Table of Contents
Introduction
In the energy sector, and particularly in the oil and gas industry, the mechanical integrity of facilities is paramount to ensure safe and efficient operations. Risk management in mechanical integrity is relevant and indispensable not only in preventing failures, but also in guaranteeing the safety of processes , workers and the protection of the environment.
Moving beyond incident prevention, risk identification extends to improving equipment performance and efficiency. This process highlights the interrelationship between mechanical integrity and risk; an understanding necessary to maintain and strengthen the integrity of mechanical systems. In particular, this dynamic is relevant in the complex industrial environments of the oil and gas sector, where effective risk management is essential for operational success.
What are operational risks?
In the oil and gas industry, these risks refer to risks associated with routine operations, which can directly affect the integrity, safety, efficiency and profitability of operations throughout their value chain. These types of risks cover a wide range of aspects, from technical failures, human errors, regulatory breaches to external events and environmental challenges.
Operational risk management and its importance
This management is a systematic process that addresses the identification, evaluation and mitigation of risks that could affect the continued operation of an organization. In the oil and gas industry, it is essential to guarantee the integrity of assets, the safety of processes, personnel, and the protection of the environment. Today there are advanced technologies that anticipate the greatest operational risks, while connecting with the cloud, to obtain effective mitigation strategies and avoid incidents.
In this sector, risks can have significant consequences; effective risk management is necessary for accident prevention and operational continuity. The importance of maintaining good management lies in the ability to anticipate and identify risk, and in turn manage unforeseen situations precisely, protecting the mechanical integrity of the assets and thus guaranteeing the success and sustainability of operations.
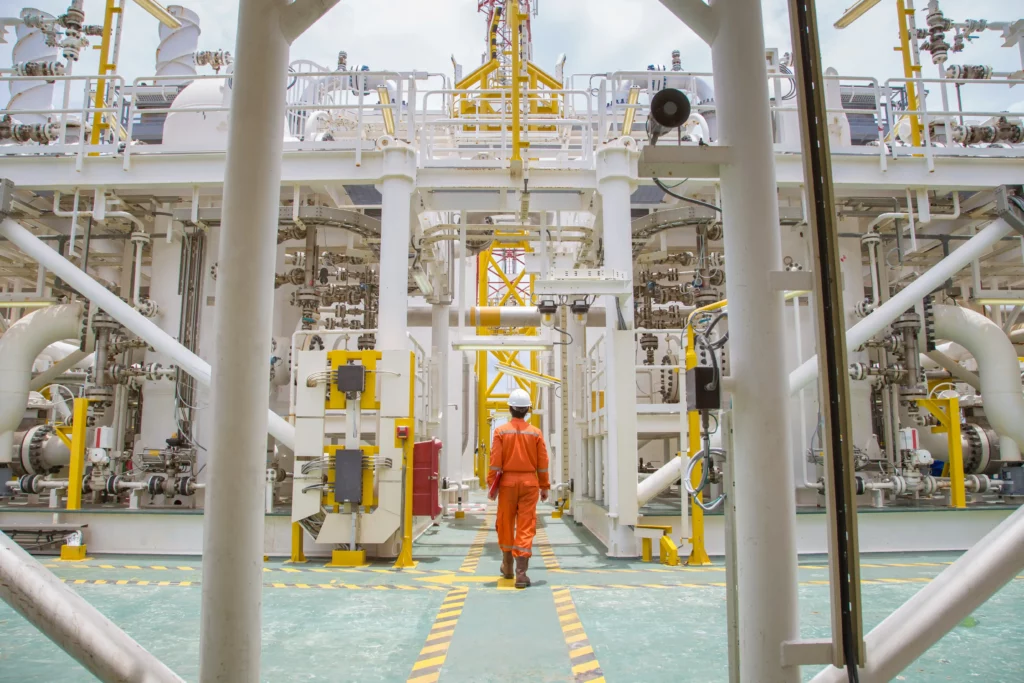
During operational risk management, risk identification, It is the first step to consolidate; This process involves a thorough analysis of possible threats and vulnerabilities that may affect the integrity of the assets; In this step, advanced techniques, such as data analysis and predictive process modeling, are implemented to identify risk scenarios and prepare appropriate response strategies.
Another important point is process safety , which is rated as a critical component in preventing accidents and equipment failures. Effective integration of process safety within risk management creates more controlled and predictable operating environments; because strategies such as automated controls and constant monitoring are used to mitigate identified risks and improve the overall security of operations.
Operational risk mitigation strategies in the oil industry
To mitigate operational risks, there are various strategies that organizations implement. One of the most effective approaches is based on establishing a comprehensive risk management framework that includes: identifying, evaluating and prioritizing risks, followed by the implementation of specific measures for each case. These measures seek to reduce the probability of risks occurring, mitigate their impact, or manage them appropriately within the organization’s tolerance thresholds.
Among the main strategies used as preventive measures for a operational risk management There is the application of the Risk Based Inspection (RBI) methodology, which involves identifying and understanding the drivers of risks, to prioritize inspection and maintenance activities on critical assets. This methodology involves performing both qualitative and quantitative assessments of the risks associated with each piece of equipment and component.
Another measure is Process Safety Management Systems (PSM); which is a set of practices designed to efficiently manage the risks associated with industrial processes, especially in environments where dangerous substances are handled, with the aim of minimizing the risk of operational accidents. PSM covers aspects such as risk identification, hazard assessment, personnel training and emergency preparedness.
Likewise, systematic techniques are used such as Root cause analysis (RCA), which is applied in risk management to identify the underlying causes of incidents or failures instead of focusing solely on the symptoms or immediate effects, preventing the repetition of the incident and improving safety and operational reliability.
The objective of these methodological strategies is to provide the information necessary to create inspection and maintenance programs that are dynamic and profitable. These programs focus especially on the management of the highest risk equipment, thus allowing continuous monitoring of its integrity. Other strategies include implementing strong internal controls, investing in technology and infrastructure, and establishing effective employee training programs.
Risk analysis and criticality of equipment in operational risk management
In the oil industry, risk analysis and criticality assessment are required to preserve the mechanical integrity of assets. This process begins with the identification of risks associated with each piece of equipment, considering its probability of failure and the potential impact of an incident. Aspects such as maintenance history and operating conditions are analyzed to then assign a level of criticality, based on the importance of the equipment to operations and its influence on safety and the environment.
Criticality determines inspection and maintenance strategies, with a more intensive approach for high-criticality equipment. This optimizes the use of resources, prioritizing equipment that requires maintaining its integrity. Risk analysis and equipment criticality guide resource allocation, focusing efforts on critical areas to prevent costly incidents and ensure operational efficiency. The adoption of advanced technologies such as real-time monitoring and predictive analysis is a priority in operational risk management.
To effectively manage operational risks, organizations adopt, focus on continuous risk monitoring and assessment. This is achieved by establishing a risk management committee that is responsible for overseeing associated activities. Additionally, organizations should establish a culture of risk awareness and responsibility, where employees are encouraged to report potential risks and are held accountable for their actions.
Importance of integrating risk management into mechanical integrity
Integrating risk management into mechanical integrity is critical in the oil industry. This integration involves the identification, assessment and continuous control of risks associated with operations to protect assets, including personnel, property and profits of the organization.
In the context of mechanical integrity, risk management includes implementing written procedures to identify and report potentially defective or unsafe equipment.
An integral part of this process is equipment inspection , which includes the implementation of field inspections, data analysis and inspection reports, management of findings and recommendations, and audits for continuous improvement. These inspections are essential to prevent failures and contribute to extending the useful life of industrial assets.
The effective integration of risk management into all organizational processes includes the identification, evaluation, design and implementation of actions to eliminate, mitigate, share, transfer or tolerate risks. These actions must be monitored and reviewed to verify their effectiveness.
Conclusions
Effective risk management in the oil and gas industry guarantees safe and efficient operations. Focusing not only on incident prevention but also on improving equipment performance, this management underlines the importance of a deep understanding of the interrelationship between mechanical integrity and risk. Identification and mitigation of operational risks, including technical failures, human errors and environmental challenges, are essential to protect the integrity, safety and profitability of operations.
In risk management in mechanical integrity, the risk and criticality analysis of equipment is of great importance . Through this analysis, the priority of equipment in terms of criticality for inspections and maintenance is determined, focusing on the probability of failure and the potential impact on safety and the environment.
Implementing risk mitigation strategies focused on the mechanical integrity of assets, such as risk-based inspection and root cause analysis in the oil industry, improve operational reliability and ensure the continuity and efficiency of operations.
Reference
Own source