Table of Contents
- Introduction
- What is pitting corrosion?
- What causes pitting corrosion?
- How does pitting corrosion occur?
- Pitting corrosion in stainless steel and other metals
- How to prevent pitting corrosion?
- Material selection: High-alloy steels with molybdenum, chromium, and nitrogen
- Surface treatments: Passivation, electropolishing, and coatings
- Environmental control: Managing chloride exposure and pH
- Cathodic protection: Sacrificial anodes and impressed current systems
- Corrosion inhibitors in industrial applications
- How to repair pitting corrosion?
- Corrosion mechanisms beyond pitting: Rust formation, crevice corrosion, and material resistance
- Conclusions
- References
Introduction
Pitting corrosion is a highly localized and destructive form of material degradation that affects metals, especially those that rely on a protective passive layer, such as stainless steel. Unlike uniform corrosion, which wears away metal surfaces uniformly, pitting corrosion manifests itself in a localized form by forming deep cracks or pits that can penetrate the material. Pitting compromises structural integrity, which makes it particularly dangerous, as it often goes unnoticed until catastrophic failure occurs.
Comparatively, crevice corrosion occurs in confined spaces where stagnant electrolytes cause localized attack, while galvanic corrosion results from electrochemical interactions between dissimilar metals in conductive environments. In contrast, pitting corrosion is unpredictable and can develop even in seemingly stable conditions due to local breakdowns in the passive layer.
Industries such as marine, oil & gas, and chemical processing are especially vulnerable to stainless steel corrosion, as chloride-rich environments accelerate pit initiation. Stainless steel, known for its corrosion resistance, can still succumb to pitting in high-chloride settings like seawater, industrial cooling systems, and chemical processing plants. Applying surface treatments plays a crucial role in mitigating these risks, enhancing the material’s ability to resist corrosion while extending its service life.
Understanding the causes, prevention methods, and repair strategies for pitting corrosion is essential to mitigate its impact on the industry. This article explores in detail the factors that trigger this phenomenon, how it can be prevented, and the most effective solutions to repair the damage caused, ensuring the safety and durability of materials in harsh conditions.
What is pitting corrosion?
Pitting corrosion is a localized electrochemical attack on a metal’s surface that leads to the formation of small, deep cavities. Unlike generalized corrosion, which uniformly affects the surface, pitting is highly concentrated, often initiating at specific sites where protective oxide layers break down. This phenomenon is self-sustaining, meaning once a pit forms, its internal chemistry promotes further localized attack, deepening the damage.
Watch this video where we explain in detail the key factors behind pitting corrosion and how to prevent its impact on critical infrastructure. Source: Captain Corrosion.

Pitting corrosion – Forms of corrosion.
Characteristics of pitting corrosion
- Localized attack: Occurs in isolated points rather than across the entire metal surface.
- Unpredictability: Pits can develop without visible warning signs, making detection difficult.
- High damage potential: Even a small pit can lead to mechanical failure, reducing structural integrity.
Pitting corrosion is a major concern in industries where stainless steel corrosion occurs under aggressive environmental conditions. For example:
- Marine industry: Stainless steel components in ship hulls, pipelines, and offshore platforms experience accelerated pitting due to high chloride ion concentrations in seawater.
- Oil & Gas sector: Pitting in pipelines and storage tanks can lead to leaks and failures, compromising operational safety.
- Chemical processing plants: Exposure to acidic environments and halides in chemical processing equipment significantly increases the risk of pit formation.
One of the most effective ways to mitigate pitting corrosion is through surface treatments, such as passivation and electropolishing, which enhance the corrosion resistance of metals by reinforcing the protective passive layer.
What causes pitting corrosion?
The role of chloride ions, oxygen levels, and acidic environments
Pitting corrosion is primarily driven by the presence of chloride ions (Cl⁻), which disrupt the passive oxide film on metals like stainless steel. Chlorides create localized weak spots in the protective layer, leading to pit initiation. High oxygen concentration can also contribute by intensifying anodic and cathodic reactions. Additionally, acidic environments (low pH) accelerate the dissolution of metal, enhancing the growth of pits.
Breakdown of passive oxide layers in stainless steel
Stainless steel relies on a thin, self-repairing chromium oxide (Cr₂O₃) passive layer to resist corrosion. However, in chloride-rich environments or under mechanical stress, this layer can break down locally, exposing the metal to direct attack. Once the passive film is compromised, anodic dissolution occurs at the affected site, leading to pitting. Implementing surface treatments such as passivation helps restore the integrity of the oxide layer and prevents further localized damage.
Electrochemical mechanisms behind pit initiation and propagation
Pitting is an electrochemical process involving:
- Initiation: The localized breakdown of the passive film creates an anodic site.
- Propagation: Inside the pit, metal dissolution occurs, generating metal cations (Mⁿ⁺) that hydrolyze, lowering pH and making the pit environment more acidic.
- Autocatalytic growth: The increasing acidity within the pit accelerates metal dissolution, while the surrounding surface remains passive, leading to continuous deepening.
Connection with crevice corrosion and other localized corrosion forms
Pitting corrosion shares similarities with crevice corrosion, where localized attack occurs in confined spaces with stagnant electrolytes. However, pitting can occur on open surfaces where local breakdown of the passive layer takes place. Understanding this mechanism is critical for industries that rely on stainless steel corrosion resistance, as unexpected failures can compromise safety and operational efficiency.
How does pitting corrosion occur?
Pitting corrosion follows a multi-phase process that begins with localized damage to the protective passive layer of metals and evolves into an aggressive, self-sustaining form of corrosion that can lead to catastrophic failures.
Initiation phase: Breakdown of passivity in localized areas
The initiation of pitting corrosion occurs when the passive oxide layer of a metal, such as stainless steel, is compromised. This breakdown can be triggered by:
- Chloride ions (Cl⁻), which penetrate weak points in the passive film.
- Localized mechanical stress that induces microcracks in the protective layer.
- Surface contamination, such as deposits of dirt, biofilms, or corrosion byproducts.
Once the passive layer is breached, the exposed metal becomes an anodic site, while the surrounding intact surface acts as the cathode, creating a localized electrochemical cell.
Applying surface treatments such as electropolishing can help reduce these surface irregularities and eliminate potential sites for pitting initiation.
Propagation phase: Self-Sustaining electrochemical attack
After initiation, pitting corrosion propagates through an autocatalytic mechanism. Inside the pit, metal dissolution releases metal cations (Fe²⁺, Ni²⁺, Cr³⁺), which hydrolyze in the presence of water, producing hydrogen ions (H⁺) and lowering the local pH. This acidification accelerates the metal dissolution process, leading to further penetration.
Simultaneously, chloride ions are attracted into the pit, forming highly aggressive conditions that sustain the reaction. Since the surrounding area remains cathodic and protected, the corrosion remains highly localized but devastating.
Autocatalytic mechanism leading to deep pits and structural failure
Once a pit forms, it continues to grow deeper, as the acidic environment inside prevents passivation from reforming. Unlike uniform corrosion, where material loss is distributed, pitting corrosion weakens the material at specific points, making it more susceptible to:
- Perforation of pipes and tanks.
- Structural failures in load-bearing components.
- Reduced mechanical integrity, increasing the risk of fractures.
Industries combat this through regular non-destructive testing (NDT) methods like ultrasonic testing (UT) and eddy current testing (ECT) to detect subsurface pits before failures occur.).
Pitting corrosion in stainless steel and other metals
Why stainless steel corrosion is often associated with pitting?
Despite its reputation for corrosion resistance, stainless steel is highly susceptible to pitting when exposed to chloride-rich environments, such as seawater, chemical processing plants, and food processing facilities.
To enhance pitting resistance, industries implement surface treatments such as protective coatings, fluoropolymer linings, and advanced alloying techniques to improve the performance of stainless steels in aggressive conditions.
This vulnerability arises due to:
- Breakdown of the chromium oxide passive layer, which is essential for corrosion resistance.
- Localized attack from chloride ions, which destabilizes the protective film.
- Environmental factors like elevated temperatures and stagnant conditions that promote pit formation.
Pitting Resistance Equivalent Number (PREN) and alloy selection
To predict the resistance of stainless steels to pitting, engineers use the Pitting Resistance Equivalent Number (PREN), calculated as:
PREN = %Cr + (3.3 × %Mo) + (16 × %N)
A higher PREN indicates better pitting resistance. For example:
- 316 stainless steel (PREN ~25) offers moderate pitting resistance due to molybdenum.
- Duplex and super duplex stainless steels (PREN 35-45) provide superior resistance due to higher molybdenum and nitrogen content.
Case study: Pitting corrosion in stainless steel vs. other alloys
In offshore oil & gas applications, traditional 304 stainless steel often fails due to pitting in seawater exposure, whereas super duplex stainless steels (e.g., 2507) show exceptional performance. This highlights the necessity of alloy selection for high-chloride environments.
How to prevent pitting corrosion?
The prevention of pitting corrosion is a critical challenge across various industries, particularly those operating in aggressive environments such as marine, chemical, and petrochemical sectors. This type of localized corrosion can compromise the integrity of metal structures and equipment, starting in small areas that, if left unchecked, may lead to catastrophic failures.
To mitigate this phenomenon, it is essential to implement strategies ranging from proper material selection to controlling the operating environment. Below, we will explore the main techniques and methods for preventing pitting corrosion, ensuring the durability and safety of exposed components.
Material selection: High-alloy steels with molybdenum, chromium, and nitrogen
Using stainless steels and alloys with higher molybdenum (Mo), chromium (Cr), and nitrogen (N) enhances pitting resistance. Duplex stainless steels and super austenitic grades (e.g., AL-6XN, Hastelloy C-22) are commonly chosen for aggressive environments.
Surface treatments: Passivation, electropolishing, and coatings
- Passivation: Removes free iron and strengthens the protective oxide layer.
- Electropolishing: Improves surface smoothness, reducing areas where pitting may start.
- Protective coatings: Fluorinated polymers and ceramics provide an additional barrier against corrosion.
Environmental control: Managing chloride exposure and pH
- Minimizing chloride ion exposure prevents passive layer breakdown.
- Maintaining alkaline pH conditions (above 9) reduces the likelihood of pit formation.
- Controlling temperature, as elevated temperatures accelerate pitting rates.
Cathodic protection: Sacrificial anodes and impressed current systems
- Sacrificial anodes (zinc, aluminum, magnesium) provide a preferential site for oxidation, protecting stainless steel structures.
- Impressed current cathodic protection (ICCP) is used in offshore platforms and pipelines to prevent localized corrosion.
Corrosion inhibitors in industrial applications
- Molybdate-based inhibitors help stabilize passive films.
- Organic inhibitors can reduce chloride adsorption on metal surfaces.
- Hydrocarbon-based protective fluids in pipelines displace water and prevent corrosion initiation.
By implementing these strategies, industries mitigate pitting corrosion risks and extend equipment lifespan.
How to repair pitting corrosion?
Once pitting corrosion has occurred, repair strategies depend on the extent of damage.
Methods for surface restoration: Polishing, grinding, and passivation
- Mechanical polishing and grinding can remove surface pits if they are shallow.
- Passivation treatments help restore the chromium oxide protective layer.
- Chemical etching can be used in some applications to dissolve corrosion byproducts.
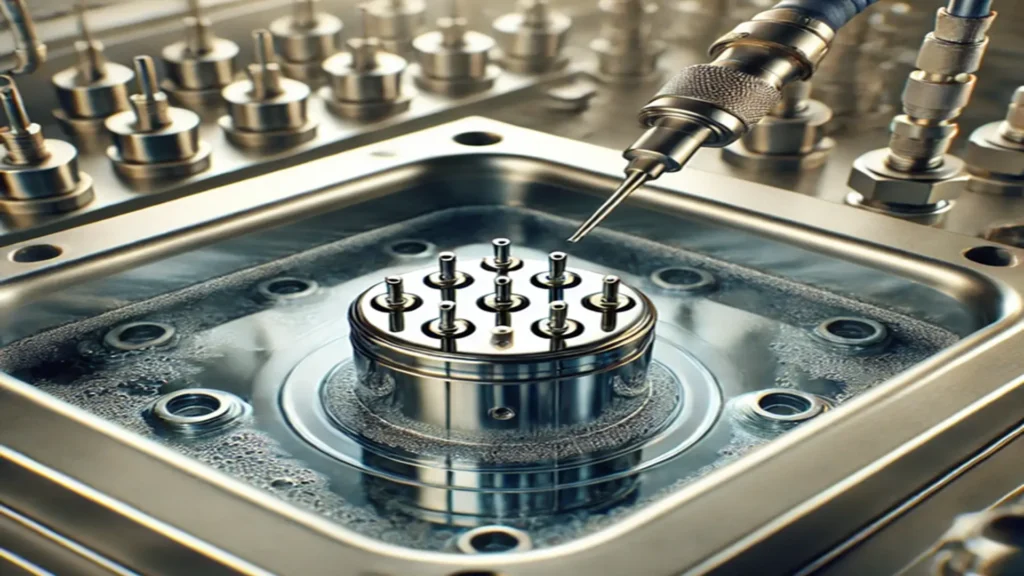
Severe pit repair: Welding, cladding, or replacing components
When pits penetrate deeply, mechanical restoration is insufficient, requiring:
- Welding: Depositing fresh material in localized corrosion sites.
- Cladding: Applying a corrosion-resistant overlay (e.g., inconel, stellite).
- Cold spray coatings: A modern alternative that restores material integrity without excessive heat input.
When structural integrity is compromised: Replace vs. repair
In cases where pitting has severely weakened structural components, decision-making is based on:
- Depth of pits vs. material thickness (if >20% thickness loss, replacement is preferred).
- Criticality of the component (load-bearing vs. non-load-bearing).
- Economic considerations (repair costs vs. new equipment installation).
Regular predictive maintenance using Non-Destructive Testing (NDT) techniques, such as ultrasonic and radiographic inspections, helps detect early-stage pitting, preventing catastrophic failures.
Corrosion mechanisms beyond pitting: Rust formation, crevice corrosion, and material resistance
What causes rust? (Iron oxide formation vs. pitting corrosion)
Rust is a specific type of corrosion that affects iron and steel, resulting in the formation of iron oxides (Fe₂O₃·xH₂O) through an electrochemical process involving oxygen (O₂) and water (H₂O). Unlike pitting corrosion, which is highly localized, rusting occurs uniformly across a metal surface, progressively weakening the material over time. Rust formation is a multi-step reaction where iron dissolves into solution and reacts with oxygen to form a porous and expansive oxide layer, which offers little to no protection against further degradation.
In contrast, pitting corrosion is far more insidious due to its autocatalytic nature, where once a pit forms, its internal chemistry sustains further metal dissolution. While rust leads to surface degradation, pitting corrosion can cause rapid and localized material failure, making it a significant concern for critical infrastructure.
Differences between pitting corrosion and crevice corrosion
Both pitting corrosion and crevice corrosion are forms of localized corrosion, but they differ in initiation mechanisms and environmental conditions:
- Pitting corrosion occurs on exposed surfaces where the passive film breaks down, typically due to chloride attack.
- Crevice corrosion occurs in shielded areas (gaps, overlaps, and under fasteners), where oxygen depletion leads to an acidic microenvironment, promoting localized attack.
Although both types of corrosion can coexist, crevice corrosion is more dependent on geometrical constraints, while pitting can initiate on any vulnerable surface.
Impact of metal surface conditions on corrosion resistance
The surface condition of a metal significantly influences its corrosion resistance. Factors such as surface roughness, contamination, and residual stress play a role in determining susceptibility to localized attack.
- Smoother surfaces (achieved through electropolishing or mechanical finishing) reduce sites for pitting initiation by eliminating micro-crevices where aggressive ions accumulate.
- Surface contamination (iron particles, welding residues) can create local galvanic cells that trigger pitting corrosion or accelerate passive layer breakdown.
- Cold working or mechanical stress can induce residual stress, leading to stress corrosion cracking (SCC), which, combined with pitting, further weakens oaterials.
The role of steel, stainless steel, and other metals in corrosion science
Different metals exhibit varying levels of resistance to pitting and other corrosion forms:o
- Carbon steel is highly susceptible to uniform corrosion and rust, requiring coatings or cathodic protection.
- Stainless steel, while resistant due to its chromium oxide layer, remains vulnerable to pitting in chloride environments.
- Nickel-based alloys (inconel, hastelloy) and super duplex stainless steels are specifically designed to resist pitting and crevice corrosion, making them ideal for extreme environments.
Understanding the interactions between metals, environmental conditions, and protective measures is crucial for designing long-lasting structures and industrial systems resistant to pitting corrosion and related phenomena.
Conclusions
Pitting corrosion presents a critical challenge in the industry due to its localized, unpredictable, and highly destructive nature. Unlike other types of corrosion, its ability to cause severe damage without visible warning signs makes it a significant risk to structural and operational safety in sectors such as maritime, oil and gas, and chemical processing. A deep understanding of its initiation and propagation mechanisms is essential for developing effective prevention and mitigation strategies.
The proper selection of corrosion-resistant materials, such as stainless steels with high levels of molybdenum and nitrogen, combined with the application of surface treatments and protective coatings, can significantly reduce the risk of pit formation. Additionally, environmental control, by limiting exposure to high chloride concentrations and maintaining favorable pH conditions, is key to extending the service life of materials.
Predictive maintenance, using non-destructive testing (NDT) techniques such as ultrasonic and radiographic inspections, enables the early detection of pitting before it leads to catastrophic failures. The combination of prevention, continuous monitoring, and effective repair is the key to minimizing the impact of pitting corrosion and ensuring the long-term integrity of critical infrastructure.
References
Own source