Introduction
Modular construction has gained popularity among companies looking for innovative, efficient, and sustainable projects, due to its speed and flexibility. This method is based on the production and assembly of prefabricated modules in factories, under controlled conditions, using the same materials and quality standards as traditional construction, but with a significant reduction in time and resources.
Modular construction on project efficiency stands out for its speed, versatility, and contribution to sustainable construction. Its growing implementation improves the quality of buildings, reduces waste, and reduces environmental impact. Moreover, this method is adaptable to projects of all scales, from small buildings to large industrial complexes.
This article discusses the fundamentals of this construction model, its importance in the industry, its advantages over traditional construction, its impact on project efficiency, and the benefits for large developments.
What is modular construction?
Modular construction is a building process where building components, called modules, are manufactured in controlled environments outside the construction site. These modular building units, once transported and assembled on site, form the overall structure of the modular buildings, reflecting identical specifications of the original design. This method is based on a reduced construction schedule, increased strength, high-quality control, and modern construction designs.
This construction model is a natural choice that offers innovative and sustainable solutions for different needs and has two main types: permanent modular construction and relocatable buildings. It is also qualified as a form of green construction because it reduces waste and therefore the environmental impact; faster, in manufacturing and assembly; and more efficient or intelligent, by minimizing the time and resources required compared to traditional construction.
Regarding the size of the modular buildings market, it is estimated at US$63.76 billion in 2024 and is expected to reach US$97.13 billion in 2029, growing at a compound annual rate of 8.78% during the forecast period (2024-2029)1.
Impact of modular construction on project efficiency
The modular construction method has a distinctive impact on the efficiency of construction projects, standing out in several aspects:
- Optimization of the construction process: Using advanced tools such as Building Information Modeling (BIM), modular construction optimizes the entire process, from design to delivery. Manufacturing in controlled environments ensures quality and reduces waste, while simultaneous site preparation decreases overall construction time.
- Improved productivity: Moving much of the work to controlled environments allows for optimal conditions and equipment specialization, reducing disruptions and downtime. Unlike traditional construction, modular construction allows several phases to be performed in parallel, which shortens total construction time and reduces labor costs and errors, resulting in up to 50% faster completion.
- Waste reduction: Manufacturing in controlled environments reduces waste, allowing for efficient use of materials and recycling of leftovers. This method minimizes errors and rework, improving resource management. Studies indicate that modular construction reduces waste by up to 90% compared to traditional construction.
- Higher Return on Investment (ROI): Modular construction offers a higher ROI due to its time and cost efficiency. By reducing construction time and reducing errors and rework, modular projects allow for faster occupancy and reduced operating costs, highlighting the cost-effectiveness of modular construction.
Modular construction is an efficient and competitive alternative to traditional construction methods, which usually involve longer construction times, risks, costs, and waste.
Importance of modular construction in the industry
Modular buildings are the boom of the construction industry through their innovation and sustainability, it is an alternative to the current situation of massive construction. Since its initial evolution, this method has introduced numerous improvements in the efficiency and quality of construction projects. Its ability to prefabricate modules in controlled environments accelerates the construction process and allows standardization and customization according to the specific needs of the project.
By manufacturing in controlled environments, waste is minimized and the use of materials is optimized, promoting more responsible and environmentally friendly practices. In addition, the flexibility and versatility of the modules allow them to be adapted to various applications, from residential to commercial and industrial projects, providing fast and efficient solutions to the fast-paced demands of the market. These characteristics highlight the importance of this construction model as innovative and prepared to overcome current and future obstacles in the construction industry.
How is modular construction carried out?
This construction model is innovative and allows for faster and more controlled construction, from the design phase to the final delivery of the project. The main stages of the modular process are detailed below:
- Design process: This process begins with detailed planning, where precise drawings and specifications are drawn up to ensure the correct assembly of the modules. This stage requires coordination between architects, engineers, and others involved. Advanced tools such as BIM and 3D design software are used to visualize the entire project, identify problems before fabrication, and optimize the efficiency and functionality of each module.
- Factory manufacturing: Once the design is finalized, the modules are manufactured in a controlled environment within a factory, which allows for strict quality control and ensures that the materials are kept in optimal conditions. During manufacturing, quality standards are followed, and periodic inspections are carried out to ensure a high-quality end product.
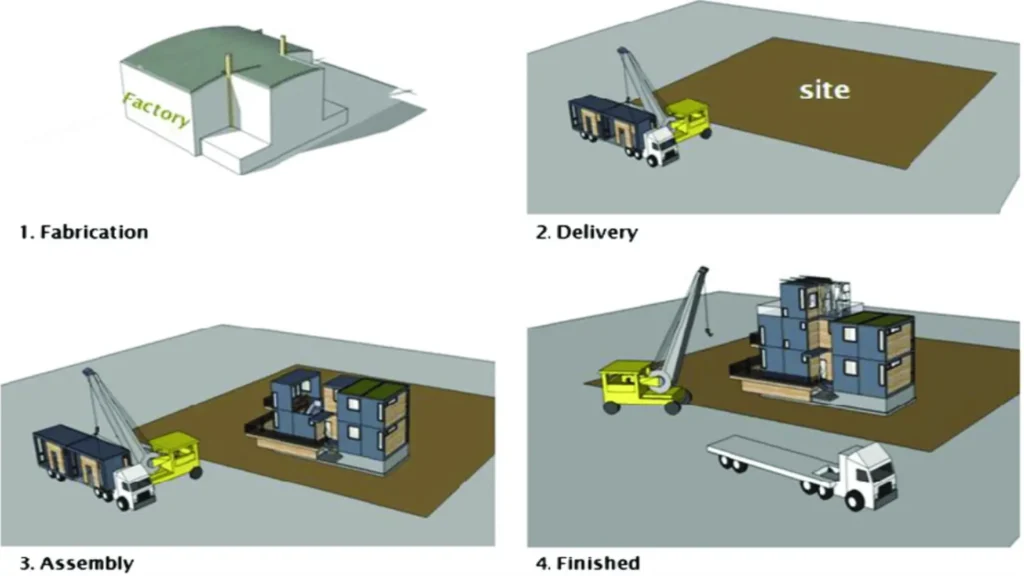
- Transportation and assembly: Once manufactured, the modules are transported to the construction site, requiring careful logistics to ensure their safe and timely arrival. At the site, the modules are assembled following specific procedures, including precise placement, structural connection and integration of ancillary systems. This assembly is done quickly and efficiently, reducing overall construction time compared to traditional methods.
- Completion and handover: The final phase of modular construction includes the installation of interior and exterior finishes, verification of all ancillary systems, and site cleanup. A final inspection is then performed with the client to ensure that the project meets all specifications and quality standards.
The following video presents the process of modular building construction, from planning and design to manufacturing, transportation, and assembly. Source: Arkitech.

Modular structure system for buildings.
Benefits of modular construction as opposed to traditional construction
The following are the advantages of this construction system, which are perceived by several companies that prefer modular construction to conventional alternatives2:
- Reduced construction time: They are 30% to 50% faster than traditional construction, due to simultaneous factory fabrication and site preparation.
- More cost-effective and better cost control: Standardization and large-scale production allow for savings, with stable prices and faster return on investment.
- Better quality control: Since most of the construction and installation are done in controlled environments, better quality controls are applied at every stage of construction. This ensures that the final product meets the highest standards and specifications.
- Simplified supply chain: Modular construction simplifies the supply chain, with a single point of contact overseeing planning, design, production, delivery, and installation.
- Adaptable design options: The modular construction model allows customizing facilities, creating functional structures according to specific needs and tastes, and offering tailor-made solutions.
- More durable materials: They use materials such as concrete, steel, and wood, designed to be durable and virtually maintenance-free.
- Energy efficiency: They offer excellent thermal, acoustic, and fire protection conditions, and allow the use of renewable energies and efficient insulation systems, reducing energy consumption by up to 70%.
- Flexibility and adaptability: Modules can be easily modified, augmented or removed, reducing raw material and energy demand for new construction.
- Increased safety: The controlled environment reduces the risk of accidents and increases the safety and productivity of workers. Modular construction minimizes the need to work at heights, resulting in a safer construction process.
- Sustainability: This model seeks to reduce the environmental impact of both manufacturing and construction. By manufacturing the modules in a factory, emissions and waste generation are minimized and the use of materials is optimized. It also allows for the reuse of materials.
- Integration of technologies: This type of design allows the integration of advanced technologies and intelligent systems, enabling users to create energy-efficient and technologically advanced spaces.
Conclusions
Modular construction is ideal for large projects, based on a specific design to facilitate the transportation and on-site assembly of the modules. It has proven to be a highly efficient solution in the construction industry, differing from traditional buildings not because of the types of materials used, but because of its innovative construction process. By optimizing processes from design to delivery, this method helps to reduce costs, increase quality and shorten lead times.
Modular construction in project efficiency stands out for its ability to minimize waste and manage resources in a sustainable manner. The benefits of modular construction include increased quality control, a simplified supply chain, and the flexibility to adapt to various needs and project types. In addition, its focus on sustainable construction allows for the creation of energy-efficient structures with less environmental impact.
This construction model is a competitive alternative that becomes the best alternative to the current massive construction, offering innovative and sustainable solutions that position it as the future of modern construction.
Learn how new technological advances are transforming the design and execution of building projects, offering an alternative that undoubtedly represents the future of the industry.
References
- https://www.mordorintelligence.com/es/industry-reports/modular-construction-market, accessed on 18-06-2024
- https://www.calaminon.com/blog/beneficios-de-la-construccion-modular/, accessed on 18-06-2024