Table of Contents
- Corrosion as a multivariable and nonlinear phenomenon
- Limitations of traditional methods
- How artificial intelligence is transforming corrosion diagnostics
- Typical workflow of a predictive corrosion system
- Case studies of real applications in industry
- Benefits of predictive asset management
- Challenges, ethical considerations, and the future of ML in corrosion
- Conclusiones
- References
Corrosion is one of the most persistent and costly silent enemies in modern industry. It affects the service life of pipelines, storage tanks, offshore platforms, heat exchangers, and a wide range of critical assets. Despite traditional monitoring and inspection efforts, many structural failures still occur without warning, causing unplanned shutdowns, high repair costs, and operational safety risks.
The corrosion phenomenon is highly complex, multivariable, and nonlinear. Factors such as water chemistry, temperature, pressure, pH, chloride presence, and carbon dioxide interact in ways that conventional deterministic models cannot accurately predict1.
In this scenario, artificial intelligence (AI) emerges as a transformative tool. Through machine learning, it becomes possible to analyze large volumes of historical and real-time data to enhance corrosion detection, identify hidden patterns, and anticipate degradation before it occurs. This marks a shift from corrective to predictive asset management, revolutionizing how mechanical integrity is preserved in demanding industrial environments.
In the following sections, we will explore how AI is reshaping corrosion diagnostics, featuring real-world use cases, model architectures, and comparisons with traditional methods. The future of maintenance starts today… and it’s driven by algorithms.
Corrosion as a multivariable and nonlinear phenomenon
Industrial corrosion is neither an isolated nor a linear process, it is results from multiple variables interacting in complex and often unpredictable ways. Key influencing factors include:
- Dissolved chlorides (common in marine or industrial water environments),
- Free CO₂ (acidifies the environment),
- Fluid temperature,
- Relative humidity of the environment,
- Flow velocity (or lack of flow, such as in stagnant water),
- Environmental pH,
- Electrochemical potential of the metallic surface.
These variables vary not only between systems but also over time. The combination of factors can trigger localized corrosion mechanisms, pitting, stress corrosion cracking, and particularly galvanic corrosion when dissimilar materials are in contact.
Limitations of traditional methods
Traditional corrosion detection methods—such as visual inspection, ultrasound (UT), radiography (RT), and metallographic analysis—have been industry staples for decades. However, they present key limitations:
- They are reactively expensive, as they rely on periodic manual inspections.
- They do not predict failures but only diagnose existing damage.
- Their effectiveness largely depends on the operator’s expertise.
- They require equipment shutdown and physical access.
In addition, most of these methods lack a holistic view of corrosive behavior as a function of time. This is where machine learning-based solutions offer a disruptive approach: anticipating damage before it becomes visible.
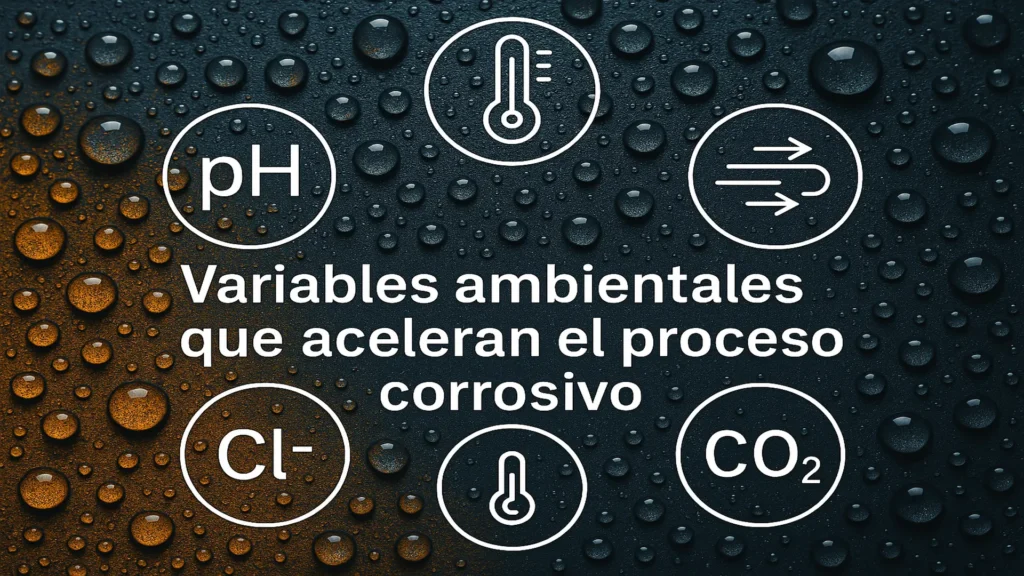
How artificial intelligence is transforming corrosion diagnostics
Machine learning (ML) enables training algorithms to identify hidden patterns in multivariable data. In the corrosion context, these algorithms learn from historical data, visual inspection reports, previous inspections, sensor measurements, operational variables, and even images captured by videoscopes or drones.
Instead of relying solely on human judgment, predictive models process millions of records to generate forecasts of when, where, and under what conditions corrosion failures are most likely to occur. Techniques such as feature engineering are key to transforming raw sensor data into meaningful variables that improve predictive accuracy.
Machine learning provides significant advancements in corrosion detection by enabling the analysis of large, multivariable datasets. Common inputs for these models include:
- Historical results from UT, RT, or EDX,
- Environmental records (temperature, humidity, chlorides),
- Pressure or flow fluctuations in piping systems,
- Thermal or visual equipment imagery,
- Alerts from corrosion or pitting sensors.
This approach allows for early warning systems, condition-based maintenance (CBM), and real-time decision-making.
Applicable model types
The most commonly used algorithms for predicting corrosion failures include:
- Random Forest: A machine learning algorithm that uses multiple decision trees to analyze complex datasets with both categorical and numerical variables. It is highly robust against outliers and noise.
- Support Vector Machines (SVM): A supervised learning model used to classify data points into categories. It is especially effective for detecting and separating deterioration states in engineering systems.
- Artificial Neural Networks (ANN): A type of deep learning model inspired by the human brain, capable of identifying complex, non-linear patterns in data. Ideal for failure prediction and anomaly detection.
- Deep Learning (CNN and LSTM): Convolutional Neural Networks (CNN) are ideal for analyzing images and detecting complex visual patterns, while Long Short-Term Memory (LSTM) networks are a type of recurrent neural network designed to work with time series data, recognizing sequential patterns such as sensor logs.
These models excel at learning from highly variable environments and changing operational conditions. Unlike deterministic equations, AI algorithms evolve, improve accuracy, and adapt to new conditions as they receive more data.
An essential part of this success lies in feature engineering, which transforms raw operational and environmental data into structured inputs that make these models more effective and interpretable.
Typical workflow of a predictive corrosion system
Implementing an AI-based corrosion prediction system involves more than installing sensors—it requires a comprehensive architecture of data, models, and validation. The typical workflow includes several critical stages that transform raw data into actionable operational decisions.
Data collection
The first step is to gather relevant data from various sources:
- Field-installed IoT sensors (pH, chlorides, humidity, temperature, electrochemical potential),
- Periodic NDT testing (UT, RT, eddy currents),
- Maintenance history, alarms, and failure records,
- Visual inspection images or videos captured using borescopes, drones, or thermal cameras remain a valuable input in AI-based models.
This phase demands robust data acquisition (DAQ) infrastructure, industrial networks, and real-time connectivity.
Data preprocessing
Raw data is rarely usable in its original form. It must be:
- Filtered to remove outliers or inconsistencies,
- Synchronized across heterogeneous sources (time, location),
- Normalized across different measurement scales,
- Enriched using feature engineering (deriving variables such as corrosion rate or thickness loss trends).
Proper preprocessing enhances model accuracy and reduces noise-related errors.
Model selection and training
Depending on the asset type, environment, and data availability, the most appropriate algorithm is selected:
- Random Forest for interpretability and robustness.
- SVM for limited but well-defined datasets.
- Deep Learning for complex image or time-series data.
Models are trained using techniques like cross-validation and fine-tuned through hyperparameter optimization to improve accuracy, precision, and sensitivity.
Evaluation and validation
Model performance is evaluated using metrics such as:
- ROC-AUC curve (discrimination ability).
- Precision/Recall (failure detection effectiveness).
- Confusion matrix (classification errors).
Underperforming models are retrained or combined into ensembles. This often requires repeating the feature engineering process to create more informative variables that reduce noise and improve predictive performance.
Field implementation
Finally, the model is deployed on a monitoring platform, integrated with:
- Predictive dashboards (featuring early warnings).
- SCADA or DCS systems for real-time decision-making.
- Mobile applications for maintenance technicians. These platforms can integrate visual inspection checklists and images to support real-time maintenance decisions.
This integration enables predictive asset management, reducing operating costs, preventing failures, and extending the service life of critical equipment.
Case studies of real applications in industry
Artificial intelligence applications for predicting corrosion failures are already transforming various industries, where visual inspection continues to play a key role when combined with predictive models. From structures exposed to extreme environments to critical assets with high downtime costs, AI enables proactive monitoring based on real-world data.
Offshore platforms and chemical plants
In subsea environments, corrosion from chlorides and microorganisms poses a constant threat. Predictive models fed with data from thickness, temperature, salinity, and pressure sensors allow for early detection of material loss and perforation risks in piles and umbilical lines.
In chemical plants, AI is applied to detect corrosion under insulation (CUI) using thermal imaging and computer vision algorithms. This reduces the need to remove coatings and improves operational efficiency.
One of the most innovative examples comes from AISUS Offshore Ltd, which, together with Robert Gordon University (UK), developed a robotic solution powered by artificial intelligence and deep learning to inspect offshore structures, particularly in critical areas such as the splash zone. The tool analyzes images and ultrasonic data collected in the field and predicts defects with 92% accuracy. This approach has revolutionized the way they inspect and make technical decisions. See the full case in the following video from the North of Scotland KTP Centre:

Inspection of offshore assets using AI.
Pipelines and storage tanks
Models trained with ultrasonic measurements and operational conditions (flow, temperature, pH) allow real-time mapping of critical zones. This enables failure anticipation before scheduled inspections and optimizes risk-based maintenance (RBI).
This approach has been successfully implemented in hydrocarbon transport systems and storage terminals, reducing costs and improving safety.
Refineries and thermal facilities
AI enables the integration of thermal and geochemical data to predict phenomena such as sulfidation and acidic corrosion. In boilers and heat exchangers, models detect anomalous patterns that signal accelerated material loss.
These tools have proven useful in refineries, where thermal cycles and aggressive compounds accelerate metal equipment degradation.
Comparison: Traditional Methods vs. Artificial Intelligence
Requires physical contact | Non-invasive, continuous |
Interval-based inspection | Real-time monitoring |
Operator-dependent | Data-driven |
High field cost | Scalable ROI after setup |
Requires physical contact | Non-invasive, continuous |
Traditional corrosion inspection relies on techniques such as ultrasound, radiography, or visual checks, which require physical contact with components, downtime, and skilled personnel. While reliable, these methods only provide a static snapshot of the equipment’s condition at a specific moment.
In contrast, AI systems allow for continuous supervision via IoT sensors and digital platforms. These models learn from operational and environmental data to predict failures before they happen. They also eliminate operator subjectivity, standardizing alert and response criteria. This translates into faster, evidence-based decision-making. The efficiency and foresight enabled by AI reduce the risk of catastrophic failures, optimize resources, and improve return on investment in predictive maintenance.
Benefits of predictive asset management
Integrating AI into corrosion prediction elevates asset management to a new level. Thanks to its ability to process vast amounts of data and detect complex patterns, companies can:
- Strengthen model performance through feature engineering, enabling the extraction of meaningful features from complex industrial data.
- Improve strategic maintenance decisions by prioritizing interventions where the risk is highest.
- Reduce unplanned shutdowns by anticipating failures based on real operating conditions.
- Optimize resource allocation by focusing inspections and repairs on previously identified critical points.
- Extend asset life by preventing severe degradation through early alerts.
This digital transformation enables a shift from corrective to predictive and data-driven maintenance, aligned with Industry 4.0 principles.
Challenges, ethical considerations, and the future of ML in corrosion
Despite its many benefits, adopting artificial intelligence in corrosion monitoring presents important challenges:
- Data quality and volume: Models require large volumes of reliable data to function properly. Poor calibration or noise can impact accuracy.
- Model biases: A model trained in one environment may not generalize well to others. Representative and diverse datasets are essential.
- Lack of technical standards: The absence of unified international standards for model validation raises concerns in regulated industries.
- Hybrid talent: Effective implementation requires professionals with expertise in both data science and corrosion engineering.
The future points toward continuous self-learning models, combined with smart sensors and cloud platforms, integrating maintenance, process control, and predictive analytics.
In this new paradigm, corrosion will cease to be a silent threat and become a predictable, controllable, and optimizable variable.
Conclusiones
Corrosion remains one of the most complex challenges in industrial asset management—especially due to its multivariable, nonlinear nature and the difficulty of prediction using conventional methods. In this context, artificial intelligence and machine learning are not just technological advantages, but strategic shifts in how mechanical integrity is addressed.
These models allow for early corrosion detection, failure anticipation, resource optimization, and extended lifespan of critical equipment from pipelines to offshore platforms.
Fostering a predictive maintenance culture is essential to reducing unplanned downtime and increasing operational safety. This requires breaking down traditional silos: corrosion specialists, data engineers, and IT teams must collaborate to create integrated, robust, and scalable solutions.
The future of mechanical integrity will depend on organizations’ ability to leverage these disruptive tools, combining technical expertise with advanced analytics. In this journey, platforms like Inspenet play a key role by offering specialized content, training spaces, and the latest insights into artificial intelligence applied to maintenance and asset management.
The time to evolve toward smart prediction is now.
References
1.Dong, Z., Ding, L., Meng, Z. et al. Machine learning-based corrosion rate prediction of steel embedded in soil. Sci Rep 14, 18194 (2024). https://doi.org/10.1038/s41598-024-68562-w