Plastic welding is a strategic process in numerous industries seeking efficient and durable solutions for joining thermoplastic materials. This method of molecular joining of thermoplastics has experienced a considerable boom due to the unique properties of plastics and the increasing demand for lightweight, durable and customized products. Through techniques such as ultrasonic, laser and thermal resistance welding, it is possible to achieve high quality bonds that withstand various operating conditions.
This article focuses on the basic fundamentals, main methods, benefits and most common applications.
What is plastic welding?
Plastic welding is a thermal or mechanical process used to join plastic parts by the controlled application of heat, pressure or vibration. Unlike metal welding, this process accommodates the reversible thermal behavior of thermoplastics, allowing the contact surfaces to melt and the molecular chains to interlock upon cooling. This results in a strong, homogeneous bond, suitable for applications requiring high mechanical and chemical resistance.
Their efficiency and precision eliminate the need for adhesives or additional mechanical elements, offering reliable solutions for industrial assemblies and complex repairs.
History and evolution
The development of this type of welding began in the mid-20th century as an alternative to chemical adhesives and mechanical joining. Early methods, such as thermal resistance welding, were used for basic applications in industries such as construction. In the 1960s, ultrasonic welding revolutionized the automotive and medical industries due to its precision and speed.
More recently, laser welding has expanded joining capabilities in complex applications, such as electronic packages. The incorporation of industrial automation has optimized repeatability, joint quality and operational efficiency.
Types of plastics that can be welded
Plastic welding is possible on a wide variety of thermoplastics due to their linear molecular structure and their ability to melt and solidify repeatedly without degrading. Among the most common are:
- Polypropylene (PP): High chemical resistance, excellent for piping and chemical components.
- Polyethylene (PE): Impact resistant and low cost, used in containers and pipelines.
- Polycarbonate (PC): Transparent and resistant, ideal for optical devices and housings.
- Acrylonitrile butadiene styrene (ABS): Rigid and impact resistant, common in the automotive industry.
- Polyethylene terephthalate (PETE or PET): Barrier properties, used in liquid containers.
- Polymethylmethacrylate (PMMA): High optical clarity, used in signage and decorative panels.
- Polyvinyl chloride (PVC): Corrosion resistant, used in plumbing systems and electrical conduits.
Even some rigid and flexible plastics can be welded using advanced techniques, although they require precise adjustments in parameters such as temperature and pressure to avoid deformation or poor joints.
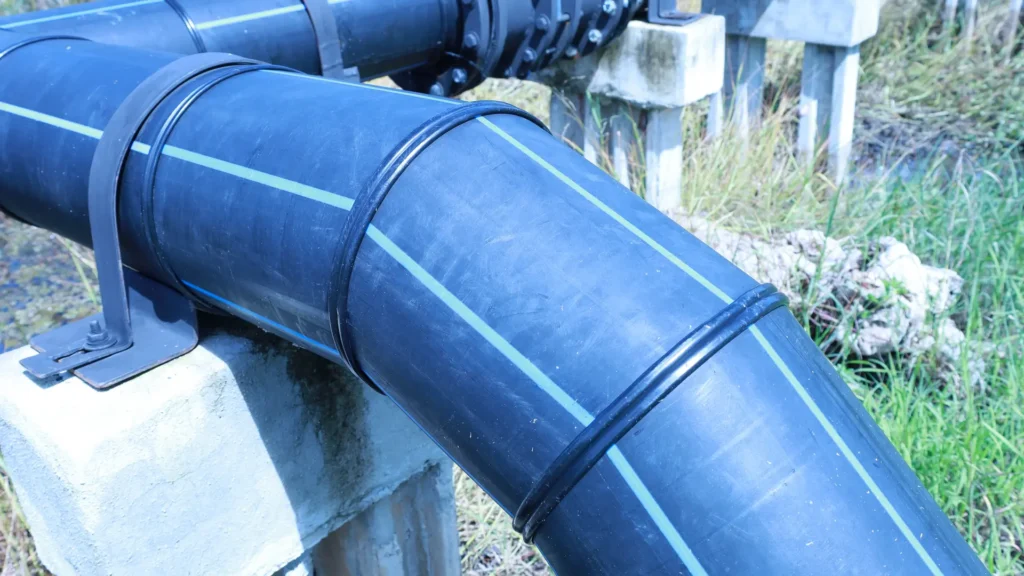
Plastics that cannot be welded
Not all plastics are suitable for welding due to their molecular structure. Prime examples include:
- Elastomers: They have a flexible cross-linked structure, where the molecular chains are joined by cross-links that allow them to recover their original shape when the heat effect ceases. This elastic behavior prevents the elastomers from permanently deforming during welding.
- Duroplastics (or thermosets): They have a rigid cross-linked structure with tight molecular bonds. When subjected to heat, these plastics do not melt, but decompose thermally, which makes them incompatible with welding processes.
Plastic welding methods
This type of welding offers techniques adapted to the specific needs of materials, geometries and application environments.
Ultrasonic welding
This method uses high-frequency mechanical vibrations (15-40 kHz) to generate frictional heat at the interface of the parts, which melts the material and forms molecular bonds in 0.1 to 2 seconds. It is ideal for thin PVC foils, being outstanding for its speed and precision; and it is used for electronic and automotive applications.
Laser welding
Employs a directed laser beam to melt thermoplastics with precision. Suitable for complex geometries and automated production lines, it requires laser-absorbing materials or specific additives. Variants such as contour welding and quasi-simultaneous welding optimize heat distribution. Used in highly aesthetic applications in medical and consumer sectors.
The following video shows how laser welding of plastics produces clean, accurate parts in fast cycle times. Courtesy of Extol, Inc.

Laser plastic welding – From design to finished parts.
Radio frequency welding
It uses high frequency electromagnetic fields to generate heat and bond materials with chemical dipoles such as PVC and polyamides. It is ideal for inflatable products and industrial textiles due to its ability to create airtight bonds.
Vibration welding
It generates frictional heat by linear or orbital motion between parts under pressure, melting the material and forming a solid bond. It is effective for semi-crystalline and amorphous plastics, including reinforced plastics; it is used in large parts or with complex geometries.
Hot plate welding
It heats the surfaces of the parts through a metal plate with temperature control. Useful for semi-crystalline thermoplastics such as PP and PE, it is a robust option for piping systems and automotive components.
Infrared welding
It is a non-contact technique that uses infrared radiation to melt thermoplastic surfaces. Infrared radiation is a form of electromagnetic radiation, which is transmitted as black or red light, depending on the wavelength emitted. It is efficient for aesthetic applications, such as in the automotive and medical industry, because of its clean joints.
Spin welding
Joins parts with circular geometries by rotational friction. One part rotates at high speed while the other remains fixed under axial pressure. It is effective in reinforced materials and specific applications such as tanks and pipes with circular joints.
The following informative video explains the types of plastics that are suitable for this technique and a detailed description of the main methods. Courtesy of RAPID DIRECT.

Plastic welding processes: Types, applications, limitations.
Plastic welding benefits
Technical
At a technical level, it offers high durability, with joints that resist mechanical stresses and chemical aggressions, guaranteeing reliable performance. Its versatility allows its application in a wide range of thermoplastic materials and complex designs. In addition, it stands out for its precision, since it makes it possible to work with parts of intricate geometries and reduced dimensions, while maintaining strict tolerances.
Economic
This method significantly reduces operating costs by eliminating the need for adhesives and secondary processes, such as mechanical assembly. Methods such as ultrasonic welding, with extremely short cycle times, optimize production times, increasing efficiency and reducing energy consumption on automated lines.
Sustainability
This welding method facilitates the circular economy by being compatible with recyclable plastics, allowing their reuse without compromising the quality of the joints. Also, by avoiding solvents and chemical adhesives, it reduces environmental impact, making it a greener and safer option for operators and the environment.
Industrial applications
Plastic welding is widely applied in the following industrial sectors:
- Automotive: Production of fuel tanks, air conditioning systems and battery casings, reducing overall vehicle weight to improve efficiency.
- Electronics: Encapsulation of circuits, manufacturing of connectors and protective housings by ultrasonic and laser welding, guaranteeing a clean assembly.
- Medical: Manufacture of blood bags, catheters and sterile packaging, where precision and clean joints are essential.
- Containers and packaging: Bag sealing and container assembly through thermal welding, standing out for its efficiency.
- Construction: Pipe and tank fabrication for water and drainage systems, with hermetic and durable joints.
- Aerospace: Production of light and resistant components to optimize efficiency and safety in aircraft.
Emerging trends and technologies in plastic welding
Plastics welding has advanced significantly, driven by the need for greater efficiency, precision and sustainability. Automation and robotics have optimized processes, improving repeatability and reducing human error. These technologies stand out in industries such as automotive and electronics, where high quality, design flexibility and reduced operating costs are required.
Advances in laser welding have expanded its applicability to different materials, offering precise control over accurate parameters such as power and speed. This allows for strong joints and aesthetic finishes, being especially useful in medical and consumer sectors that demand high precision and visual quality.
Sustainable welding has gained prominence with the development of techniques that are compatible with recyclable and biodegradable plastics. Methods such as infrared and ultrasonic methods eliminate solvents and chemical adhesives, promoting more environmentally friendly processes. These trends highlight the industry’s commitment to innovation and sustainability in plastics manufacturing.
Conclusions
Plastic welding is a technology that is constantly evolving to meet the demands of modern industry. Current trends, such as automation, the use of recyclable plastics and advances in laser welding, reflect a focus on sustainability and process precision. These innovations are transforming sectors such as automotive, electronics and medicine, enabling the creation of lighter, more durable and sustainable products.
As industries seek solutions that balance cost, efficiency and environmental responsibility, plastic welding is positioning itself as an indispensable tool. Its ability to adapt to advanced materials and complex applications ensures its relevance in the future, leading innovation in manufacturing and design.
References
- https://www.aristegui.info/tipos-de-soldadura-de-termoplasticos/
- https://www.herrmannultraschall.com/es/soldadura-con-ultrasonido/soldadura-de-plasticos/soldadura-de-plastico-por-ultrasonido
- https://www.aristegui.info/8-tecnicas-y-metodos-de-soldadura-de-plastico/
- https://www.hotairtools.com/blog/what-is-plastic-welding/?srsltid=AfmBOoqsAQpHbvUbMDb9WjMz6DBYs_degCfjo2otF8pe6NCYCV3c1x1Z