Introduction
Reliability in the mining industry is one of the variables that directly impacts the safety, efficiency, and productivity of operations. Ensuring or minimizing the probability of reliability failures in mining equipment and processes improves operational performance, and also reduces costs and minimizes the risk of accidents.
This article analyses the interrelationship between the maintenance of equipment used in mining and the operational reliability that the mining operator must provide. In order to comply with the different phases of the process and guarantee safe and sustainable production in terms of time and quality.
Maintenance of mining equipment
Due to the disruptive environment and intensive demands of mining, a proactive and well-structured approach to maintenance is vital. Two key aspects of mining equipment maintenance are detailed below, including some emerging strategies and technologies.
Diagnostics and preventive maintenance
Diagnostics and preventive maintenance are essential components of ensuring reliability in the mining industry. These practices prevent unexpected failures, optimize equipment life, improve operational safety and increase the overall efficiency of mining operations.
- Mining equipment diagnostics: involves the identification and assessment of conditions that may affect the performance of mining equipment. This process uses state-of-the-art technology and real-time monitoring tools. A prime example is vibration analysis, a condition monitoring technique that detects imbalances, misalignment, and other mechanical problems through abnormal vibration patterns.
- Preventive maintenance: Based on scheduled and systematic interventions, this approach includes a variety of activities designed to keep equipment in optimal operating condition. Replacing worn components before they fail is a key strategy, ensuring that equipment continues to operate efficiently and safely. The following image shows an operator cleaning the front cover of an AC electric motor in a mine as part of the maintenance program.
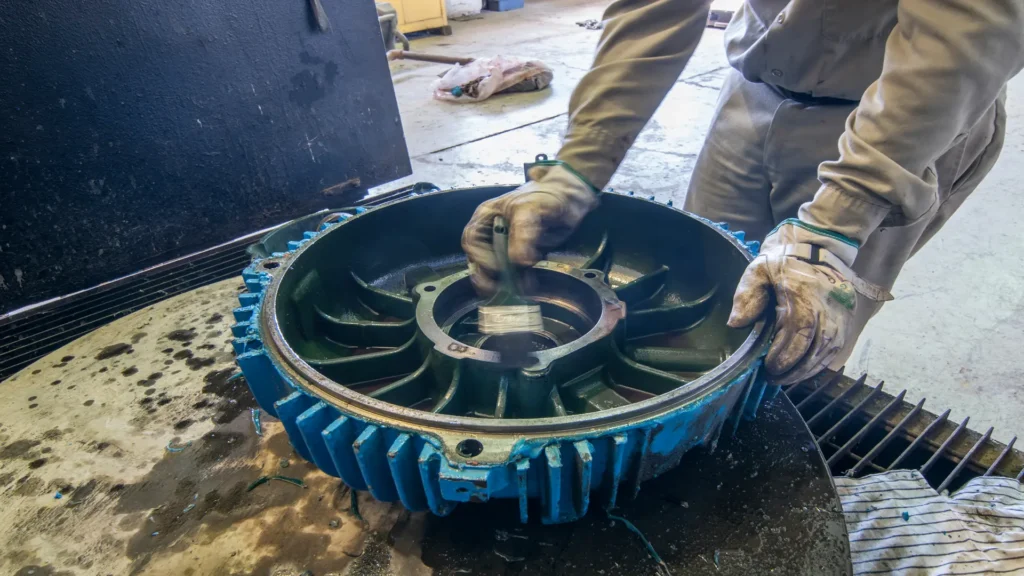
What is operational reliability?
Operational reliability is defined as the ability of an organization to perform its functions optimally over a specified operational time period. It is specifically influenced by equipment reliability and process reliability. Equipment reliability is measured by the frequency of failures over time: if there are no failures, the equipment is completely reliable; if failures are very infrequent, reliability is acceptable; but if failures are frequent, the equipment is unreliable.
techniques for the assessment reliability in the mining industry
In the mining environment, this management is fundamental and mandatory to ensure efficient and safe operations. The application of reliability techniques to reduce the likelihood of failure and ensure that equipment operates continuously and without failure is necessary to maximize productivity and minimize operating costs.
Assessing the reliability of mining equipment involves the use of various methodologies and tools to analyze and improve equipment performance. Some of the most commonly used techniques are described below:
Failure Mode and Effects Analysis (FMEA)
A Failure Mode and Effects Analysis (FMEA) is a risk estimation technique, a comprehensive analysis of possible failure points in multiple system components, which determines the degree of resistance to failure of the observed system.
In addition to identifying weak points – failure modes – the teams also examine their possible causes and, especially, their possible effects on other system components – effect analysis. The possible failures, the probability of their occurrence and the magnitude of their impact are expressed quantitatively in a graph. It is a systematic technique used to identify and evaluate potential failure modes in a system or equipment and their effects on performance. This methodology helps to prioritize problems according to their severity, occurrence, and detectability.
Example of a case study on equipment reliability improvements: The following case study is from a mining operation in Australia, where condition monitoring and predictive maintenance techniques were implemented on excavator shovels. As a result, the reliability of these shovels increased by 18%, and overall mine production increased by 12%, demonstrating the effectiveness of these practices. This example underlines the importance of strong maintenance and reliability management in the mining industry.
Reliability Centred Maintenance (RCM)
The integration of reliability management systems (RCM) is a recognized methodology used to develop maintenance plans for industrial equipment, ensuring that it performs its functions to the satisfaction of the user or owner.
RCM guarantees an effective maintenance program, focusing on maintaining the original inherent reliability of the equipment. This process determines the actions necessary to ensure that any asset continues to perform its intended functions within its operational limits.
It is a tool that allows mines to optimize their maintenance and operational programs. In the process, of risk identification and assessment, RCM focuses on identifying and addressing the most critical failure modes, using a structured approach to determine the necessary maintenance tasks.
Benefits of RCM in operational reliability management
- Data monitoring and analysis: Enables the collection and analysis of real-time operational and maintenance data, which helps identify trends and patterns that may indicate potential problems.
- Maintenance task prioritization: Helps prioritize maintenance tasks based on the impact of failures, ensuring resources are used efficiently.
- Continuous improvement: Facilitates a proactive approach to continuous improvement of maintenance processes, increasing equipment life and reducing the risk of unexpected failures.
Optimization and operational security : Reduction of operational risks
Integrated Risk Management involves the identification, analysis, assessment, evaluation, control, and monitoring of corporate risks that may affect the organization. This proactive approach seeks to minimize negative impacts and improve efficiency and reduce operational risks, through the use of techniques and tools that allow the mining industry to evaluate different scenarios and make informed decisions to improve the operation.
Techniques and tools used in risk reduction
- Process simulations: Use computer models to recreate mine operating conditions, allowing engineers to test different strategies and see their impact on production.
- Predictive models: Use real-time and historical data to predict the future behavior of mining systems. This allows mines to anticipate problems and adjust their operations to minimize risk.
- Bottleneck analysis: Identifies points in the process where delays or inefficiencies occur, allowing mines to focus on improving these specific areas.
Benefits of process optimization
- Increased efficiency: Improves operational efficiency by identifying and eliminating process inefficiencies.
- Cost reduction: By optimizing processes, operational and maintenance costs are reduced, improving overall profitability.
- Improved safety: Process optimization also contributes to improved safety by reducing the likelihood of failures and accidents.
Mining safety and the relationship with reliability
Implementing safety standards to strengthen reliability
Risk identification and assessment and safety standards, such as those set by the Occupational Safety and Health Administration (OSHA), are critical to ensuring reliability in mining operations. Rigorous implementation of these standards not only protects workers, but also improves the efficiency and reliability of equipment and processes.
Benefits of safety standards
- Incident reduction: They help minimize accidents, creating a safer and more reliable working environment.
- Improved staff morale: A safe working environment improves worker satisfaction and morale, which can increase productivity and reduce staff turnover.
- Increased operational reliability: By preventing accidents, disruptions to operations are reduced, improving equipment reliability and efficiency.

How SAFE is the MINING industry?
Emerging technologies in equipment maintenance
The adoption of technologies such as the Internet of Things (IoT) and artificial intelligence (AI) is revolutionizing maintenance in mining. Smart sensors installed on haul trucks, for example, can monitor critical parameters such as engine temperature and vibration in real time, enabling predictive maintenance and reducing unexpected failures.
Real-time monitoring and control technologies
Risk identification and assessment, real-time monitoring and data analysis technologies, such as Supervisory Control and Data Acquisition (SCADA) systems, are essential for the continuous supervision of mining operations. These technologies enable operators to quickly detect and respond to any anomalies, thereby improving reliability in the mining industry.
Benefits of real-time monitoring technologies
- Early detection of problems: SCADA and other monitoring systems allow anomalies to be detected before they become serious failures.
- Rapid response: The ability to monitor in real time enables immediate response to any problem, minimizing downtime and repair costs.
- Continuous improvement: Data collected in real time provides valuable information for continuous process improvement and optimization of equipment performance.
Conclusions
The interconnection between reliability engineering in the mining industry, safety, implementing effective maintenance and reliability management strategies, adopting emerging technologies and following rigorous safety standards are fundamental to optimizing mining operations. These practices increase operational efficiency, reduce costs, and ensure a safer and more productive work environment.
By integrating risk identification and assessment with real-time data monitoring and analysis, significant improvements in the reliability and safety of mining operations can be achieved. Adopting a proactive and technologically advanced approach ensures efficient, sustainable mining and provides a competitive advantage in an increasingly demanding environment.
References
Own source
Implement these strategies now for safer and more efficient mining!