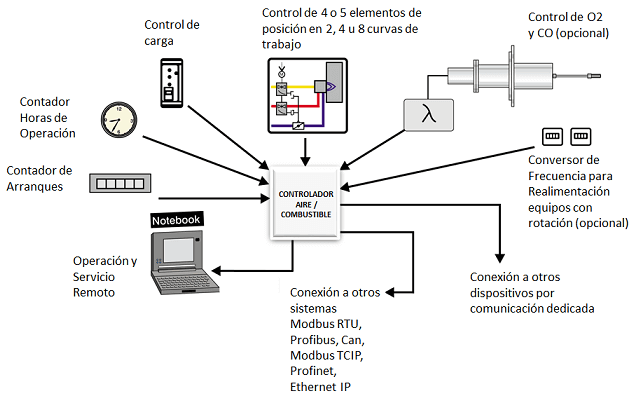
With what could be aspired to take the operation of the boilers to what is considered today within the new trends of Industry 4.0 (3).
However, there are facilities in which, despite having updated instrumentation and control systems in their production process, the boilers remain equipped with their original long-standing control systems, with little maintenance and sometimes without complying with the minimum preventive maintenance and calibrations suggested in the manufacturer’s O&M manual and international boiler care standards.

From the point of view of reliability and maintenance
Even in facilities where the proactive or reliability-centered maintenance (RCM) methodology is used for dynamic or rotating equipment (Turbine, Fans and Pumps), where there are control systems that monitor the parameters within the operating limits and manage to anticipate and prevent failures of this equipment, the “control” parameters of the boilers are limited to what is indicated above and their inspection and maintenance plans are usually Reactive (corrective), limited to what is required by the local regulation where the boiler is installed, in In exceptional cases, the inspection is extended to the measurement of the thickness of the tubes of the different components of the boilers, with which wear due to erosion and/or corrosion is being assumed as the only evaluation criterion, without considering possible mechanisms of mechanical damage. such as fatigue and/or thermal aging, which normally do not show thickness loss. It is often observed that supplemental inspections and maintenance or repairs are planned based, above all, on the components in which recent and recurrent failures have occurred. In the best of cases, there are facilities in which the Risk-Based Inspection (RBI) methodology is also applied to their boilers.
In facilities where Boiler Inspection Plans are developed based on the analysis of their conditions and care, there is normally no continuous feeding of the information required to establish the Risk-Based Inspection Plans (RBI) or Risk Assessment. Condition (Condition Assessment), as proposed by the Recommended Practice of API 584 “Operational Integrity Windows” (IOW), leaving this as an information retrieval and processing job at the end of the production period (annually or more).
From the point of view of maintenance, these tend to follow a routine (daily, weekly, monthly and yearly) raised by checklists of certain codes or standards and/or the manufacturer’s manual (Maintenance Checks), which tend to move in time due to production commitments, lack of resources or other priorities. Operations personnel are usually consulted about obvious defects or damages that affect the normal operation of the boilers, which in plant terms translates into conditions that limit reaching the maximum steam production required for the process. Included within the scope of maintenance are the activities that were pending in previous shutdowns, either due to insufficient time or due to not having the necessary resources to carry them out.
What do operational integrity windows pose?
To operate the boilers at their maximum reliability, a set of operating ranges and limits must be established for the key variables of the steam generation process, to ensure what is expected from the point of view of steam specifications, in an efficient, safe operation. and reliability-integrity, etc.
Integrity Operational Windows (IOWs) are a specific subset of these key operating limits that need to be established and implemented and that focus on maintaining the integrity or reliability of process equipment.
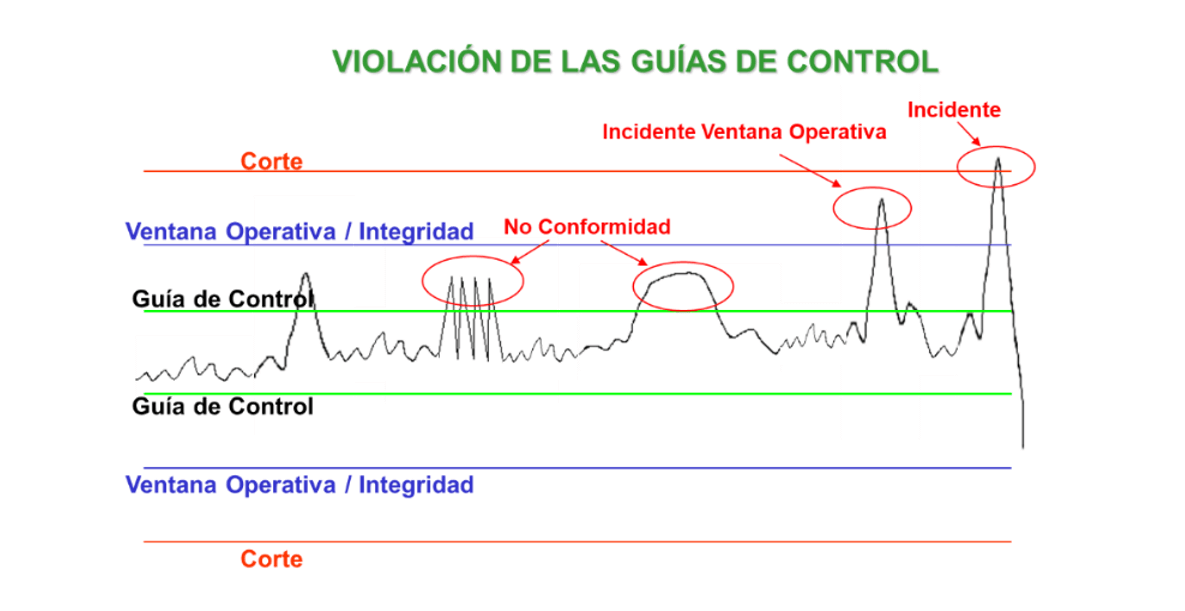
In general, when irregular trends are not monitored or controlled in a timely and effective manner, nor are irregular trends analyzed and corrected, the probability and rates of occurrence and acceleration of damage mechanisms may be promoted and, as a result, “unforeseen” failures for the system. boiler case in this article.
Operation within preset limits should result in predictable and reasonably low degradation rates.
For the case shown below, the level fluctuations, which should have been considered “Non-Conformities ”, even if they had not reached alarm values and/or boiler trips, they should have been considered by those responsible for the operation, as a condition that affects the proper circulation of water inside the boiler and relate this to potential damage mechanisms.
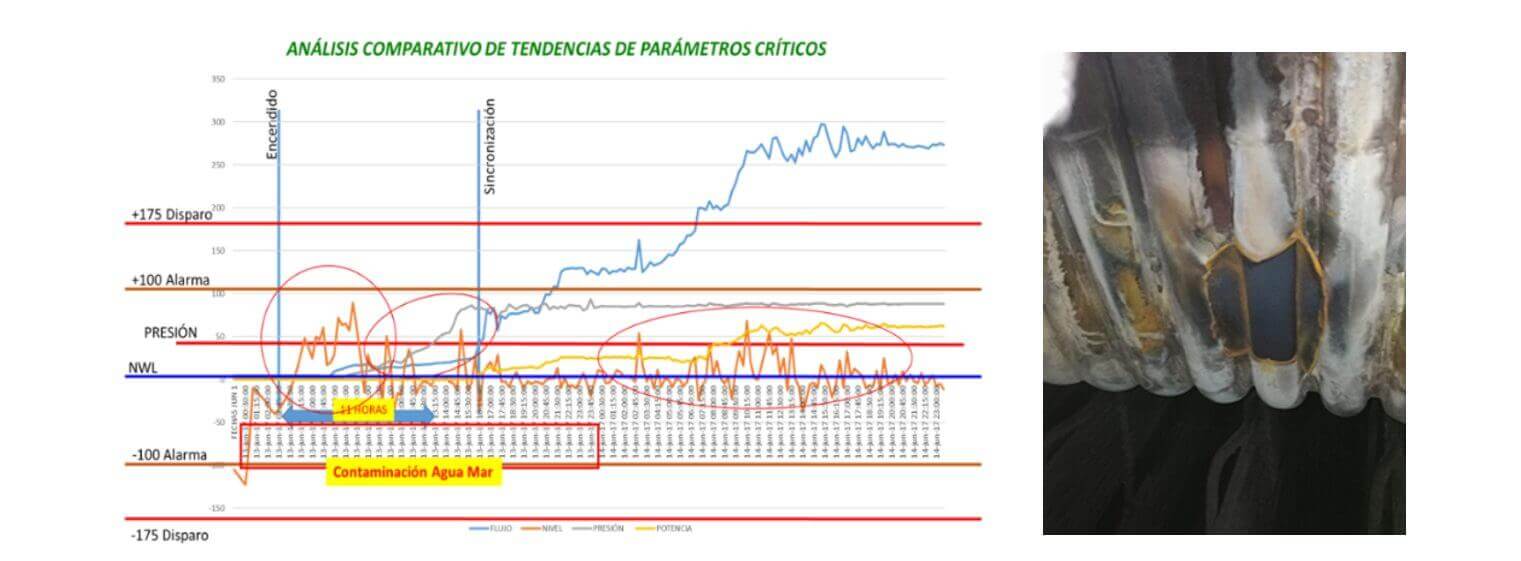
According to the methodology of the “Operational Integrity Windows” (IOW – Recommended Practice of API 584), Real Time Monitoring – Permanent of the Critical Operating Limit Parameters must be carried out, by a well-trained operator to take timely and correct corrective actions, in order to optimize safety and efficiency, in addition to understanding and identifying the conditions that promote the generation of probable and credible damage mechanisms in each component of the boiler, with the consequent loss of reliability if these operating limits are not sufficiently controlled.
In addition, this information – correlated with credible damage mechanisms should constantly feed what has to be the Risk-Based Inspection Plan or Condition Assessment. (Condition Assessment) of the boiler at the next planned shutdown, without waiting to retrieve said information at the end of the operational period.
The result of the planned and executed inspections based on the operational condition of the boilers will feed a Reliability Centered Maintenance Plan for the short and medium term.
Operating conditions – Not considered in the operational routine
Effect of operating conditions on integrity and reliability
Availability and use of temperature measurements
Boilers that could be under a condition of operational cycles, due to requirements of the electrical network for boilers in the cogeneration area or due to work shifts or production plans in the Chemical and Process industry; by the use of fuels out of specification, which could produce irregularities in the combustion conditions, thermal balances in relation to the design conditions; In addition to damage due to corrosion and erosion, the boilers enter into conditions that favor the preferential development of damage mechanisms such as mechanical and/or thermal fatigue, aging or thermal degradation of different types. These conditions are not always prevented and become a problem of loss of reliability, availability and even security.
In the normal and/or routine operation of boilers, the operators basically keep track of the parameters indicated above based on the requirements of the process, although in many cases there are temperature measurements of both fluids (gases, water and/or steam) in several of its steps, such as the skin of tubes and/or essential components, which provide information on irregular operating conditions.
If these temperatures were used in real time and analyzed, it would be possible to correct trends and irregular operating conditions, maintain optimal efficiency, ensure reliability, prevent degradation and/or unexpected failures with unscheduled stops, meet the life expectancy of the various boiler components and even optimize its safety.
The monitoring of temperatures of the fluids (combustion gases, water or steam) and of the metals of the components, at the different loads or operational conditions of the boiler, following what is indicated by the manufacturer’s operation and maintenance manual, can and should be correlated with the evolution of specific damage mechanisms in particular components, examples of this:
Economizer:
- Temperature differential greater than 93°C between the feed water at the inlet and the combustion gases at the outlet of the economizer, can encourage the generation of thermal fatigue, especially if the inlet collector is located within the passage of the gases;
- Low temperatures of the feed water, at the economizer inlet, which condense acids carried by the combustion gases;
Upper dome: The temperature differential between its upper and lower part, or between one side and the other, during the start-up (heating) and shutdown (cooling) processes, could lead to differential stresses and the generation of fatigue cracking or pitting alignment. by oxygen or CO2 in the lines of stress.
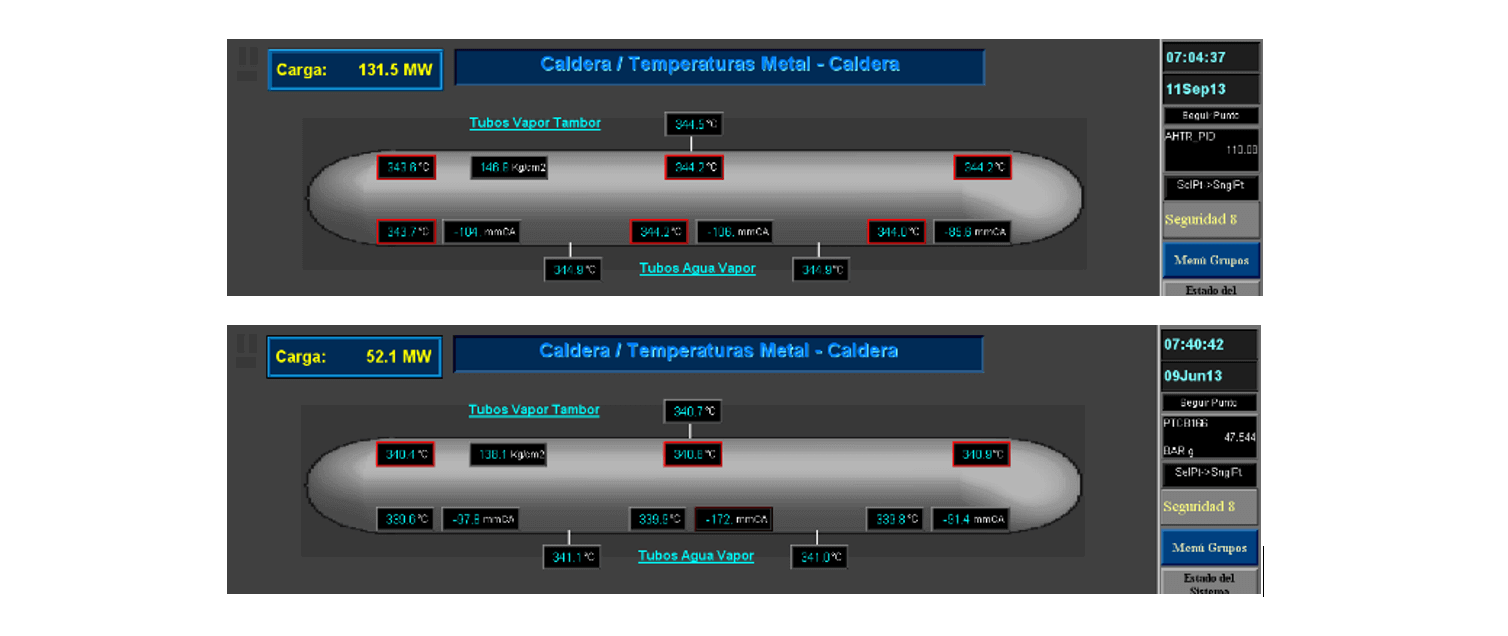
Boiler hearth walls
- Exposure of household tube metals, normally low carbon content steels, to temperatures above those considered maximum – according to ASME manufacturing code 1,000°F (538°C), can accelerate the aging of tubes due to thermal creep slow or creep, but also:
- Localized drying (steam blanketing) and embedding of dissolved and suspended solids, increases in concentration and attacks by caustic corrosion.
- When the boiler operates at pressures above 1000 psi, it can be susceptible to hydrogen damage under a number of conditions.
This temperature monitoring is very useful and important to identify the most critical areas of the boiler hearth and emphasize the evaluations at the time of inspection. These tube skin temperature measurement points in the home can be factory installed or can be installed by the user of the boiler.
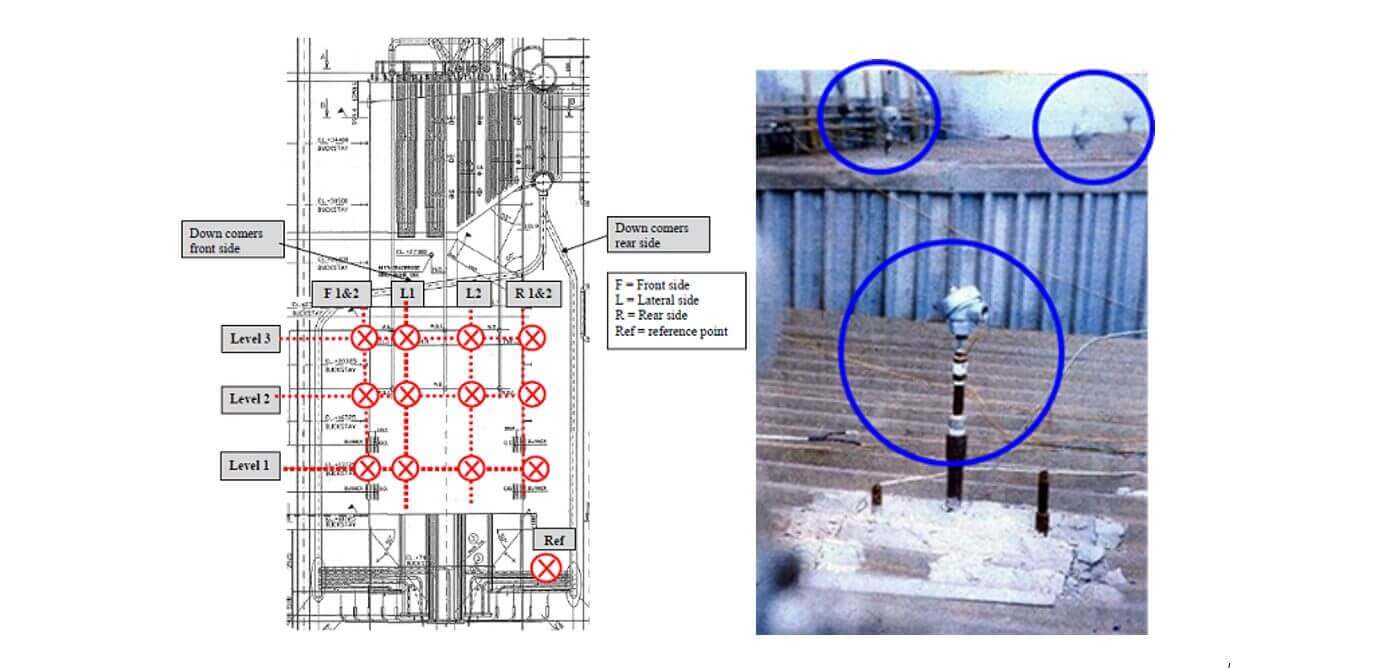
If the thermocouples that are installed on the walls of the furnace are of the Chordal type, it will be possible to monitor the evolution of the limit temperatures of oxidation and creep of the tube material and make decisions such as the right time to plan a chemical cleaning.
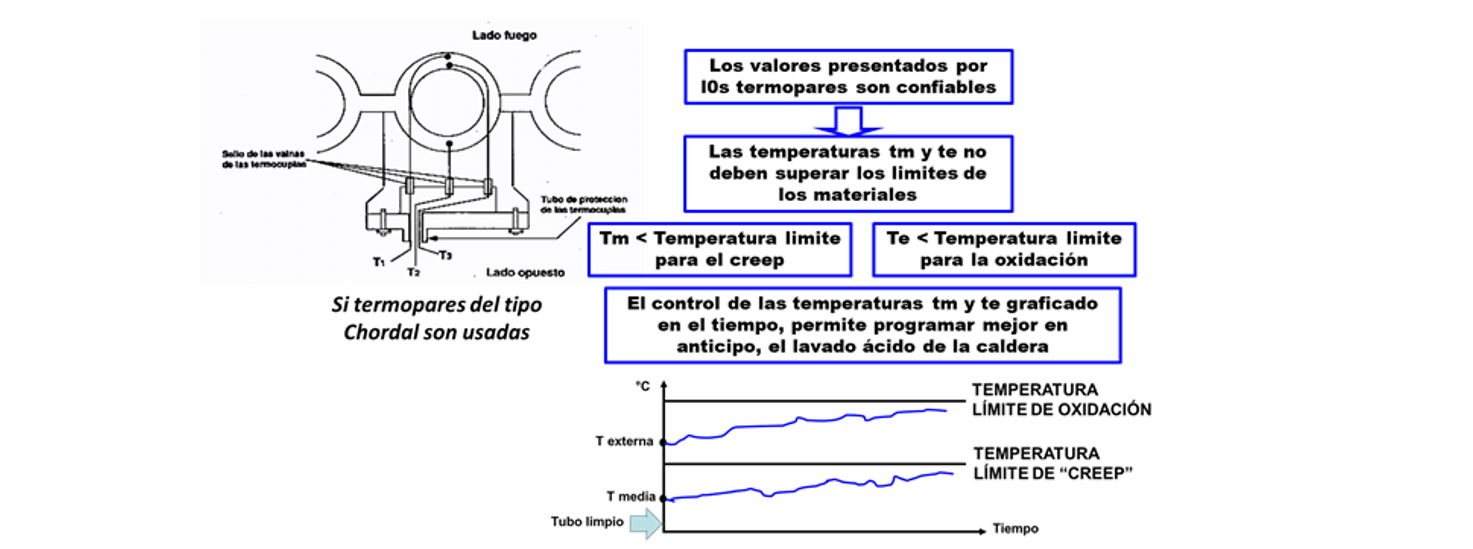
Overheater Manifolds
Although they are located in chambers isolated from the passage of combustion gases, the ingress of gases and exceeding the maximum temperatures of the materials of these collectors can accelerate the aging of the tubes due to creep.
Secondary Superheater Vapor Outlet Manifold Differences in temperature between the right and left sides of the superheated steam outlet collector – product steam, can generate problems of dilation differences and thermal fatigue in the joints between the collector and the tubes.
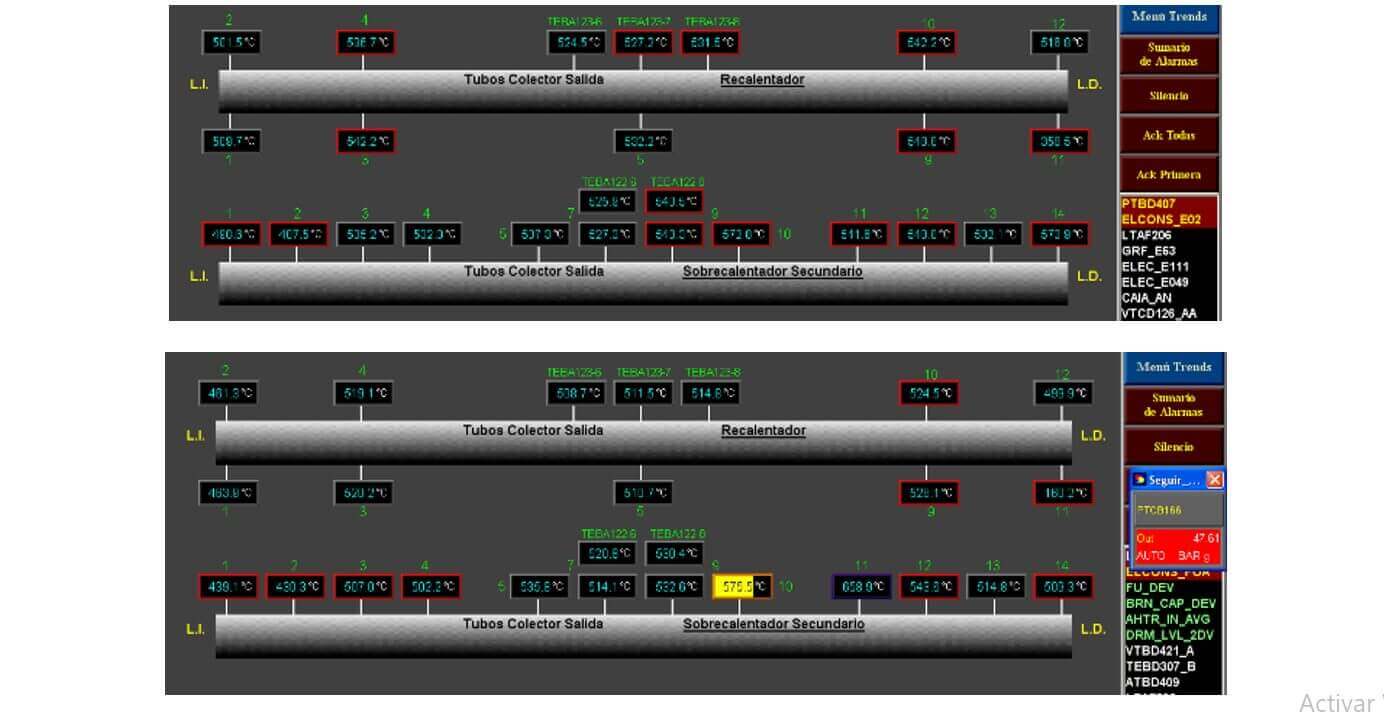
Overheater Tubes
- Whose materials can range from carbon steels (maximum temperature 1,000°F (538°C)), through steels with low alloys (maximum temperatures between 1,000°F (538°C) and 1,200°F (649°C)) that in If these temperatures are equal to or exceeded, it can accelerate the aging of the tubes due to creep.
- In the case of stainless steels (maximum temperatures in the order of 1,500°F (816°C)), if the operating temperatures exceed these maximum temperatures, the aging process can be accelerated by Sensitization.
IOW and reliability
Carrying out an Inspection Plan using the RBI methodology (API-ASME) or Condition Assessment (EPRI) is definitely a very convenient option, since depending on its operating times, conditions and operational regimes, they are generated and evolve. a certain variety of damage mechanisms, which are not usually evident upon visual inspection. By analyzing design details of the boiler and its components, possible modifications with respect to the original design, and by gathering the necessary historical information on inspections, failures, repairs, replacements, maintenance, chemical control and operating parameters that the operator typically does not attend to among its common parameters of “control” in boilers, it will be possible to identify the credible damage mechanisms for each component, establish the appropriate test methods to identify them and define the inspection plan by a multidisciplinary work group.
In addition to the excellent results obtained under the RBI and/or Condition Assessment methodology, it is possible with the information on the changing conditions of the operation, once the operating limits have been established for the key variables of the steam production, feed the Inspection Plan of the boiler in a dynamic way and in real time, based on the Recommended Practice of API 584 “Integrity Operational Windows” (IOW).
Discussion and Conclusions
After reviewing the Current Situation in the Use and Care of Boilers, from the point of view of Operation, Inspection and Maintenance, on the diagram of the trend of the maturity levels of the implementation of the predictive strategy, including in industrial installations where there are advanced levels of automation and maintenance programs focused on reliability, whose Level of implementation of said strategy can be considered at Level 3 and Industry 4.0 is spoken of, the boiler area could be below a Level 2, for reasons ranging from the criterion that the business is not to produce steam, through the lack of knowledge or lack of definition of Critical Operating Parameter Limits and concentrating the operator’s attention on the amount of steam required to guarantee the production, neglecting many of the available parameters, which could be correlated with damage mechanisms of different components of the cald It was, and finally, the limitation of only considering the thickness measurement to evaluate the mechanical integrity condition of the boiler and to close the fact of focusing the maintenance scopes on the areas where the most recent or recurring failures have occurred.
Defining the Critical Operating Limit Parameters that ensure the operational safety, efficiency and reliability of the boilers, and including in the operators’ verification routine real-time monitoring and immediate and timely adjustments-corrections of non-conformities in the IOW, will guarantee greater availability of the boilers.
In many installations there are adequate control systems and automation levels to move up the scale of maturity of the predictive strategy of the steam generation system, to higher levels, defining the Critical Operating Limits, training operators in this methodology , defining the correlation between the Critical Operating Limit Parameters and the generation of damage mechanisms and changing the inspection strategy based on condition. All this receiving information in real time.
By defining the “Operational Integrity Windows” (IOW) – the Critical Operating Limit Parameters and carrying out their Real-Time Monitoring, the operator aligned and instructed in this new methodology:
- It will generate correct and immediate corrective actions, in order to optimize operational safety and efficiency, and
- The conditions or contingencies that promote the generation of probable and credible damage mechanisms in each component of the boiler, with the consequent loss of reliability, will be identified.
With this information, the inspection and maintenance of the boiler, from the current average level based on frequent failures and visual inspections or limited to thickness measurements, will rise to a condition of much greater reliability.
With existing resources and staff training, Caldera 4.0 can be aspired to.
References
- “Integrity Operating Windows” API Recommended Practice 584, American Petroleum Institute (API), 1st Edition, May 2014.
- Guillermo Alberto Molina, “The Electronic Control for the Air-Fuel Ratio” , Boilers. User’s Guide (in Industry and Commerce) http://www.ceaca.com/revistas , 3rd Edition, January 2021.
- Marta Alberdi, “Holistic view of condition-based maintenance within the 4.0 framework” , Online Technical Conference on Reliability in AEM Maintenance, November 2020 – February 2021.
- “Risk-Based Inspection” API Recommended Practice 580 , American Petroleum Institute (API), 3rd Edition, February 2016
- “Inspection Planning Using Risk-Based Methods” ASME PCC-3–2017.
- R. Tilley, “ Boiler Condition Assessment Guideline ”, EPRI (Electric Power Research Institute), Fifth Edition, USA 2011[Reporte Final] .
- The Babcock & Wilcox Company “ Steam its generation and use ”, Chapter 46, Issue 42, USA 2015[Libro] .
- C. Lasarte, “Traditional Reactive Maintenance of Boilers versus Condition-Based Maintenance and the Next Level Result of Monitoring Windows of Operational Integrity” , Online Technical Conference on Reliability in AEM Maintenance, November 2020 – February 2021.
- C. Lasarte, “Monitoring Temperatures in Boiler Tubes and Components to Optimize Efficiency, Operational Health and Generate Inspection Priorities” , 1st Conference on Reliability in AEM Maintenance, Madrid, November 27 and 28, 2019.
- C. Lasarte, ” Optimization of the Boiler Inspection Plan for More Accurate Maintenance Scopes and Greater Reliability “, ID AEND-3926, 14th National Congress of Non-Destructive Testing, Vitoria – Spain June 2019[Artículo] .
About the Author.
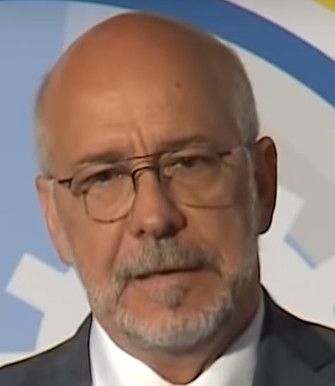
Lic. Carlos Luis Lasarte V.
General Director – Consultant Combustion, Energy & Environment, SA ( carlos.lasarte@ceaca.com )