Reliability Centered Maintenance (RCM) is a widely recognized and widely used methodology for developing industrial equipment maintenance plans to ensure equipment functions to the satisfaction of the user or owner.
RCM ensures an effective maintenance program that focuses on maintaining the original reliability inherent in equipment as a process used to determine what must be done to ensure that any asset continues to do what its users want it to do within its limits. operational.
In this context, the case of the acquisition of a wet gas compressor for the Catalytic Cracking (FCC) unit of an oil refinery is presented below.
Success story in the application of Reliability Centered Maintenance
The compressor purchased, after a long bidding process that will guarantee quality at the best price, once in the plant is installed strictly following all established standards and guidelines. Each step was supervised by personnel from operations and maintenance with adequate training, evaluating critical aspects of the equipment, ensuring that each component was assembled precisely, with the aim of achieving optimal and sustainable performance; which, added to its robust design, will guarantee the reliability of this highly critical equipment for the plant.
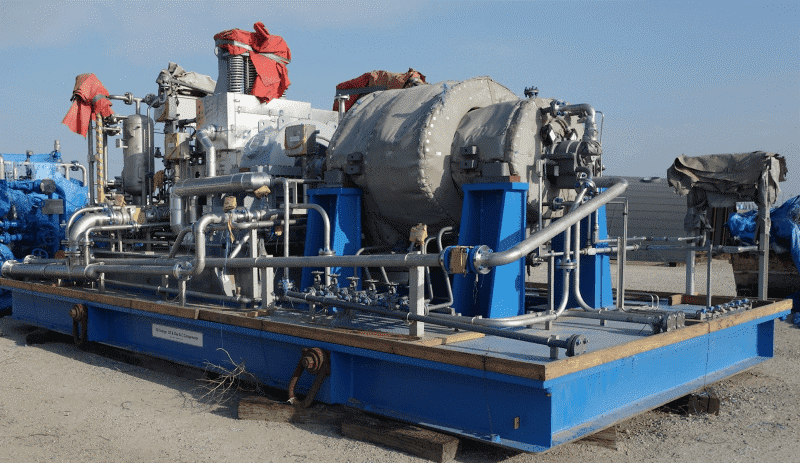
During the review of the maintenance manuals with the purpose of planning future interventions in this equipment, which will operate continuously during the 4 years of the plant’s run, it was discovered that the preventive maintenance tasks must begin after 6 months. with the revision of bearings, followed by more invasive activities that require stopping the equipment after a year of operation.
This information led even the most experienced experts in this equipment to question whether the equipment, manufactured by one of the most recognized manufacturers in the world, would be able to maintain its performance during the entire 4-year run.
Fortunately, the answer to this question was yes. There are numerous Catalytic Cracking (FCC) plants that use the same model and manufacturer, which has been corroborated through references collected since the initial bidding phases.
So why aren’t the manuals adapted for the 4-year run? The reason is that the manufacturer provides only a standard manual and expects the user, like most, to adjust it according to their specific operating environment.
Well, how is this adaptation to the real context of operation of this equipment carried out?
Here questions arise about the possible alternatives to achieve it.
- Skipping the invasive activities of 6, 12, 18, 36 months and taking everything to 48 months?
- Rethink the whole maintenance thing, including activities that make up for those that can’t be done?
This organization acted correctly, following the approach adopted by the main leading companies globally. It brought together a team of experts from various areas, such as operations, maintenance in all its specialties, engineering, dynamic teams, safety and the environment. They were given the task of developing an optimal maintenance plan that would ensure optimum reliability and availability of this compressor.
Today, and since a few years ago, the most appropriate methodology and luckily selected for this mission, is RCM or MCC: Reliability Centered Maintenance.
The process is very laborious and takes a long time. For this reason, most of the time it can only be applied to highly critical computers. They lasted 2-3 months, meeting 2-3 times a week, accompanied by an adviser and an appropriate methodology, but with a largely satisfactory result, which could be summarized as:
- Achievement of an optimal maintenance plan, agreed upon by the entire team and where each one expressed their agreement with all the listed activities and their frequencies.
- Reinforced teamwork: now there is a team of committed people, who support each other, where synergy and empathy is very visible.
- During the process, some aspects of the day-to-day operation of the equipment were resolved, such as communication problems, understanding of processes and procedures, and even some design aspects were resolved.
- All maintenance personnel now know the most important aspects of the operating processes of the compressor and its auxiliary equipment, which will allow them to provide you with better service and attention.
- Operations personnel now have a better understanding of maintenance aspects, which they were previously unaware of and limited in their interaction with personnel from different specialties.
- All the actions of the Maintenance and Operations departments have full traceability, prioritization and justification.
The experience was totally positive. At that refinery today no one would question the large number of man hours consumed by this project. The refinery continued to successfully apply RCM to the rest of its critical equipment. He even applied RCM to medium-critical teams, taking advantage of advance work (templates) for high-critical teams.
References
Own source.
About the Author:
Emilio Trejo Petit, Mechanical Engineer specializing in Reliability of Industrial Systems. He has 17 years of experience in the Venezuelan oil industry and more than 15 years in the area of consulting and courses in Root Cause Analysis, Reliability Centered Maintenance, Reliability Engineering, in which he has taught courses to more than 2000 people and participated in more than 100 projects in Venezuela, Mexico, Colombia, Peru, Ecuador, in the main oil companies in the region and in companies such as cement, food, automotive, among others.