In the complex energy and petrochemical industry, pipeline construction and operations stand out as fundamental pillars for the transportation of hydrocarbons. These critical systems not only connect production points with consumption centers, but also represent unique challenges in terms of safety, environment and operational efficiency.
Managing these challenges begins with a thorough pipeline risk analysis. This approach is not only a preventive measure, but a fundamental strategy that underpins the integrity and reliability of critical infrastructures that transport millions of barrels of hydrocarbons on a daily basis worldwide.
According to data from the International Pipeline Association, safe and efficient transportation through these systems is responsible for the movement of 60% of the oil and gas consumed globally. Without meticulous risk analysis, the consequences of failure can be devastating, not only in economic terms, with losses that can exceed billions, but also in irreparable environmental impacts and significant risks to public health.
This article dives into the practices and regulations governing risk analysis, offering a guide for businessmen, managers and professionals in the energy, industrial and related sectors interested in optimizing the safety and efficiency of these vital infrastructures.
Importance of risk analysis in pipeline construction
Pipelineis the name given to the pipeline and related facilities used to transport oil, its derivatives and biobutanol over long distances. The construction of oil pipelines is complex and requires mechanical engineering studies for their design, as well as environmental impact studies in the areas where they will be laid.
Pipeline construction and operation involves multiple phases, each with its inherent risks. From design to operation and maintenance, pipeline risk analysis provides a basis for identifying, assessing and mitigating potential threats. This practice is not only crucial to prevent spills or leaks, but also guarantees the safety of operations, protects the environment and ensures business continuity.
The following video is presented below to complement the content of this topic “the process of building a pipeline”. Courtesy of X-Machines.
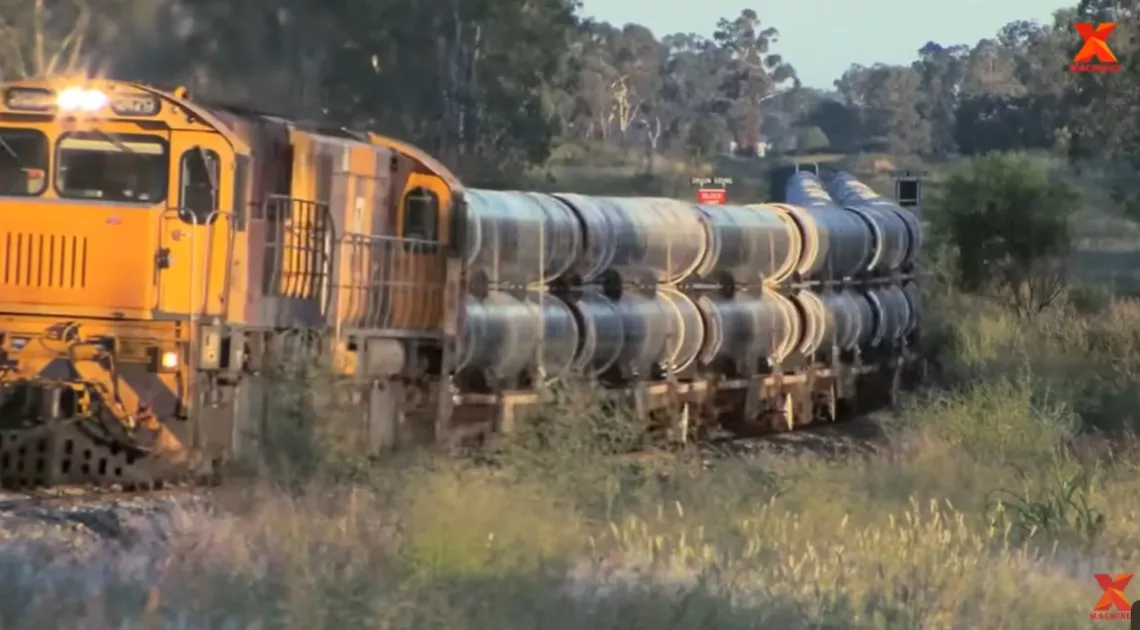
Construction process of one of the largest oil and gas pipelines in the world.
In quantitative terms, it is estimated that the implementation of integrity management and risk analysis programs can reduce pipeline incidents by up to 40%.
Risk identification
Every analysis begins with the identification of risks. In the context of pipelines, this ranges from technical failures, such as corrosion and mechanical failures, to external challenges, such as environmental impacts and natural disasters. The methodology for this phase is diverse, ranging from Preliminary Hazard Analysis (PHA) to Failure Mode and Effects Analysis (FMEA), underlining the importance of a comprehensive approach.
Effective risk identification is the foundation on which all other phases of risk analysis are built. By understanding and anticipating the unique challenges facing pipelines, from construction to operation and maintenance, the industry can move toward safer and more sustainable management of this vital infrastructure.
Risk assessment and analysis
Once the risks have been identified, the next step is to evaluate them quantitatively. Using Quantitative Risk Analysis (QRA), engineers can determine the likelihood and potential consequences of each identified risk.
This process is supported by standards for pipeline construction such as API 1160, oriented to the integrity management of pipeline systems carrying hazardous liquids, and ASME B31.4 (American Society of Mechanical Engineers), providing guidelines for the design, construction, inspection, testing and maintenance of pipeline systems for liquid hydrocarbons, petroleum products, liquid natural gas (LNG), carbon dioxide, and cryogenic liquids.
Mitigation strategies
With a thorough risk analysis, customized mitigation strategies are developed. From the design to withstand adverse conditions to the selection of advanced materials and the implementation of cathodic protection systems, each measure is carefully chosen to minimize the identified risks.
Adherence to pipeline construction standards is essential to ensure the long-term integrity of these infrastructures. He American Petroleum Institute is the most influential institution worldwide in terms of engineering standards for the construction of oil pipelines, being API 5L (Specifications for Line Pipe) the applicable specification for the construction of pipelines for the transportation of crude oil, gas, as well as hydrocarbon derivatives. The latest version of API 5L was released in October 2007 in its 44th edition.
Steel pipe pipelines are constructed by joining on site (field) series of pipes of the required diameter that have been brought to the laying site, the joining is usually by welding. The pipes, on the other hand, can have diameters from 1/2″ (12.7 mm) to 144″ (approximately 360 cm) and come from pipe mills that can use various methods for their manufacture; according to the API 5L standard, the most commonly used methods are:
- Seamless (a type of pipe that is not welded).
- ERW (Electrical Resistance Welding or Electrical Resistance Welding today known as High Frequency Welding or HFW).
- SAW (Submerged Arc Welding). Of this type there are SAWL (with longitudinal seam) and SAWH (with helical or spiral seam).
Continuous monitoring and management
Risk analysis does not end once the pipeline is in operation. Risk management is a continuous cycle that includes regular inspection and integrity monitoring. Regular inspections, pipeline integrity monitoring using techniques such as pigging inspection (internal inspection with special devices) and corrosion monitoring are performed. An example of remote inspection is the one used by Morken Group used in this content to illustrate to readers the topic in question.
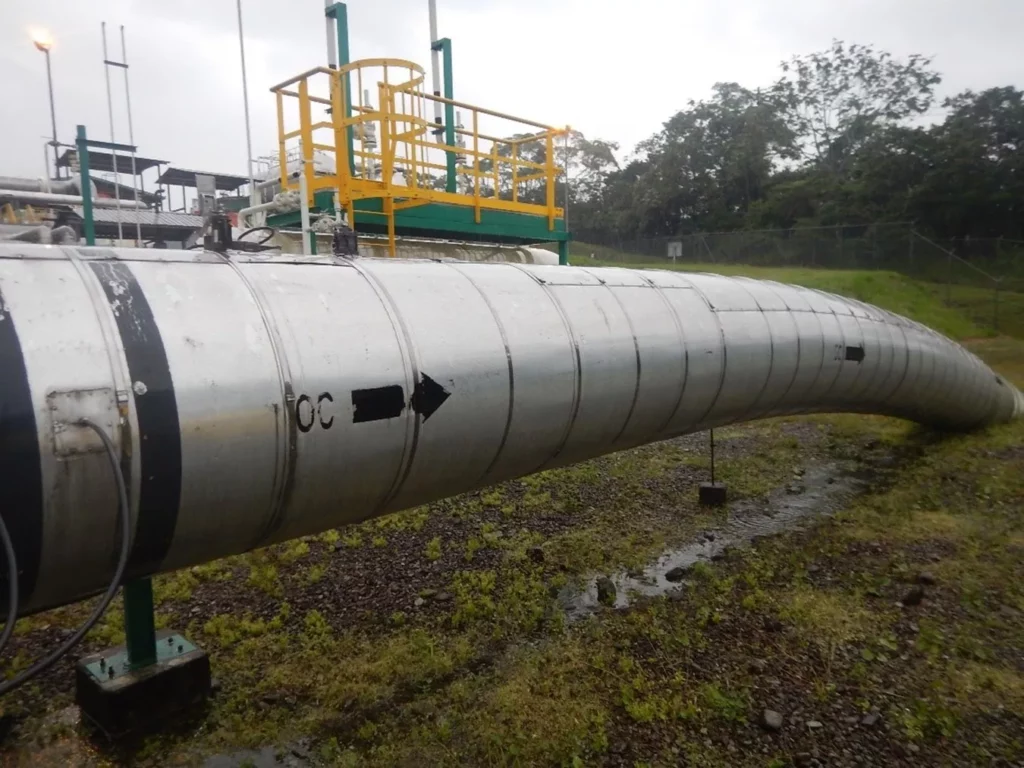
API (American Petroleum Institute) standards, has a number of key standards for pipelines, including:
- API 5L: Specifies requirements for the manufacture of two specification levels of steel pipeline pipe.
- API 1104: Establishes welding practices for pipelines and related facilities.
- API 1160: Aimed at managing the integrity of piping systems that transport hazardous liquids.
These standards provide guidelines for continuous monitoring and reassessment of risks, ensuring that any changes in operating conditions or discoveries of new vulnerabilities are managed effectively.
Emergency preparedness and response
Pipelines can be the target of vandalism, sabotage or even terrorist attacks. In warfare, pipelines are often the target of military tactics, as the destruction of pipelines can seriously disrupt enemy logistics.
An integral part of risk analysis is emergency planning. This component ensures that, in the event of an incident, quick and effective actions can be implemented to minimize impacts. The performance of drills and coordination with local authorities are standard practices in this phase, emphasizing the importance of thorough preparation to prevent spills or leaks.
A practical but regrettable example of this point is the accident of January 18, 2019, where a PEMEX pipeline exploded in the state of Hidalgo, due to the drilling and misuse of the pipeline, leaving a preliminary toll of 66 dead and 79 injured. This case shocked the world and is where point 6 of this practice emphasizes a good plan to be prepared for any emergency.
Conclusions
Risk analysis in pipeline construction and operations is a fundamental pillar to ensure the efficiency, safety and sustainability of hydrocarbon transportation. Through a rigorous methodology that encompasses risk identification, assessment, mitigation and continuous monitoring, as well as emergency preparedness, organizations can address the challenges inherent in these critical systems.
Adherence to standards by owners, standards for pipeline construction and the implementation of best practices in risk analysis not only fulfill regulatory obligations, but also reinforce corporate reputation, strengthen stakeholder confidence and ensure a socially and environmentally responsible operation.
Safe and efficient pipeline construction and operations are a common goal that benefits everyone, and by engaging in pipeline risk analysis, we can move towards a safer and more sustainable energy future.
“Protect your energy future: act now.”
References
- American Petroleum Institute (API)
- API 5L: “Specification for Line Pipe”.
- API 1104: “Welding of Pipelines and Related Facilities”.
- API 1160: “Managing System Integrity for Hazardous Liquid Pipelines”.
- American Society of Mechanical Engineers (ASME)
- ASME B31.4: “Pipeline Transportation Systems for Liquids and Slurries”.