Mechanical integrity is the fundamental pillar that supports mechanical engineering , a discipline that is intrinsically intertwined with the safety, efficiency and durability of systems and structures. This article dives into vibration analysis , a vital tool for engineers dedicated to preserving and improving the mechanical integrity of equipment.
Through this journey, we will explore how vibration analysis not only prevents catastrophic failures, but also optimizes performance and extends the life of mechanical components, thus ensuring safe and efficient operations.
Fundamentals of vibration analysis in mechanical engineering
Vibration analysis is a critical technique in mechanical engineering used to detect anomalies and prevent failures in equipment and structures. Through vibration measurement and analysis, engineers can identify a variety of problems, from imbalances and misalignments to material wear and fatigue. This technique is not only necessary for predictive maintenance , but also contributes significantly to operational safety and resource optimization. By understanding the causes and effects of vibrations, engineers are better able to design more robust and reliable systems.
Technologies and tools in vibration analysis
Vibration analysis is a sophisticated technique that relies on a variety of advanced technologies and tools; which not only facilitate the detection and analysis of problems, but also improve the understanding of operating conditions and decision making. Below are some of the most significant components in this field.
- Sensors and measurement equipment: Sensors are devices used in vibration analysis . They range from accelerometers and speedometers to displacement sensors and lasers. Accelerometers, in particular, are widely used due to their ability to measure the acceleration of vibrations, providing crucial data on vibration intensity and frequency. These devices can be wired or wireless, offering flexibility in various operating conditions.
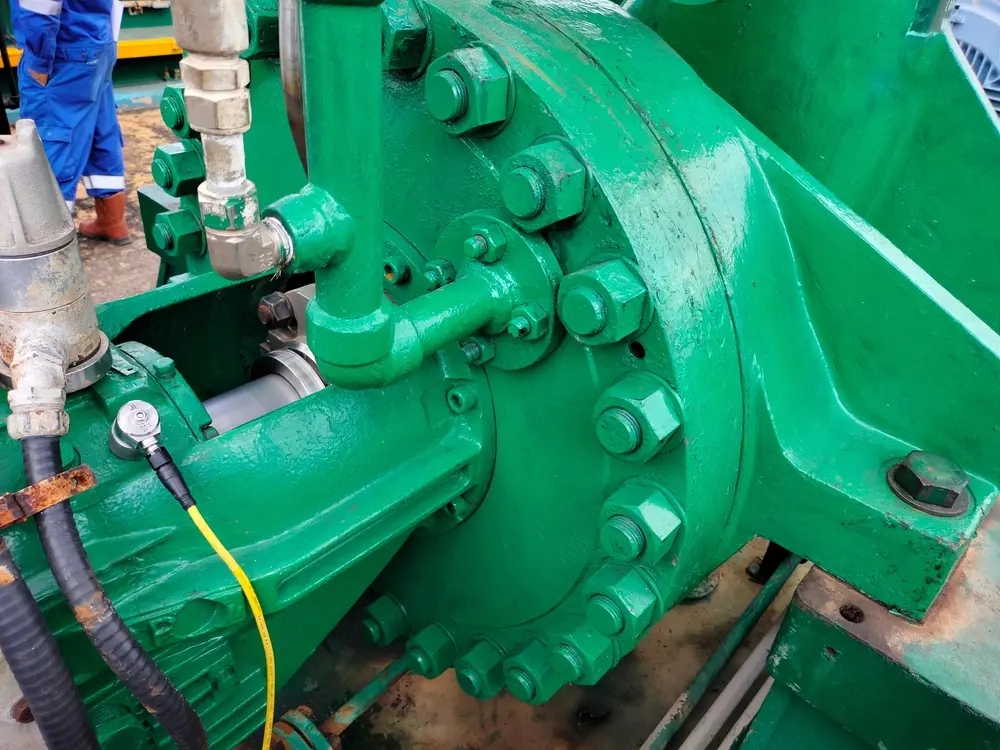
- Real-time monitoring systems: their function is to capture instantaneous changes and prevent imminent failures. Modern systems use advanced communication technologies to transmit data from sensors to analytics platforms in real time. This allows engineers to continually monitor the condition of the machinery and act quickly on any sign of a problem.
- Data analysis software: These are important for the interpretation of vibration data. These advanced programs can perform Fourier analysis to decompose vibrations into their frequency components, thus identifying specific sources of problems. Additionally, the software can employ artificial intelligence and machine learning algorithms to predict trends and detect abnormal patterns within a data set.
- Artificial intelligence and machine learning: Artificial intelligence (AI) and machine learning are revolutionizing vibration analysis . These technologies allow systems to learn from historical data and continually improve their ability to detect and diagnose problems. They can identify atypical patterns and predict failures before they occur, allowing for more effective predictive maintenance and more efficient maintenance planning.
- Integration with maintenance management systems: Integrating vibration analysis with maintenance management systems (CMMS) allows for more efficient management of maintenance activities. Vibration data can automatically trigger work orders and ensure maintenance is performed at the optimal time, based on the actual state of the equipment rather than a fixed schedule.
Case Studies: Vibration Analysis Successes
Vibration analysis has been an invaluable tool in multiple industries, helping to prevent failures, improve efficiency and reduce costs. Below are several case studies that illustrate the positive impact and practical applications of this technique.
Aerospace industry: Aircraft turbine maintenance
Context: Aircraft turbines are critical to the safety and efficiency of aircraft. A failure can have catastrophic consequences.
Application: Vibration analysis is used to monitor the status of turbines in real time. Sensors detect abnormal vibrations that can indicate problems such as imbalances, wear or cracks in the blades.
Result: In several cases, vibration analysis has allowed airlines to detect problems prematurely, avoiding in-flight failures and reducing downtime. This not only improves safety, but also reduces maintenance costs by allowing repairs before problems become serious.
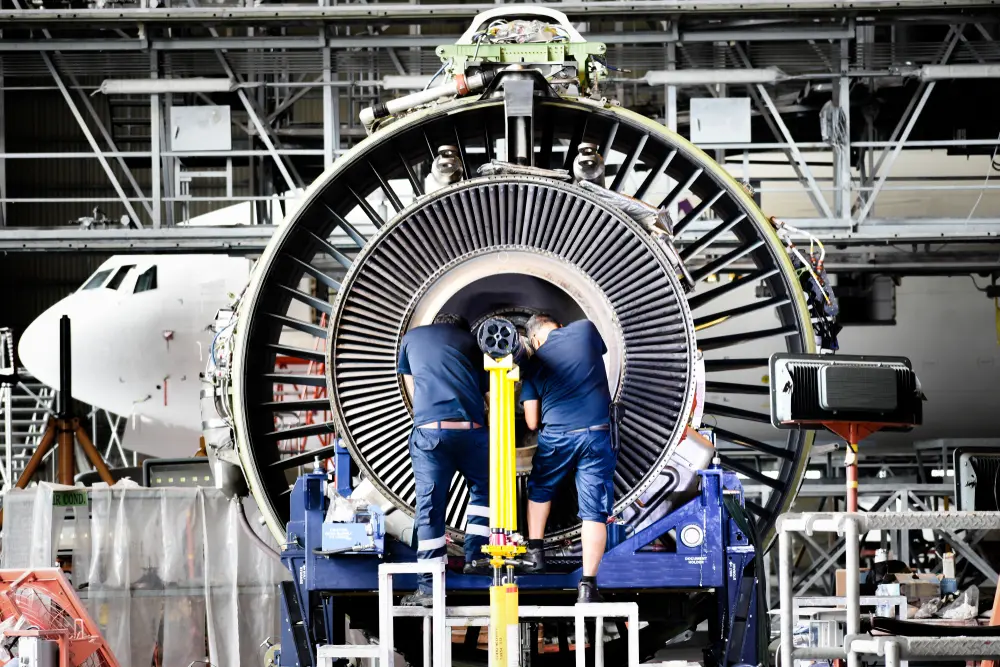
Power generation: Monitoring of wind turbines
Context: Wind turbines are subject to variable environmental conditions and constant loads, which can lead to mechanical failures.
Application: Vibration analysis is used to monitor the structural integrity of turbines. Sensors placed on key components, such as the blades and gearbox, provide real-time data.
Result: In several wind farms, the use of vibration analysis has made it possible to identify problems such as misalignments and imbalances before they cause major damage. This has resulted in greater operational efficiency and a reduction in repair and replacement costs.
Automotive industry: vehicle design and testing
Context: Excessive vibration in vehicles is not only uncomfortable for passengers, but can also indicate underlying problems that affect safety and performance.
Application: During the design and testing of new vehicles, vibration analysis is used to evaluate and improve the vehicle’s response to different driving conditions.
Result: In several cases, automobile manufacturers have used this technique to identify and correct problems before the vehicle is released. This has led to design improvements, greater passenger comfort and, most importantly, safer vehicles.
Processing industry: Heavy machinery monitoring
Context: In processing plants, heavy machinery such as pumps, compressors and conveyors are essential for daily operations. A failure can cause costly outages.
Application: Vibration analysis is used to monitor the condition of these machines. Sensors detect changes in vibrations that may indicate wear, misalignment or inadequate lubrication.
Result: In many plants, this technique has allowed predictive maintenance to be carried out, avoiding unexpected failures and prolonging the useful life of the machinery. This not only improves operational reliability but also reduces maintenance and replacement costs.
Challenges and future of vibration analysis
Vibration analysis is a powerful technique in mechanical engineering , but it is not without challenges. As it progresses, it faces new complications and at the same time opens doors for future innovations. Let’s delve into the current challenges and future perspectives of this discipline.
Current challenges
- Complexity of modern systems: Mechanical systems today are more complex, making accurate interpretation of vibration data difficult. The presence of multiple vibration sources and interaction between components can obscure critical signals and lead to misdiagnoses.
- Big data: The increase in the amount and speed of data collected by advanced sensors can be overwhelming. Processing and analyzing this data effectively to obtain useful information is a significant challenge.
- Need for specialized expertise: Vibration analysis requires a high level of knowledge and experience. A lack of trained personnel may limit an organization’s ability to implement and benefit from this technique.
- Implementation Costs: The acquisition and installation of high-tech equipment, along with the need for constant maintenance and upgrades, can be expensive, especially for small and medium-sized businesses.
The future of vibration analysis
- Integration of artificial intelligence and machine learning: AI and machine learning are poised to transform vibration analysis . They can handle large volumes of data, identify complex patterns, and predict failures more accurately. This will not only improve problem detection but also optimize maintenance strategies.
- Autonomous monitoring systems: Monitoring systems are expected to evolve towards more autonomous solutions, capable of self-diagnosing and, in some cases, self-correcting without human intervention. This could significantly reduce downtime and maintenance costs.
- Improvements in sensor sensitivity and accuracy: The continued development of more sensitive and accurate sensors will allow problems that are currently undetectable to be detected. This will further improve the ability to prevent failures and extend the life of the machinery.
- Augmented reality and advanced visualization: Augmented reality could provide engineers and technicians with a more intuitive and detailed view of vibration data, improving understanding and decision-making. Advanced visualization can also help explain findings to non-experts, facilitating communication and collaboration.
- Accessibility and democratization: As technology becomes more accessible and affordable, organizations will be able to adopt vibration analysis . This could democratize access to this powerful technique, allowing even the smallest companies to benefit from its advantages.
Conclusion
Vibration analysis is more than a technique; It is science, technology and ingenuity that resonates with the future of mechanical engineering . As we move toward that future, we do so with the certainty that mechanical integrity is not just an ideal to achieve, but a reality that can be maintained, improved, and ensured. Engineers, trained with advanced knowledge and innovative technologies, are ready to meet the challenges of tomorrow, ensuring that the vibrations of today resonate safely and successfully into tomorrow.
References
Own source