Table of Contents
- Introduction
- Polymers and their history
- What are polymers?
- Mechanical, chemical and thermal properties
- The four Leading polymers in industry
- Classification of polymers: Types and characteristics
- Advantages and disadvantages of polymeric materials
- New manufacturing and processing techniques
- Prominent examples of polymers and their applications
- The top 3 polymers for specific applications
- Regulations and standards for polymers
- Challenges and opportunities in polymer usage
- Frequently asked questions
- Conclusions
- References
Introduction
Since their introduction into the industrial sector, macromolecules, particularly polymers, have revolutionized countless industries thanks to their versatility and ability to meet specific needs. Materials such as food packaging, advanced electronic components, and medical tools are just a few examples of how these substances have transformed our daily lives.
Their relevance lies in unique properties such as lightness, strength, flexibility, and, in many cases, biodegradability or recyclability. These qualities have positioned them as an ideal alternative to traditional materials like metals and ceramics, helping reduce costs and enhance performance in key applications.
This article addresses key questions to better understand this fascinating field: What are the main polymers used today? What types of polymers exist, and how are they classified? What specific examples stand out for their industrial and scientific applications? Additionally, we will explore the historical evolution of polymers, from natural materials to current innovations in advanced polymers.
The article will also analyze the latest advancements in this field, highlighting how polymeric materials are shaping the future of technology and sustainability. This journey will provide an understanding of not only the impact of polymers on our daily lives but also their role in solving global challenges and their promising horizon in technological innovation.
Polymers and their history
The use of these materials dates back to ancient times when natural substances like cellulose and rubber were used in tools and textiles. However, these natural materials had significant limitations in terms of stability and strength.
In the 19th century, methods to modify these materials were developed, such as rubber vulcanization, which improved its elasticity and heat resistance by adding sulfur. The real breakthrough came in the 20th century with the creation of synthetic materials specifically designed to overcome these limitations.
A pivotal moment was the discovery of nylon in 1935 by Wallace Carothers at DuPont. This polymer, the first completely synthetic one, revolutionized the textile industry and demonstrated the potential of polymeric materials to replace traditional materials. During World War II, nylon was widely used in parachutes, ropes, and other critical applications. Later, engineering plastics such as high-density polyethylene (HDPE), polypropylene (PP), and polyvinyl chloride (PVC) were developed.
These materials combined strength, lightness, and durability while transforming industries like automotive, construction, and electronics. For example, HDPE became a key material for pipes and packaging, PP excelled in medical and textile applications, and PVC became a cornerstone in construction due to its durability and fire resistance.
In recent decades, concerns about the environmental impact of plastics have led to the development of biodegradable polymers like polylactic acid (PLA), designed to reduce waste accumulation and promote sustainability.
For an overview of polymers, their evolution, properties and applications in everyday life, check out this informative video. Source: UB, Dr Chong Cheng.
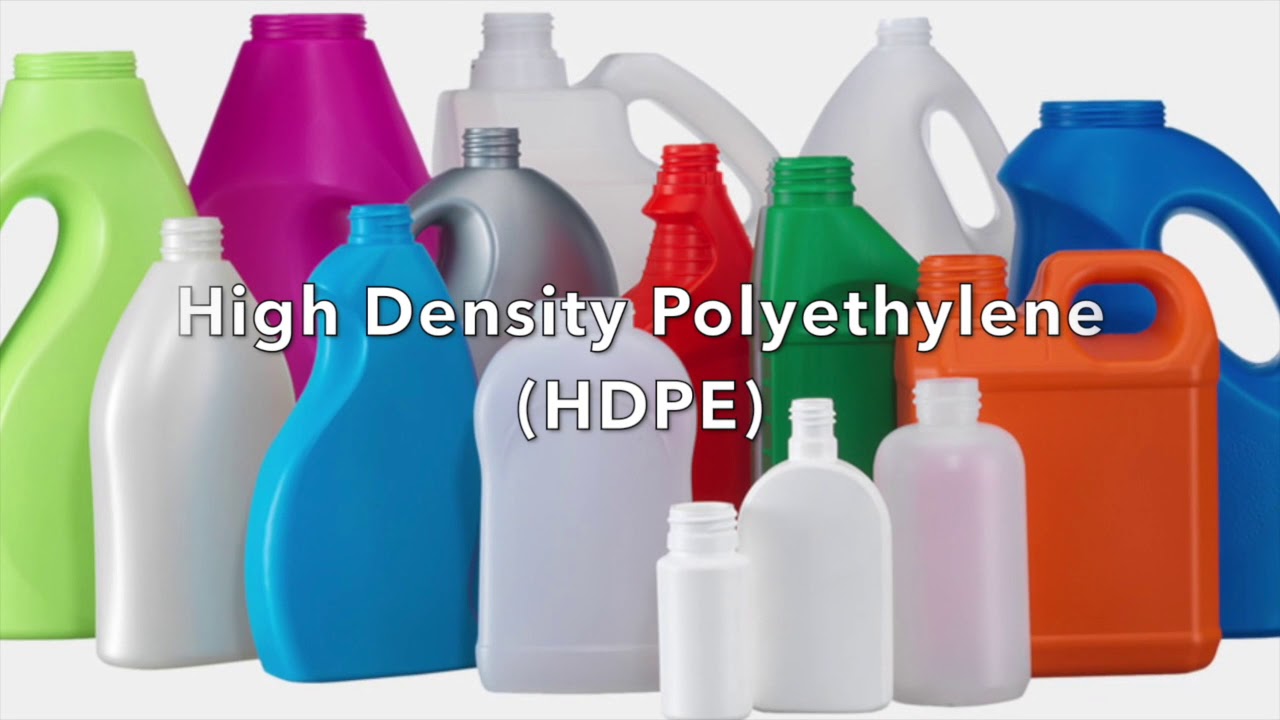
Polymers in everyday life.
The development of polymers has been one of the greatest technological advances made by mankind since they have become the base material without which we would not be able to manufacture a large number of objects.
What are polymers?
Polymers, a subset of macromolecules, are formed by the repetition of smaller units called monomers, which are linked by covalent bonds. These bonds create long, varied structures that can be linear, branched, or three-dimensional. The diversity in the arrangement of monomers and the nature of the bonds is what gives these materials their unique properties, including their distinct mechanical properties, making them essential in a wide range of applications.
From a chemical perspective, these materials are classified as organic or inorganic compounds. In organic polymers, the covalent bonds between monomers typically involve atoms of carbon, hydrogen, oxygen, and nitrogen. In inorganic polymers, such as silicones, other elements like silicon play a key role. A crucial aspect of polymer chemistry is polymerization, the process by which monomers bond to form long chains.
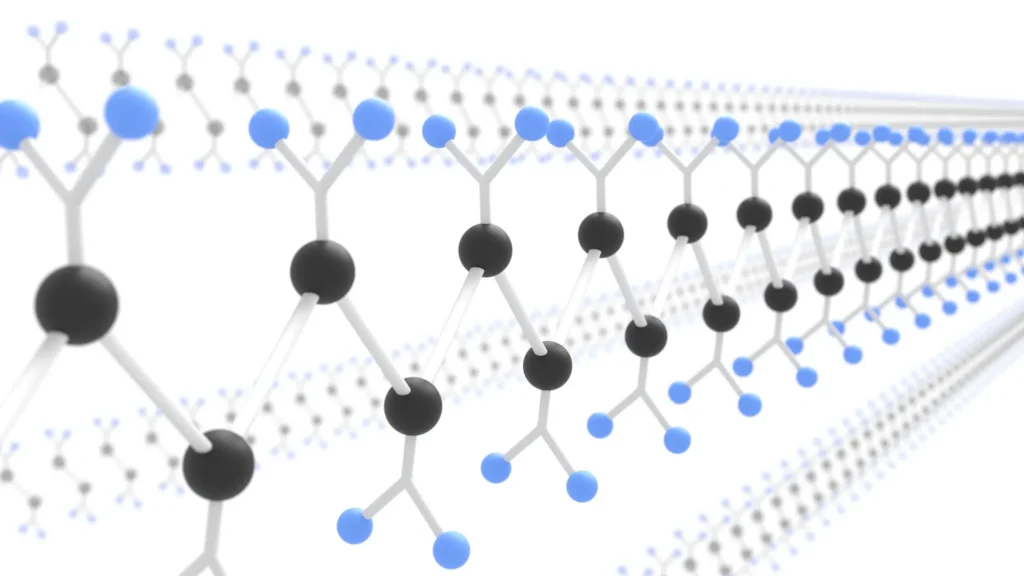
There are two major categories of polymers: natural and synthetic. Natural polymers, such as cellulose, natural rubber, and proteins, are found in nature and are fundamental to biological processes. On the other hand, synthetic polymers, such as polyethylene and nylon, are manufactured by humans and designed to fulfill specific functions in industrial applications.
For example, cellulose is a natural polymer used in paper manufacturing, while polyethylene, a synthetic polymer, is used in packaging and pipes. These two categories demonstrate how polymers can meet both biological and industrial needs.
Mechanical, chemical and thermal properties
The properties of polymers are fundamental to understanding their behavior in different applications. These properties fall mainly into three categories:
Mechanical properties
Polymers are characterized by their tensile strength, elasticity, and hardness. For instance, high-density polyethylene (HDPE) has excellent tensile strength, making it ideal for pipes. Elasticity, as seen in natural rubber, allows polymers to regain their shape after deformation. Hardness, found in materials like polyurethane (PU), ensures durability in high-wear applications. Self-healing polymers take these mechanical properties a step further by enabling materials to restore their integrity after damage, making them ideal for applications requiring extended durability.
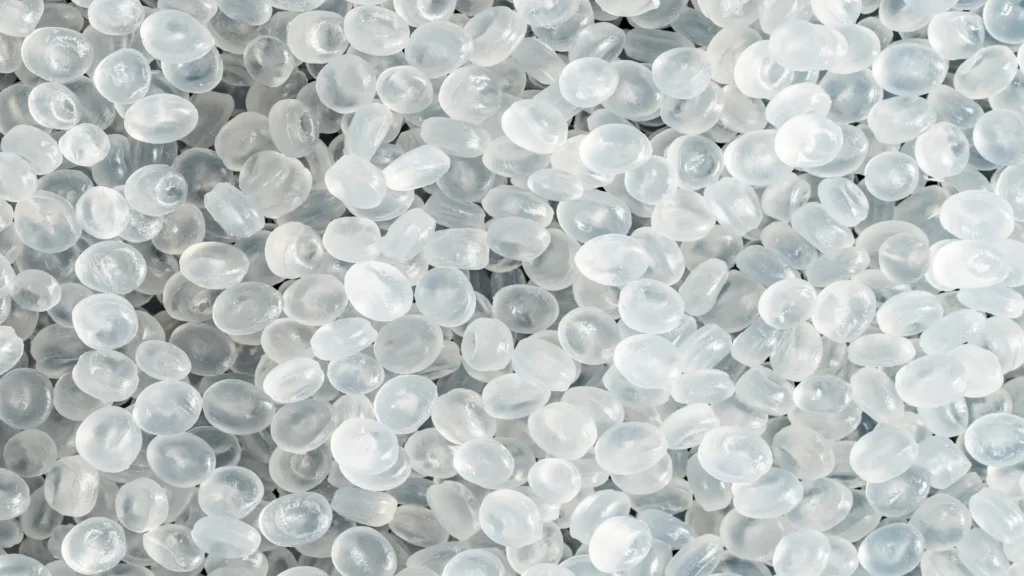
Thermal properties
These materials possess unique thermal characteristics, such as the glass transition temperature (Tg), marking the point where a polymer transitions from rigid to flexible. Thermosetting polymers, like epoxy, exhibit high thermal stability, resisting extreme temperatures without degrading, making them ideal for demanding industrial applications.
Chemical properties
The chemical resistance of polymeric materials allows them to withstand harsh environments without degrading. For example, polypropylene resists most acids and alkalis, making it ideal for chemical containers. Additionally, many polymers are hydrophobic, such as Teflon, which makes them perfect for non-stick and water-resistant applications.
The combination of mechanical properties with chemical and thermal features ensures polymers remain versatile materials capable of meeting the demands of applications across automotive, medical, and electronics industries
The four Leading polymers in industry
Polymeric materials dominate the industry due to their exceptional properties and ability to adapt to multiple uses. Among the most prominent are:
- Polyethylene (PE): One of the most widely produced materials globally, used in bags, packaging, bottles, and pipes. Its versatility stems from its chemical resistance, low cost, and lightness. Polyethylene is classified into various forms, such as low-density polyethylene (LDPE) and high-density polyethylene (HDPE), depending on its structure and properties.
- Polypropylene (PP): This polymer is known for its excellent impact resistance, low weight, and thermal stability. It is used in the automotive industry to manufacture lightweight parts, in non-woven textiles such as diapers, and in medical devices due to its chemical resistance and biocompatibility.
- Polyvinyl Chloride (PVC): Popular in construction, PVC is used in pipes, windows, and coatings due to its durability and fire resistance. It is also employed in electrical applications like cable insulation, thanks to its heat and chemical resistance.
- Polyurethane (PU): This polymer is extremely versatile and is used in furniture foams, protective coatings and adhesives. Its ability to be rigid or flexible, depending on the formulation, makes it indispensable in both industrial and domestic applications.
Comparative table: Key properties of polymers
Polymer | Density (g/cm³) | Resistance | Main applications |
Polyethylene (PE) | 0.91-0.97 | Up to 80°C | Bags, packaging, pipe |
Polypropylene (PP) | 0.9 | Up to 130°C | Automotive, textiles, medical devices |
PVC | 1.3 – 1.4 | Up to 60°C | Construction, electrical insulation |
Polyurethane (PU) | 1.2 – 1.3 | Variable | Foams, coatings, adhesives |
These polymeric materials form the foundation of many modern industries, illustrating how the specific properties of each material dictate its use in key applications.
Classification of polymers: Types and characteristics
Polymers, as a type of macromolecule, are classified based on their origin, structure, thermal behavior, and applications.
Classification by origin
1. Naturals: These are found in nature and fulfill biological or structural functions. Examples:
- Cellulose: A primary component of plant cell walls, used in paper and textiles..
- Natural Rubber: Extracted from latex, known for its elasticity and resilience, key in tires and industrial products.
2. Synthetic: Man-made through chemical processes, these materials offer specific properties tailored to various applications. Examples:
- Nylon: Used in textiles and mechanical components for its strength and flexibility.
- Polystyrene: Utilized in packaging and insulation due to its lightness and thermal resistance.
Classification by structure
- Linear: Polymers with long, straight chains, such as polyethylene, which are flexible and easy to process.
- Branched: Featuring side chains that enhance impact resistance and reduce density. Example: Low-density polyethylene (LDPE).
- Cross-linked: Interconnected chains forming a three-dimensional network, making them rigid and durable. Example: Epoxy resins..
Classification by thermal behavior
- Thermoplastics: Recyclable polymers that soften when heated and can be reshaped repeatedly. They are flexible, lightweight, and used in packaging, automotive components, and pipes.
- b) Thermosets: Rigid polymers that cannot be reshaped after curing. They resist heat and chemicals, making them ideal for adhesives, coatings, and aerospace applications. Example: Polyurethane (PU).
Classification by application
- General-use polymers: Widely utilized for their low cost and ease of processing. Example: Polyethylene and PVC.
- Engineering polymers: Offering superior properties, such as high mechanical and thermal resistance. Example: Polycarbonate (PC).
- Specialized polymers: Designed for specific applications, such as electronics or biomedicine. Example: Conductive and biodegradable materials.
Comparison: Polymers vs. metals and ceramics
Property | Polymers | Metals | Ceramics |
Lightness | High | Medium | Low |
Flexibility | High (in thermoplastics) | Moderate | Low |
Thermal Resistance | Variable (high in thermosets) | High | Very high |
Cost | Bajo a moderado | Moderado | High |
Fragility | Medium – high | Low | Very high |
Advantages and disadvantages of polymeric materials
Advantages
- Lightness and flexibility, reducing weight in applications like automobiles.
- Low production and processing costs.
Disadvantages
- Lower thermal resistance compared to metals and ceramics.
- Higher susceptibility to chemical and thermal degradation.
New manufacturing and processing techniques
Traditional methods
- Injection molding: Polymer is heated and injected into a mold. Ideal for mass production of complex parts.
- Extrusion: A continuous process forcing polymer through a die, used for pipes and film.
Advanced methods
- Additive manufacturing (3D Printing): Creates complex parts layer by layer using thermoplastics and thermosets. Essential for prototypes and customized components.
- Electrospinning: Generates ultrafine fibers from a charged polymer solution. Critical for biomedical applications like tissue engineering scaffolds.
- Nanotechnology in polymers: Incorporates nanoparticles into the polymer matrix to enhance properties like mechanical strength, electrical conductivity, and chemical barriers.
Comparative diagram: Thermoplastics vs. Thermosets
Feature | Thermoplastics | Thermosets |
Recyclability | They can be recycled and remodeled. | They are not recyclable from curing. |
Flexibility | High flexibility and adaptability. | Rigid, limited flexibility after molding. |
Thermal resistance | Low thermal resistance (they soften with heat). | High thermal resistance (they do not soften). |
Mechanical strength | Moderate, depending on polymer type. | Excellent, ideal for high voltage applications. |
Applications | Packaging, containers, automotive components. | Aerospace, adhesives, high temperature coatings. |
Prominent examples of polymers and their applications
Macromolecules such as polymers play a critical role across multiple sectors due to their unique properties and adaptability. Below are some key examples:
Healthcare sector
In modern medicine, they are indispensable. Biodegradable sutures made of polyglycolic acid (PGA) and polylactic acid (PLA) safely degrade within the body, eliminating the need for surgical removal. Additionally, medical devices like heart valves and catheters utilize biocompatible polymers such as thermoplastic polyurethane (PU), which combines flexibility and mechanical strength.
Aerospace industry
Lightweight and durable polymers such as polyether ether ketone (PEEK) are fundamental in this industry. PEEK offers high resistance to temperature and wear, making it ideal for structural aircraft components and engine parts. Its lightness enhances energy efficiency in flights, while its thermal stability ensures optimal performance under extreme conditions.
Fashion and textiles
Polyester and nylon are cornerstones of the modern textile industry. Polyester, renowned for its wear resistance and low moisture absorption, is used in sportswear and durable clothing. Meanwhile, nylon is essential for manufacturing hosiery, underwear, and technical fabrics due to its elasticity and strength.
Energy sector
Conductive polymeric materials like PEDOT:PSS (Poly(3,4-ethylenedioxythiophene):polystyrene sulfonate) are transforming solar cells and batteries. These materials enable the production of lightweight and flexible devices, with applications in renewable energy and portable storage.
Oil & gas sector
They play a fundamental role due to their unique mechanical properties, such as corrosion resistance, lightness, flexibility, and durability under extreme conditions like high pressure, elevated temperatures, and corrosive environments.
Protective coatings such as epoxy, polyurethane (PU), and fluoropolymers (PTFE) are widely used to safeguard pipelines, storage tanks, and equipment against chemical and gas-induced corrosion.
In thermal and electrical insulation systems, polymers like polyurethane (PU) and silicone maintain proper temperatures in subsea pipelines and provide reliable electrical insulation on platforms and control systems. For seals and gaskets in valves and pumps, elastomers (NBR, FKM, and PEEK) are ideal due to their wear resistance and ability to function under high pressure and temperature.
Moreover, these materials reinforce offshore platform structures, with epoxy resins and FRP (fiber-reinforced polymer) composites used in decks, ladders, and components resistant to weather and saltwater.
Reinforced polymer pipes (HDPE, PP, and PVC) are crucial for water injection, hydrocarbon transport, and other corrosive liquids due to their chemical resistance and durability.
Advanced polymeric materials like PEEK and polyimides are used in drilling equipment for internal tool parts, such as bearings and valves, that require high mechanical and chemical resistance.
Low-friction internal coatings in pipes, like PTFE, minimize friction during oil and gas transport, enhancing operational efficiency. Expanded polyurethane foams are essential for flotation systems and thermal insulation in subsea applications.
Finally, epoxy resins and unsaturated polyester composites are vital for repairing and maintaining metal structures due to their ability to endure extreme conditions and provide durable adhesion.
In wastewater and residue treatment, PVDF polymer membranes are employed to separate hydrocarbons and treat wastewater, ensuring sustainability in industrial processes. These applications highlight how these materials have transformed the Oil & Gas sector, delivering efficient, durable, and sustainable solutions.
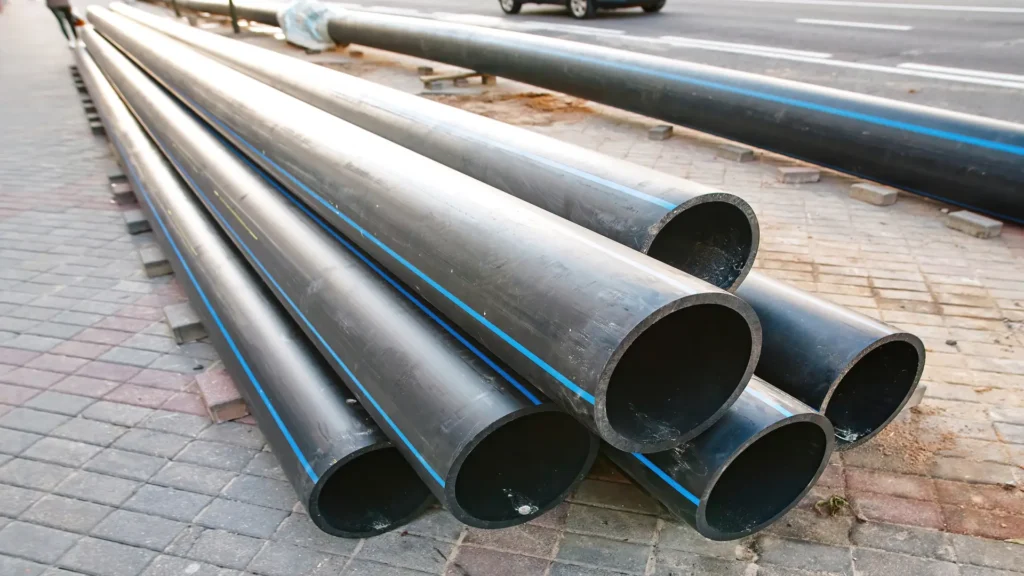
Emerging applications of advanced polymers
- Self-healing polymers are particularly valuable in high-stress applications like aerospace components and medical devices, where maintaining material integrity is critical.
- Biodegradable polymers: Used in eco-friendly packaging and temporary medical devices, reducing environmental impact.
- Advanced polymer composites: Incorporating nanoparticles like graphene to enhance electrical and thermal conductivity. For example, graphene-polymer composites are used in flexible electronic devices and high-precision sensors.
The top 3 polymers for specific applications
- High-density polyethylene (HDPE): One of the most widely used materials in industrial applications due to its mechanical strength, durability, and low cost. It is extensively employed in the production of pipes, food containers, and chemical products because of its resistance to impact, aggressive chemicals, and moisture. Its versatility and ease of processing make it ideal for applications requiring lightweight yet robust materials.
- Teflon (PTFE): Known for its chemical resistance, low friction, and thermal stability, polytetrafluoroethylene is used in non-stick coatings for cookware, medical applications, and electronics. Its ability to withstand extreme temperatures and corrosive environments makes it indispensable. Additionally, its excellent electrical insulation properties make it a key component in cables and electronic circuits.
- Epoxy resins: These thermosetting materials have high mechanical properties and adhesive strength, making them essential in various industrial applications. They are used in structural adhesives, industrial coatings to prevent corrosion, and advanced composite materials such as wind turbine blades, where a combination of stiffness, durability, and wear resistance is required.
Compared to metals, these materials offer lightweight construction, lower costs, and superior corrosion resistance. However, their downside is a lower resistance to heat and tension in extreme applications, often necessitating their combination with other materials
Regulations and standards for polymers
Regulations governing the use of polymers are essential to ensure safety, sustainability, and quality in their applications. In the field of recycling, directives such as the European plastics regulations set strict targets to reduce pollution through the use of recyclable and reusable polymeric materials. These policies have fostered innovations in biodegradable plastics and more efficient recycling techniques.
Regarding plastics in contact with food, organizations like the FDA (Food and Drug Administration) in the United States and the EFSA (European Food Safety Authority) in Europe oversee and regulate polymers used in food packaging. These entities ensure that materials comply with safety standards to prevent the migration of harmful chemicals into food.
Finally, quality standards developed by organizations such as ASTM International and ISO are crucial for standardizing tests for the mechanical, thermal, and chemical properties of polymeric materials, ensuring their performance and reliability in critical applications.
Challenges and opportunities in polymer usage
The widespread use of these materials presents significant challenges, especially in terms of environmental impact. Plastic pollution, including microplastics accumulating in marine and terrestrial ecosystems, is one of the most pressing issues. Addressing the environmental challenges associated with macromolecules, particularly polymers, requires innovative recycling and biodegradation techniques. However, both industry and academia have developed solutions to mitigate these effects.
Advanced recycling techniques, including chemical processes to break down these materials into their original monomers, are gaining traction as a viable solution. Additionally, biodegradable polymers like polylactic acid (PLA) are emerging as sustainable alternatives for single-use applications.
Technological advancements have led to the development of self-healing materials that extend the lifespan of products by automatically repairing cracks and minor damages. These self-healing polymers address a key challenge in material science by reducing the need for frequent replacements and maintenance, thus contributing to a more sustainable material lifecycle. Similarly, fully recyclable materials are being created, designed to retain their properties through multiple processing cycles, aligning with the principles of the circular economy.
The circular economy seeks to close the life cycle of polymers through strategies such as designing materials to be easily recyclable and developing compostable polymeric materials that decompose safely in controlled environments. Recent innovations, such as additives that facilitate recycling and chemical recycling technologies, are revolutionizing polymer waste management.
Despite the challenges, these materials represent a unique opportunity to address global issues such as sustainability, energy efficiency, and access to advanced materials. With adequate regulations, technological innovations, and sustainable strategies, the future of polymers can align with environmental and social goals. This positions polymers as key materials for technological development and environmental preservation.
Frequently asked questions
How can you distinguish a thermoplastic from a thermoset polymer?
A thermoplastic polymer can soften and be reshaped repeatedly when heated, such as polyethylene or polypropylene, making it easier to recycle. In contrast, a thermoset polymer like epoxy cannot be reshaped after curing due to its three-dimensional crosslinked network, providing high thermal and mechanical resistance.
Which polymeric materials are safe for food use?
Materials such as high-density polyethylene (HDPE), polypropylene (PP), and polycarbonate (PC) are commonly approved for food use. These materials comply with regulations from entities like the FDA and EFSA, ensuring they do not release harmful substances when in contact with food. They are used in packaging, kitchen utensils, and reusable bottles.
What are the most sustainable polymers?
Biodegradable polymers, such as polylactic acid (PLA) and starch-based materials, are considered the most sustainable as they decompose under natural or controlled conditions. Additionally, 100% recyclable polymers, such as those using advanced polyethylene recycling, contribute to sustainability by reducing environmental impact.
Conclusions
Polymers are fundamental to modern science and industry due to their mechanical properties, versatility, adaptability, and wide range of applications, spanning health care to energy. Their ability to replace traditional materials, enhance efficiency, and lower costs has transformed key sectors. However, their environmental impact presents urgent challenges requiring innovative solutions.
The future of these materials lies in the development of sustainable and high-performance polymers. Self-healing polymers exemplify how innovation can redefine material longevity and reduce waste across industries. Additionally, the focus on the circular economy and stricter regulations are driving a shift toward more responsible use of these materials.
Exploring more about macromolecules, including polymers, provides insight into how these materials are shaping a more sustainable and efficient future. Exploring more about polymers and their impact provides insight into how these materials are shaping a more sustainable and efficient future. Innovation in this field is crucial to addressing global challenges and ensuring a balance between technological development and environmental preservation.
References
Own Source