Table of Contents
- Introduction
- Challenges of welding in extreme environments
- New welding techniques on offshore platforms
- Technological advances and automation in platform welding
- Innovations in steam compressors on platforms
- Benefits and limitations of new welding techniques on platforms
- Success stories: Applications of new welding techniques on platforms
- Future of welding on platforms: Continuous innovation and sustainability
- Conclusions
- References
Introduction
Welding on offshore platforms presents unique challenges that require precision, strength, and adaptability. Offshore welders must possess advanced skills and utilize cutting-edge tools, such as robotic welding, to operate in extreme conditions, facing factors like high humidity, saltwater exposure, and temperature fluctuations. These elements, common in marine environments, demand continuous adaptation of offshore welding techniques and the development of innovative methods to ensure structural integrity on oil and gas extraction platforms.
The role of a platform welder goes beyond creating robust joints; it also involves overcoming environmental and accessibility obstacles. Unlike other industrial settings, offshore welding requires high precision on materials that withstand the pressure and adverse conditions of marine depths. This type of work demands a combination of human skill and technological advancement to ensure that each weld endures the harsh marine environment.
In this context, this article explores new welding techniques on platforms and how they have been developed specifically to help welders meet these challenges. The evolution of offshore welding is fundamental to maximizing efficiency and safety in operations, where every welded joint plays a crucial role in the sustainability of operations.
Challenges of welding in extreme environments
Platform welding jobs in extreme environments are particularly challenging due to constant exposure to adverse conditions that compromise joint durability. High-pressure welding is essential to counter the impact of marine depths, where intense pressures can affect material stability and strength. Additionally, platform welders must confront accelerated corrosion caused by saltwater, which can damage even the strongest joints without proper materials and techniques.
Underwater welding is another essential technique in these settings, enabling repairs and assembly on the seabed without removing structures to the surface. However, this technique requires high precision and specialized equipment capable of withstanding low temperatures and pressure. Welders must be skilled at adapting to these environmental factors and highly trained to operate safely in hard-to-reach areas and challenging positions.
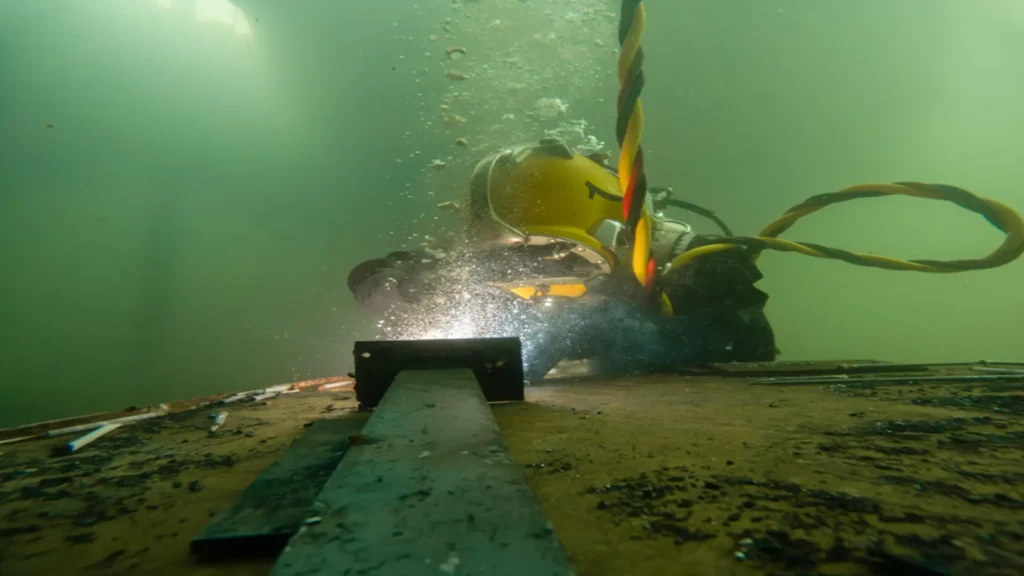
In addition to these challenges, robotic welding and welding automation are transforming the role of platform welders, especially in high-pressure environments where risks to humans are significant. Robotic welding enables joints in hard-to-reach locations and enhances safety by reducing direct exposure to extreme conditions.
Offshore platform welding requires a combination of advanced techniques and technological innovation to ensure joint longevity and strength, keeping structures safe and operational under adverse conditions. Each platform welder must be prepared to face these challenges with precision and the support of cutting-edge technology.
New welding techniques on offshore platforms
Offshore platforms present unique conditions requiring continuous innovation in welding techniques. These advanced methods allow platform welders to create stronger, safer, and more durable joints, tackling the challenges of marine welding in extreme environments, such as high pressure and corrosion exposure.
Friction Stir Welding (FSW)
Friction Stir Welding (FSW) is a technique where a rotating tool generates friction as it moves across the metal surface, creating a joint without melting the material. This minimizes thermal distortion, making it ideal for marine applications where corrosion resistance and structural durability are essential. In offshore platforms, FSW is particularly useful for joining materials like aluminum, which must withstand high humidity and saltwater.
Hybrid Laser-GMA Welding
Hybrid Laser-GMA welding combines the precision of a laser beam with the filler capacity of a metallic arc, allowing for deep penetration and precision on thick materials. This method significantly reduces work time, optimizing efficiency on large platforms. In marine welding applications, the hybrid technique is ideal for high-demand structural components like beams and supports that require precision and strength.
High-Pressure Solid-State Welding
High-pressure solid-state welding creates strong joints without melting materials, which is useful in environments where constant pressure and vibrations challenge structural integrity. This method is commonly applied on offshore platforms to join structural components that must endure high levels of pressure and continuous wear.
Specialized Underwater Welding
Underwater welding is essential for repairing and maintaining underwater structures, allowing platform welders to make joints without bringing the structure to the surface. Typically performed with coated electrodes, this technique requires highly trained welders due to challenging visibility and pressure conditions. It is indispensable for maintaining the structural integrity of submerged platforms and equipment.
The video below shows a case study of underwater repair in a real-life environment, showing the application of advanced underwater welding techniques to address corrosion challenges on offshore platforms. Video courtesy: Millennium Marine Contractors Ltd.

Underwater corrosion damage repair (Underwater welding).
Advanced TIG and MIG Welding in Controlled Environments
Advanced TIG and MIG techniques are ideal for applications requiring high precision, particularly in controlled environments on the platform. These methods create strong, corrosion-resistant joints necessary for critical components that demand strict tolerances and high-quality finishes in the marine environment.
Robotic welding and AI-Driven Automation
Robotic welding and automated systems with artificial intelligence (AI) are crucial innovations for offshore platforms. Welding robots can operate in hard-to-reach areas where risks to human welders are high. These automated systems offer superior precision and consistency, with integrated sensors that monitor parameters in real time, adjusting welding to maintain optimal standards.
Additionally, AI-driven automation enhances operational safety and efficiency by enabling platform welders to remotely supervise processes, minimizing exposure to extreme conditions. The ability of these systems to work continuously and at high speed also reduces project timelines and optimizes resource use.
Technological advances and automation in platform welding
Robotic welding is revolutionizing the role of platform welders, bringing efficiency and safety to the most demanding environments. The use of welding robots enables welds in hard-to-reach areas or controlled environments, where precision is critical to maintaining structural integrity.
Welding robots are particularly useful on platforms, operating in confined spaces and under high-pressure and humidity conditions typical of marine welding. Their precision allows for continuous welding on large structures, reducing work time and improving joint quality. Robots also allow platform welders to focus on supervisory and control tasks, reducing their direct exposure to potentially hazardous conditions.
Welding automation reduces human error and ensures superior consistency in joints, which is essential in structures requiring high strength. In addition to enhancing safety, automation allows processes to be faster and more efficient, optimizing resource use and minimizing maintenance costs. Advances in sensors and integrated monitoring systems also enable real-time welding adjustments, adapting to specific marine environment conditions.
In platform welding environments, automation not only improves efficiency but also enables welds in controlled settings, maintaining quality standards in high-pressure, saline conditions. Welding robots and automation remain key tools in platform modernization, allowing joints to be stronger and more precise under the most extreme conditions.
Innovations in steam compressors on platforms
Steam compressors have evolved significantly, providing improvements that optimize platform welding operations. These innovations allow for precise regulation of pressure and temperature in controlled environments, creating ideal conditions for platform welders and other offshore professionals.
Advanced steam compressors are designed to maintain a constant pressure flow, crucial for automation in welding tasks. These devices feature pressure and temperature control systems that automatically adjust to environmental conditions, ensuring stability in welding processes. Additionally, smart compressors are equipped with sensors that monitor equipment status in real-time, detecting potential issues before they impact operations.
On platforms, the ability of steam compressors to adapt to environmental fluctuations reduces failure risk and facilitates a safe, controlled work environment. This is crucial in welding processes requiring stable conditions to prevent defects and ensure joint quality. With these innovations, steam compressors enhance efficiency, safety, and sustainability in offshore platform industrial processes.
Benefits and limitations of new welding techniques on platforms
New welding techniques on platforms offer significant benefits, especially for platform welders working in extreme environments. One of the main advantages is increased joint strength, essential in marine welding where materials face high pressures and constant exposure to saltwater. These advanced techniques enable durable, highly resilient welds that resist corrosion and wear, extending the lifespan of offshore structures.
Another key benefit is adaptability to different materials, which facilitates the creation of complex structures with various types of metals and alloys. This is fundamental on platforms, where specialized materials are commonly used to meet operational demands. Additionally, innovations in high-pressure welding and underwater techniques enable complex welds in extreme conditions, offering precision and stability that enhance project safety and effectiveness.
However, these techniques also present limitations. Initial implementation costs are often high due to the specialized equipment and advanced technology required. For platform welders, using these techniques involves intensive training, as operating in extreme conditions with high-tech equipment requires specific skills. Additionally, transporting and handling this equipment on offshore platforms poses significant logistical challenges, complicating the welding process in some circumstances.
Despite these limitations, the benefits of new welding techniques on platforms outweigh their drawbacks in the long run, reducing maintenance costs and improving the strength and safety of structures in offshore environments.
Success stories: Applications of new welding techniques on platforms
Various offshore platforms have successfully implemented advanced welding techniques, optimizing operations and extending the lifespan of structures. A notable example is the use of Friction Stir Welding (FSW) on platforms in the North Sea, where this technique has improved corrosion resistance of key components exposed to extreme conditions. This innovation has allowed platform welders to create robust, durable joints, essential for withstanding harsh marine and weather conditions.
Another successful case is the implementation of underwater welding on platforms in the Gulf of Mexico, where critical repairs were performed on submerged structures without lifting parts to the surface. This technique enabled welders to complete complex repairs in record time, ensuring platform structural integrity and reducing operational costs.
Future of welding on platforms: Continuous innovation and sustainability
The future of offshore platform welding points toward continuous innovation with a focus on sustainability. As technology advances, new techniques and welding automation will enable complex tasks to be performed with greater efficiency and lower environmental impact. The integration of welding in controlled environments promises to enhance joint safety and quality, allowing platform welders to work in stable, protected conditions, which is crucial in high-pressure environments with corrosive elements.
Additionally, robotic welding and automated systems will reduce direct exposure of welders to risks inherent in these extreme environments, improving both occupational safety and efficiency. Implementing more precise, automated welding processes will also help minimize resource consumption and waste generation, aligning with offshore industry sustainability goals. As the sector seeks to reduce its environmental footprint, platform welding will continue to adapt to meet higher sustainability and safety standards, driving a safer and more efficient future for offshore operations.
Conclusions
New welding techniques are revolutionizing the work of platform welders, especially in the extreme conditions of offshore platforms. The incorporation of advanced marine welding methods and automation not only improves joint precision and durability but also enhances safety in high-risk operations. These advances enable complex welds tailored to marine conditions, essential for the durability and efficiency of structures.
The integration of advanced methods such as robotic welding and marine welding marks a transformation in industry standards, optimizing both operational times and long-term costs. With constantly evolving technology, platform welding remains a key field for modernization, ensuring offshore facilities operate safely and efficiently in one of the most challenging environments.
References
Own source