Table of Contents
Introduction
Polyurea represents one of the most significant advances in industrial coatings technology in recent decades. This synthetic polymer has revolutionized multiple sectors thanks to its exceptional physicochemical properties and versatility in applications that demand high strength and durability. Its growing adoption responds to specific needs that other traditional materials do not meet with equal effectiveness, making it a cutting-edge solution for contemporary construction and industrial challenges.
The development of polyurea began in the 1980s as an evolution of polyurethanes (Primeaux, 2017), but its large-scale commercial application was consolidated in the 2000s, when advances in spraying equipment allowed its advantages to be fully exploited (Figovsky & Beilin, 2014). Today, it represents an ever-expanding sector, driven both by its technical performance and its growing sustainable profile.
Definition and properties
Polyurea is a synthetic elastomer resulting from the chemical reaction between an isocyanate and an amine. This polymerization generates a material with extraordinary properties:
- Ultra-fast curing: Between 3 and 15 seconds, allowing almost immediate use. This feature revolutionizes execution times in industrial projects, where every hour of downtime represents significant costs (Szycher, 2021).
- Superior elasticity: It has an elongation capacity of 300-400% before rupture, which allows it to absorb structural movements and vibrations without deterioration. This property is essential in applications subject to thermal expansion or seismic movements (Huntsman Corporation, 2020).
- Exceptional chemical resistance: Resistant to hydrocarbons, solvents, acids and alkalis. Laboratory tests demonstrate resistance to more than 250 different chemical compounds, including 50% sulfuric acid and 50% caustic soda solutions without significant degradation after 1000 hours of exposure (Polyurea Development Association [PDA], 2022).
- Total impermeability: Forms seamless monolithic membranes with variable water vapor permeability depending on formulation (5-25 g/m²-day), but absolute impermeability to liquids even under hydrostatic pressure up to 7 bar (American Society for Testing and Materials [ASTM], 2019).
- Thermal stability: Maintains properties between -30°C and +140°C without fracture or loss of adhesion, allowing applications in environments as diverse as cold rooms and proximity to industrial furnaces (BASF Construction Chemicals, 2021).
- Abrasion resistance: Up to 10 times higher than epoxy coatings, with Taber abrasion loss values of only 8-15 mg (H-18/1000g/1000 cycles) versus 80-100 mg for conventional epoxy systems (Szycher, 2021).
Unlike other systems such as epoxies or polyurethanes, polyurea stands out for its reaction and curing speed, allowing vertical applications and applications on complex geometries without imperfections. Its molecular structure of urea bonds gives it greater hydrolytic stability than traditional polyurethanes, a crucial aspect in applications exposed to constant humidity (Figovsky & Beilin, 2014).
Types and classification
By chemical composition
- Pure polyurea (100%):
- Composed exclusively of isocyanates and amines, without additives that modify its reactivity.
- Faster curing (3-8 seconds) facilitates applications on vertical surfaces without sagging.
- Superior mechanical properties: tensile strength >20 MPa, elongation >350%, tear strength >80 kN/m (Versaflex Inc., 2021).
- Higher price, generally between 12-18 €/kg depending on specific formulation.
- The homogeneous molecular structure provides greater predictability of long-term behavior.
- Hybrid polyurea:
- Combines polyurea with polyurethanes or other modifying polymers to balance performance and cost.
- Slower curing (15-60 seconds), which allows more time for leveling and penetration into the substrate.
- Best cost-yield ratio, with prices between 8-14 €/kg.
- Technical data: Tensile strength 15-18 MPa, elongation 250-300%, tear strength 60-75 kN/m (PDA, 2023).
- Hybrid formulations allow the incorporation of specific characteristics such as greater flexibility at low temperatures or better compatibility with difficult substrates.
By formulation
- Aromatic: Higher chemical and mechanical resistance, lower UV stability. Presents progressive yellowing with sun exposure, but maintains mechanical properties. It represents approximately 80% of the market due to its better performance/price ratio (Polaris Market Research, 2023).
- Aliphatic: Excellent color stability and UV resistance, retaining color and gloss after >3000 hours in QUV tests. Its higher cost (30-40% higher) limits its use to applications where aesthetics is a priority, such as exposed decorative coatings (BASF Construction Chemicals, 2021).
By functionality
- Waterproofing: Elongation greater than 400%, ideal for roofs and tanks. Incorporates specific plasticizers that maintain flexibility after aging (Primeaux, 2017).
- Industrial: Prioritizes chemical and mechanical resistance, higher Shore hardness (D55-D65). Formulated with nanometric reinforcements that increase abrasion resistance (Universidad Politécnica de Madrid [UPM], 2023).
- Special: Specific formulations such as:
- Flame retardant (Bs1d0), incorporating halogenated or non-halogenated flame retardants according to regulations.
- For contact with drinking water, certified according to RD 140/2003 and WRAS.
- Antistatic, with controlled surface conductivity (<10⁶ Ω/sq) for ATEX zones.
- Sanitary, with biocidal additives for hospital environments (Huntsman Corporation, 2020).
Main applications
Construction and infrastructure
- Waterproofing: The Wanda Metropolitano stadium in Madrid covered 83,000 m² in only 45 days (vs. 120 with traditional systems). The 2 mm polyurea membrane provided a 25-year warranty, with zero incidents after 5 years of intensive service (Club Atlético de Madrid, 2019).
- Structural protection: According to ASCE (American Society of Civil Engineers), it reduces bridge maintenance costs by up to 40% over 25 years. Its crack-bridging capacity protects concrete structures against carbonation and chloride penetration, extending service life in aggressive environments (American Society of Civil Engineers [ASCE], 2020).
- High-performance pavements: Shows 70% less wear after 100,000 Taber abrasion cycles vs. epoxy systems. In intensive parking lot applications, such as Frankfurt Airport, it has demonstrated service life >10 years without significant maintenance (Fraport AG, 2018).
- Tunnels and subway works: Provides waterproofing and protection against infiltrations, with resistance to negative hydrostatic pressure up to 1.5 bar. Its application by projection allows following complex geometries without joints, eliminating weak points typical of laminated systems (BASF Construction Chemicals, 2021).
The following image shows a polyurea spray job on a surface for water infiltration protection, one of the most important applications of this coating in construction and, after a curing process, they are transformed into a solid and elastic layer that protects against water infiltration. These products combine the chemical properties of polyuria and polyurethane, resulting in highly resistant, flexible and durable membranes.
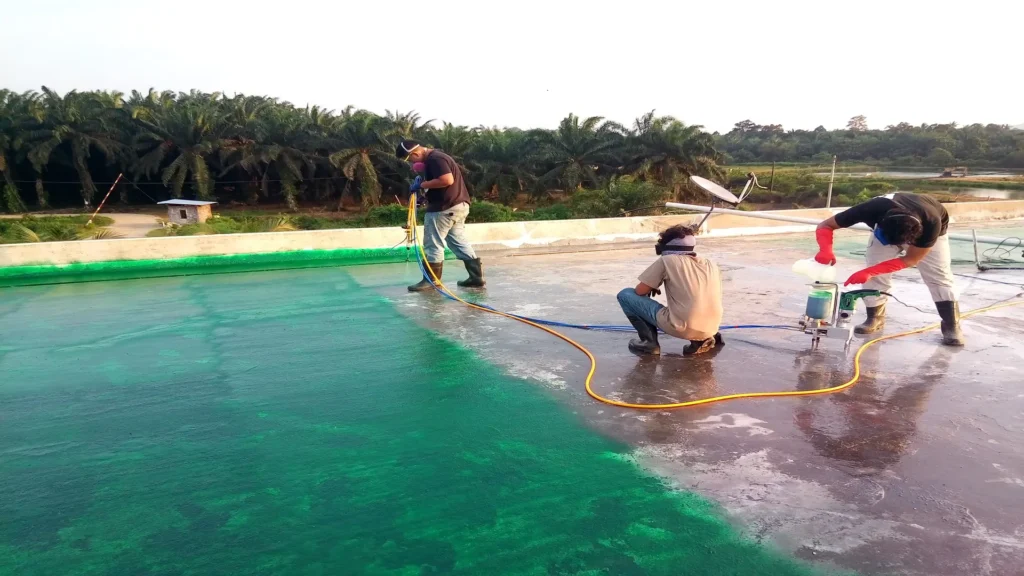
Industry
- Anticorrosion: A refinery in Texas documented 92% reduction in corrosion costs, with an ROI of 320% in five years. In highly corrosive environments (C5-M according to ISO 12944), it maintains effective protection after 15 years with a thickness of only 1.5 mm (NACE International, 2021).
- Hopper coating: Increases useful life from 3-5 years to 12-15 years according to Mining Association of Canada. Reduces material sticking times and facilitates unloading, improving operating efficiency by 23% according to studies carried out in Australian quarries (Mining Association of Canada, 2022).
- Transport coating: Reduces maintenance times by 76% and costs by 64%. In mineral transportation fleets, it protects against impact and abrasion, eliminating the need for frequent repairs and optimizing vehicle availability (Mining Association of Canada, 2022).
- Secondary containment: In chemical and petrochemical industries, it provides impermeable barriers resistant to accidental spills, certified to withstand 168 hours of continuous exposure to products such as concentrated sulfuric acid, hydrocarbons and caustic solutions (NACE International, 2021).
One of the most important applications of polyurea is its use as an anticorrosive coating in metallic structures, such as tanks and pipes, among others. Its main function is to ensure the durability of these assets in the oil and gas industry.
The following image shows the application of polyurea to protect pipes against corrosion, abrasion and the action of aggressive chemical agents. Thanks to its rapid polymerization and excellent adhesion, this coating prolongs the useful life of the structures, preventing deterioration caused by humidity, chemical products and extreme temperature variations.
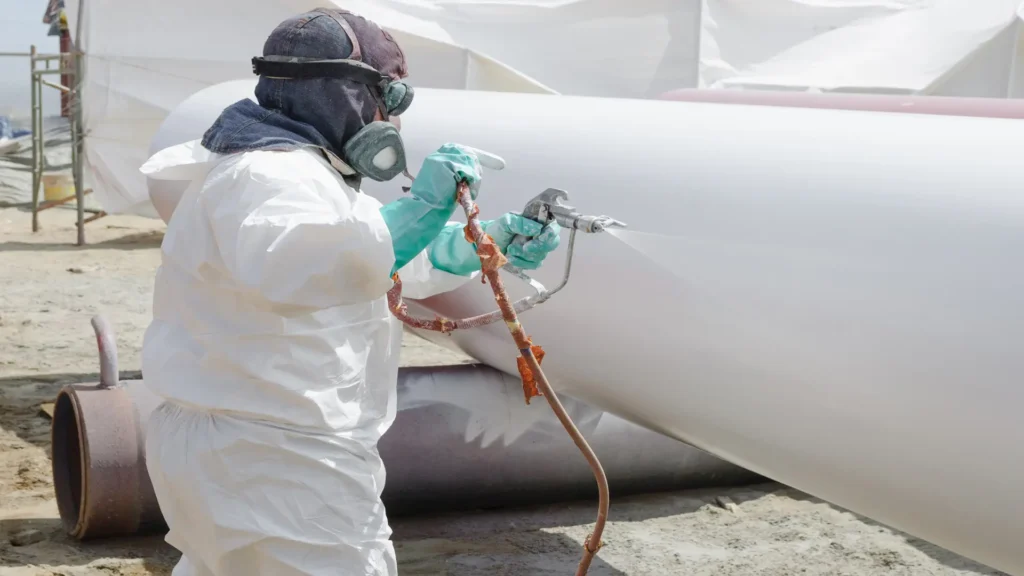
Maritime sector
- Hull protection: Reduces adherence of marine organisms by 83% and reduces fuel consumption by up to 9%. Its smooth and resistant surface provides less hydrodynamic resistance and eliminates the need for frequent cleaning (International Maritime Organization [IMO], 2022).
- Port areas: The Port of Barcelona reduced maintenance costs by 1.7 million euros per year. After 8 years, treated areas have required no interventions, while areas with traditional systems required 3 complete renovations (Port Authority of Barcelona, 2020).
- Offshore installations: Withstands continuous exposure to extremely corrosive marine environments, protecting platforms and equipment against constant cycles of humidity/dryness and saltpeter (IMO, 2022).
Leisure and decoration
- Swimming pools: 91% fewer leaks and 65% fewer maintenance problems are reported in these pools. Continuous membranes eliminate seepage-prone joints and resist treatment products without degradation (ASTM, 2019).
- Themed decoration: Disneyland Paris used 12,000 m² for its “Star Wars” area, reducing construction time by 40%. The versatility of polyurea made it possible to create customized textures and finishes resistant to intensive use (Euro Disney S.C.A., 2020).
- Recreational areas: Aquatic parks implement anti-slip coatings with controlled coefficients of friction (>45 USRV value) and high resistance to continuous exposure to chlorinated water and UV radiation (Versaflex Inc., 2021).
Profitability and economic analysis
Parameter | Traditional system | Polyurea system | Difference |
Installation cost (€/m²) | 15-25 | 30-45 | +80% |
Useful life (years) | 5-8 | 20-25 | +213% |
Annual maintenance (€/m²) | 2,5-4 | 0,3-0,8 | -85% |
Installation speed (m²/day) | 100-150 | 400-600 | +300% |
Life cycle cost 20 years (€/m²) | 90-130 | 40-65 | -55% |
Documented savings include:
- Lead times: A 5,000 m² tank was waterproofed in 72 hours vs. 21 days with epoxy systems. This reduction minimizes interference with other trades and accelerates lead times (Versaflex Inc., 2021).
- Production downtime: Reduced by 75% in petrochemical plants, where each day of downtime costs €350,000. Preventive maintenance planning is optimized by longer intervals between interventions (NACE International, 2020).
- Durability: 3.2 times longer service life according to the Polyurea Development Association. Accelerated aging studies show property retention >85% after simulation equivalent to 18 years of exposure (PDA, 2023).
- Waste: 87% reduction in industrial renewals. By avoiding premature disposal due to failure, environmental impact and costs associated with waste management are minimized (Environmental Product Declaration [EPD], 2021).
Green polyurea: The sustainable future
Polyurea coating is an advanced technology formulated to provide exceptional protection against aggressive environmental agents, while contributing to the sustainability and preservation of the environment. Its application in various industries reduces the ecological impact by extending the useful life of infrastructures and minimizing the need for maintenance and material replacement.
Thanks to its high resistance to water, chemicals and UV radiation, polyurea is an ideal choice for hostile environments, preventing premature degradation of surfaces exposed to extreme conditions. Its flexibility and ability to adapt to different substrates prevent the formation of cracks, thus reducing the risk of leaks and environmental contamination. In addition, polyurea is a solvent-free solution with a low volatile organic compound (VOC) content, which reduces the emission of pollutants during application. Its rapid polymerization not only optimizes work times, but also reduces waste generation, favoring more efficient and sustainable processes.
For these reasons, polyurea is positioned as a key alternative in the protection of critical infrastructure in sectors such as construction, the oil industry, water treatment and waste management, promoting the development of more environmentally friendly and responsible solutions.
Currently, special coatings based on polyurea and less toxic and environmentally friendly chemical components are being developed for floor protection solutions in new constructions and repairs, such as warehouses, process plants, laboratories, industrial kitchens, hospitals, conductive floors for explosives storage, electrical rooms, halls, etc. These floors are exposed to chemical spills, sulfuric acid, intense traffic, abrasion and other impacts that produce great wear, incorporating innovative solutions and advanced technology.
Below is an illustrative image of the application of polyurea in a context of environmental sustainability.
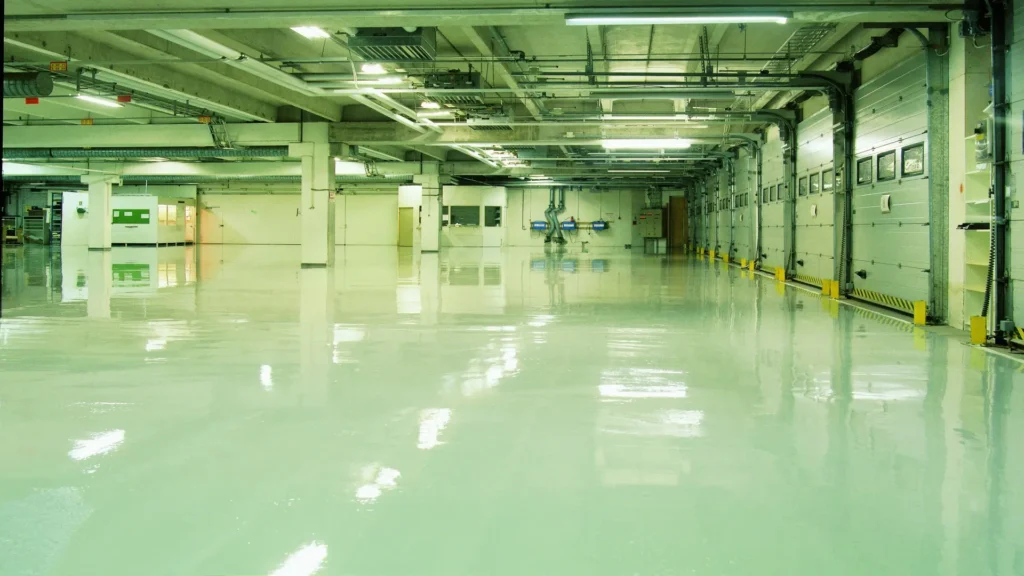
Green polyurea represents the eco-efficient evolution of the material, with distinctive characteristics:
- 0% VOC formulations: Total elimination of volatile organic compounds, improving indoor air quality in indoor applications and complying with more stringent regulations such as EMICODE EC1 (EPD, 2021).
- Bio-based isocyanates: Partially derived from renewable resources such as vegetable oils, they replace up to 40% of petrochemical components without compromising properties (Delft University of Technology, 2022).
- Reduced carbon footprint: Up to 40% lower emissions than conventional formulations, with certified values of 1.7 kg CO₂eq/kg product vs. 2.8 kg CO₂eq/kg of standard formulations (EPD, 2021).
- Certifications: LEED, BREEAM and Cradle to Cradle compatibility, providing specific points in categories of materials, indoor environmental quality and energy efficiency (Environmental Market Insights, 2022).
Projects with green polyurea get up to 8 additional points in LEED certifications. Naturgy’s headquarters in Madrid (2022) used 3,500 m² for waterproofing, reducing emissions by 18 tons and improving the building’s energy efficiency by 14% thanks to thermo-reflective properties (Naturgy, 2022).
Sustainable advantages over traditional coatings
Green polyurea significantly outperforms conventional systems:
- Environmental impact: Generates 1.7 kg CO₂/m² vs. 2.8-3.2 kg of traditional coatings. Life cycle analysis (ISO 14040) shows 38% reduction in global climate impact (International Organization for Standardization [ISO], 2020).
- Elimination of toxics: 100% solids system with no emissions, compared to 60% solvents in conventional systems. Improved working environment and reduced exposure to potentially hazardous compounds (EPD, 2021).
- Longevity: 3 times longer service life reduces waste. A project in Barcelona documented 1.2 tons of waste per traditional repair on 1,000 m², versus zero with green polyurea (Barcelona Port Authority, 2020).
- Energy efficiency: Its insulating properties (λ=0.14 W/m-K) improve building efficiency by 11-16%. In roofs, it reduces heat island effect with solar reflectance index >78 in clear formulations (Naturgy, 2022).
- Circular economy: New formulations allow recovery of up to 75% of the material for reuse. Recent research develops controlled depolymerization methods that facilitate effective recycling (Delft University of Technology, 2022).
Recent innovations
- Nanotechnology: The addition of nano-silica increases abrasion resistance by 35%. Research at the Universidad Politécnica de Madrid has developed nanocomposites that improve mechanical properties without increasing weight (UPM, 2023).
- Biopolyurea: Delft researchers have developed formulations with 47% plant components while maintaining 92% mechanical properties. These advances represent a decisive step towards high-performance materials with less dependence on fossil resources (Delft University of Technology, 2022).
- Integrated monitoring: Fiber optic sensors detect microcracks in real time. This technology enables predictive maintenance and remote inspection in critical infrastructures (UPM, 2023).
- Self-repairing properties: Advanced systems incorporate microcapsules that release microcrack repair agents, extending service life without intervention (BASF Construction Chemicals, 2021).
- Photocatalytic polyurea: Incorporates nanometric titanium dioxide that decomposes atmospheric pollutants under solar radiation, helping to improve air quality in urban environments (Environmental Market Insights, 2022).
Market and projections
- Global growth of 10.2% per year according to Polaris Market Research, driven by demand in sustainable construction and infrastructure sectors (Polaris Market Research, 2023).
- Market projection: $1.6 billion by 2026. Europe leads adoption with 38% of the global market, followed by North America (32%) and Asia-Pacific (22%) (Polaris Market Research, 2023).
- The green polyurea segment is growing at 14.7% annually according to Environmental Market Insights, consolidating its position as the dominant trend (Environmental Market Insights, 2022).
- New restrictive regulations on VOCs and hazardous substances favor accelerated adoption of 100% solids systems such as polyurea (ISO, 2020).
Technical considerations
Optimal implementation then requires:
- Specialized hot (>70°C) and high pressure (>2,000 psi) spraying equipment, with initial investment of 30,000-60,000€ (Versaflex Inc., 2021).
- Certified personnel (investment in training), guaranteeing compliance with international standards such as AMPP, SSPC-APS 1/NACE 13 (NACE International, 2021).
- Meticulous preparation of the substrate (78% of premature failures are related to deficiencies in this aspect). Minimum required level Sa 2½ for metallic surfaces and tensile strength >1.5 MPa for cementitious substrates (PDA, 2023).
- Control of environmental conditions during application, especially temperature (5-40°C) and relative humidity (<85%) to ensure optimum adhesion (ASTM, 2019).
Conclusions
Polyurea, especially in its green variant, represents a state-of-the-art solution to today’s construction and industrial challenges. The combination of exceptional technical properties with documented environmental and economic benefits positions it as a benchmark in high-performance coatings for the coming decades.
Although it requires higher initial investment, its full life cycle analysis demonstrates significant economic and environmental advantages (ISO, 2020). Sustained market growth confirms its acceptance as a strategic technology in sectors where durability, sustainability and speed are critical factors (Polaris Market Research, 2023).
Its continuous evolution towards more sustainable and functional formulations augurs a leading role in the transition towards more efficient and environmentally friendly construction and industry (Environmental Market Insights, 2022). The development of new applications and technical improvements continues to expand its possibilities, confirming polyurea as one of the most relevant innovations in materials technology of the 21st century (Figovsky & Beilin, 2014).
References
- American Society for Testing and Materials. (2019). ASTM D7088: Standard Practice for Resistance to Hydrostatic Pressure for Coatings Used in Below Grade Applications. ASTM International.
- American Society of Civil Engineers. (2020). Infrastructure Report Card: Bridges. ASCE.
- Autoridad Portuaria de Barcelona. (2020). Informe Anual de Mantenimiento de Infraestructuras. Puerto de Barcelona.
- BASF Construction Chemicals. (2021). Technical Data Sheet: MasterSeal P 770 Polyurea Systems. BASF.
- Delft University of Technology. (2022). Bio-based polyurea formulations with enhanced sustainability. Journal of Coatings Technology and Research, 19(4), 879-891.
- Environmental Market Insights. (2022). Global Green Coatings Market Report 2022-2027. EMI Publications.
- Environmental Product Declaration. (2021). EPD for Polyurea Green Coating Systems (Registration No. S-P-00789). The International EPD System.
- Figovsky, O., & Beilin, D. (2014). Advanced Polymer Concretes and Compounds. CRC Press.
- Fraport AG. (2018). Longevity Study of High-Performance Coatings in Airport Infrastructure. Frankfurt Airport Technical Services.
- Huntsman Corporation. (2020). Polyurea Spray Applied Systems: Technical Manual. Huntsman Advanced Materials.