Introduction
Industry 4.0 and Industry 5.0 share several key similarities, mainly in the application of advanced technologies, interconnection, and digitization, as well as customization and flexible production. Both focus on automation and the use of cutting-edge technology to improve industrial processes, facilitating the connection and communication between machines and systems to increase efficiency and productivity.
The interconnection of industrial systems and processes is fundamental to both, with digitization playing a crucial role in converting analog information into digital data, thus simplifying its storage, analysis, and subsequent use.
What is Industry 5.0?
Industry 5.0 represents a significant evolution from Industry 4.0, not only focusing on automation and technological efficiency, but also on the reintegration of human values into the production environment. This approach seeks closer and more meaningful collaboration between humans and machines, promoting a balance where technology amplifies human capabilities rather than simply replacing them.
Industry 5.0 is knocking on our doors, many organizations are in the process of transition: Automation, Integration, and Information Management. Get ready to watch the following video and learn more about it. Source: VA ControlGroup.
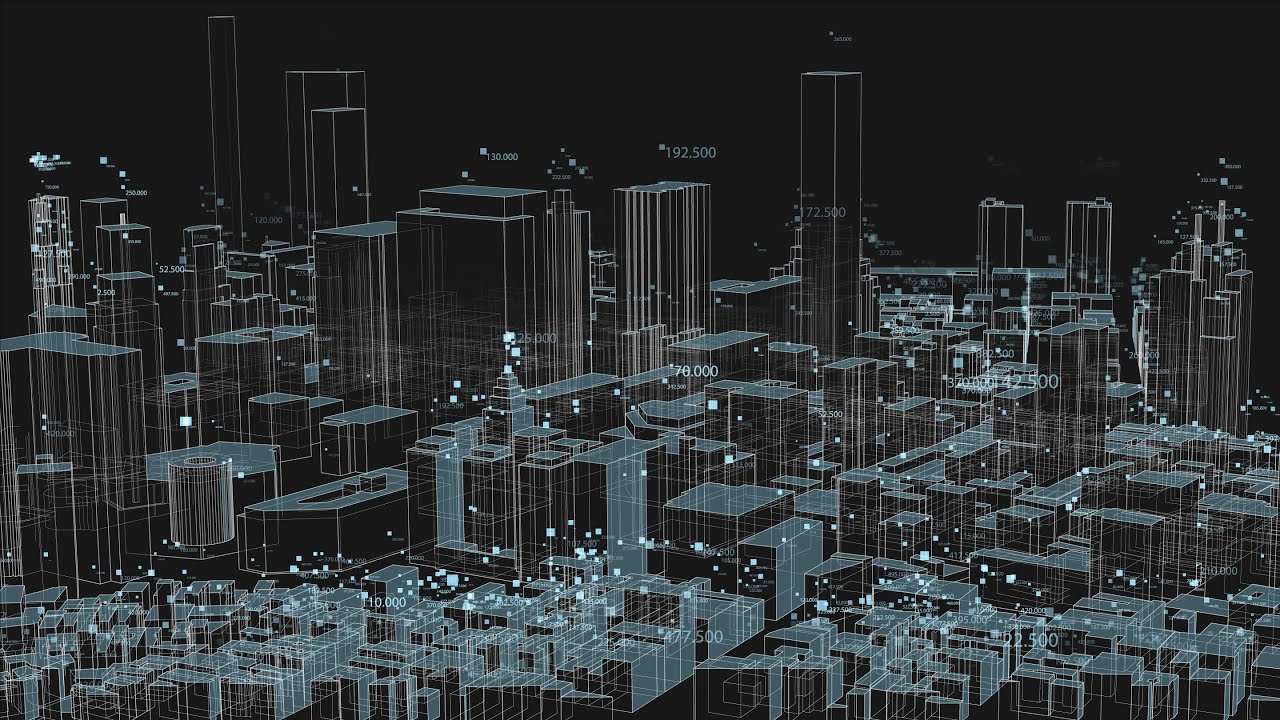
Industry 5.0, towards Society 5.0
Main characteristics
- Human-Machine Collaboration: Industry 5.0 is based on the synergistic interaction between human workers and collaborative robots (cobots). These robots not only perform repetitive and precise tasks but also support humans in creative and decision-making activities.
- People-centered: Unlike Industry 4.0, which focuses on automation, Industry 5.0 puts people at the center of the production process. Technology is adapted to improve the worker’s experience and well-being, providing a safer and more enriching work environment.
- Sustainability and resilience: Industry 5.0 promotes sustainable and resilient practices, ensuring that industrial processes are not only efficient, but also environmentally friendly and able to adapt to unexpected changes and challenges.
Benefits
- Improved quality of work life: By integrating technologies that support and complement human skills, workers can focus on more rewarding and less repetitive tasks, improving their job satisfaction and well-being.
- Mass customization: The combination of human skills and technological capabilities enables highly personalized production that better matches consumer needs and preferences.
- Innovation and creativity: By freeing workers from monotonous tasks, Industry 5.0 fosters an environment where creativity and innovation can flourish, driving the development of new products and services.
Challenges
- Technology integration: One of the biggest challenges is the integration of new technologies with existing systems, ensuring that humans and machines can work together efficiently.
- Training and adaptation: Workers need to acquire new skills to interact effectively with advanced technologies. This requires a continuous focus on training and professional development.
- Cybersecurity: With increased interconnectivity, protecting data and systems against cyber-attacks becomes a critical priority to maintain the integrity and security of production processes.
Industry 5.0 represents not only a technological breakthrough but also a cultural and organizational shift, where collaboration and mutual respect between humans and machines drive a new era of productivity and well-being. This holistic approach promises not only to improve production efficiency and customization but also to create more humane and sustainable work environments.
What is Industry 4.0?
Industry 4.0, also known as the Fourth Industrial Revolution, represents a profound transformation in industrial processes through digitization and advanced automation. It is characterized by the interconnection of systems through technologies such as the Internet of Things (IoT), Big Data, artificial intelligence (AI) and cloud computing.
Main characteristics of Industry 4.0
- Interconnectivity and communication: Machines and IT systems can now communicate with each other in real-time thanks to the integration of sensors and IoT devices. This enables continuous monitoring and control of production processes.
- Automation and efficiency: Automation is one of the central pillars of Industry 4.0. The use of robots and automated systems reduces the need for human intervention in repetitive tasks, increasing precision and production speed.
- Big Data and Data Analytics: The collection and analysis of large volumes of data enables companies to optimize their processes, predict failures, and improve decision-making. AI and Machine Learning play a crucial role in interpreting this data and continuously improving processes.
- Simulation and Digital Twins: Digital simulation allows the creation of virtual replicas of physical systems, known as digital twins, which help predict behavior and optimize performance before implementing changes in the real world.
- Cybersecurity: With digitalization, the protection of data and systems against cyber-attacks becomes critical. Cybersecurity in Industry 4.0 focuses on protecting the integrity and availability of connected systems.
- Cloud computing: The use of the cloud facilitates the management of data and applications, allowing flexible and scalable access to the resources needed for industrial processes.
Benefits and challenges
Benefits:
- Increased productivity: Automation and process optimization result in greater efficiency and cost reduction.
- Product customization: The ability to tailor production to specific customer needs improves satisfaction and competitiveness.
- Sustainability: Advanced technologies enable more efficient use of resources, contributing to environmental sustainability.
Challenges:
- Initial investment: The implementation of advanced technologies requires significant investment.
- Workforce adaptation: It is necessary to train workers in new skills and manage cultural change within organizations.
- Cybersecurity: Protecting interconnected systems against cyber threats is an ongoing and complex task.
Industry 4.0 is revolutionizing the industrial landscape, creating opportunities and challenges that companies must manage to stay competitive in an increasingly digitized global marketplace.
Industry 4.0 vs. Industry 5.0
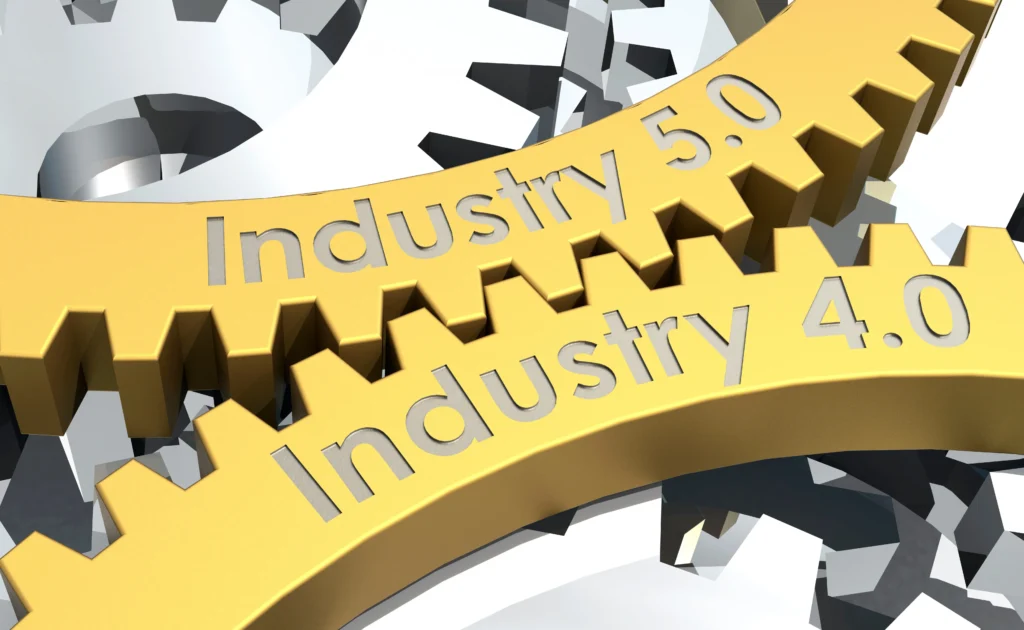
Industry 4.0 and Industry 5.0 represent different stages in industrial evolution, each with particular approaches and technologies.
Approach
- Industry 4.0: Focuses on automation and interconnection of systems through the use of advanced technologies such as the Internet of Things (IoT), Big Data, and artificial intelligence (AI). The main objective is to improve efficiency and productivity through digitization and process automation.
- Industry 5.0: Goes a step further by emphasizing collaboration between humans and machines. It focuses on personalization and sustainability, seeking to make technologies serve people. Industry 5.0 aims to create an environment where workers and artificial intelligence work together to achieve more personalized and environmentally friendly production.
Technology
Industry 4.0:
- IoT: Enables communication between machines and systems in real time.
- Big Data and AI: Analysis of large volumes of data to optimize processes.
- Automation: Robots and automated systems perform repetitive tasks.
Industry 5.0:
- Cobots: Collaborative robots that work alongside humans, complementing their skills.
- Sustainability: Efficient use of resources and waste reduction.
- Customization: Production tailored to individual consumer needs.
Benefits
Industry 4.0:
- Increased efficiency and reduced operating costs.
- Improved data-driven decision-making.
- Increased productivity through automation.
Industry 5.0:
- Improved quality of work life by freeing workers from monotonous tasks.
- Production is more adapted to market demands, reducing surpluses and waste.
- Attraction and retention of young and digitally skilled talent, promoting a more attractive and sustainable work environment.
Challenges
Industry 4.0:
- High initial investment for the implementation of new technologies.
- Need to adapt existing infrastructure.
- Cybersecurity risks associated with the interconnection of systems.
Industry 5.0:
- Integration of advanced technology with current systems.
- Continuous training and adaptation of the workforce.
- Management of human-machine collaboration to maximize benefits and minimize conflicts.
Comparison between Industry 4.0 and Industry 5.0
The evolution of industry has reached a point where not only efficiency and automation are paramount, but also the integration of human values into the production environment. The transition from Industry 4.0 to Industry 5.0 represents this change, highlighting the importance of human-machine collaboration.
Table: Differences between Industry 4.0 and Industry 5.0.
Aspect | Industry 4.0 | Industry 5.0 |
Approach | Digitization and advanced automation. | Human-machine collaboration. |
Automation and efficiency | Robots and automated systems perform repetitive and precise tasks. | Cobots support creative and decision-making tasks. |
IoT and Big Data | Connected devices share data in real-time. | Connected devices share data in real time. |
Artificial intelligence | Algorithms optimize processes and predict failures. | Algorithms optimize processes and predict failures. |
Human-robot collaboration | N/A | Collaborative robots work alongside humans. |
Focused on people | N/A | Improved worker experience and well-being. |
Sustainability | N/A | Sustainable industrial practices. |
Key benefits | Increased efficiency, cost reduction, improved decision making. | Improved quality of working life, adapted production, talent attraction. |
Key challenges | High initial investment, infrastructure adaptation, cybersecurity. | Advanced technology integration, continuous training, man-machine collaboration management. |
Benefits of adopting Industry 5.0 over Industry 4.0
The transition to Industry 5.0 offers significant improvements in efficiency, productivity, and sustainability. These benefits are discussed below with highlighted examples for improving efficiency, increasing productivity, and managing sustainability: We describe some examples:
- Autonomous manufacturing: Industry 5.0 incorporates collaborative robots (cobots) that work alongside humans, performing repetitive and monotonous tasks. This not only frees workers to focus on strategic tasks but also increases operational efficiency by enabling continuous production without interruptions. One example of this is Universal Robots, which uses cobots to improve productivity and reduce operating costs.
- Hyperpersonalization: Industry 5.0 enables companies to offer personalized products and services, better adjusting to consumers’ needs and preferences. Using advanced technologies such as Big Data and AI, companies can analyze data in real time and adapt their products quickly. This not only improves customer satisfaction, but also increases conversion rates and loyalty. Universal Robots in Denmark has implemented robots that collaborate with humans to perform repetitive tasks, allowing employees to focus on more creative and strategic activities.
- Sustainable practices: Industry 5.0 focuses on reducing environmental impact through the efficient use of resources and minimizing waste. This is achieved through the implementation of technologies that optimize the consumption of energy and material resources. In addition, it encourages circular production models that promote the reuse and recycling of materials. For example, the transition to renewable energy sources and improving the energy efficiency of industrial processes are common practices in this new industrial era.
Additional benefits
- Social value: Industry 5.0 places a strong emphasis on human and environmental well-being, seeking not only profitability but also a positive impact on society. This includes the creation of more skilled jobs and the development of safer and more enriching work environments.
- Responsive supply chain: Companies can adapt quickly to changes in demand and market conditions, improving resilience and competitiveness. This flexible and adaptable approach enables a more agile response to customer needs and global market challenges.
- Interactive products: The combination of advanced technologies and a human-centered approach enables the creation of products that offer enhanced user experiences. This not only increases customer satisfaction but also fosters loyalty and differentiation in the marketplace.
The role of collaborative robots in Industry 5.0
Collaborative robots, or cobots, play a key role in Industry 5.0 by facilitating better integration and collaboration in production processes. Unlike traditional robots that operate in isolation, cobots are designed to work alongside humans, complementing their skills and enabling greater efficiency and flexibility in production.
Benefits of Cobots
- Reducing monotonous tasks: Cobots take over repetitive and tedious tasks, freeing workers to focus on more strategic and creative activities. This not only increases job satisfaction but also improves overall productivity.
- Accuracy and consistency: By performing tasks with high precision, cobots reduce errors and improve product quality. This is crucial in industries where accuracy is vital, such as electronics manufacturing or the automotive industry.
- Flexibility in production: Cobots can be easily reprogrammed and adapted for different tasks, enabling more agile and customized production. This is essential in a market that increasingly demands customized, high-quality products.
- Improved safety: Equipped with advanced sensors, cobots can work safely alongside humans, reducing the risk of workplace accidents. This creates a safer and more efficient work environment.
Implementation examples of these technologies
Companies such as Universal Robots in Denmark have implemented cobots to improve integration and collaboration on their production lines. These cobots assist human workers in repetitive tasks, allowing them to focus on activities that require more creativity and strategic skills.
Conclusions
Industry 4.0 focuses on automation and efficiency through the use of technology, while Industry 5.0 harmonizes human and technological capabilities to achieve more customized, sustainable, and collaborative production.
Industry 5.0 improves efficiency and productivity through the integration of advanced technologies and human-robot collaboration and promotes sustainable practices with a focus on human and social well-being. This industrial evolution promises a more balanced and sustainable future for businesses and society at large by fostering more sustainable and personalized production.
References
- https://www.mecalux.com.mx/blog/industria-4-0-vs-industria-5-0
- https://www.telefonica.com/es/sala-comunicacion/blog/industria-5-diferencias-industria-4/
- https://www.sap.com/latinamerica/insights/industry-5-0.html
- https://icemd.esic.edu/knowledge/articulos/industria-5-0-lo-que-significa-y-sus-beneficios/