Industrial automation is essential for measuring, controlling and optimizing various processes. However, there are important differences between traditional and advanced instrumentation. Traditional instrumentation focuses on basic measurements and monitoring, while advanced instrumentation incorporates automation and data analysis technologies, allowing for more precise and efficient control.
The year 2025 is shaping up to be a revolutionary period for emerging technologies and technological evolution in general. From advances that transform industries to innovations that directly affect the quality of life, these tools are changing the way humans interact with their environment.
In this context, industrial instrumentation, which includes tools and devices designed to monitor and manage variables such as pressure, temperature, flow and level in industrial environments, is key to process optimization. Its role is fundamental to ensure safety, efficiency and consistency in production, minimizing human intervention and errors.
In recent years, instrumentation technologies have progressed significantly, incorporating innovations such as smart sensors, IoT connectivity and predictive analytics. Below, we will examine these technologies and their potential to influence various fields, offering a comprehensive, real-time view of processes, with accurate information for decision making and automation of critical processes.
Differences between traditional and advanced instrumentation
This comparative table summarizes the differences between traditional instrumentation and advanced instrumentation in a very general way:
Aspect | Traditional instrumentation | Advanced instrumentation |
Operation | Manual, operated directly from front panels. | Automated and computer controlled. |
Flexibility | Limited, each device measures a specific variable. | High, allows configuration and control of multiple variables. |
Processing capacity | Low, no data processing or analysis capability. | High, uses software for advanced processing and analysis. |
Interconnectivity | Individual operation; integration requires space and resources. | Connectivity through interfaces (GPIB, VXI), allows remote integration. |
Data presentation | Real-time visualization without storage or analysis options. | Graphical user interfaces (GUI) and data storage for future analysis. |
Accuracy and efficiency | Basic, limited to measuring equipment. | High, employs digital technology and sensors for greater accuracy. |
Application | Specific and punctual measurement. | Use in complex systems and process optimization. |
This table highlights how advanced instrumentation, with its automation, connectivity and processing capabilities, surpasses traditional instrumentation in functionality and accuracy, making it an essential tool in modern industrial and scientific applications.
Benefits of emerging technologies in industrial automation
Emerging technologies in industrial automation are delivering numerous benefits that transform the efficiency and competitiveness of companies. Among the most prominent are:
Improved efficiency and cost reduction
By 2024 and looking ahead to 2025, emerging technologies have dramatically improved efficiency in industrial automation by integrating advanced artificial intelligence and real-time data analytics. This level of efficiency enables rapid adaptation to market fluctuations and customer demand, minimizing waste and increasing productivity.
Automating repetitive and hazardous tasks reduces operating costs by reducing the number of human errors and the need for manual intervention. By 2025, companies adopting these systems are expected to achieve even greater savings in operating and personnel costs through smarter and more flexible automation.
Predictive maintenance and process optimization
In 2024, predictive maintenance has been transformed with the incorporation of advanced sensors and machine learning, allowing machines to anticipate failures before they occur. By 2025, this maintenance capability will become even more sophisticated, integrating prediction and repair automation through autonomous systems and advanced predictive analytics. This will enable companies to optimize equipment uptime and reduce unplanned outages, positively impacting production and revenue.
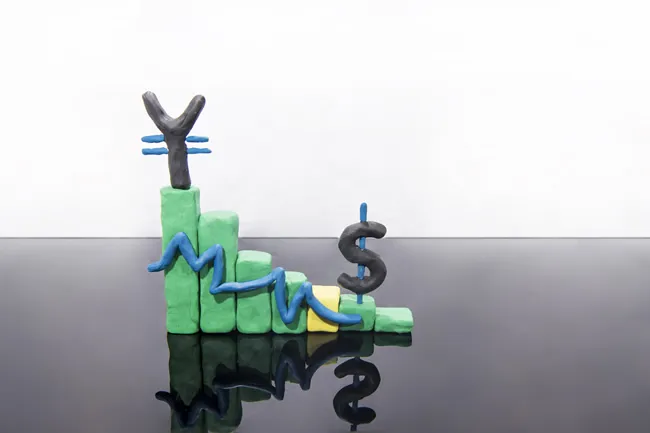
Real-time connectivity and analysis
Connectivity, driven by the Industrial Internet of Things (IIoT), has reached a new level by 2024, enabling companies to collect and analyze large volumes of data from every machine and process in real time. By 2025, this connectivity will be even more optimized, facilitating quick decisions based on accurate and relevant data.
This capability is crucial for companies seeking to remain competitive and respond quickly to events, which will reduce response times and improve the quality of customer service. Improved quality and consistency Today, automation reduces variability in products and ensures a constant level of quality.
This is critical in industries where accuracy and standardization are critical. By 2025, automation will enable even greater consistency, thanks to advances in automated quality control technology and online data analytics that identify and correct defects in real time. This will increase customer satisfaction and brand trust, generating loyalty and better positioning.
Occupational safety and welfare
Safety has been one of the strengths of automation in 2024, where technologies have made it possible to eliminate dangerous or physically demanding tasks for workers. In 2025, automation systems are projected to become even more advanced, incorporating real-time monitoring of environmental conditions and robotic assistance for hazardous tasks, thus promoting a safer work environment. With these innovations, companies not only protect their workers, but also enhance their reputation as responsible employers and reduce costs related to workplace accidents.
These benefits are evidence of how emerging technologies are transforming the industry and will continue to be critical for any company that wants to remain competitive in an increasingly digital and automated marketplace.
Major trends in industrial automation
Industrial automation is undergoing a remarkable transformation, driven by a number of emerging trends that promise to redefine production processes. The following are the main trends in this field:
Collaborative robotics
Collaborative robots, or “cobots,” are designed to work safely and efficiently alongside humans in shared environments. These devices are sensitive to human presence and can perform dangerous or monotonous tasks, improving efficiency and reducing labor fatigue. Their flexibility makes them an ideal choice for industries such as automotive, metalworking, electronics, logistics and healthcare.
Artificial Intelligence (AI) and machine learning
The integration of AI and machine learning enables machines to make decisions based on data and continuous learning. This facilitates failure prediction and process optimization, improving decision making and enabling more effective predictive maintenance. Sectors such as manufacturing, energy and data processing benefit greatly from these technologies. Industrial Internet of Things (IIoT): The IIoT fosters real-time connectivity of devices and machinery, collecting data for analysis and facilitating informed decisions.
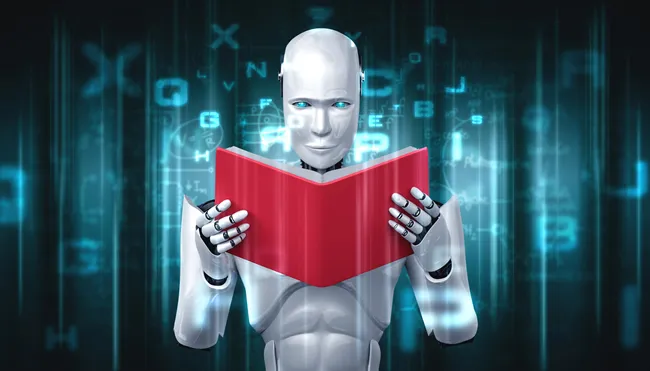
This connectivity enables predictive maintenance, improves efficiency and reduces operating costs, being especially advantageous for sectors such as manufacturing, logistics and energy.
Advanced predictive maintenance
Through the use of sensors and data analytics, advanced predictive maintenance anticipates failures and plans interventions before problems arise. This reduces maintenance costs, minimizes unplanned downtime and extends asset life, benefiting industries such as energy, manufacturing, transportation, automotive and logistics.
Augmented Reality (AR) and Virtual Reality (VR)
These are technologies that are applied in training, product design and problem solving, improving accuracy and efficiency in decision making. These tools facilitate training, design and problem solving, resulting in more accurate and efficient production, with applications in education, product design and healthcare.
Incorporation of renewable energies
The integration of sustainable energy sources, such as solar and wind, into industrial automation aims to reduce the carbon footprint of production. This not only decreases the environmental impact, but also reduces long-term costs, benefiting industries such as the energy, manufacturing, construction and electro-intensive sectors.
Use of modern industrial sensors
Modern industrial sensors are key devices in automation, as they detect and transform physical variables such as temperature, pressure, level and flow into electrical signals that can be processed. These sensors enable real-time process monitoring and control, which improves production efficiency and accuracy.
In addition, their integration with advanced control systems facilitates the implementation of predictive maintenance strategies, reducing downtime and optimizing resources. The evolution of these sensors towards more intelligent and connected versions has been crucial for the development of Industry 4.0 and 5.0, enabling greater interconnectivity and data analysis in industrial environments.
In the field of industrial automation, new technologies are expected to generate significant changes that will increase efficiency, reduce costs and optimize processes in various industries. Collaborative robotics, Artificial Intelligence and the Industrial Internet of Things (IIoT) are revolutionizing production, allowing humans and machines to collaborate safely and effectively.
Advanced predictive maintenance and the use of modern sensors will improve real-time control and monitoring, facilitating a more agile response to potential failures. These innovations, together with the integration of renewable energies, outline a more sustainable, precise and connected future in industrial automation, making companies more competitive and responsible.
Conclusion
Industrial automation, driven by emerging technologies, is revolutionizing production processes by improving accuracy, efficiency and safety. The incorporation of smart sensors, IoT and data analytics is enabling a more detailed, real-time view of operations, helping industries to optimize their processes and reduce human error. In this context, companies that adopt these advanced tools will be better positioned to face future challenges and take advantage of opportunities in an ever-changing market.
References
- https://www.emprenderalia.com/tecnologia-emergente/
- https://www.cursosaula21.com/que-son-los-sensores-de-automatizacion-industrial/