Table of Contents
- Basics of nuclear fusion
- Overview of fusion reactors
- The role of iron silicate in fusion reactors
- Innovations in materials for nuclear fusion
- Specific applications of Iron silicate in nuclear fusion
- Recent advances and future perspectives on the use of iron silicate
- Challenges and opportunities
- Future of fusion reactors and iron silicate
- Conclusions
- References
Nuclear fusion, the process that powers the sun, promises a clean and nearly limitless source of energy, without the harmful greenhouse gas emissions that come from fossil fuels. Unlike nuclear fission, which splits heavy atoms, fusion combines light nuclei to form a heavier one, releasing large amounts of energy. Advances in technology are making controlled fusion energy more achievable. In this context, iron silicate has emerged as a potentially important material due to its unique properties, particularly its suitability for protective coatings that could enhance the efficiency and safety of fusion reactors.
Basics of nuclear fusion
Nuclear fusion involves combining light nuclei, usually hydrogen isotopes like deuterium and tritium, at extremely high temperatures (millions of degrees Celsius). Under these conditions, atomic nuclei have enough energy to overcome their repulsion and fuse, releasing energy in the form of neutrons and radiation. This process is more efficient and safer than fission because it doesn’t produce long-lived radioactive waste and carries a lower risk of major accidents. However, containing the super-hot plasma needed for fusion poses significant technical challenges. Reactor designs like the Tokamak and Stellarator are being developed to solve these problems, aiming to confine the plasma in a stable and efficient way to ensure a reliable energy source.
Overview of fusion reactors
The most advanced fusion reactors today include the Tokamak, which uses a donut-shaped magnetic field to confine plasma, and the Stellarator, which twists magnetic fields to maintain plasma stability. Projects like ITER in France are leading fusion research, aiming to prove that fusion energy is technically and economically viable. ITER’s goal is to produce more energy than it consumes, a crucial step toward building commercial reactors. Other projects like DEMO, a demonstration fusion plant, are also planned to follow ITER’s progress and bring fusion technology closer to commercial use.
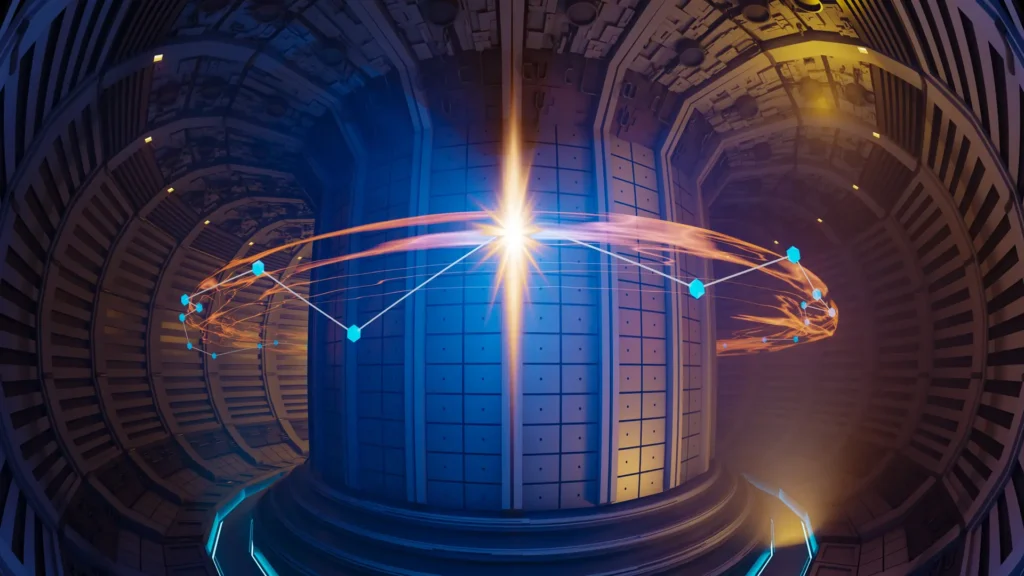
Watch this video for a visual explanation of how nuclear fusion works, the technology behind fusion reactors, and the potential impact this revolutionary energy source could have on our future. Source: Real Engineering.
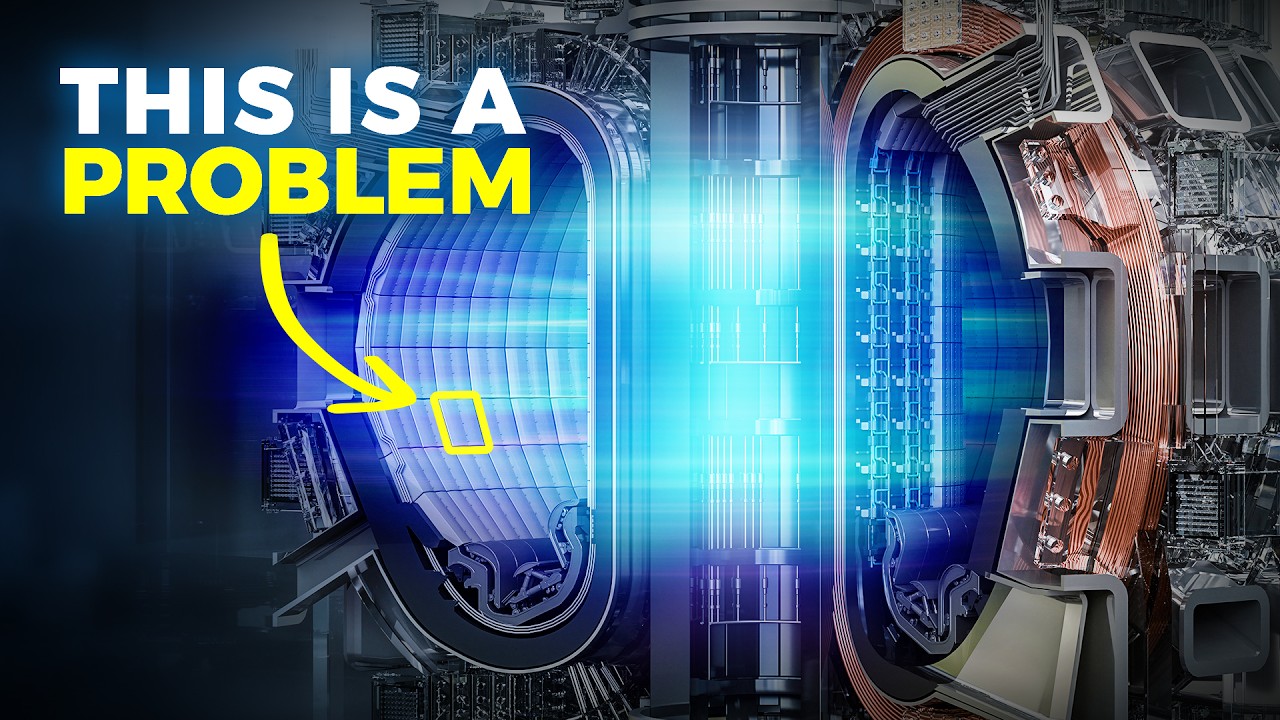
The problem with nuclear fusion.
The role of iron silicate in fusion reactors
Iron silicate, made of iron, silicon, and oxygen, has properties that make it ideal for use in fusion reactors, especially for absorbing neutrons. In fusion reactors like the Tokamak, many fast neutrons are generated during fusion reactions. These neutrons can damage the reactor’s structural materials, reducing their lifespan. Iron silicate is effective at capturing these neutrons, thereby reducing radiation exposure to other materials and protecting the reactor’s inner walls from wear and erosion. Its neutron-absorbing ability also minimizes the radioactive activation of other elements, reducing the amount of long-lasting radioactive waste. These properties make iron silicate a key material for protective coatings and structural components, enhancing the safety and operational efficiency of nuclear fusion reactors and supporting its use as a safe and sustainable energy source.
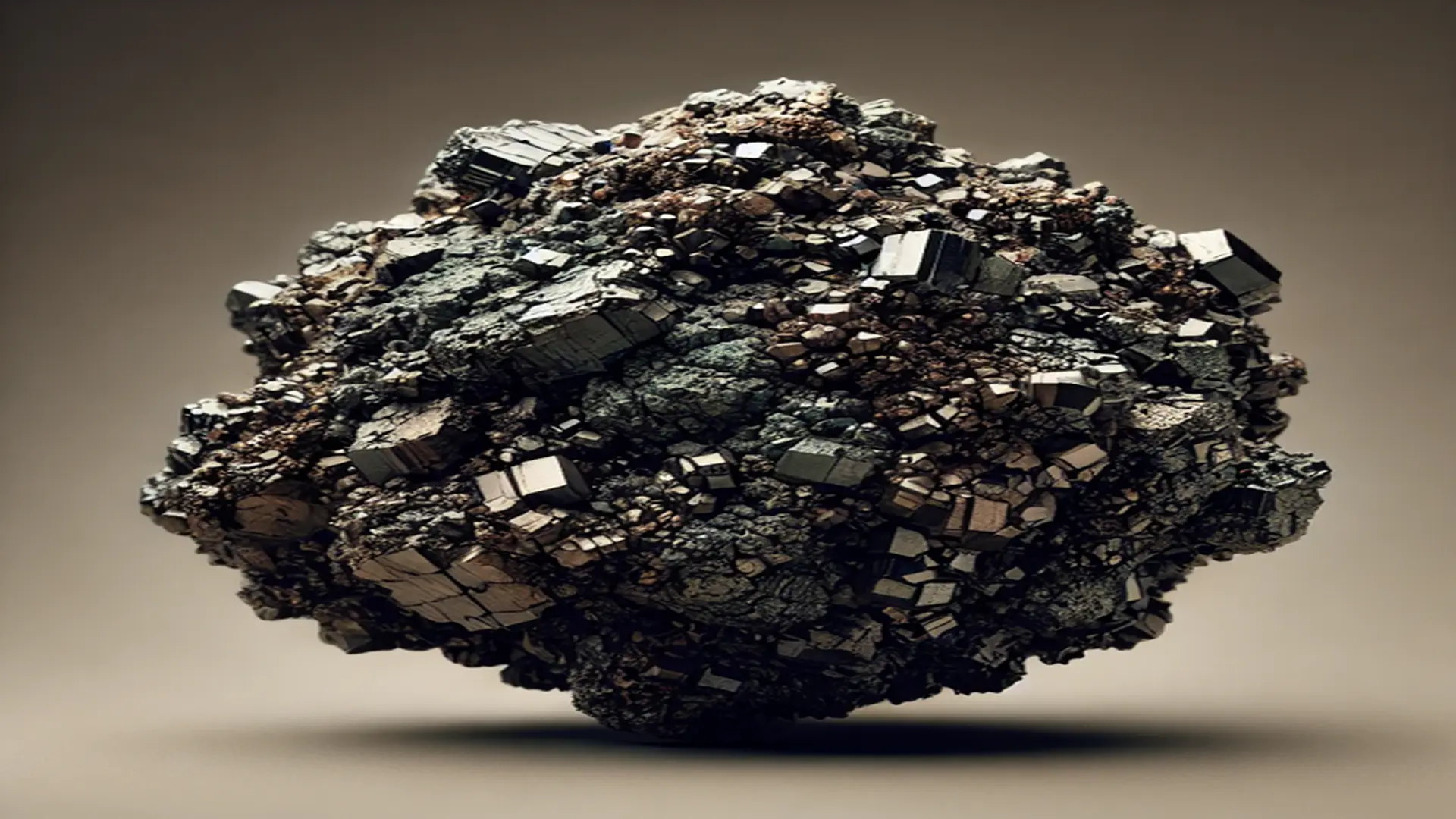
Innovations in materials for nuclear fusion
Nuclear fusion requires advancements not only in reactor design and operation but also in the materials used. Besides iron silicate, other materials are being intensively studied for their unique properties, particularly their use in protective coatings that can withstand extreme fusion environments. Tungsten, for example, is known for its high melting point and resistance to erosion, making it suitable for areas of the reactor that come into direct contact with hot plasma. Another promising material is carbon-fiber-reinforced carbon (CFC), which offers excellent thermal resistance and can withstand extreme temperature cycles without deforming.
Additionally, Reduced Activation Ferritic-Martensitic (RAFM) steels have been specifically developed to minimize radioactive activation and make waste management easier. These steels, which combine iron with other elements like chromium and tungsten, show good resistance to neutron irradiation and have mechanical properties suitable for fusion applications. Projects like ITER are testing these materials in simulated fusion environments to evaluate their performance and durability. Innovations in these materials will improve reactor safety and efficiency and lower maintenance and decommissioning costs, bringing fusion energy closer to becoming commercially viable.
Specific applications of Iron silicate in nuclear fusion
In fusion reactors, iron silicate could be used to create protective coatings on the inner walls, effectively acting as a barrier against erosion and neutron irradiation, thus playing a fundamental role in reactor longevity and efficiency. Its ability to absorb neutrons can also help control plasma reactions and reduce wear on other structural materials, thereby extending the reactor’s lifespan. Recent research suggests that iron silicate could also be useful in making structural support components, such as those supporting the magnetic coils in Tokamak reactors, due to its resistance to thermal and mechanical fatigue.
Recent advances and future perspectives on the use of iron silicate
Interest in iron silicate as a key material for fusion reactors has grown in recent years, driven by its ability to absorb neutrons and withstand extreme conditions. Current research focuses on optimizing its properties and exploring its integration into critical reactor components. Collaborative projects between research institutions and universities are developing advanced iron silicate protective coatings that not only enhance durability but also improve reactor energy efficiency. Advanced manufacturing methods, such as 3D printing, are being explored to build customized iron silicate parts, potentially revolutionizing reactor construction and maintenance in the future. These advances pave the way for safer and more efficient applications of fusion energy, highlighting the importance of ongoing research and the development of new materials.
Challenges and opportunities
While iron silicate offers several advantages, integrating it into fusion reactors faces technical challenges. One of the main issues is whether this material can maintain its structural integrity under continuous exposure to high levels of radiation and extreme temperatures. Additionally, producing and processing iron silicate, particularly for protective coatings in fusion reactor applications, require advancements in materials technology and production engineering. However, these challenges present opportunities for innovation in material design and manufacturing techniques. Collaboration between materials scientists and nuclear engineers could open new ways to optimize the use of iron silicate and similar compounds in fusion energy.
Future of fusion reactors and iron silicate
The future of fusion reactors largely depends on the development of materials that can withstand the harsh conditions of the fusion environment. Iron silicate, with its unique properties, has the potential to play a significant role in building safer and more efficient reactors. As advancements in fusion research and materials science continue, new applications for iron silicate are likely to emerge in this field. Successfully integrating iron silicate, especially in the form of protective coatings, could not only improve the feasibility of fusion reactors but also accelerate their development towards a commercially viable and sustainable energy source.
Conclusions
Nuclear fusion represents one of the most ambitious promises for the future of clean, sustainable energy. By mimicking the processes occurring in the sun, fusion offers the possibility of a virtually limitless energy source, without the risks and waste of nuclear fission. However, for this promise to become a reality, it is essential to solve the technical and material challenges presented by the containment and control of plasma in fusion reactors.
Iron silicate could be critical to the success of projects such as ITER and DEMO, due to its high strength and absorbance properties. This compound increases reactor efficiency and safety, and enables innovations in material design, including protective coatings and structural components. Along with advanced materials such as tungsten and RAFM steels.
The convergence of advances in materials technology, innovative manufacturing methods, and a sustained focus on research and development offers to make nuclear fusion a commercially viable energy source. Success in this area advances the way energy is generated, and would transform the fight against climate change, offering a safe and sustainable path to a clean energy future.
References
Own Source