Table of Contents
- Introduction
- What is sandblasting?
- International standards for sandblasting surface preparation
- Types of sandblasting equipment
- Classification of sandblasting according to techniques and abrasives used
- Abrasives used and ecological alternatives in process application
- Environmentally friendly cleaning alternatives to traditional sandblasting
- Industrial sandblasting applications
- Conclusions
- References
Introduction
Sandblasting, also known as shot blasting, is a mechanical cleaning process used for surface preparation by applying a high-pressure abrasive material, usually sand, to remove surface layers of oxides or paints. Historically, this method has advanced from traditional approaches, integrating sustainable strategies in response to environmental and safety concerns.
In this article, we will discuss the sandblasting process, types, emerging technologies and sustainable solutions that are transforming the industry. In addition, green alternatives that minimize environmental impact without compromising surface preparation efficiency will be discussed.
What is sandblasting?
Sandblasting consists of projecting different types of abrasive particles at high pressure against a surface using compressed air or mechanical systems, in order to clean, deoxidize or prepare surfaces to improve the adhesion of subsequent coatings and prolong the useful life of materials.
The effectiveness of the process depends on factors such as the type of abrasive, the pressure applied, the adherence of the dirt and the distance between the nozzle and the surface to be treated. Depending on the abrasive material used and the pressure applied, different finishes and degrees of cleanliness can be achieved.
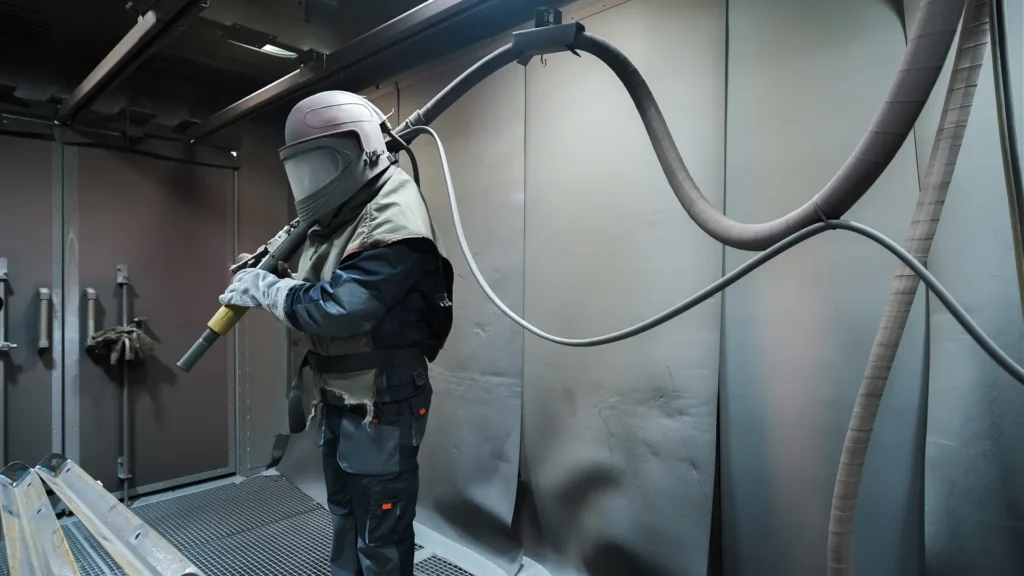
Basic components of a dry sandblasting equipment
This equipment is composed of several elements that together guarantee an efficient and safe operation:
- Pressurization system: Supplies the compressed air necessary to project the abrasive with the appropriate force. It can be driven by air compressors or pressure controlled systems.
- Hopper or storage tank: Contains the abrasive material and allows controlled dosing to ensure uniform application.
- Mixing valve: Regulates the mixture of air and abrasive, controlling the proportion and flow to achieve the required cleaning intensity.
- Hoses and control valves: Convey and regulate the flow of air and abrasive, allowing adjustments according to the application.
- Sand nozzle: Directs the abrasive jet to the target surface. Its design and material influence the precision and efficiency of the process.
- Dust collection and filtering system: Reduces the dispersion of particles in the environment, improving safety and visibility during the process.
The following video highlights the innovative features and reliability of Elcometer’s ASME-compliant, heavy-duty sandblasting equipment. These systems incorporate robust hoppers, heavy-duty tubing, high-pressure hoses, bearing wheels and a multi-layer corrosion resistant coating. In addition, pneumatic remote control valves such as the RCB 4000 allow safe and precise control at the nozzle, minimizing flow and pressure loss.

Sandblasting equipment.
Influence of nozzle distance on sandblasting performance
The distance between the nozzle and the surface is a critical variable in determining the intensity and effectiveness of the cleaning:
- Short distance (5-15 cm): Provides aggressive cleaning and a deep anchor profile, but may cause excessive wear or irregularities if not properly controlled.
- Medium distance (15-30 cm): Offers a balance between efficiency and control, achieving uniform cleaning without compromising the integrity of the treated substrate.
- Long distance (more than 30 cm): Decreases the effectiveness of the abrasive impact, being less suitable for deep cleaning or when a specific anchor profile is required.
International standards for sandblasting surface preparation
To ensure proper surface preparation and achieve optimum results in this process, there are international standards that establish specific cleaning requirements according to the type of application. Among the most recognized are the SSPC (Steel Structures Painting Council) and NACE (National Association of Corrosion Engineers) standards, currently integrated in the AMPP (Association for Materials Protection and Performance).
These standards define different degrees of cleanliness, from the removal of loose contaminants to white metal cleaning, where all visible contaminants are removed. Through this mechanical cleaning process, various levels of SSPC cleanliness are achieved, ensuring that surfaces are adequately prepared for the subsequent application of protective coatings.
Surface preparation categories established by SSPC and NACE include:
Surface preparation categories established by SSPC and NACE inSSPC SP5 / NACE 1: Abrasive blast cleaning to a white metal, completely removing contaminants, oxides and previous coatings. This is the most demanding cleaning grade used in highly corrosive environments:
- SSPC SP10 / NACE 2: Abrasive blast cleaning to near white metal, removing at least 95% of adhering contaminants and oxides (allowing for light shading or staining). Provides an excellent surface for high performance coatings.
- SSPC SP6 / NACE 3: Commercial abrasive blast cleaning, removing at least 67% of existing oxides and coatings, (slight traces of residues are allowed). It is suitable for applications where good general cleanliness is required.
- SSPC SP7 / NACE 4: Fast abrasive blast or “blast” cleaning, which removes loose contaminants, but leaves some adhering residue. It is a light cleaning, used for less demanding applications.
- SSPC SP14 / NACE 8: Industrial abrasive blasting, removing most contaminants, but not necessarily strongly adhering imperfections.
Types of sandblasting equipment
The equipment for this cleaning process has diversified to adapt to different applications or industrial needs, improving efficiency and reducing environmental impact:
- Sandblasting booths: Small, enclosed systems used for small parts and precision work. These circuits control the generation and recovery of powder and abrasive.
- Sandblasting rooms: Large spaces designed for the treatment of parts of various sizes and complexities; they optimize abrasive recovery and reduce dust emission.
- Portable equipment: Mobile units used for field applications, mostly in large structures.
- Simultaneous recovery systems: Combine the cleaning process with vacuum systems to minimize waste and reuse the abrasive.
- Wet sandblasting equipment: Uses a mixture of water and abrasive, which reduces dust generation and abrasive consumption. This process performs a deeper cleaning.
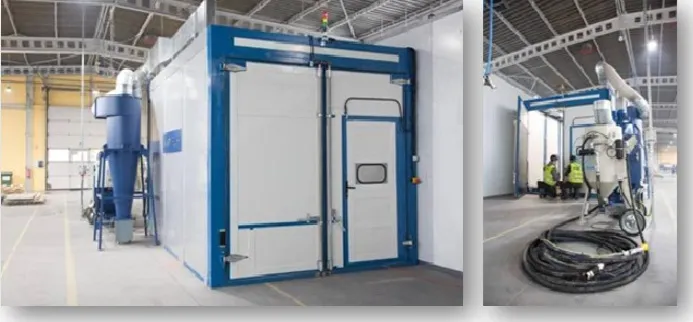
Classification of sandblasting according to techniques and abrasives used
The sandblasting process is classified into different types according to the technique used and the abrasive material employed. With the advance of technology, more efficient and environmentally friendly methods have emerged that optimize the process and reduce its environmental impact. The main categories are listed below:
Depending on the type of abrasive
- With silica sand: Traditional method, currently in disuse in many regions due to the risks of silicosis and environmental restrictions.
- Steel shot blasting: Uses steel shot, a highly reusable and effective metallic abrasive for metal surfaces.
- With aluminum oxide: Aggressive abrasive suitable for the preparation of hard metals.
- With glass microspheres: Ideal for delicate cleaning and decorative finishes.
- With environmentally friendly abrasives: Use biodegradable materials such as baking soda, walnut shells, corn husks or recycled glass.
Depending on the application medium
- Dry: This is the most common method, where the abrasive is discharged with compressed air.
- Wet: Mixes water and abrasive to reduce dust generation.
- Hydroblasting: Uses ultra high pressure water (+20,000 PSI) without abrasives, being a different alternative and not a direct variation of sandblasting.
Depending on the automation and technology used
- Manual: Operated directly by a technician who controls the nozzle and abrasive flow.
- Robotic: Uses programmable robots to optimize cleaning in complex industrial applications, increasing accuracy, operational efficiency, and reducing operator exposure to occupational hazards.
- With abrasive recovery: Equipment designed to collect and reuse abrasive, reducing operating costs and waste.
- With precision control: Advanced systems that allow precise adjustment of abrasive pressure and flow, optimizing material consumption.
- With solid CO₂ (dry ice): It uses dry ice pellets that sublimate upon impacting the surface, eliminating contaminants without leaving secondary residues; it is an environmentally friendly and safe method.
The following video shows the VertiDrive V700 sandblasting robot operating on a ship’s hull, demonstrating its accuracy and efficiency. These remotely controlled robots minimize operator exposure to hazardous environments, increase productivity by operating continuously and reduce downtime.

Robot for sandblasting
Abrasives used and ecological alternatives in process application
The choice of abrasive is critical to sandblasting success. As technology has advanced, safer and more sustainable options have emerged that minimize environmental impact and health risks.
Traditional abrasives
These abrasives have been widely used for their effectiveness, although some have disadvantages in terms of safety and sustainability:
- Silica sand: Economical and effective, but generates silica dust, associated with respiratory diseases such as silicosis.
- Aluminum oxide: One of the most widely used sandblasting abrasives, it is a very hard medium, mainly used for deep cleaning.
- Silicon carbide: The hardest abrasive for sandblasting, used in applications requiring extremely high abrasion, such as stone, ceramics and glass.
- Steel shot: Durable and effective for the cleaning and preparation of metal surfaces in heavy industry.
Ecological alternatives
The use of environmentally friendly abrasives in this type of cleaning is the most widely used for reducing hazardous waste generation and improving occupational safety. Some outstanding options include:
- Sodium bicarbonate: Gentle, water-soluble and non-toxic, ideal for delicate cleaning without damaging the underlying surface.
- Garnet: A natural abrasive, free of contaminants, with good reusability and less dust generation.
- Copper slag: Recycled industrial by-product, economical and effective for removing coatings and oxides.
- Glass bead: Reusable and recommended for fine and polished finishes without affecting the integrity of the surface.
- Biodegradable plastic abrasive: Made with polymers of natural origin, used for the removal of coatings without damaging the base surface.
- Walnut shell: An organic and biodegradable abrasive with mild characteristics, used in the cleaning of engines and automotive components without risk of damage.
- Dry ice (solid CO₂): It does not generate secondary waste, as the pellets sublimate upon impacting the surface, making it ideal for cleaning machinery in the food and electronics industry.
- Vegetable abrasives (corn cob, fruit seeds): Biodegradable and low abrasiveness, used in soft and delicate cleaning.
- Recycled glass: Sustainable alternative that reuses materials, available in different granulometries for various cleaning applications.
- Iron silicate: It is an environmentally friendly recycled shot and this reduces the need to extract new natural resources.
Environmental impact and benefits of green alternatives
The use of environmentally friendly abrasives has been shown to reduce hazardous waste generation by up to 80% compared to the use of silica sand. In addition, biodegradable and renewably sourced abrasives contribute to the reduction of the carbon footprint, minimizing the environmental impact of the industry.
Environmentally friendly cleaning alternatives to traditional sandblasting
Faced with the environmental impact of traditional sandblasting, innovative solutions have emerged that not only reduce waste, but also optimize the cleaning process:
- Laser cleaning: Uses a beam of light to remove oxides without generating abrasive residues or damaging the integrity of the material.
- Dry ice blasting: high velocity ice pellets are projected, removing contaminants by sublimation without leaving secondary residues.
- Controlled chemical cleaning: Uses chemical solutions to dissolve impurities and coatings, but requires proper handling to avoid environmental impacts.
- Ultrasonic cleaning: Uses high-frequency vibrations in a liquid medium to dislodge contaminants without abrasives, ideal for delicate parts and electronic components.
- Nanotechnology applied to cleaning: Develops self-cleaning coatings that reduce the need for abrasive processes.
Industrial sandblasting applications
This type of cleaning is widely used in various industries for surface preparation and maintenance. Some of its most relevant uses include:
- Metal surface preparation: Ensures proper adhesion of paints and anticorrosive coatings.
- Mold and die cleaning: Keeps molds in optimal conditions in the plastics and foundry industry.
- Rust and corrosion removal: Used in shipbuilding and the energy industry.
- Structure and monument restoration: Allows deep cleaning of stone, concrete and other materials without damaging them.
- Engine and industrial components maintenance: It is used to clean mechanical parts without compromising their functionality.
- Decorative finishes in glass and stone: Creates textures and patterns in materials used in architecture and design.
Conclusions
Sandblasting continues to be a strategic technique for surface preparation, but its evolution is marked by the search for greater efficiency and sustainability. With the incorporation of innovative technologies such as abrasive recovery blasting and the use of dry ice, industries are reducing environmental impact and improving operational safety.
In addition, the adoption of environmentally friendly abrasives and residue-free alternatives, such as nanotechnology, offers cleaner and more effective solutions without compromising process performance. In the future, sandblasting is expected to continue to adapt to stricter environmental regulations and automation with robotic equipment will further optimize its application in sectors such as construction, manufacturing and the energy industry.
References
- https://www.codinter.com/es/abrasivos-para-sandblasting-todos-los-tipos-y-usos-para-cada-uno/
- https://grupoagras.com.mx/sandblast-arenasilicasandblast-arenasilica-sandblasteo-arenassilicas-arenasilicasanblasteo-arenassilicassandblast-arenasilicasanblastear-arenasilicaparasandblast