Table of Contents
- Introduction
- What is Reliability Centered Maintenance?
- How does the method contribute to the optimization of maintenance resources?
- How can RCM help extend equipment life?
- Economic benefits of RCM in reducing maintenance costs
- Strategies to effectively implement RCM and reduce maintenance costs
- Conclusiones
- References
Introduction
Maintenance costs have become a priority focus in an increasingly competitive business environment, where operational efficiency is key for organizations in the energy, industrial, and related sectors. To achieve these objectives, Reliability Centered Maintenance (RCM) has proven to be a powerful tool capable of optimizing resources, reducing costs, and extending equipment life.
Reliability Centered Maintenance not only focuses on maintaining equipment reliability but also optimizes available resources, minimizing operating costs and extending asset life. This article explores how to effectively implement this approach to maximize operational efficiency and reduce costs.
What is Reliability Centered Maintenance?
Reliability Centered Maintenance is a methodology that seeks to ensure maximum equipment reliability through the implementation of predictive and preventive maintenance strategies. Unlike traditional methods, which rely on time or usage to schedule interventions, it uses asset-specific data and detailed failure mode analysis to determine the most effective maintenance tasks.
This approach allows you to identify and prioritize interventions that are critical to the operation, avoiding unnecessary repairs and minimizing unplanned downtime. By focusing on what really matters, it significantly reduces maintenance costs and improves equipment reliability.
How does the method contribute to the optimization of maintenance resources?
The implementation of the method is based on a structured approach that seeks to optimize the use of available resources. By analyzing failure modes and their consequences, organizations can identify which equipment requires priority attention and which can operate safely without immediate intervention.
This prioritization allows companies to allocate their resources more effectively, focusing on the tasks that have the greatest impact on equipment reliability and, ultimately, on maintenance costs. For example, avoiding unnecessary maintenance interventions on non-critical equipment frees up resources that can be used in areas where they are really needed.
It promotes the adoption of predictive and preventive maintenance practices that anticipate failures before they occur, avoiding costly repairs and reducing downtime. This approach not only optimizes resources but also contributes to operational stability, ensuring that equipment operates reliably for longer.
How can RCM help extend equipment life?
One of the most significant benefits of the methodology is its ability to extend equipment life. By implementing predictive and preventive maintenance strategies based on failure mode analysis, it is possible to detect and correct problems before they become major failures. This not only avoids costly repairs but also extends the useful life of assets by keeping them in optimal operating condition.
It also fosters a culture of continuous improvement, where organizations are constantly looking for ways to improve their maintenance practices and optimize the performance of their assets. By identifying failure patterns and taking preventive action, the effects of wear and aging of equipment can be minimized, helping to extend its useful life and reduce long-term operating costs.
In addition, by improving equipment reliability, it helps companies maintain a more stable and efficient operation, which translates into a reduced need for equipment replacement and reduced maintenance costs associated with asset renewal.
Economic benefits of RCM in reducing maintenance costs
Implementing the method not only improves operational efficiency but also has a direct impact on costs. By focusing on failure prevention and resource optimization, organizations can achieve significant savings in their daily operations.
Task optimization
- Elimination of unnecessary tasks: By analyzing equipment function and failure modes, non-value-added maintenance tasks are identified and eliminated, thereby reducing the time and resources spent on these activities.
- Focus on critical tasks: Efforts are concentrated on maintenance tasks that have the greatest impact on equipment availability and reliability, thus ensuring that resources are used efficiently.
Reduction of unexpected failures
- Increased equipment availability: By performing necessary maintenance before catastrophic failures occur, equipment downtime is reduced and production losses are minimized.
- Collateral damage prevention: Unexpected failures can cause collateral damage to other equipment or facilities, resulting in additional repair and replacement costs. This method helps prevent such damage.
Figure 1 shows a pump station repaired and upgraded with technology to eliminate unexpected failures as a result of an RCM methodology analysis.
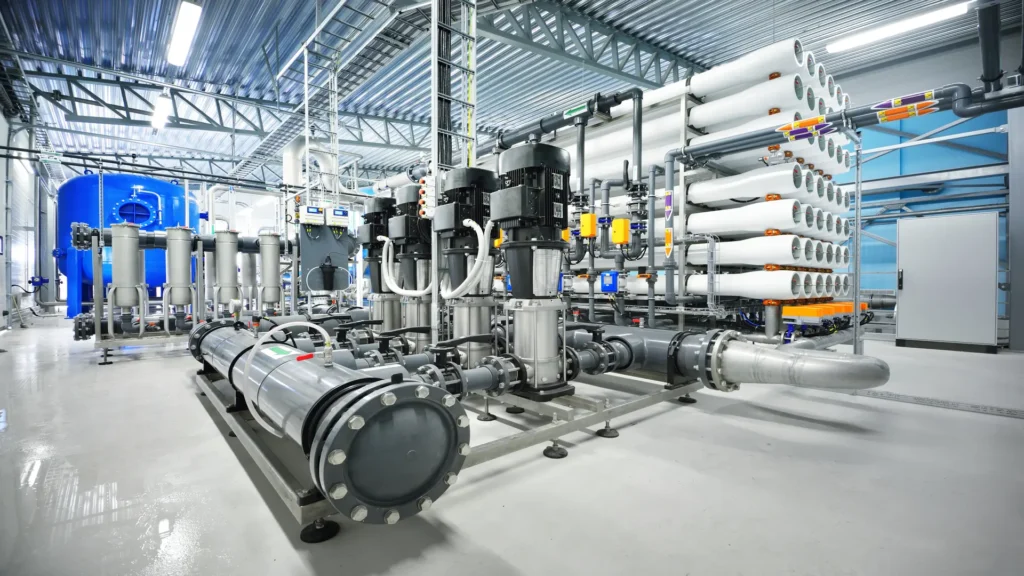
Extending the useful life of equipment
- Early detection of incipient failures: Allows incipient failures to be detected and corrected before they become major failures, thus extending equipment life and reducing the need for premature replacements.
Reduction of spare parts and labor costs
- Spare parts planning: By knowing the maintenance needs of each piece of equipment, spare parts purchases can be planned more efficiently, avoiding the purchase of unnecessary components or stock-outs.
- Labor optimization: Focusing on critical tasks and eliminating unnecessary ones optimizes the use of maintenance labor, reducing labor costs.
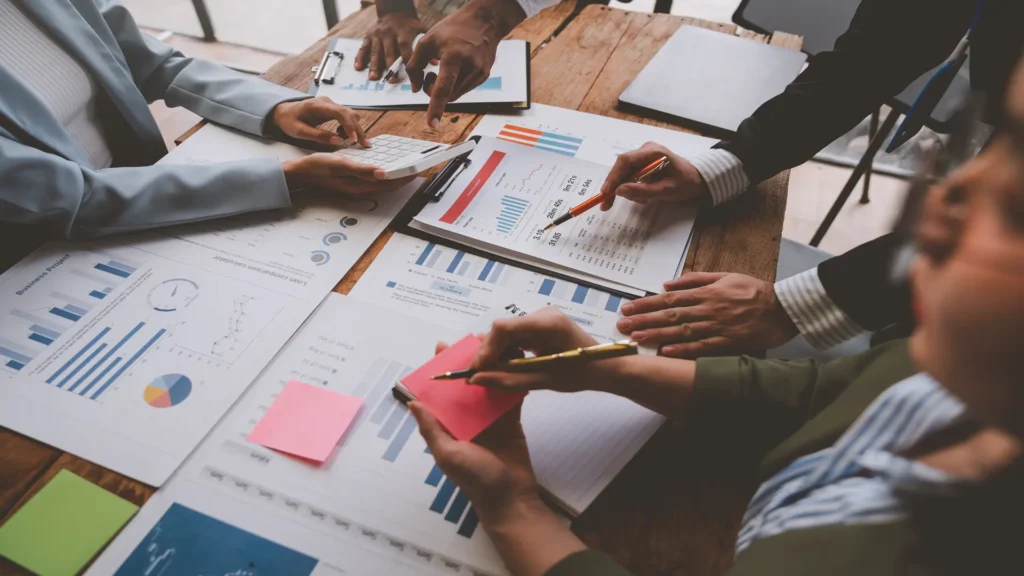
Improved safety
- Risk identification: Allows to identify the risks associated with each piece of equipment and to establish the necessary safety measures to minimize them.
- Reduction of accidents: By reducing unexpected failures and improving equipment availability, the risk of occupational accidents is reduced.
This methodology is a powerful tool for reducing maintenance costs by optimizing tasks, preventing failures, extending equipment life, and improving safety. By implementing this methodology, organizations can achieve greater efficiency in their operations and increased profitability.
Strategies to effectively implement RCM and reduce maintenance costs
Implementing the method effectively requires a systematic and well-planned approach. Below are some key strategies to maximize the benefits:
Senior management commitment
- Visibility: Ensure that senior management understands the benefits of the tool and communicates it throughout the organization.
- Resources: Allocate the necessary resources (personnel, budget, technology) to carry out the implementation.
- Clear goals: Establish clear goals and objectives for the tool program, aligned with the overall objectives of the organization.
Maintenance team training
- Knowledge: Train maintenance personnel in the principles and tools of the methodology.
- Skills: Develop the skills necessary to perform failure mode analysis, criticality analysis, and other techniques specific to the method.
- Mindset: Foster a culture of continuous improvement and problem-solving.
Selection of critical assets
- Clear criteria: Establish clear criteria to identify critical assets requiring focus.
- Criticality analysis: Perform a criticality analysis to assess the impact of each asset failure on production and costs.
- Prioritization: Prioritize assets according to their criticality and improvement potential.
Data collection
- Historical information: Collect historical data on equipment failures, maintenance, and performance.
- Management systems: Implement computerized maintenance management systems (CMMS) to store and analyze data.
- Key indicators: Define key performance indicators (KPIs) to measure the success of the program.
Failure Mode and Effects Analysis (FMEA)
- Failure mode identification: Identify all possible failure modes for each critical asset.
- Consequence assessment: Evaluate the consequences of each failure mode in terms of cost, safety, and availability.
- Maintenance task development: Develop preventive and predictive maintenance tasks to mitigate critical failure modes.
Development of maintenance tasks
- Risk-based tasks: Develop maintenance tasks based on risk analysis and asset criticality.
- Interval optimization: Optimize maintenance intervals to maximize availability and minimize costs.
- Detailed procedures: Develop detailed and easy-to-follow maintenance procedures.
Implementation and follow-up
- Implementation plan: Develop a detailed implementation plan and establish a timeline.
- Communication: Communicate the implementation plan to all personnel involved.
- Tracking and adjustment: Monitor program performance and make adjustments as needed.
Use of specialized software
- Analysis tools: Use specialized software to perform data analysis, simulations, and optimizations.
- Information management: Centralize program information on a single platform.
For more content on the topic, watch the following video on reducing maintenance costs, with Tor Idhammar from IDCON Reliability and Maintenance.

Reducing Maintenance Costs the Right Way.
In summary, the successful implementation of this methodology requires a holistic approach that involves the entire organization. By following these strategies, companies can maximize benefits and achieve greater efficiency and reliability in their operations.
Conclusiones
Reliability Centered Maintenance is a fundamental strategy for any organization wishing to optimize resources, improve equipment reliability, and reduce maintenance costs. By implementing predictive and preventive maintenance practices based on data and detailed asset analysis, it offers a comprehensive approach to maximize operational efficiency.
The key to the success of the method lies in careful planning, ongoing staff training, and a commitment to continuous improvement. The benefits it offers, both in terms of cost savings and increased reliability, make this methodology a valuable investment for organizations in the energy, industrial, and related sectors. By adopting this methodology, companies not only improve their profitability and competitiveness in the marketplace but also ensure a more sustainable and efficient operation in the long term.
Implement RCM today and maximize your company’s operational efficiency!
References
Own source