Table of Contents
- What is operational reliability in maintenance?
- Benefits in operational reliability in maintenance
- Effective maintenance strategies for operational reliability improvements
- How to create a Reliability-Centered Maintenance plan?
- Effective Maintenance Management
- Computerized Maintenance Management System (CMMS)
- Conclusion
In contemporary business, particularly in the industrial energy sector, operational reliability improvements emerge as a fundamental pillar to ensure efficiency, safety, and competitiveness. This reliability is achieved through effective maintenance strategies that not only prevent unforeseen failures but also optimize resources and extend equipment lifespan.
This article focuses on the concept of operational reliability improvements, employing the most effective maintenance strategies, utilizing best practices in industrial maintenance, and available technologies.
What is operational reliability in maintenance?
It is the organization’s capacity to perform its functions optimally within a specific timeframe and under operational conditions. It concerns the probability that equipment, processes, and systems function correctly over a specified period.
Operational reliability in maintenance defines the likelihood of a system or component executing its required functions under specific conditions for a set period. In maintenance, this entails ensuring machines and systems are always ready, operate efficiently, and without unexpected failures during the production cycle. The main objectives of Operational Reliability in Maintenance are outlined below:
- Minimizing equipment and process downtime.
- Reducing maintenance and repair costs.
- Increasing productivity and efficiency.
- Enhancing workplace safety.
To achieve effective operational reliability improvements, it is necessary:
- Implement effective maintenance management strategies: Preventive maintenance, predictive maintenance, reliability-centered maintenance, etc.
- Have a safety and prevention culture: Employee training, risk identification, implementation of control measures.
- Utilize appropriate tools and technologies: Maintenance software, condition monitoring, data analysis, computerized maintenance management system (CMMS).
- Manage risks effectively: Risk analysis, contingency plans, change management.
Benefits in operational reliability in maintenance
- Profitability: Cost reduction, increased productivity.
- Safety: Reduced risk of accidents.
- Customer satisfaction: Higher availability of products and services.
- Enhanced company image: Increased trust from customers and investors.
- Effective maintenance strategies for operational reliability improvements
To achieve improvements in operational reliability in industries, it is crucial to implement effective maintenance management strategies. These strategies aim not only to prevent failures and reduce downtime, but also to optimize equipment performance and prolong their lifespan. Below are some effective strategies:
Effective maintenance strategies for operational reliability improvements
To achieve improvements in operational reliability in industries, it is essential to implement effective maintenance management strategies. These strategies aim not only to prevent failures and reduce downtime, but also to optimize equipment performance and prolong their lifespan. Below are some effective strategies:
Preventive Maintenance (PM)
- Description: It involves performing planned maintenance management interventions based on established schedules or predetermined operational conditions, with the aim of preventing failures before they occur.
- Advantages: Reduces downtime, extends equipment lifespan, minimizes repair costs, improves safety.
- Disadvantages: Can be costly if unnecessary tasks are performed, not always effective in preventing all failures, requires a well-defined maintenance plan.
- Example: Changing the oil of an engine every 5,000 kilometers, conducting periodic inspections of industrial machinery.
- Effectiveness: Reduction of downtime by up to 30%, reduction of maintenance costs by up to 15%, increase in equipment lifespan by up to 20%.
Preventive Maintenance (PM) stands out as an essential and effective strategy for most industrial equipment. The key lies in a flexible and adaptable plan to changing operational conditions. The success of this tool is based on the precise execution of scheduled tasks, ensuring the reliability and efficiency of the equipment over time.
Predictive Maintenance (PdM)
- Description: Computerized maintenance management software (CMMS) is based on monitoring equipment condition to determine when maintenance is needed. It utilizes real-time monitoring technologies and diagnostic tools to predict potential equipment failures. This includes vibration analysis, thermography, oil analysis, and others. It relies on monitoring the condition of the equipment to determine when maintenance is needed.
- Advantages: Minimizes downtime, optimizes maintenance, improves reliability, enhances safety.
- Disadvantages: Requires initial investment in monitoring technology, requires trained personnel to use the technology and interpret data, developing a data management process can be complex, integration with existing management systems may be challenging.
- Example: Monitoring motor vibrations to detect bearing wear: Oil analysis to detect oil contamination and component wear. Vibration analysis with measurement equipment. Below is a representative image of vibration monitoring using a sensor.
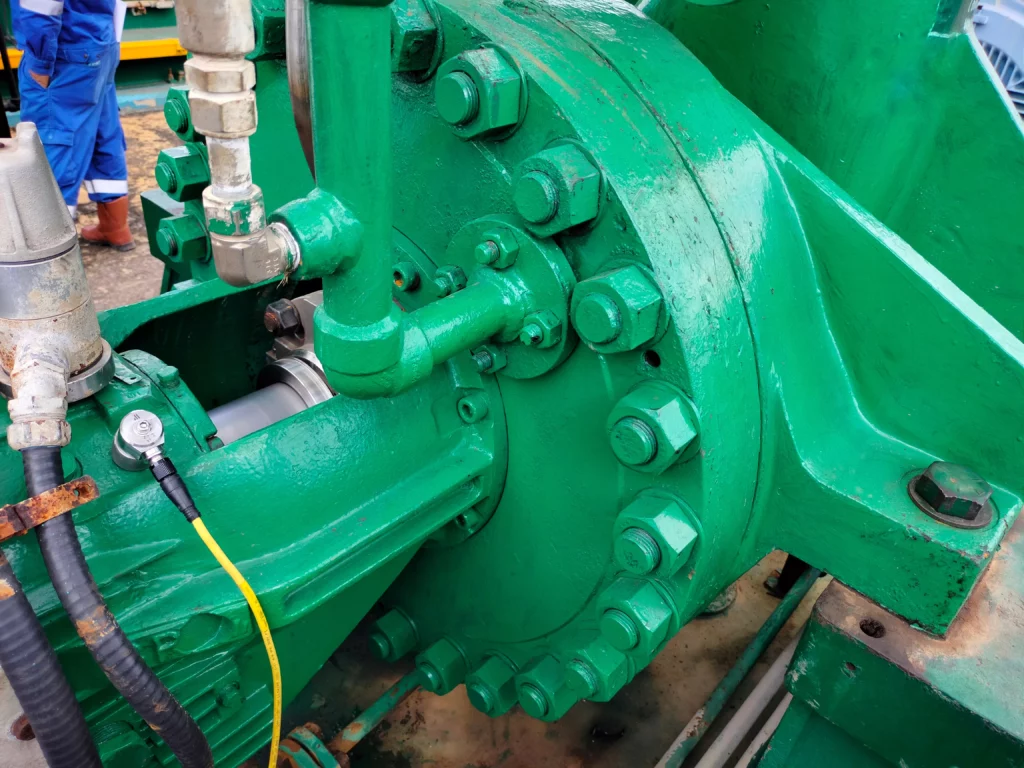
- Effectiveness: Reduction of downtime by up to 40%, reduction of maintenance costs by up to 25%, increase in reliability by up to 50%.
Predictive Maintenance (PdM) is optimal for critical, expensive, or high-failure-rate equipment. Its implementation requires an initial investment and sustained commitment. In the energy, industrial, and related sectors, PdM stands out as a powerful tool for achieving operational excellence.
Reliability-Centered Maintenance (RCM)
- Description: Reliability-Centered Maintenance (RCM) is a maintenance strategy based on comprehensive analysis of equipment to determine the most critical failures and establish the most effective maintenance strategies. This approach focuses on understanding and managing the failure modes of critical equipment to enhance operational reliability. It involves evaluating equipment functions, identifying failure modes, and implementing specific maintenance strategies for each type of failure.
- Advantages: Maximizes reliability, reduces costs, improves safety, optimizes asset management.
- Disadvantages: Requires complex and detailed analysis, needs highly trained personnel, RCM success depends on data quality, RCM can be inflexible.
- Example: Implementing an RCM program for a fleet of aircraft, analyzing the causes of failure of critical equipment to determine the best maintenance strategies.
- Effectiveness: Reduction of downtime by up to 50%, reduction of maintenance costs by up to 30%, increase in reliability by up to 60%.
Reliability-Centered Maintenance (RCM) is paramount for companies with critical equipment; RCM ensures operational excellence by optimizing equipment maintenance and reliability.
How to create a Reliability-Centered Maintenance plan?
- Define Objectives: Establish specific objectives for the maintenance plan, such as reducing downtime, improving safety, or decreasing costs.
- Identify Critical Equipment: Analyze equipment and determine which are critical for operations. Consider factors such as failure frequency, production impact, and repair costs.
- Analyze Failure Modes: Identify the most common failures of critical equipment and determine root causes.
- Develop Maintenance Strategies: Select the most suitable maintenance strategies for each critical equipment, such as preventive maintenance, predictive maintenance, or RCM.
- Implement the Maintenance Plan: Establish an action plan for implementing the maintenance plan, including assigning responsibilities, allocating resources, and budgeting.
- Monitor and Evaluate the Plan: Measure and evaluate the performance of the maintenance plan and make adjustments as necessary.
Effective Maintenance Management
It constitutes the first step towards strengthening operational reliability, involving planning, scheduling, and execution of maintenance activities aimed at minimizing interruptions and maximizing equipment lifespan. The adoption of best practices in industrial maintenance is fundamental in defining specific methodologies for each equipment or system.
Computerized Maintenance Management System (CMMS)
The Computerized Maintenance Management System (CMMS) provides a series of key benefits:
- Maintenance Scheduling: Through its use, efficient planning and scheduling of maintenance activities are achieved, ensuring they are carried out at the right time to avoid unplanned interruptions in production.
- Asset Management: Facilitates tracking and management of all company assets, including equipment, machinery, and facilities, aiding in optimizing their performance and extending their lifespan.
- Maintenance History Tracking: Detailed records of all maintenance activities performed on each piece of equipment can be maintained, facilitating trend analysis, identification of recurring issues, and informed decision-making.
- Inventory Control and Purchasing: Assists in managing spare parts inventory and materials required for maintenance, optimizing stock levels, and facilitating timely ordering.
- Cost Tracking: Using this software enables precise tracking of costs associated with asset maintenance, aiding in identifying areas for improvement and optimizing the maintenance budget.
- Regulatory Compliance: Regulates compliance with regulatory and statutory requirements related to asset maintenance by providing accurate documentation and records of activities performed.
In summary, a CMMS helps improve efficiency, reliability, and profitability of maintenance operations by providing a centralized platform for managing and tracking all activities related to asset maintenance.
Conclusion
Operational reliability and the adoption of effective maintenance strategies, along with advanced technologies, not only enhance competitiveness and bolster market confidence, but also ensure safe and profitable operations. These improvements represent a smart investment towards sustainability and long-term success in the business sector.
“Boost your efficiency now”
References
Own Source.