Table of Contents
- Key concepts in advanced materials
- Duplex stainless steels: Properties and advantages
- Composite tubes and bimetallic tubes: Efficiency and durability
- Strategies to improve corrosion resistance in duplex stainless steels
- Success cases in the implementation of duplex stainless steels
- Design and manufacturing of equipment with duplex stainless steel
- Comparison with carbon steels in terms of service life and maintenance costs
- Conclusions
- References
The selection of innovative materials is a key factor in the engineering of equipment subjected to highly corrosive environments. In sectors such as the petrochemical industry, energy, desalination process, materials are exposed to extreme conditions that accelerate degradation processes. Corrosion reduces equipment life, increases maintenance costs and, in critical cases, causes catastrophic failures that can compromise safety and operational continuity.
The industry has sought advanced solutions to mitigate these problems, developing metal alloys with higher mechanical and chemical resistance. In this context, duplex stainless steels have emerged as a highly efficient option due to their balance between mechanical strength and corrosion resistance, allowing the design of lighter and more durable equipment.
The current challenge lies in selecting the optimum materials for each application, considering not only their corrosion resistance, but also their long-term cost-benefit. The implementation of duplex stainless steels in industrial applications has been shown to extend equipment life, reduce maintenance costs, and improve operating efficiency.
This article discusses the evolution of corrosion resistant materials, their applications in industry and the advantages offered by these steels over other alloys in terms of mechanical performance and corrosion protection.
Key concepts in advanced materials
What are duplex stainless steels?
Duplex stainless steels are a family of metallic alloys that combine ferritic and austenitic phases in their metallurgical structure. This combination gives them higher mechanical strength and better localized corrosion resistance compared to traditional austenitic and ferritic stainless steels.
These steels contain balanced levels of chromium, molybdenum, and nitrogen, which enhance their resistance to aggressive environments such as seawater, strong acids, and chloride-rich solutions. Thanks to their dual-phase microstructure, duplex stainless steels can withstand high mechanical loads and offer greater durability in high-risk applications.
Evolution of metallic alloys to improve corrosion resistance
Throughout history, engineers have developed new materials to combat corrosion. Initially, carbon steels were the predominant option, but their low oxidation resistance led to the introduction of austenitic stainless steels (such as 304 and 316), which provided better protection in corrosive environments.
However, the need to improve the service life of equipment in demanding industries drove the development of duplex stainless steels, which emerged in the 1930s and were perfected in the 1970s with modern versions such as 2205 and 2507.
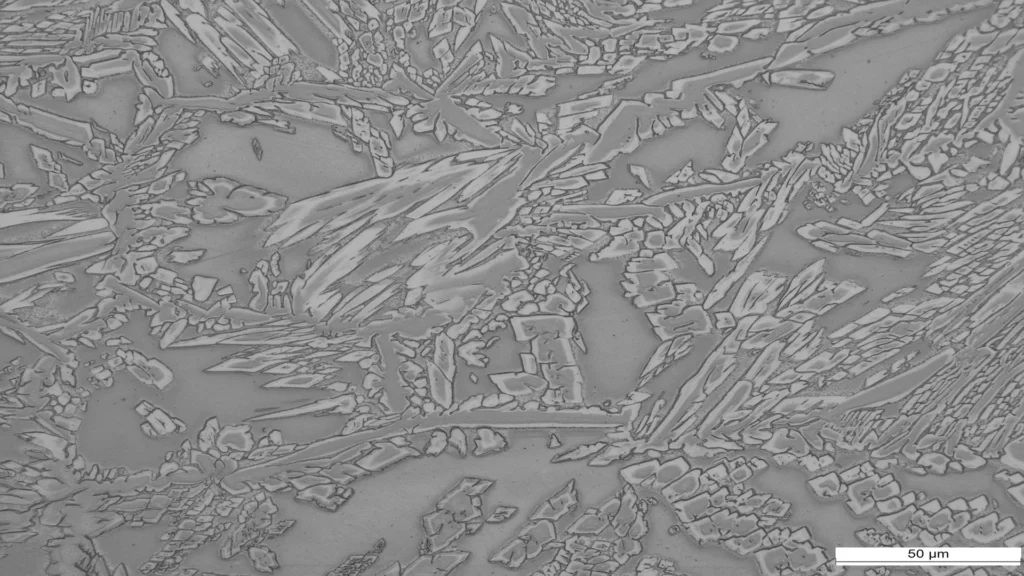
Key factors in material selection
- Mechanical and chemical properties:
- High mechanical strength, allowing for thinner walls and lighter equipment.
- Excellent resistance to pitting, intergranular, and stress corrosion cracking.
- Corrosion resistance in different environments:
- Superior performance in environments with high concentrations of chlorides and strong acids.
- Maintain structural integrity in elevated temperatures and extreme pressure conditions.
- Cost-benefit in critical industrial applications:
- Reduction of operational costs by minimizing failures and maintenance.
- Extended service life of equipment, reducing long-term financial impact.
Duplex stainless steels: Properties and advantages
Composition and metallurgical structure
Duplex stainless steels are characterized by their balanced microstructure, composed of approximately 50% ferritic phase and 50% austenitic phase. This duality provides a unique combination of high mechanical strength and excellent corrosion resistance.
The main alloying elements and their impact on properties are presented below:
- Chromium (Cr): Provides oxidation and corrosion resistance.
- Molybdenum (Mo): Improves pitting and crevice corrosion resistance.
- Nitrogen (N): Increases mechanical strength and reinforces austenitic phase stability.
The most common duplex stainless steel grades include 2205 (standard duplex) and 2507 (super duplex), both designed to withstand extreme corrosion conditions in critical industrial applications.
Mechanical strength and corrosion performance
Duplex stainless steels stand out for their combination of high mechanical strength and superior corrosion resistance, allowing them to outperform other metallic alloys in harsh environments.
Comparison with austenitic and ferritic stainless steels:
- Higher mechanical strength than austenitic steels, allowing for thinner components without compromising structural safety.
- Better stress corrosion cracking resistance compared to austenitic steels (such as 316L), making them ideal for chemical and marine industries.
- Lower nickel content, making them more cost-effective in terms of production costs and less susceptible to market price fluctuations..
Performance in aggressive environments:
- Petrochemical industry: Sulfide corrosion resistance enables use in refining and hydrocarbon transportation systems.
- Desalination plants: Ideal for high chloride environments, preventing premature equipment deterioration.
- Naval and marine industry: Protect submerged structures in seawater, where conventional steels fail quickly.
Service life of equipment in duplex stainless steel applications
One of the primary benefits of duplex stainless steels is their ability to extend the service life of equipment, reducing mechanical failures and maintenance costs. Compared to other alloys, duplex steel equipment can operate for decades without significant degradation.
By offering a solution with high mechanical resistance and corrosion protection, duplex stainless steels have been established as an efficient and economical alternative for critical applications where safety and durability are essential.
Composite tubes and bimetallic tubes: Efficiency and durability
In high-demand industrial applications, where materials are exposed to extreme conditions of temperature, pressure, and corrosion, the integration of composite tubes and bimetallic tubes represents an innovative solution to optimize equipment service life.
These tubes combine two or more strategically selected materials to maximize their best properties. For example, a tube may have an internal layer of corrosion-resistant duplex stainless steel, while its external structure is made of a more cost-effective material, such as carbon steel. This configuration provides excellent corrosion resistance in contact with aggressive fluids without compromising the project’s profitability.
Benefits of combining materials in composite tubes
- Cost optimization: Reduces the use of expensive materials without sacrificing performance.
- Enhanced corrosion resistance: Duplex stainless steel inner layers protect against chemical attack, pitting, and crevice corrosion.
- High mechanical strength: The material combination allows the tubes to withstand high pressures and temperatures without structural deformation..
Key industrial applications
- Heat exchangers: Used in petrochemical plants and power generation, where tubes are exposed to high temperatures and corrosive fluids.
- Chemical and petrochemical processes: Ideal for handling aggressive substances such as acids and chloride-rich solutions.
- Transport of highly corrosive fluids: Applied in industries such as desalination and water treatment, where conventional materials would fail rapidly.
The use of composite tubes and bimetallic tubes significantly extends the service life of equipment, reduces maintenance, and lowers operational costs.
Strategies to improve corrosion resistance in duplex stainless steels
Despite their excellent performance in aggressive environments, corrosion-resistant duplex stainless steels can further optimize their durability through advanced strategies that minimize material degradation over time.
Optimization of process conditions
The corrosion behavior of duplex stainless steels is highly influenced by operational factors such as temperature, pressure, and chemical composition of the environment.
Key factors affecting corrosion in duplex steels:
- Chloride presence: Can accelerate pitting and crevice corrosion, especially at elevated temperatures.
- High-temperature oxidation: Prolonged exposure to temperatures above 250-300°C should be avoided, as it can cause the precipitation of intermetallic phases, reducing corrosion resistance.
- Selection of specific grades: For more aggressive environments, the use of super duplex steels (2507) with higher molybdenum and nitrogen content is recommended.
Application of advanced coatings
Specialized coatings can significantly improve corrosion resistance in duplex stainless steel components, protecting them from chemical agents and extreme conditions.
Recommended coating types:
- Metallic oxide coatings: Form a passive barrier against corrosion in marine and high-salinity environments.
- Polymeric and ceramic coatings: Ideal for applications in the chemical industry, where acid contact can degrade the base material.
- Surface treatments such as electropolishing and passivation, which enhance the protective layer of duplex stainless steel. Electropolishing is a crucial finishing process for duplex stainless steel, enhancing its corrosion resistance, removing surface imperfections, and improving cleanliness. This video courtesy of New England Electropolishing, provides an in-depth look at how electropolishing works, the steps involved, and the importance of adhering to industry standards like ASTM B912 and ASTM A967. Learn how this process ensures superior performance in critical applications where corrosion resistance and precision are essential:
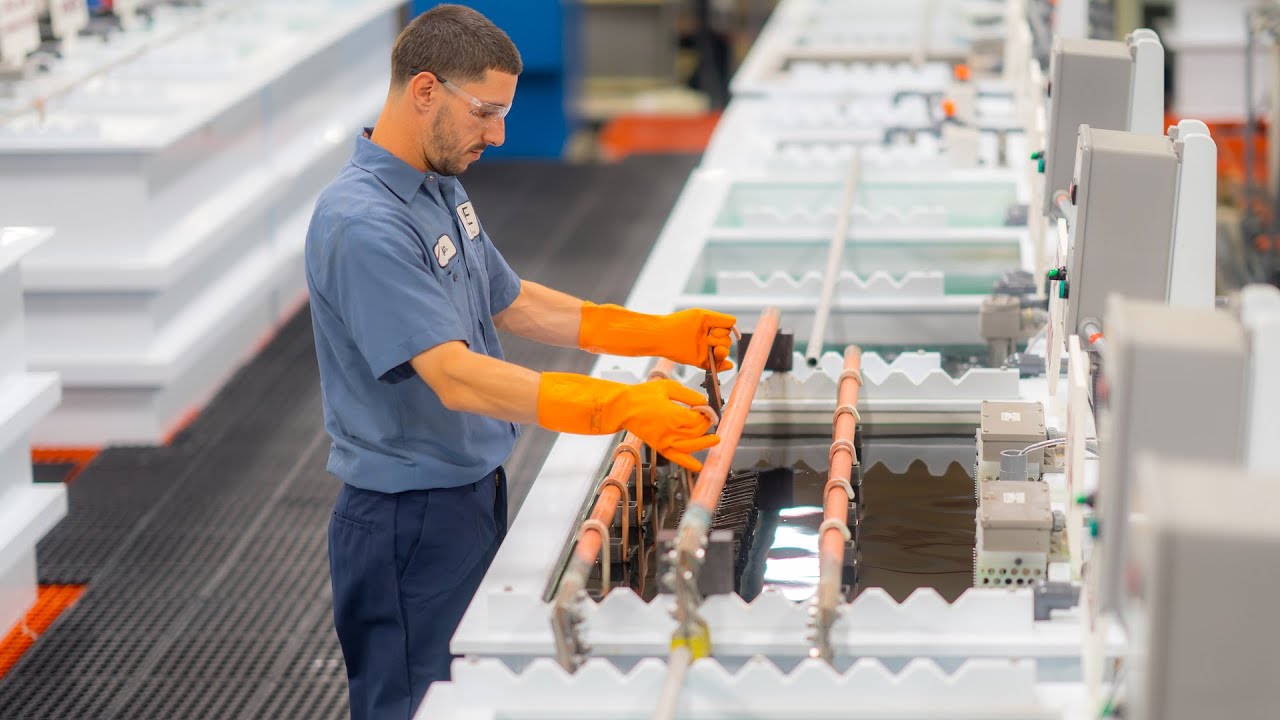
The electropolishing process.
Integration with cathodic protection
Cathodic protection is an electrochemical technique used to mitigate corrosion in metallic structures exposed to aggressive environments, such as seawater and industrial fluids. In corrosion-resistant duplex stainless steels, its integration helps extend equipment service life and prevents pitting and crevice corrosion, especially in high-chloride environments.
Success cases in the implementation of duplex stainless steels
Duplex stainless steels have demonstrated high efficiency and durability in various industrial applications, where traditional materials failed due to corrosion and high mechanical demands. Their use has extended the service life of equipment, reduced maintenance costs, and improved operational performance.
Desalination plants
The super duplex 2507 stainless steel has been successfully used in pipes, evaporators, and pumps in reverse osmosis plants, where highly corrosive seawater rapidly deteriorated conventional austenitic stainless steels. The implementation of duplex stainless steel has reduced failures due to pitting corrosion and extended system service life by up to 30%.
Petrochemical industry
In refineries, duplex 2205 stainless steel has replaced carbon and austenitic steels in hydrocarbon transfer pipelines with high sulfur and chloride content, significantly reducing stress corrosion cracking and unplanned maintenance shutdowns.
Energy sector
In heat exchangers and high-pressure boilers, the use of duplex stainless steels has allowed for thinner tube walls without compromising mechanical strength, increasing thermal efficiency and improving resistance to intergranular corrosion and erosion.
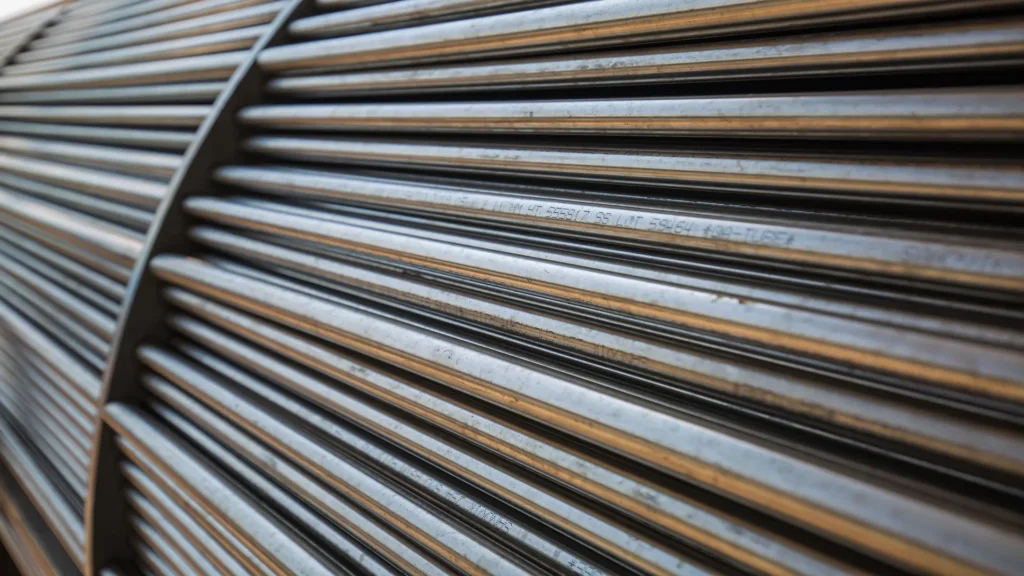
These success cases validate the positive impact of duplex stainless steels, establishing them as an ideal solution in high-demand industries.
Design and manufacturing of equipment with duplex stainless steel
Impact of thermal expansion on heat exchangers made of duplex stainless steel
Heat exchangers operate in environments with significant temperature variations, causing thermal expansion and contraction in materials. Duplex stainless steels exhibit lower thermal expansion than austenitic steels, reducing mechanical stress in joints and extending equipment service life. This property minimizes structural deformation and thermal fatigue risk, which is critical in petrochemical and desalination plants.
Optimization of wall thickness and its effect on operating pressure
The high mechanical strength of duplex steels allows for the manufacture of equipment with thinner walls without compromising structural safety. In high-pressure applications, reducing wall thickness decreases total equipment weight, improves heat transfer efficiency, and lowers manufacturing and transportation costs. Additionally, the lower material density enables the design of more compact equipment with optimized performance in industrial cooling and energy generation systems.
Comparison with carbon steels in terms of service life and maintenance costs
Unlike carbon steels, duplex stainless steels offer superior corrosion resistance and greater structural stability in aggressive environments. In pipes and heat exchangers , carbon steels require frequent coatings or anti-corrosion treatments, increasing maintenance costs. Duplex steels eliminate the need for these treatments, reducing intervention frequency and extending equipment service life by 30-50%.
Key factors in manufacturing high corrosion-resistant components
To ensure the maximum performance of duplex stainless steel, it is essential to:
- Control welding to avoid the precipitation of intermetallic phases that affect corrosion resistance.
- Select the appropriate alloy according to chloride concentration and operating temperature.
- Optimize design to reduce mechanical stresses in critical areas and improve thermal efficiency.
Implementing these factors ensures greater durability and operational efficiency in duplex stainless steel equipment for the energy, petrochemical, and fluid processing industries.
Conclusions
Duplex stainless steels have revolutionized the industry with their unique combination of high mechanical strength and excellent corrosion resistance, making them the ideal choice for high-demand environments. Their integration into desalination, petrochemical, and energy sectors has significantly extended equipment service life, reduced maintenance costs, and improved process efficiency.
The future of innovative materials is focused on the development of new duplex alloys with even greater resistance to extreme environments, optimizing safety and sustainability in industrial infrastructure. Technologies such as composite tubes, advanced coatings, and cathodic protection will continue to enhance the performance of these steels, allowing large-scale projects to be implemented with greater operational efficiency.
Success cases in desalination plants, refineries, and the energy sector have demonstrated that duplex stainless steels do more than just replace conventional materials—they set a new standard in durability and performance. Their strategic use in heat exchangers , pipelines, and structures exposed to extreme conditions confirms that investing in advanced alloys is key to the future of the industry.
References
Own source