Introduction
The petroleum industry faces constant challenges due to the extreme conditions in which systems operate: high pressure, extreme temperatures and continuous exposure to corrosive substances. These factors demand materials that can maintain structural integrity over long periods of time. In this regard, monel, a nickel-copper alloy, stands out for its corrosion resistance, durability and ability to withstand high-pressure conditions, making it a strategic choice for the oil industry.
This article discusses the importance, types and strategic applications of monel, highlighting how its properties make it indispensable in critical systems in the petroleum industry.
What is monel and its importance to the oil industry?
Monel is a metallic alloy consisting mainly of nickel and copper in a ratio of approximately 2:1 by weight. This composition gives it outstanding corrosion resistance, especially in marine and acidic environments. In addition, it is characterized by its ductility, resistance to high temperatures and non-magnetic properties, which ensures its performance in extreme conditions.
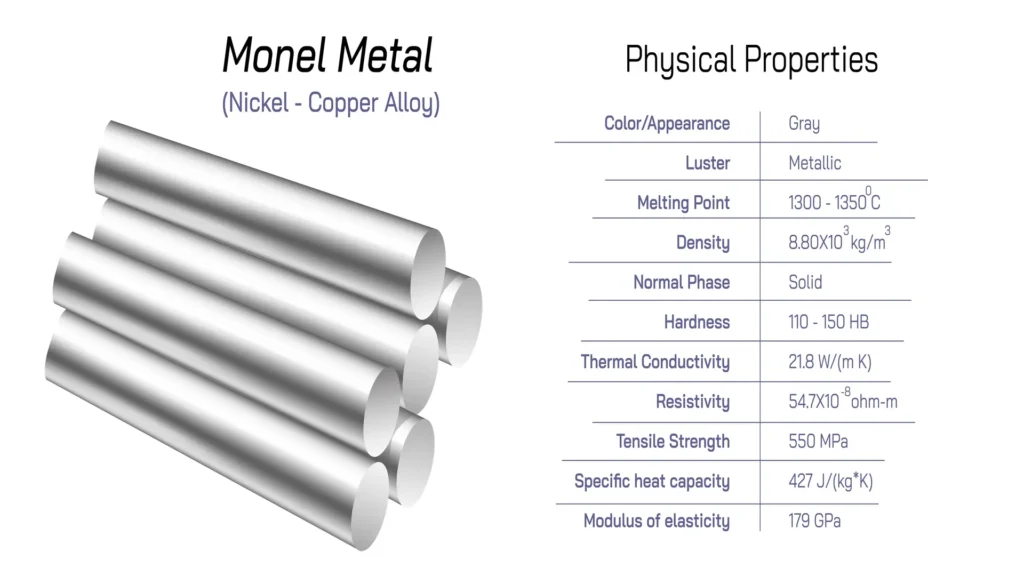
Through a thermal precipitation or aging process, the properties of the alloy are optimized by incorporating titanium and aluminum into its base composition. This treatment significantly improves resistance to stress corrosion cracking, a significant property for use in high-pressure, highly corrosive environments.
Monel properties for the oil industry
Corrosion resistance
Monel is highly resistant to corrosion, especially in acidic, alkaline and marine environments, so it can resist damage from pitting, stress cracking and corrosion in reducing media (such as hydrochloric acids); therefore, it is generally used in the refining industry in chemical reactors in alkylation units.
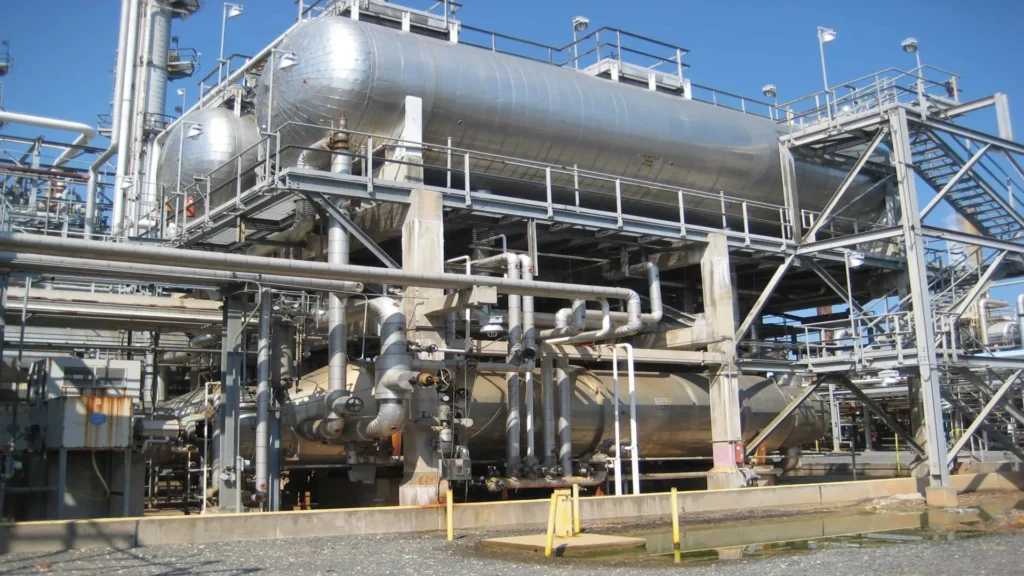
- Resistance in marine environments: It is particularly effective in saltwater environments due to its ability to resist corrosion in the presence of chlorides.
- Resistance to acids: Monel 400, in particular, shows excellent corrosion resistance to acids such as dilute sulfuric acid and hydrochloric acid at moderate temperatures.
Due to these properties it is also used in aggressive environments such as offshore platforms and oil transportation systems, where exposure to salt water and acidic compounds is common.
High ductility and mechanical strength
This alloy has good ductility and mechanical strength. These properties allow the material to be used in different applications that require components subjected to pressure and high mechanical stresses.
- Tensile strength: It has significant tensile strength, so it resists deformation under heavy loads.
- Ductility: It is a material that can be machined, in various shapes and sizes, without losing its properties, facilitating the use of this alloy in welding applications and manufacturing of complex components.
Non-magnetic properties
One of the most important characteristics is its non-magnetism, making it ideal for applications where interference with magnetic fields must be avoided. This is especially relevant in components operating near measuring equipment or navigation systems, where the presence of magnetism can alter the performance of these devices.
- Non-reactivity with magnetic fields: The absence of magnetism also makes monel suitable for applications in subsea drilling systems and offshore drilling rigs, where magnetic interference is undesirable.
Extreme temperature resistance
Monel performs excellently in extreme temperature conditions, both at high and low temperatures. This property is important for applications in the petroleum industry, where components can be exposed to a wide range of temperatures, from the cold depths of the ocean to the elevated temperatures of refineries or drilling operations.
- High temperatures: This material is mechanically stable and resistant to operating temperatures up to 1000°F (537°C).
- Low temperature resistance: It also shows good ductility at low temperatures, being suitable for subsea drilling rigs and extraction platforms in cold environments.
High fatigue and abrasion resistance
This alloy exhibits high fatigue and abrasion resistance, two outstanding characteristics for components subjected to cyclic loading or constant motion, such as parts in contact with moving fluids within piping systems or pumps on drilling rigs.
- Fatigue resistance: Due to its crystalline structure, monel is resistant to fatigue under vibration or cyclic loading conditions, which extends the service life of physical assets.
- Abrasion resistance: Its hardness and abrasion resistance make it a suitable material for surfaces that are exposed to erosion or constant wear.
Ease of fabrication and weldability
This material is relatively easy to fabricate and weld compared to other high-strength alloys. Although its thermal conductivity is lower compared to copper or aluminum, its mechanical properties make it possible to work with it using common fabrication and welding techniques.
- Weldability: Monel can be welded with standard procedures, although it is preferable to use TIG or MIG welding to obtain an optimum finish.
- Fabrication: It can be cold or hot worked, being a suitable material for a variety of industrial processes such as molding, extrusion and forging.
Cracking and stress corrosion resistance
It is especially resistant to stress corrosion cracking (SCC), a form of corrosion that can affect metals under stress conditions and in the presence of certain chemicals. This phenomenon is particularly important in the petroleum industry, where components are exposed to mechanical stress and corrosion simultaneously.
- SCC prevention: Due to its composition and heat treatment, this alloy shows high resistance to cracking and pitting in chlorine and saltwater environments, minimizing the need for maintenance and replacement of critical equipment.
Its history in the oil sector
Monel was discovered in 1905 by the American chemist Robert Crooks Stanley at the International Nickel Company (INCO). However, it was in the middle of the 20th century when it began to gain relevance in the oil industry, especially when the increasing demands of exploration and extraction in offshore environments demanded more resistant materials. Its high resistance to corrosion, particularly in saline waters and acidic environments, made it an ideal choice for offshore applications.
Throughout the 1950s, with the expansion of offshore exploration, monel alloy began to be used in various operating components. Its ability to resist mechanical fatigue and wear, even under extreme conditions of pressure and temperature, effectively integrated it into the oil industry’s most severe operating systems, establishing itself as a necessary material in the design of oil platforms and refineries.
Strategic applications in the oil industry
The properties present in monel alloys make it a material with multiple advantages and benefits to be used in the oil sector, as well as in other industrial sectors. Thus, we are dealing with a metal that is used in:
- Drilling equipment: It is used in tools and components, such as drilling risers, mud pumps, drill bits, valves and pipes, resisting wear, abrasion that are exposed to aggressive fluids and extreme conditions of pressure and temperature.
- Offshore platforms: Used in components exposed to the sea and extreme pressure and temperature changes, such as valves, piping, control systems, couplings, trailing cables, electrical components, monitoring systems and processing equipment.
- Conveyor systems: Used in pipelines transporting crude oil and gas, ensuring resistance to corrosion and wear in marine and offshore environments.
- Internal coatings and linings: Equipment such as distillation towers and columns, separation and gas treatment drums, valves and pumps are internally coated to protect them from acid gases and sulfur compounds, common during the oil separation and refining process.
- Cables and electrical connections: Provides corrosion resistance in monitoring and control systems, especially in offshore platforms and drilling wells.
- Heat exchangers: They are sometimes manufactured with this material due to its resistance to corrosion, especially in aqueous environments or in contact with aggressive compounds such as sulfides; maintaining its resistance to high temperatures during thermal processes.
- Compressors and turbines: Used in internal components such as rotors and turbine blades, due to its ability to resist fatigue and corrosion at high temperatures and pressures.
Monel 400 vs. Monel K-500 vs. Monel 500
These three variants of the monel alloy have specific characteristics that make them ideal for different applications in the oil industry, adapting to corrosion resistance, hardness and tensile strength needs.
- Monel 400: This alloy contains approximately 63% nickel and between 28% and 34% copper, with traces of iron, manganese and silicon. The nickel gives the alloy high thermal and mechanical stability, while the copper gives it excellent resistance to corrosion, especially in marine environments and in contact with acids such as sulfuric, phosphoric, hydrochloric and organic compounds. Monel 400 represents a strategic choice for applications where materials are continuously exposed to salt water and other corrosive agents, such as in pipelines, pumps and valves.
- Monel K-500: This variant is a precipitation strengthened version of monel 400, obtained by adding aluminum and titanium. Making it more hardenable with aging, improving its mechanical properties, such as strength and hardness. It is also more resistant to seawater salts and acid gases. It is especially used in applications requiring high tensile strength, fatigue and corrosion resistance, such as in subsea drilling equipment and tools, as well as in internal components of pumps exposed to extreme pressure and temperature conditions.
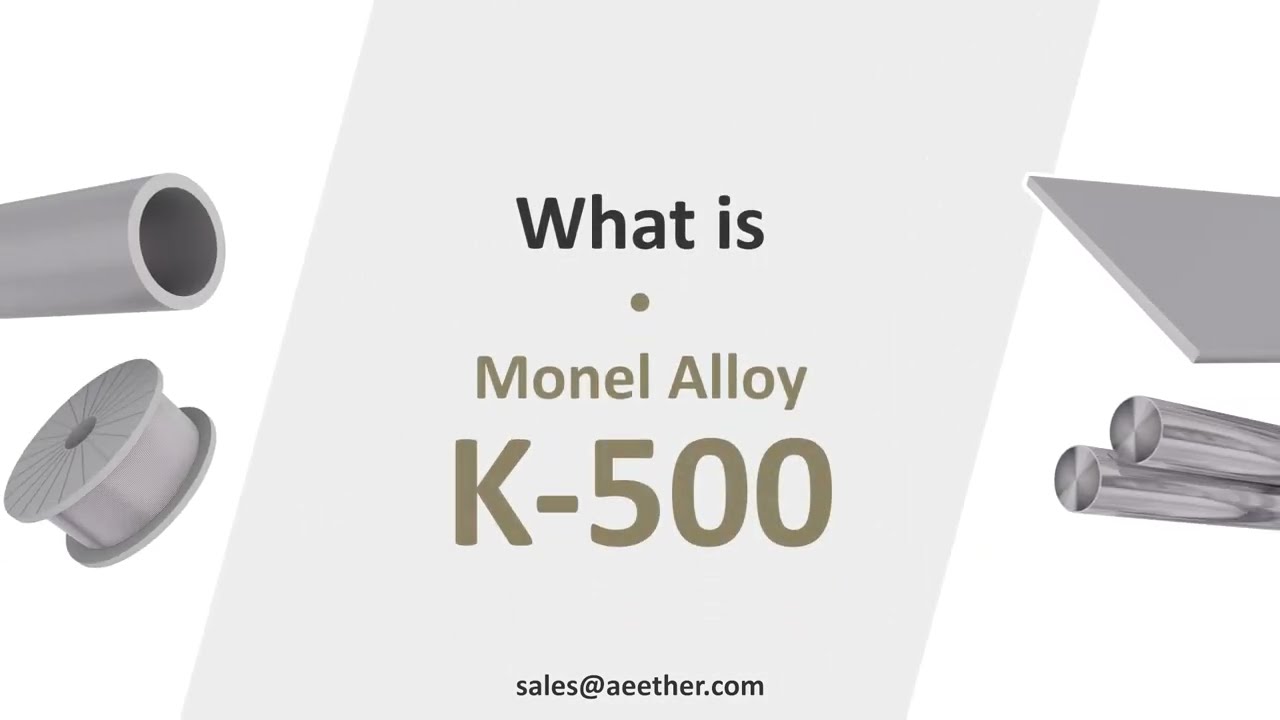
Properties of K-500 monel.
- Monel 500 (also known as 505): This alloy is distinguished by its increased resistance to abrasion and erosion, which, makes it a suitable material for applications where metals are subject to constant wear. Monel 500 combines the corrosion resistance properties of Monel 400 with increased mechanical strength, making it suitable for oil and gas transportation pipelines, heat exchangers and separation system components.
Each variant of the monel alloy is selected depending on the specific demands of the operating environment and the requirements for durability, strength and performance, ensuring reliability and safety in the oil industry.
Conclusion
Monel is a strategic material in the oil industry due to its exceptional capacity, corrosion resistance, durability and ability to withstand extreme temperature and pressure conditions. Its use in oil extraction, transportation and refining systems has proven to be a profitable long-term investment, reducing maintenance costs and improving operational efficiency. Due to its resistance in highly corrosive environments, this material will remain a strategic resource in the oil industry.
References
- https://www.metalstripsolutions.com/es/advantage-and-disadvantage-of-monel-alloy/
- https://blog.goldsupplier.com/es/monel-metal-3/