Table of Contents
- Operational reliability management
- How to implement operational reliability
- Analysis of operational reliability in the industry
- How technology and training can improve operational reliability
- The influence of operators on operational reliability
- Impact of artificial intelligence on operational reliability
- Success stories in the implementation of operational reliability
- Conclusion
Modern industry is faced with increasing technological influence to maximize efficiency and minimize costs. To achieve these goals, organizations have turned to implementation of operational reliability with innovative approaches in the industry; which represents the incorporation into the productive system of a series of processes of continuous improvement in a consistent manner, using diagnostic tools and analysis methodologies with new technologies to optimize the management, planning, execution and control of industrial processes.
Operational reliability management
It is a holistic approach to asset management that focuses on improving the reliability and performance of equipment, processes and systems, based on the concept that the reliability of equipment and processes is essential for operational efficiency, higher production and improvement of operational safety. It involves identifying critical assets, evaluating current reliability, and implementing design and maintenance improvements to increase equipment life. It also involves developing a proactive approach to problem identification and resolution, continuous improvement, and change management.
How to implement operational reliability
The main steps include the following.
- Identification of critical assets: Key point for the success of the implementation of operational reliability. Critical assets are those that are essential to the operation of the organization and that have a significant impact on production, safety, and profitability.
- Current reliability assessment: It is essential to identify critical assets to determine the current level of reliability and performance. This involves performing a root cause analysis to identify the problems and the underlying causes of the failures found.
- Implementation of improvements: It must be carried out in a systematic and controlled way, ensuring that the improvements are effective and that no new problems are introduced. This implies changes in maintenance management, the implementation of new processes or the adoption of new technologies.
- Monitoring and measurement: They are essential to evaluate the performance and effectiveness of the improvements implemented and make adjustments as necessary.
Analysis of operational reliability in the industry
Organizations obtain several benefits when implementing this methodology.
- Improved efficiency: Increases the availability and capacity of equipment and processes, which improves operational efficiency and reduces costs associated with downtime and unscheduled maintenance.
- Reduction of operational risks: Reducing operational risks associated with assets, processes and systems, improves security and reduces the risk of unforeseen incidents.
- Improved profitability: By reducing the costs associated with the maintenance, repair and replacement of equipment and processes, the production and efficiency of the systems increases, generating greater income in the organizations.
- Continuous improvement: It is a hierarchical element of the implementation of operational reliability, periodic evaluations of reliability and performance must be carried out, identifying new opportunities for improvement and ensuring that the plans are effective and sustainable.
How technology and training can improve operational reliability
A common barrier in organizations is the lack of investment in technology and staff training. The implementation of operational reliability requires the acquisition of innovative technologies, monitoring and analysis tools to evaluate the effectiveness of the implemented strategy.
On the other hand, having mastery of the processes is important for the job; It is necessary to train and train all the personnel involved, complementing their skills and knowledge will result in a progressive advance in the implementation and development of operational reliability in organizations. It is essential that companies understand the importance of these investments and make them to achieve success and a competitive advantage in the implementation of this methodology.
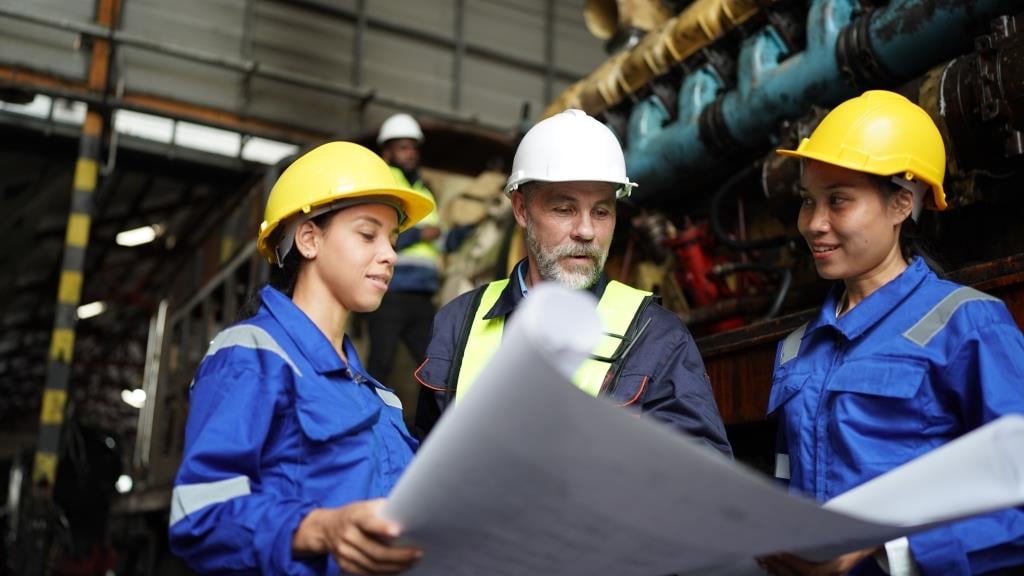
The novelties do not stop, new methodologies, software, tools, devices, computer programs, training techniques in operational reliability among others emerge daily, which generate solutions and make the environment between professionals and work more practical and productive for the companies.
It is important that the leaders of the organizations are committed to the strategy and provide the necessary resources for its implementation and efficiency. In addition, it is essential that leaders provide a clear and coherent vision of the strategy and communicate its importance and benefits to all workers in the company.
The influence of operators on operational reliability
Operators need practical skills and up-to-date knowledge, it is a prerequisite for general monitoring and evaluation of equipment and systems. They know and trust their team, once they have received instructions on the methodologies and practices to be implemented, they will more efficiently collect and analyze the data, where they can prepare checklists that meet their own requirements. Contributing with the determination of the evaluation intervals and times is also essential, since the work must be carried out while the equipment is operating.
Impact of artificial intelligence on operational reliability
Artificial intelligence (AI) is increasingly being used to improve operational reliability in various industries. Processing large amounts of data and finding hidden patterns to identify problems before they become failures is a powerful resource to reduce operating costs, improve availability and operational productivity of industrial plants. Additionally, it can help predict when a failure is likely to occur, allowing companies to take preemptive action to avoid costly outages.
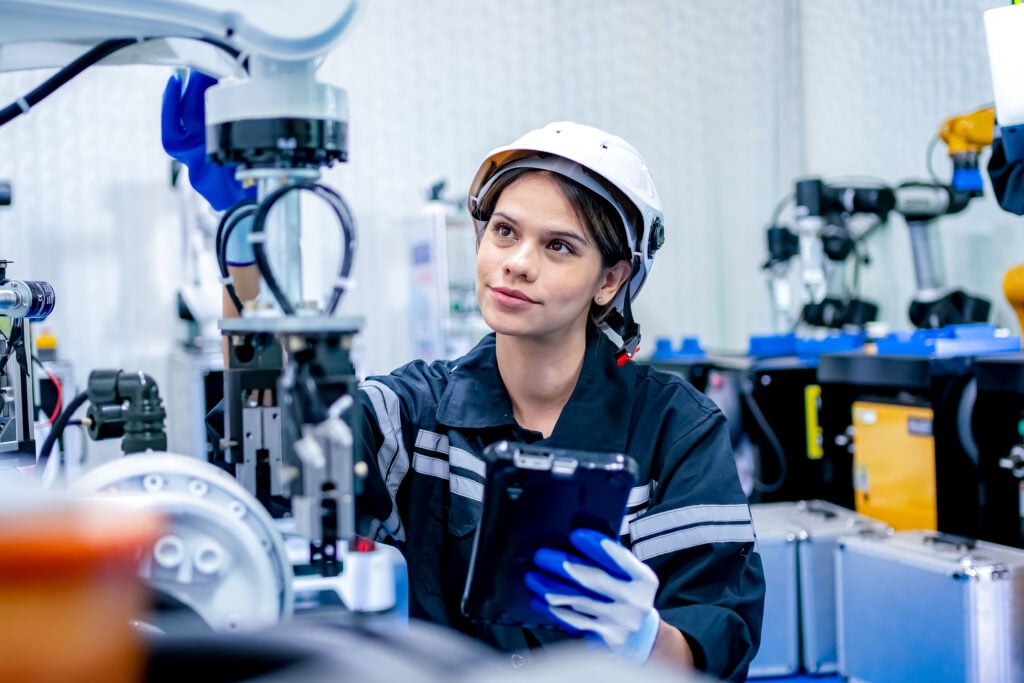
AI makes it possible to quickly identify the root cause of process deviations or equipment failures, materialize savings in a short time, predict events in real time to take immediate corrective actions, and define the foundations and strategies for large-scale digitization programs.
One way AI is being used is by monitoring operating conditions in real time and identifying any abnormal changes in equipment performance. This may include detection of vibrations, changes in temperature or pressure, and other indicators of an operational malfunction.
Another way that AI can improve operational reliability is through predictive analytics. Examine the historical data of a piece of equipment and use machine learning algorithms to predict when it is likely to fail. This allows companies to plan preventative maintenance instead of waiting for the event to occur, reducing downtime and associated costs.
Companies using AI to improve operational reliability
General Electric Storm Readiness: Combines historical weather and outage data to accurately predict the impact of weather conditions on the grid and safely prepare first responders.
IBM : Empower operations, quality and maintenance teams on remote asset monitoring, asset health and predictive maintenance, powered by AI
Honeywell: Features Honeywell Forge Energy Optimization , which uses artificial intelligence (AI) to autonomously and continuously optimize a building’s HVAC system to help save energy. In relation to industrial facilities, many offers focus on the digitization of assets to optimize their performance and also that of people.
Success stories in the implementation of operational reliability
There are multiple companies worldwide that have successfully implemented operational reliability systems in their production processes for some time.
A well-known example in the industry is the British oil and gas giant British Petroleum (BP), which has adopted an approach that involves all levels of the company, from top management to field professionals. The company has established an operational reliability framework that includes policies, standards, and practices to ensure the integrity of equipment and processes, and to prevent accidents.
The ConocoPhillips company, after implementing an operational reliability program at its Liquefied Natural Gas (LNG) plant in Australia, significantly improved plant performance due to equipment reliability and reduced the risk of operational incidents.
Conclusion
Implementing operational reliability can be a winning strategy to improve an organization’s efficiency, safety, and profitability, while reducing unplanned downtime by predicting equipment problems before they occur.
The implementation of operational reliability has been very successful in the industry globally, because it prioritizes the identification of critical assets, the evaluation of current reliability, and the implementation of design and maintenance improvements to increase the performance of equipment and processes. .
References
- https://cmc-latam.com/2022/02/23/analisis-de-criticidad-que-es-y-por-que-es-importante/
- https://cmc-latam.com/wp-content/uploads/2019/09/Aplicación-de-inteligencia-artificial-e-ingeniería-de-confiabilidad-en-el-mejoramiento-de-productividad-en-operaciones-de-petróleo-gas-Brújula.pdf
- https://www.ge.com/digital/sites/default/files/download_assets/storm-readiness-ebook-spanish-ge-digital.pdf
- https://www.ibm.com/mx-es/business-operations/asset-performance-management
- https://www.automaticaeinstrumentacion.com/texto-diario/mostrar/3922392/soluciones-transversales-honeywell-digitalizacion-automatizacion-edificios