Table of Contents
- Introduction
- Inspection and maintenance of complex structures
- ROVs and Mini-ROVs Fundamentals
- Abilities of the Mini-ROVs
- Applications of Mini-ROVs in the inspection of structures
- Advantages of Mini-ROVs over traditional methods
- Challenges and operational considerations
- Future trends and technological development
- Conclusions
- References
Introduction
In the field of industrial engineering and maintenance, ensuring the integrity and efficiency of complex structures is critical to operational safety. Faced with the challenges of accessibility and associated risks, ROVs, especially Mini-ROVs, have emerged as innovative alternatives, fundamentally changing the way these essential tasks are performed.
These devices, which range from compact to more sophisticated units, facilitate access to areas previously inaccessible or high-risk for manual inspections, including underwater infrastructure, confined spaces and significant heights. The ability of ROVs, particularly Mini-ROVs, to provide detailed visualizations and collect real-time information has revolutionized the field of inspection and maintenance, allowing accurate assessments to be made without compromising operator safety.
The use of ROVs and Mini-ROVs is not only redefining inspection methodologies for complex structures, but also setting new industry standards, underscoring the crucial role of technological innovation in the maintenance and assessment of the structural integrity of key infrastructure.
Inspection and maintenance of complex structures
During inspection and maintenance processes, these types of structures face significant challenges ranging from physical accessibility to accuracy and efficiency of assessments. Traditionally, these tasks have required the mobilization of human teams to potentially hazardous environments, such as elevated, underwater or confined areas, increasing the risk of occupational accidents and exposing workers to adverse conditions.
The manual operation of inspections often leads to a greater investment of time and resources, which generally results in reactive rather than preventive maintenance, thus affecting the longevity and functionality of the infrastructure.
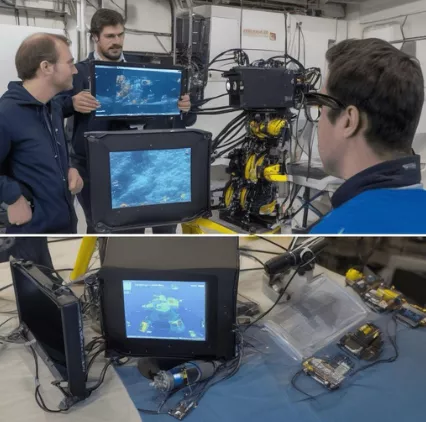
The relevance of innovating in the field of inspection and maintenance of complex structures lies in the need to overcome these obstacles by adopting advanced technologies that allow accurate and efficient diagnostics without compromising human safety.
The integration of tools such as ROVs and Mini-ROVs into inspection practices represents a significant advance, offering the ability to access difficult locations, reduce downtime and minimize the risks associated with working in hazardous conditions. This approach not only improves the efficiency of inspections and maintenance, but also promotes a culture of prevention and continuous improvement, which is significant for the sustainability of any complex infrastructure.
ROVs and Mini-ROVs Fundamentals
The need to overcome conventional challenges in the inspection and maintenance of complex structures, ROVs (Remotely Operated Vehicles) and, in particular, Mini-ROVs, have emerged as fundamental tools in this field. ROVs are unmanned, remotely controlled devices designed to operate in harsh and potentially hazardous environments for humans, such as underwater, at high altitudes or in confined spaces. Mini-ROVs, a subcategory of ROVs, are more compact and agile versions, optimized for inspection and maintenance tasks in hard-to-reach locations, offering a unique combination of mobility, functionality and safety.
The evolution of ROVs and Mini-ROVs has been marked by significant advances in technology, including improvements in propulsion, navigation systems, imaging and sensor capabilities, as well as the integration of specialized tools. These devices are equipped with high-resolution cameras, sensors to measure critical variables and robotic arms to perform specific tasks, remotely controlled by operators.
The technology behind ROVs and Mini-ROVs continues to advance, driven by research and development, broadening their application in inspection and maintenance and redefining what is possible in complex infrastructure management. This technological progress not only responds to the growing demand for safer and more efficient solutions, but also opens new horizons in the approach to preventive and corrective maintenance of critical structures.
Abilities of the Mini-ROVs
Mini-ROVs, with their compact design and advanced technology, are equipped with a number of capabilities that make them exceptional instruments for the inspection and maintenance of complex structures. Their maneuverability is one of the highlights, allowing these vehicles to navigate through tight spaces and reach areas inaccessible or dangerous to human inspectors. Thanks to sophisticated propulsion systems and precise controls, the Mini-ROVs can perform complex movements with high accuracy, which is crucial for inspecting infrastructure in adverse conditions.
The technological equipment of the Mini-ROVs includes high-resolution cameras, advanced sensors and, in some cases, robotic arms that can perform specific tasks, such as collecting samples or performing minor repairs. This technology not only improves the quality and scope of inspections, but also significantly reduces the time required to perform them, providing detailed images and data that can be analyzed in real time or reviewed later for further evaluation.
Real-time analysis capability is another key ability of Mini-ROVs. Data collected during inspections is instantly transmitted to operators, enabling fast and informed decision making. This feature is essential to identify potential problems before they become critical failures, facilitating a proactive approach to the maintenance and management of structures. In addition, real-time analysis enables continuous monitoring of infrastructure conditions, which contributes to effective maintenance planning and to extending the service life of the facilities.
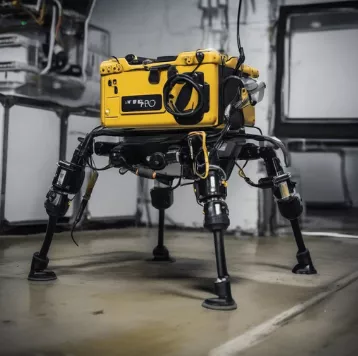
Overall, the abilities of Mini-ROVs in terms of maneuverability, technological equipment and real-time analysis capabilities make them indispensable tools for the inspection and maintenance of complex structures, marking a turning point in the efficiency and safety of these critical operations.
Applications of Mini-ROVs in the inspection of structures
Mini-ROVs have found applications in a variety of environments, demonstrating their versatility and effectiveness in the inspection of complex structures. A prime example is its use in the oil and gas industry, particularly in the inspection of offshore platforms and pipelines.
In these environments, Mini-ROVs perform detailed structural integrity assessments and look for signs of corrosion or damage, tasks that are critical to preventing spills and ensuring operational safety. Thanks to their ability to operate at significant depths and in adverse conditions, Mini-ROVs offer a safe and efficient solution, eliminating the need for human divers in many cases.
Another field of application is in civil engineering, where they are used for the inspection of bridges, dams and tunnels. These vehicles allow engineers to image hard-to-reach areas, such as the underwater foundations of bridges or the inner walls of dams, facilitating early detection of structural problems and avoiding costly repairs or catastrophic failures.
In marine research and conservation, Mini-ROVs play an important role in mapping underwater ecosystems, monitoring biodiversity and assessing the environmental impact of human activities. Their ability to access sensitive environments without significantly disturbing wildlife or habitat allows scientists to collect valuable data that contributes to marine conservation.
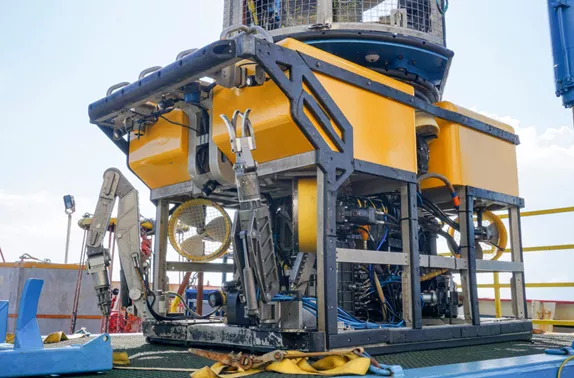
ROVs, especially Mini-ROVs, can be equipped with a variety of specialized accessories and tools to perform detailed assessments and specific tasks. The customizability of these devices allows them to be adapted to a wide range of applications, from simple inspections to complex maintenance operations. The following are some of the most common accessories that can be attached to ROVs:
- High resolution cameras and 3D cameras: Capture detailed images and videos of the inspected structures. 3D cameras offer the possibility of generating three-dimensional models of the structures, which is useful for more in-depth analysis.
- Sensors and sonars: Including side scan sonars, multibeam sonars and echo sounders, they are used to map the seabed and detect anomalies in submerged structures. The sensors can measure variables such as temperature, salinity, depth and the presence of hydrocarbons.
- Thermography equipment: This equipment can be attached to ROVs, including Mini-ROVs, to perform thermographic evaluations underwater or in hard-to-access environments. Thermography, which uses infrared cameras to detect and measure thermal radiation, makes it possible to identify temperature variations in the inspected structures. This technology is especially useful for detecting problems such as heat leaks, insulation failures, hot spots that indicate electrical overheating, and other anomalies that would not be visible with conventional visual inspection. To perform an effective thermographic inspection, the thermography equipment must be adequately protected and adapted to operate in the specific environment, especially underwater.
- Manipulator arms: Their function is to perform minor repair tasks or to collect samples. These arms can be simple, with gripping functions, or more complex, with specialized tools.
- Cutters and cleaning tools: They are used to remove obstructions, such as fishing nets or accumulation of algae and other organisms, as well as to make precise cuts if necessary.
- Lighting: The addition of high-powered lights is crucial to improve visibility during inspections in dark underwater environments.
- Sampling systems: For the collection of samples of water, sediments or marine organisms, which is especially useful in environmental and marine research.
- Measuring tools: Such as gauges and thickness probes, which allow measuring the thickness of materials and detecting possible corrosion or erosion.
- Navigation systems: Improve ROV positioning accuracy, especially useful in deep water or strong currents.
The integration of these accessories makes the Mini-ROVs highly versatile platforms, capable of performing a wide variety of inspection and maintenance tasks in diverse environments. Tool selection will be based on the specific needs of each operation, ensuring that ROVs can perform accurate and effective assessments.
Advantages of Mini-ROVs over traditional methods
Mini-ROVs offer significant advantages over traditional methods of inspection and maintenance of complex structures, particularly in terms of safety, cost and efficiency. First, they improve safety by eliminating the need to expose workers to hazardous or difficult-to-access environments, such as underwater depths or confined spaces. By using Mini-ROVs, companies can reduce the risk of accidents and ensure compliance with occupational safety regulations.
From a cost perspective, Mini-ROVs reduce the investments associated with inspection operations. The mobilization of human teams for underwater or high altitude inspections often requires specialized equipment, additional insurance and, in some cases, temporary facility closures. Mini-ROVs, on the other hand, offer a more economical solution by requiring fewer human and logistical resources.
In terms of efficiency, Mini-ROVs allow for faster and more accurate inspections and maintenance. Equipped with advanced technology, they can collect detailed data in real time, facilitating early identification of problems and informed decision making. This contributes to more efficient infrastructure management, optimizing maintenance processes and extending the service life of the inspected structures.
Challenges and operational considerations
The deployment of Mini-ROVs in inspection and maintenance operations presents specific technical and operational challenges. One of the main challenges is the design and maintenance of effective underwater communication systems, where signal propagation can be significantly affected by factors such as salinity, depth and physical obstacles. This requires innovative telemetry solutions and remote control systems to ensure operability and real-time data transmission. In addition, limited energy autonomy imposes operational constraints on the duration and mission range of Mini-ROVs.
Another relevant challenge is the specialized training required for Mini-ROV operators. Given the level of technical complexity and the need to perform precise tasks in challenging environments, operators must possess advanced skills in navigation, control systems management and data analysis. This involves an intensive training process that encompasses both theoretical knowledge and operational practice, ensuring that operators can maximize the capabilities of the Mini-ROVs and respond effectively to unforeseen situations.
Future trends and technological development
The future of ROV technology looks promising, with advances that promise to further transform inspection and maintenance practices. The integration of artificial intelligence (AI) and machine learning is at the forefront of these innovations, enabling Mini-ROVs to perform inspection and diagnostic tasks autonomously, improving accuracy and reducing operating times. In addition, the development of new energy sources, such as longer-lasting batteries and wireless underwater recharging systems, is anticipated, which will extend the autonomy of ROVs.
In addition, improved communication systems will allow operations beyond visual range, opening up new possibilities for exploration and maintenance in previously inaccessible areas. These advances will not only increase the efficiency and safety of operations, but will also expand the field of application of Mini-ROVs to new sectors and industries, marking an era of innovation in the inspection and maintenance of complex infrastructures.
Conclusions
The adoption of Mini-ROVs in the inspection and maintenance of complex structures represents a significant advance towards improving safety and efficiency in critical operations. These devices have not only overcome the accessibility and risk challenges inherent in traditional methods, but have also incorporated state-of-the-art technology to provide detailed visualizations and real-time analysis.
Despite facing operational and technical challenges, such as the need for specialized training for operators, Mini-ROVs continue to evolve, with promises to integrate artificial intelligence and improvements in communication and power. This progress portends a future where inspection and maintenance can be performed with unprecedented accuracy and safety, marking an era of technological innovation that redefines standard industry practices and promotes the sustainability of critical infrastructures.
References
Own source