Table of Contents
Introduction
Positive Material Identification (PMI) is a fast, non-destructive method for verifying the chemical composition of metals and alloys. The portable and cost-effective PMI can be performed in laboratories or on site. The END include techniques that not only allow the evaluation of the condition of mechanical integrity, but also the identification of materials for their segregation. Among the best known are X-Ray Fluorescence or XRF.
In all industries or disciplines there are certain gray areas; in the case of material identification, it is not incorrect to define it as an NDT despite its purpose, which is the differentiation and identification of metallic materials. It is also more commonly known as PMI for its acronym in English: Positive Identification of Materials. Depending on the needs, X-Ray Fluorescence, known as XFR, Optical Emission Spectroscopy or OES, and Laser Induced Breakdown Spectroscopy or LIBS are used.
Positive Material Identification is a cost-effective method of verifying common material types. Although not as comprehensive as other chemical analysis methods, PMI is an excellent choice for checking the alloy or type of large batches of materials, testing finished components, recertifying materials, and evaluating materials that cannot be destroyed or sent to a laboratory.
As we already know, this differentiation of alloys will allow the segregation of these materials for later use. The field of materials analysis has changed tremendously in recent decades. Today it is easier than ever for companies to find a team that fits their needs.
This powerful tool has become indispensable in countless industries. As a quality control check, mainly. This equipment has become cheaper and more sophisticated, as has happened with most of our technological tools in this wonderful branch of engineering in which we work.
And since we now need to take care of the environment more than ever, the identification of materials that could contain elements potentially harmful to ecosystems has been increasingly taken more seriously. The wide spread of electronic equipment in the world has made it necessary to implement regulations such as RoHS, which refers to Directive 2011/65/EU on the Restriction of Hazardous Substances in electrical and electronic equipment.
Thanks to an efficient discrimination of waste, it is possible to prevent, for example, groundwater sources from being fatally contaminated with toxic components present in certain types of “electronic waste”.
That said, we can elaborate a bit on the history of these techniques before briefly describing their working principles. For a long time, the selection of materials was made by experienced personnel, and with relatively conventional methods: laboratory analysis, for example. These methods were time consuming and did not meet the productivity standards of a company whose core business was, say, scrap metal recycling. Therefore, a technological solution was sought, and the results were splendid. Modern gadgets even have connectivity and go online in order to adjust the parameters of what goes into a foundry, for example. Or generate an immediate alert to the purchasing department that a batch of materials does not meet the specifications of the certificate, for example. Needless to say, this is a way to ensure properties such as resistance to heat, corrosion, weldability, among others.
Why is it important?
PMI testing ensures that every component that enters a plant was manufactured to specification. In this way, critical parts that are to be used as replacements will be of the proper alloy and grade; all materials are exactly what they should be. And this can be the difference between uninterrupted operation…or catastrophic failures that can be fatal. This assay puts fast and highly reliable quality control in the hands of operators. And its wide acceptance is due to the fact that it is exactly what the day-to-day demands of any modern plant demand: a peripheral view of the entire mechanical arrangement, of all the critical parameters, the essential variables that could affect operations, but with methods that do not interrupt them.
We are going to limit ourselves to portable equipment that is used in the field; The variety of laboratory equipment is vast, and as inspectors, we are (or will be) much more likely to be familiar with the equipment used in the field. The goal is clear: to confirm or determine the grade of an alloy. The current equipment has a very high degree of precision regarding the differentiation of alloys, and an extensive database that is constantly updated, with which the assertiveness of the test has grown a lot. It is interesting to note that due to their detection capabilities, they are very useful for verifying the chemical composition of weld seams.
Principles of X-Ray Fluorescence
This technique can be used to study the composition not only of metallic materials, but also includes samples of petroleum and minerals.
From our basic physics lessons, we know that X-rays are part of the electromagnetic spectrum. These rays are on the high-energy side of ultraviolet rays; and are expressed in terms of energy in kEv or wavelengths in nanometers. The range of elements that can be analyzed is wide, going from sodium to uranium, being able to detect concentrations from parts per million (ppm) to high percentages in different material morphologies, such as solids, liquids and pulverized material.
All XRF instruments are designed around two components: an X-ray source (commonly a tube) and a detector. The primary X-rays are generated by the source and are directed at the surface of the sample, usually passing through a filter to modify the X-ray beam. When this beam hits the atoms of said sample, they react producing a secondary broadcast X-rays of certain characteristics (see image).
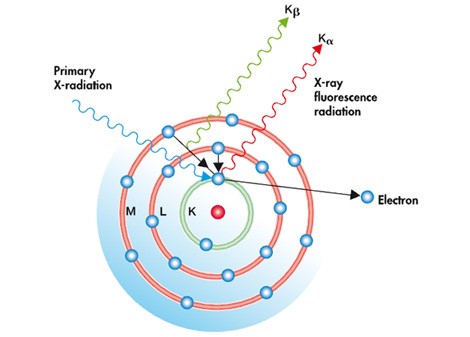
This secondary emission occurs as follows: A stable atom is made up, recalling our basic chemistry lessons, of a nucleus and electrons orbiting around it. These electrons are arranged in energy levels also called lobes. Different energy levels can have a different number of electrons. When the primary beam of high-energy X-rays strikes an atom, it alters its balance, generating the ejection of electrons from the lowest energy levels, destabilizing the atom. In order to restore this balance, an electron from a higher energy level falls into this vacancy. The excess energy released when this movement between the two levels is generated is then emitted as secondary X-rays, which are then captured and processed by a detector.
This energy released in the process turns out to be characteristic for each element. Therefore, XRF is a qualitative measurement test, which tells us which elements are present and in what proportion. Information that, conveniently processed, is located in a database and the result presented in the form of the chemical composition of the most important elements, and the code with which the alloy itself is denoted.
In the next articles, we will continue with the description of the mentioned methods.
Best of luck!