Table of Contents
Quality management in the supply chain is implemented with the aim of improving operational performance and reducing risks associated with regulatory, strategic, financial, operational, reputational and legal aspects. It is applied to detect and minimize risks in the supply network, identifying quality problems as soon as possible through comprehensive supervision of products and processes.
Quality can become an issue at any point throughout the supply chain process, so it is important for companies to detect it as early as possible to avoid cost overruns and mitigate risks to their reputation, compliance, security, and financial bottom line .
Poor quality management in the supply chain can result in higher production and distribution costs, and contribute to lost revenue due to unplanned downtime, delays.
However, maintaining a high level of quality in complex global supply networks is challenging. As companies increasingly rely on complex and globally distributed supply partner networks, limitations in visibility into this supply chain make it difficult to manage quality in the supply process.
Organizations need a way to gain greater visibility into partner performance and facilitate seamless information sharing and collaboration to ensure product and process quality throughout the value chain.
Quality management in the supply network helps manufacturing companies to ensure that quality is built into every product and every step of the production and distribution processes. It helps hold third-party sourcing partners accountable for the quality of their products and enables them to better protect the integrity of their brand, while increasing profitability.
Supply chain optimization
Supply chain optimization involves adjusting operations so that they reach their maximum efficiency. This is achieved through the consideration of indicators, such as operating expenses and inventory yields. The primary objective is to provide products to customers at the lowest possible total cost while maintaining high profit margins. To achieve this goal, managers must balance the costs associated with manufacturing, inventory management, transportation, and meeting customer expectations.
Given how complex the supply chain optimization process is, it is advisable to approach it as a long-term activity, where changes in costs and services are implemented over time, taking into account the variations in the costs of the resources, changes in carriers, customer demographics, and other factors that require constant analysis.
When a company is considering a merger or acquisition, or is concerned about financial results, supply chain optimization is the first area to look at. During the investigation, the organization can identify various causes of problems, such as high transportation costs, suboptimal service levels, or dissatisfied suppliers throughout the supply chain.
As the number of providers increases, expectations can change or grow unexpectedly. The response to high market demand has led e-commerce companies to get involved in direct selling without integrating it with other channels. This approach often results in higher costs and fragmented management. Supply chain optimization is what will enable better standards to be set throughout the supply chain.
Supply Chain Optimization Process
The supply chain optimization process starts with a systematic and comprehensive analysis based on forecast demand. From this, a production and inventory plan is created that is based on the existing forecast. This process covers aspects such as incoming raw materials or inputs, the manufacturing process, transportation, and distribution.
Most companies typically work with professional service providers or consultants to implement the necessary technology and organizational changes that deliver tangible, real-world results.
Phases of the supply chain optimization process
Phase 1. Design: Understands network design processes, such as the location of storage facilities, the flow of products between suppliers and customers, and the strategic goals of manufacturing operations, including forecasting demand, establishing supply and planning and scheduling.
Phase 2. Planning: This second stage focuses on creating a strategic implementation, inventory planning, and asset coordination to optimize the delivery of products, services, and information between suppliers and customers. The purpose is to balance supply and demand.
Phase 3. Execution: Finally, this last part of the optimization process deals with all applications and systems related to execution, such as inventory and warehouse management, facilities management, transportation efficiency, and international trade management. It also considers execution support applications that play a supporting role in the supply chain process, such as real-time decision-making systems, supply chain visibility, and order management systems.
A supply chain network is a dynamic ecosystem. As it grows, so do the risks and uncertainty associated with activities across the chain. Factors that affect performance can be internal or external and can be driven by competition or the business environment. Given the wide variety of factors, various supply chain models have emerged. An organization’s choice of a specific model is based on the specific supply chain optimization issues that are particular to its business.
There are a number of components that are commonly part of an organization’s supply chain optimization model, such as inventory, product receiving and storage, order processing, dispatch and distribution, and customer service systems. to the client. These elements, when combined, allow a business to address most supply chain optimization issues and create a seamless and comprehensive operation that ensures seamless work with all trading partners.
Supply Chain Optimization Techniques
There are several key techniques used to achieve supply chain optimization:
- Cost optimization: The objective of this technique is to find opportunities to minimize expenses and maximize efficiency throughout the chain. It consists of identifying areas in which operating costs can be reduced. A detailed analysis of the different cost segments in the supply chain, such as those related to ordering, warehousing, transportation, and inventory management, is performed.
- Inventory optimization: Focuses on achieving the right balance in inventory levels. It consists of analyzing demand and supply, using advanced models and algorithms, to determine the optimal inventory levels that allow meeting the needs of customers without incurring excess inventory or shortage. Inventory optimization helps minimize storage costs and the risks associated with overstocking or understocking.
- Route and Transportation Optimization: Involves evaluating different transportation options, alternate routes, and shipping modalities to minimize costs and maximize efficiency in product delivery. The use of transportation management systems and real-time tracking technologies helps to optimize the planning and execution of shipments.
- Collaboration with Supply Chain Partners: Effective collaboration with suppliers, manufacturers, distributors, and other supply chain partners is essential to optimizing product flow. Sharing information in real time, establishing clear agreements and working closely with partners allows for better coordination, reduced response times and optimization of processes throughout the chain.
- Use of advanced technology: The application of technologies such as the Internet of Things (IoT), artificial intelligence (AI) and data analytics can help optimize the supply chain. These technologies make it possible to collect and analyze large volumes of data in real time, facilitating decision-making based on accurate information and automating repetitive tasks.
Importance of quality management in the supply chain
The efficient management of the supply chain plays a fundamental role for several reasons. First, it helps reduce costs, avoid waste, and optimize production cycle time. Currently, the industry standard is based on the implementation of a “just in time” supply chain, where retail sales act as an automatic signal for manufacturers to place replenishment orders. This allows store shelves to be quickly restocked as products sell out. However, further improvements can be achieved by analyzing data from supply chain partners.
By analyzing such data, three situations can be identified where effective supply chain management adds value to the cycle:
- Early identification of potential problems: By anticipating shortages before customers are faced with product shortages, manufacturers can avoid buyer dissatisfaction due to poor service. Through data analysis, you can anticipate these situations and take proactive measures to avoid inconvenience.
- Dynamic Price Optimization: Seasonal products have a limited shelf life and, at the end of the season, are often thrown away or sold at deeply discounted prices. However, through the use of analytical software and forecasting techniques, prices can be dynamically adjusted to meet demand and improve profit margins, even for durable products.
- Improved allocation of available inventory to fulfill orders: Analytical software tools help dynamically allocate resources and schedule work based on sales forecasts, actual orders, and promised delivery dates for materials cousins. Manufacturers can confirm a product’s delivery date at the time of ordering, significantly reducing errors in the order fulfillment process.
Quality management tools in the supply chain
Quality management in the supply chain requires the use of effective tools to ensure that products and services meet quality requirements and meet customer needs.
This management involves the evaluation and selection of reliable suppliers and the implementation of measures to ensure that suppliers meet quality requirements. Appropriate tools include supplier evaluation, supplier audits and the execution of measures that certify the quality of materials and supplies.
Some of these tools are described below:
- QA: It means the implementation of measures to ensure that products are consistently produced and meet quality requirements; For which, it is necessary to establish a series of measures that guarantee the quality of the products such as: Inspection, quality tests and measures that guarantee the availability of materials and supplies.
- Product delivery management: This methodology is applied to ensure that products are delivered in a timely manner and meet quality requirements.
- Data quality management: It refers to the application of measures that guarantee the use of accurate and reliable data used in the supply chain, here it is denoted the validation of data, data cleaning and the use of measures to guarantee the quality of the data used in the supply chain.
Increasingly, companies are using supply chain quality management data analytics to provide the information needed to quickly resolve problems and seize opportunities for competitive advantage.
Supply chain data analytics is a type of analysis designed to discover information about an organization’s supply chain by analyzing data from its various systems and applications.
Data can provide visibility into every link in the chain: procurement, inventory management, order management, warehousing, fulfillment, and shipping.
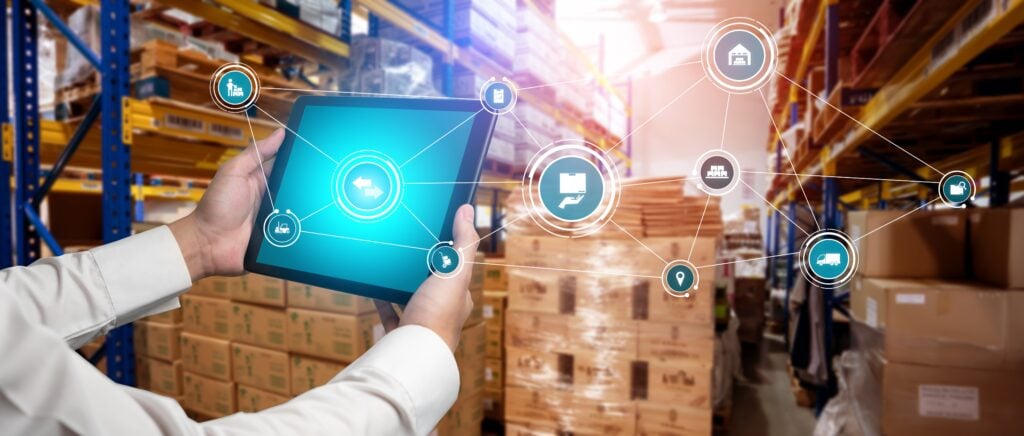
Due to the complexities involved in managing quality in the modern supply chain, there are many potential points of failure. If one link in the chain experiences a bottleneck or shutdown, the entire system following the point of failure will be affected.
Supply chain data analytics can help companies identify where they are vulnerable and how to avoid preventable problems. You can find ways to solve problems when they occur, and you can discover opportunities to streamline the supply chain and make it even better.
Future of supply chain optimization
Supply chain optimization in the future will be influenced by globalization, technology and increasingly empowered consumers. Supply chains of the future are expected to be able to self-regulate and take appropriate action, far exceeding current capabilities. Supply chain operators will use technologies such as artificial intelligence (AI)-based control towers to gain crucial performance insights and plan activities across the chain.
They will also be able to anticipate logistics cost and performance anomalies before they occur, and take advantage of automation at scale. These technologies will continue to transform supply chain optimization:
- Artificial intelligence: Intelligent and autonomous AI will improve inventory monitoring, achieving greater accuracy and reducing material waste.
- Internet of Things (IoT): Data collected by IoT sensors will provide detailed information on inventory location and status, enabling better decision making.
- Blockchain: This technology will guarantee authenticity, improve traceability and visibility, and increase trust in transactions carried out in the supply chain.
- Intelligent order management: Supply chains will be dominated by increased inventory visibility through better demand forecasting and automation, enabling more efficient order management.
- Quantum Computing: Quantum computing, with its unprecedented processing power, will solve problems that previously seemed intractable, opening up new opportunities to optimize the supply chain.
Conclusions
The main supply chain optimization techniques include cost reduction, inventory optimization, route and transportation optimization, collaboration with partners, and the use of advanced technology. By applying these techniques effectively, organizations can improve efficiency, reduce operating costs, and offer quality service to their customers.
Effective supply chain management is important to reduce costs, anticipate and fix problems, optimize prices, and improve inventory allocation. Through data analysis and the use of analytical tools, organizations can make proactive decisions that create value in all links of the supply chain.
References
Own source