Introduction
Materials procurement is a fundamental process in the management of industrial projects, where the quality of the materials purchased plays a crucial role in the success and safety of operations. Quality in materials procurement ensures that all components and supplies meet the necessary technical and regulatory standards, preventing failures and guaranteeing operational efficiency.
The objective of this article is to provide effective strategies for quality assurance in the materials procurement process, from the selection of suppliers to the final inspection of incoming products. We will address best practices and emerging technologies that can significantly improve this process.
Throughout the article, we will answer key questions such as: What is materials procurement, and What is quality control in purchasing? The concepts and fundamentals of these methodologies are important to understand how to implement a robust quality assurance system that optimizes resources, and minimizes the risks associated with the procurement of defective or inadequate materials.
Quality fundamentals in materials procurement
Definition: This process is defined as the procurement of goods and services required for the execution of industrial projects. This process includes identifying needs, selecting suppliers, negotiating contracts, and managing the delivery and storage of materials. The main objectives are to guarantee the availability of high-quality materials, at the right time and at the optimum cost, to ensure the good performance of the project.
Quality control in procurement: This refers to the activities and procedures implemented to ensure that purchased materials meet the required technical and regulatory specifications. This process includes the evaluation and selection of suppliers, inspection of materials received, and periodic audits to verify compliance with quality standards. The relevance of quality control in purchasing lies in the prevention of failures and defects that could compromise safety and operational efficiency.
Relationship between quality and procurement: Maintaining high-quality standards in the procurement process is significant to ensure the integrity and functionality of the materials used in the projects. The effective procurement process focuses not only on acquiring materials at the lowest cost, but also on ensuring that each material meets the necessary quality requirements.
This involves the implementation of a robust quality management system that encompasses all stages of the purchasing process, from the initial evaluation of suppliers to the receipt and verification of purchased materials. Integrating quality into the procurement of materials not only optimizes resources but also minimizes the risks associated with the acquisition of defective or unsuitable materials, thus ensuring the success and efficiency of projects.
Procurement management
Procurement plan: Consists of a detailed roadmap that guides the entire materials procurement process. It includes strategies and planning to ensure that all necessary materials are procured efficiently and meet the required quality standards. The effectiveness of this plan begins with the accurate identification of project needs, followed by the selection and evaluation of potential suppliers. In addition, consideration must be given to delivery scheduling, risk management, and ongoing evaluation of supplier performance.
Material requisition: A formal procedure by which the characteristics and quantities of materials required for the project are specified. This process includes the development of detailed technical specifications, verification of availability, and comparison of supplier options. The criteria for material selection should be based on quality, supplier reliability, cost, and delivery time. Proper execution of the material requisition ensures that only products that meet the project requirements are procured.
Purchasing strategies: These are techniques used to optimize the procurement of materials, ensuring both quality and efficiency in the process. These strategies include negotiating long-term contracts with reliable suppliers, making volume purchases to obtain discounts, and establishing collaboration agreements with suppliers to ensure a continuous, high-quality supply.
In addition, it is essential to implement a system of continuous supplier evaluation and auditing to ensure compliance with established quality standards. By optimizing purchasing strategies, companies can reduce costs, minimize risks, and ensure the availability of high-quality materials for their projects.
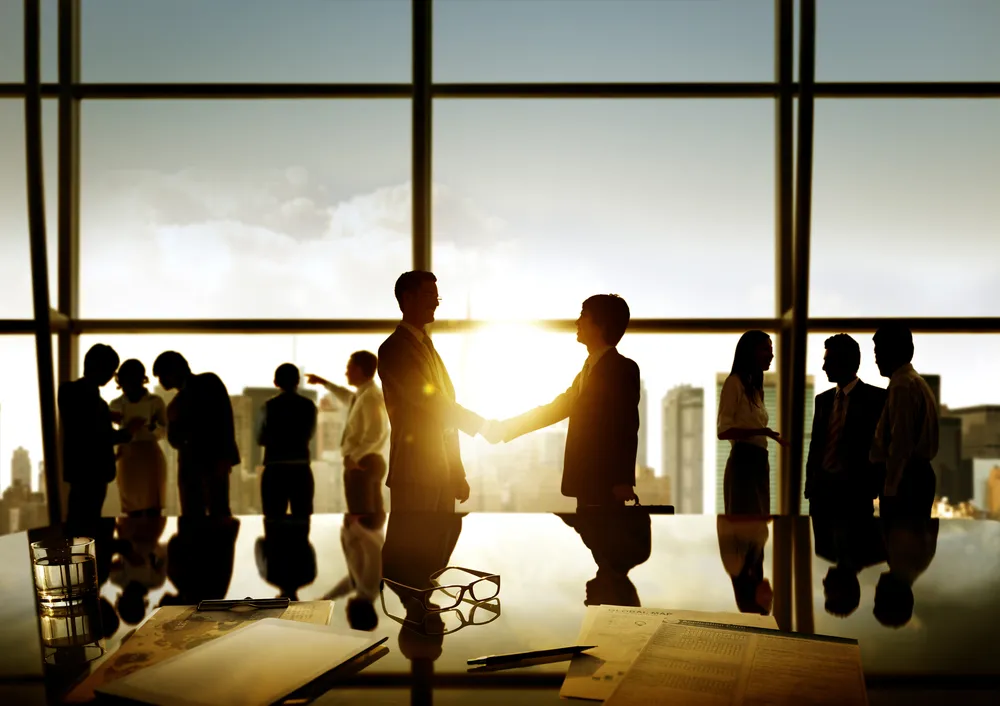
Quality control in purchasing
Control procedures: This process begins with the inspection and testing of materials, and includes verification that the materials received comply with the technical specifications established in the purchase orders. Physical, chemical, and mechanical tests are performed to ensure that the materials have the properties required for use in the projects. Inspections may be visual or through the use of specialized equipment to detect defects or inconsistencies that could compromise the integrity and functionality of the material.
Supplier evaluation: Ensuring quality suppliers is critical to maintaining the desired standards in the procurement of materials. Supplier evaluation involves a thorough review of their capabilities, performance history, regulatory compliance, and ability to meet technical specifications and delivery times.
Criteria for evaluation include the supplier’s technical capability, the quality of materials supplied, consistency in meeting deadlines, and the supplier’s financial stability. A formal supplier approval and periodic audit process ensures that only those suppliers that maintain high standards of quality and reliability are used.
Documentation and tracking: Continuous record-keeping and monitoring are necessary for an effective quality control system. Detailed documentation of each step of the purchasing process, from material requisition to receipt and testing, allows for rigorous tracking and traceability of materials. This includes keeping records of technical specifications, test results, supplier evaluations, and any issues or nonconformances detected.
A continuous monitoring system facilitates the identification of recurring problems and the implementation of timely corrective actions, thus improving the overall quality of the materials procurement process and ensuring consistency in the quality of materials received.
Quality assurance technologies and tools
Quality management software: The implementation of quality management software (QMS) provides a centralized platform for managing all aspects of quality control. An efficient QMS enables process integration, documentation, and audit trails, facilitating compliance with regulations and quality standards. The benefits of a QMS include improved coordination and communication between departments, reduced human error, and the ability to perform detailed analysis and real-time reporting on quality performance.
Advanced technologies: The use of technological innovations such as the Internet of Things (IoT) and Artificial Intelligence (AI) has revolutionized quality control in materials procurement. IoT enables continuous monitoring of materials throughout their lifecycle, from production to delivery, providing real-time data on their condition and status. AI is used to analyze large volumes of data, identify patterns, and predict potential failures in time, enabling proactive intervention.
Data analysis: These tools are critical for informed decision-making in quality assurance. Data analysis facilitates the identification of trends and recurring problems, enables the evaluation of supplier performance, and optimizes inspection and testing processes. Tools such as predictive analytics and Machine Learning help anticipate and mitigate risks, improving the quality and efficiency of materials procurement.
The implementation of these technological tools improves the accuracy and effectiveness of quality control and also provides a competitive advantage by enabling more agile, data-driven management.
Best practices in storage and control of materials and equipment
Handling and storage procedures
To maintain the quality of materials and equipment, it is necessary to implement effective handling and storage strategies. This includes the use of proper handling techniques to avoid physical damage, the implementation of controlled storage conditions to prevent degradation, and the use of labeling and coding systems to ensure traceability. Ongoing staff training in the best handling and storage practices is also critical to maintaining quality standards.
Inventory control
It is essential to prevent deterioration of materials and ensure quality. Techniques include inventory rotation using the FIFO method (First In, First Out), regular inspections of stored materials, and the use of automated inventory management systems to monitor storage conditions in real-time. These practices help detect any quality problems in a timely manner and implement corrective actions before materials are used on projects.
Case studies
There are numerous successful examples of the implementation of best practices in materials handling, storage, and control. For example, a construction company reduced its material spoilage losses by 30% by adopting an automated inventory management system. Another success story is a manufacturing plant that improved the quality of its final products by implementing strict storage and handling procedures, resulting in a significant decrease in customer complaints.
Benefits of effective quality assurance
Operational efficiency
Effective quality assurance significantly improves operational efficiency by optimizing production processes and reducing downtime. High-quality materials minimize defects and rework, allowing operations to run more smoothly and without interruption. This not only increases productivity but also enables better utilization of resources.
Cost reduction
Quality in materials procurement contributes to cost reduction by minimizing errors and waste of resources. Rigorous quality control ensures that only standard-compliant materials are used, avoiding costly failures in the final product. In addition, reducing defects and rework significantly reduces the costs associated with correcting problems and handling customer complaints.
Customer satisfaction
Quality assurance has a direct impact on customer satisfaction, which enhances reputation and strengthens business relationships. Consistently delivering high-quality products increases customer confidence and fosters long-term loyalty. A strong track record of quality also positions the company as a trusted and preferred supplier in the marketplace, opening up new business opportunities and strategic partnerships.
Conclusions
The implementation of quality assurance strategies in materials procurement is significant to the success and safety of industrial projects. Adopting a comprehensive approach that includes control procedures, rigorous supplier evaluation, and the use of advanced technologies such as IoT and artificial intelligence significantly improves customer satisfaction.
Implementing a robust quality management system ensures the consistency and reliability of purchased materials, minimizing the risk of failures and defects. This not only contributes to the integrity and functionality of projects but also strengthens the company’s reputation as a reliable and high-quality supplier in the market. The best practice examples and case studies presented demonstrate that a proactive and systematic approach to quality management can result in considerable loss reduction, productivity improvements, and increased customer loyalty.
Ultimately, quality assurance in materials procurement is a strategic investment that offers substantial returns in terms of efficiency, costs, and business relationships. Maintaining high-quality standards is an operational necessity and a competitive advantage that positions companies to successfully meet future challenges and seize new opportunities in an increasingly demanding business environment.
References
Own source