Table of Contents
- Reliability Centered Maintenance training covers several components
- Impact on operational efficiency
- Training in Reliability Centered Maintenance contributes to the extension of the useful life of assets through:
- Application of Reliability Centered Maintenance in real world scenarios
- Optimization of training programs for specialists in Reliability Centered Maintenance
- Absence of education! For Reliability Centered Maintenance
- Conclusion
- References
Reliability Centered Maintenance (RCM) builds a solid knowledge base, improves operational efficiency, and prolongs asset life. It is a systematic process used to determine the most efficient maintenance approach for assets, focusing on achieving the highest levels of reliability, safety, and cost effectiveness.
Training plays a fundamental role in the successful implementation of Reliability Centered Maintenance, equipping personnel with the necessary skills and knowledge to analyze, plan and execute maintenance strategies.
Through training, staff acquire the technical skills and specialized knowledge to apply analysis and evaluation methodologies, such as Failure Mode and Effect Analysis (FMEA), root cause analysis (RCA) and risk management, along with the ability to develop preventive and predictive maintenance plans.
Likewise, training in Reliability Centered Maintenance encourages the adoption of a proactive approach in maintenance management, promoting continuous improvement and optimization of processes, which leads to greater efficiency and operational profitability.
Reliability Centered Maintenance training covers several components
Understand asset criticality: Training staff to identify and assess asset criticality allows them to prioritize maintenance efforts based on risk and consequences.
Failure Modes and Effects Analysis (FMEA): Educating personnel on these techniques helps them identify potential failure modes, their causes, and the effects on equipment performance.
Risk Assessment: Training in risk assessment methodologies enables maintenance teams to assess the severity, probability, and detectability of potential failures.
Selection of maintenance strategy: Guides the staff in choosing the optimal maintenance strategies, such as preventive, predictive or corrective maintenance, based on the criticality of the equipment and the results of the risk assessment.
Continuous Improvement: Training staff on these principles fosters a culture of continuous evaluation and refinement of maintenance strategies, leading to greater operational efficiency.
Impact on operational efficiency
Reduced downtime: Properly trained and qualified personnel can identify potential failures before they occur, allowing timely maintenance interventions and minimizing unplanned downtime.
Optimized resource allocation: Empowered teams can allocate resources more efficiently, focusing efforts on critical assets and using maintenance budgets effectively.
Improved planning and scheduling – Develop well-informed maintenance plans and schedules, leading to smoother execution and fewer disruptions.
Training in Reliability Centered Maintenance contributes to the extension of the useful life of assets through:
Proactive Maintenance: Training equips personnel to anticipate and address problems before they escalate, thus preventing premature degradation of assets and extending their operational useful life.
Preservation of design intent: Properly trained and certified teams ensure that maintenance activities align with the original design intent of the equipment, reducing the risk of deterioration and ensuring long-term performance.
Data-Driven Decision Making: RCM-trained personnel rely on data and analytics to make informed decisions, leading to optimized maintenance strategies that promote asset longevity (Figure 1).
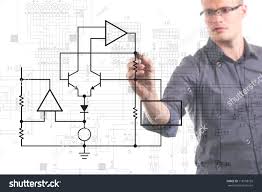
Application of Reliability Centered Maintenance in real world scenarios
The training provides practical examples and case studies that allow individuals to apply the principles and techniques in real-world settings.
This hands-on experience helps them develop the skills and confidence to implement successfully in their organizations.
Collaboration and Communication Skills: This training often involves group exercises and discussions, fostering collaboration and improving communication skills among participants.
These skills are essential for effective teamwork during studies, as they involve cross-functional collaboration and the sharing of knowledge and experience.
Reliability-Centered Maintenance is used to determine what failure management strategies need to be applied to ensure that a system achieves desired levels of safety, reliability, environmental robustness, and operational readiness in the most cost-effective manner.
This may mean identifying various maintenance actions. For example, one of the most useful products of an analysis is the identification of technically defensible proactive maintenance tasks, such as scheduled restore tasks.
In addition, it can generate other results that also contribute significantly to the safe and reliable operation of assets. These may include design modifications, changes to a training program, identification of new operating and emergency procedures, or modifications to technical manuals (Figure 2).
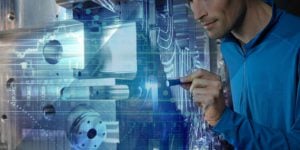
Optimization of training programs for specialists in Reliability Centered Maintenance
to. Comprehensive Curriculum: Training should cover a wide range of topics, including RCM principles, equipment analysis, failure modes, decision logic, and implementation strategies.
b. Practical Exercises: Practical exercises, case studies, and simulations allow scholars to apply theoretical knowledge to real-world scenarios, improving their problem-solving skills.
c. Industry Specific Training: Tailoring training to specific industries ensures that analysts understand the unique challenges and requirements of their respective industries.
d. Collaboration and Communication Skills: Technicians must receive training in effective communication and collaboration to work seamlessly with multidisciplinary teams.
and. Continuous Learning: Maintenance practices and technologies evolve over time. Instructed teams must engage in continuing education to stay current on industry advancements.
Absence of education! For Reliability Centered Maintenance
Sounds simple, right? You don’t know what you don’t know. Just train people and you’ll be fine, right?
Well no. However, a lack of education can manifest itself in multiple ways, such as the mistaken belief that reliability is limited to maintenance functions, a narrow perspective focused on individual goals that overlooks the holistic view, and lack of commitment due to the inability to perceive the inherent value of the program.
Many professionals do not understand what is required, what the expected results are, and what happens within the realm of reliability. Concepts related to developing reliability strategies may be completely unfamiliar to those unfamiliar with reliable maintenance, and may not be accepted or considered.
The rapid development of IoT technologies has enabled various possibilities to improve Reliability Centered Maintenance and asset management. One of the main objectives of IoT technologies is to simplify processes, improve system efficiency and add more value to an organization (Figure 3).
Being able to keep up with this accelerating pace of technologies and their ever-increasing uses has become a key issue for an aging or uninformed workforce, where a new and new sensor, program, process, and even operating strategy sparkles seem to pop up every day.
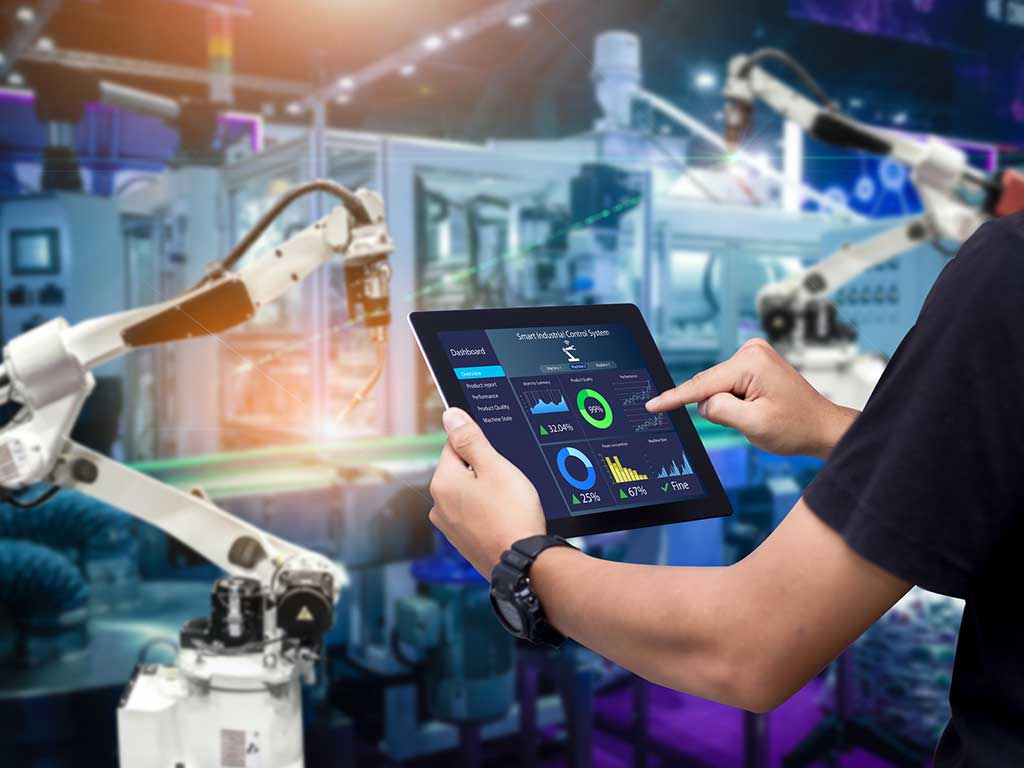
In some cases, the obstacle arises due to a lack of understanding of the need to implement the IoT. For example, in the process of determining which data sources need to be monitored, it may be necessary to perform detailed process mapping and define critical assets or relevant process information.
The constant search for new technologies to find better ways to acquire new knowledge often requires diligence in learning the seemingly endless types of programs and platforms applied to Reliability Centered Maintenance.
For most members of the organization, the interest in learning or assimilating the technical details of the IoT, beyond its immediate usefulness, is usually limited. The lack of an effort to level the IoT knowledge can create a constant obstacle in the implementation, causing a series of insurmountable obstacles.
During the process of figuring out what data needs to be analyzed and how, there is a critical step in understanding which data points are important. With the advanced analytical tools available, data requirements increase, extracting data that was previously not considered necessary.
Lack of education on this can derail your implementation if people do not understand the new techniques and technologies available for the process of evaluating data for faults.
From an educational perspective, it is especially frustrating when failures to implement reliability-centered maintenance training occur due to a lack of awareness or a refusal of individuals to recognize the impact they have within an organization.
Conclusion
The optimization of expert training programs is essential to guarantee the successful implementation of Reliability Centered Maintenance practices. A comprehensive curriculum, hands-on exercises, industry-specific training, and continuous improvement are key components of an effective training strategy. By investing in well-educated professionals, organizations can improve equipment reliability, minimize downtime, and improve overall operational efficiency.
References
- John Moubray, Reliability-centred Maintenance, second edition 1997.
- Uptime Elements Implementation Guide / Enabling the Sustainability and Reliability Journey • 2nd Edition. Publisher: Reliabilityweb, Inc. ©2022.
- Chapter 4. Reliability-Centered Maintenance author: Darrin Wikoff Maintenance Engineering Handbook.