Reliability Centered Maintenance (RCM) is a proactive strategy that optimizes the life cycle of assets, ensuring maximum availability and performance at the lowest cost. Instead of reacting to failures, RCM anticipates and prevents problems, minimizing operational risks.
The purpose of this article is to promote Reliability Centered Maintenance (RCM) as a key strategy to optimize assets and reduce risks.
How do we achieve this?
- Thoroughly understanding the asset: We begin by understanding the critical function of each piece of equipment and the impacts of its potential failures. We identify its weak points and evaluate the nature and consequences of each failure to prioritize maintenance actions.
- Anticipating failures: We simulate equipment operation under different conditions to anticipate possible failure modes and their root causes.
- Customized maintenance tasks: We design specific maintenance tasks for each piece of equipment, based on a detailed analysis of its needs and risks.
- Optimizing maintenance frequency: We determine the ideal frequency of maintenance tasks to maximize reliability and minimize costs.
- Leveraging technology: We use advanced technologies such as condition monitoring to detect early signs of deterioration and prevent catastrophic failures.
- Learning from experience: Every failure is an opportunity for improvement. We analyze root causes and continuously adjust our maintenance strategies.
Benefits of Reliability Centered Maintenance (RCM)
RCM offers a transformation in asset management, providing the following key benefits:
- Production optimization: By minimizing unscheduled downtime and maximizing equipment availability, RCM ensures greater operational continuity and thus increases production.
- Cost reduction: Through the elimination of unnecessary maintenance tasks and the optimization of resource usage, RCM generates significant savings in operating costs.
- Improved safety: By proactively identifying and mitigating potential risks of failure, RCM contributes to a safer working environment, reducing the likelihood of accidents and incidents.
- Extending the useful life of assets: Preventive maintenance based on the actual condition of equipment prolongs its useful life, delaying the need for investments in replacements.
- Data-driven decision-making: RCM provides accurate and up-to-date information on the condition of equipment, enabling more informed and strategic maintenance decisions.
- Increased efficiency: By focusing on the maintenance tasks that really add value, RCM optimizes processes and improves the overall efficiency of the operation.
RCM represents a significant evolution in asset management, moving from a reactive to a proactive approach. By investing in equipment reliability, organizations gain a tangible return in terms of increased productivity, reduced costs, improved safety and process optimization.
There is extensive evidence to support the exceptional results achieved through the correct implementation of the RCM methodology, which makes clear its effectiveness and extremely high cost-benefit ratio. In the words of John Moubray, author of the worldwide best-selling book “RCMII”:
“The author and his associates have helped RCM companies in more than 1,500 sites spanning 44 countries and in almost every form of organized human endeavor. We have found that when RCM has been properly applied by well-trained people working on clearly defined and properly managed projects, the analyses generally pay for themselves within two weeks to two months. In fact, this is a very quick payback.”
Successfully implementing a Reliability Centered Maintenance (RCM) program requires three fundamental pillars:
- Sound methodology: Apply RCM in a rigorous manner, following the established guidelines and adapting them to the particularities of each equipment and process.
- Skilled team: To have a team of professionals with solid knowledge in RCM, capable of analyzing data, identifying failure modes and proposing effective solutions.
- Leadership and commitment: Obtain the support and commitment of top management to ensure the allocation of resources, the clear definition of objectives and the monitoring of results.
Most companies are hesitant to initiate an RCM project due to the perception that the benefits are not immediate. However, it is important to note that the long-term results are significant and can generate a considerable return on investment. Lack of time and resources, combined with the urgency to address immediate problems, are common barriers.
Parallel RCM with root cause analysis (RCA)
Many organizations are too busy resolving day-to-day equipment failures that it will be difficult to divert resources into RCM. This is where it becomes apparent that as we move forward with RCM, we should perform some RCAs for equipment with a high recurrence of failures that impact operations. Any Pareto analysis will give us a hierarchical list of these equipment.
A well conducted RCA process on these problematic equipment will lead to the eradication of the recurrence of failures, only if we solve the tangible causes that generate them, but also the organizational or latent ones. In this way, the organization will be strengthened, teamwork will be significantly improved and, above all, resources previously spent on correcting failures will be freed up.
RCM failure patterns
For decades, maintenance was based on the premise that historical failure records were sufficient to predict component life and schedule preventive maintenance just prior to impending failure. This traditional view, prevalent until the mid-20th century, assumed a linear relationship between the age of equipment and its probability of failure, suggesting that frequent intervention guaranteed greater reliability.
However, this perspective changed radically with the publication of Howard Heap and Stanley Nowlan’s study in 1978. Their research, condensed in the Reliability-Centered Maintenance report, revealed the existence of six patterns of failure that challenged established beliefs. These patterns demonstrated that the relationship between the age of equipment and its probability of failure is much more complex and variable than previously thought.
By understanding these failure patterns, it became clear that a maintenance strategy based solely on the age of a piece of equipment and frequency of interventions was insufficient. RCM emerged as a more effective alternative, proposing an approach based on the critical function of each component and the identification of the most likely failure modes. Instead of performing indiscriminate preventive maintenance, RCM makes it possible to optimize maintenance tasks and significantly reduce operating costs, while improving equipment availability and reliability.
Understanding failure patterns: The key to Reliability Centered Maintenance (RCM)
The effectiveness of a maintenance strategy is based on a deep understanding of how equipment fails. Just as a doctor diagnoses a disease through its symptoms, an RCM expert identifies the characteristic failure patterns of each component to implement the most appropriate maintenance actions.
Why is it important to identify failure patterns?
Imagine trying to avoid a failure without knowing its cause: it would be like shooting at random. By identifying failure patterns, we can establish more accurate preventive and predictive maintenance strategies, thus optimizing the availability and reliability of our assets.
Major failure patterns and their significance
In the context of RCM, several frequently recurring failure patterns have been identified. Each of them represents a characteristic behavior of the equipment throughout its service life:
A. Bathtub Pattern: Starts with a high initial failure rate (due to manufacturing or installation defects), followed by a period of stability and concludes with a gradual increase in failures due to wear and tear.
B. Deterioration pattern: Characterized by a relatively low failure rate at the beginning, which gradually increases until reaching a point of catastrophic failure.
C. Fatigue pattern: Failures occur gradually and progressively, often due to cyclic loading or vibration.
D. “Best new” pattern: Equipment exhibits a low failure rate initially, but then experiences a higher random failure rate.
E. Random pattern: The failure rate remains relatively constant over the life of the equipment.
F. Infant mortality pattern: Characterized by a high initial failure rate, followed by a more stable failure rate.
Why is it important to know these patterns?
By identifying the failure pattern of a specific component, we can:
- Employ appropriate maintenance tasks: For example, for a wear pattern, we can implement a preventive lubrication and replacement program.
- Optimize maintenance intervals: We can adjust the frequency of inspections and maintenance tasks according to the failure pattern.
- Reduce costs: By avoiding performing unnecessary maintenance tasks and focusing on those that have the greatest impact on reliability.
- Improve availability: Anticipating failures and reducing downtime.
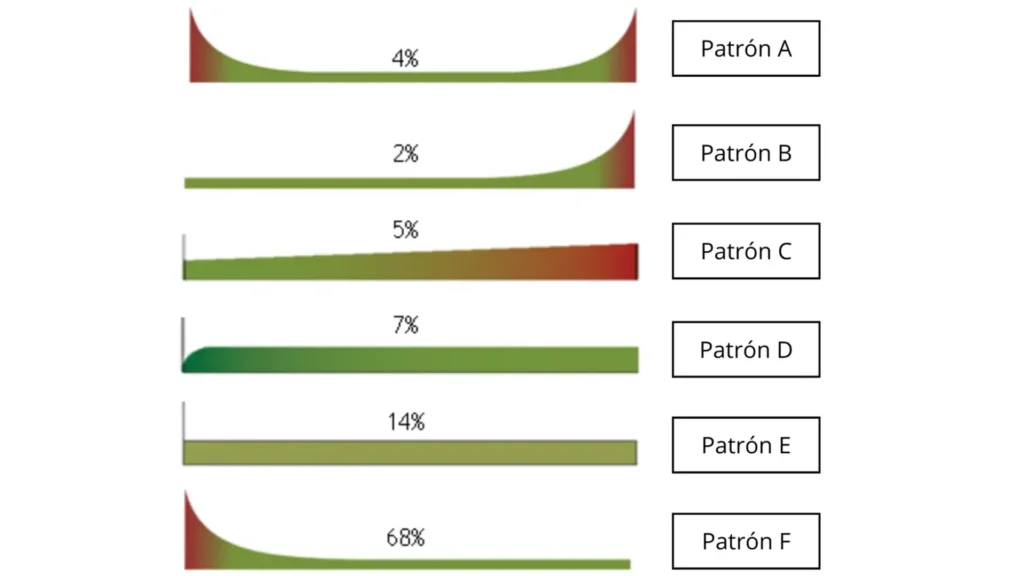
Knowledge of failure patterns is the cornerstone of implementing a truly effective reliability-focused maintenance program. By understanding the underlying mechanisms that lead to failures, we can anticipate adverse events, optimize preventive maintenance tasks and maximize the useful life of our assets, significantly reducing operating costs and improving equipment availability.
Conclusions
We subscribe to the words of John Moubray “Since RCM was developed it has become apparent that there is no other comparable technique for identifying the true and safe minimum of what must be done to preserve the functions of physical assets. As a result, RCM has been used by thousands of organizations spanning almost every major field of organized human endeavor.”
Applying RCM is the best cost-benefit decision for any organization and even for any criticality of equipment. Its benefits in process optimization will far outweigh the resources and time spent. Experience has given us the opportunity to apply in parallel in RCA to take some “low-hanging fruit” and stop the high recurrence of failures of problematic equipment and consolidate teamwork.
References
Own source