In large industries there are diversities of processes that involve equipment for the storage or conversion of fluids; either, in its liquid, gaseous phase or even in a state transition phase, where the working medium may have corrosive properties or during the process its decomposition occurs, releasing very aggressive distillates that compromise the wall of the container, hence the importance of having a protective coating that allows to extend the useful life of the asset, protecting it from corrosive agents that may compromise its integrity and that of the process unit to which it belongs.
Pressure vessels are designed according to the type of material and wall thickness, which support the working conditions to which they will be exposed. The chemical processes developed in the oil industries generally handle very corrosive substances, where the base material of the container is required to be protected internally through the use of a coating; either in a section or in its entire surface, which generally consists of an elastomeric, ceramic, metallic, fibrous material, among others. In the case of the oil and gas industries, the ASME Code is used in its section VIII, which is the standard for the construction of pressure vessels where all the parameters for their design are considered, this standard in its part UCL, indicates the requirements that must be considered for the installation of integral coating resistant to corrosion; either, by means of metal overlapping (cladding), welding application (weld overlay) or fixed in the form of strips (strips lining).
When pressure vessels are in service and changes occur in the process parameters, due to pressure increase, temperature variation or the process is modified (such as the inclusion of additives, mixtures, steam injection points), damage can be caused to the the lining manifesting itself as cracking, erosion, pitting, among others, because these variations were probably not considered during the design of the vessel; and in turn, this condition puts at risk the integrity of the asset that needs to be protected and that could lead to unplanned maintenance of a process unit. When evaluating the interior of a container, visual inspection plays an important role in determining the condition of the coating, since through it, relevant information is obtained about the existence of indications, either in the form of pitting or cracks in the welds in the case of a strip linning or a weld overlay, and for a cladding there could be cracks, eroded areas, perforations, lack of adherence of the coating (bulging) with respect to the wall, head or some component of the container . The liquid penetrant technique is used to reinforce the visual evaluation of internal weld beads throughout their length and intersections to rule out cracking generated during service, or in any region where coating anomalies are visible.
The bulging or partial detachment of the inner lining in the container could cause the wall of the asset to have been affected by the exposure of the fluid and the damage could be seen with the naked eye. On the contrary, if the indication is in the form of: fissure, crack, pitting, there could be filtration between the wall of the container and the lining, allowing the damage to be progressive with a type of corrosion depending on the operational environment and its TAN (Total Acid Number), to cite a case, could be mentioned in a crude oil distillation process where corrosion is generated by HCL, Naphthenic, Sulfidation, among others. Once identified, the affected area is delimited to carry out the most pertinent repair, such as the application of material by placing lining strips (strips linning) or coating an area with welding (weld overlay), all this after sanitation. and preparation of the affected area. Taking as reference the applicable codes and culminating with a new application test of penetrating liquids to verify that there are no relevant indications within the repairs.
Bibliographic references.
ASME BPVC Section VIII Div. 1 Rules for Construction of Pressure Vessels.
ASME PCC-2 Repair of Pressure Equipment and Piping.
API 510 Pressure Vessel Inspection Code: In-service Inspection, Rating, Repair, and Alteration.
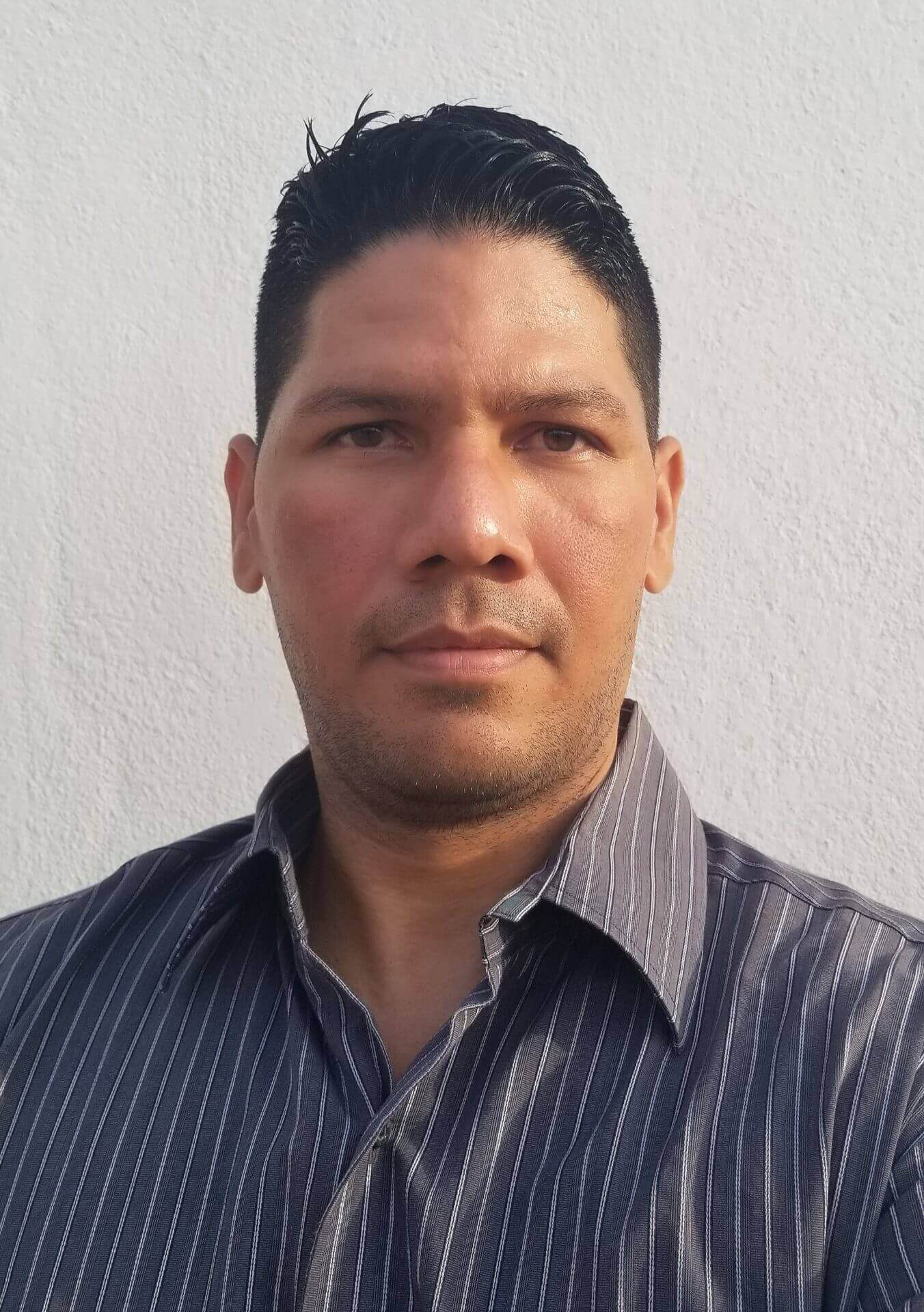
About the author: Ing. Edward Madrid.
Mechanical Engineer, with more than 8 years of experience in the area of equipment inspection in the oil and gas industry.
For more articles visit https://inspenet.com/en/articles/.