Table of Contents
- Introduction
- What is the oil refining process?
- Crude oil preparation
- Separation of components: Initial distillation
- Atmospheric distillation
- Hydrocarbon Conversion: Cracking, Reforming and Alkylation
- Treatment and desulfurization: Improving product quality
- Storage and distribution of refined products
- Environmental impact and sustainability in refining
- Conclusions
- References
Introduction
Industrial refining processes of petroleum are fundamentals for converting crude oil into higher value products in the energy and petrochemical industries. These processes, such as petroleum are essential for converting crude oil into higher value products in the energy and petrochemical industry. This process not only allows crude oil to be transformed into useful products such as gasoline, diesel, kerosene and petrochemicals, but also plays a crucial role in the production of vital resources for the global economy.
In this article, we will analyze in detail the industrial processes of petroleum refining, explaining how the different hydrocarbons are separated, treated and processed from crude oil, from the chemical bases to the advanced techniques used in the industry.
What is the oil refining process?
A set of industrial operations by which crude oil is converted into refined products suitable for consumption or for further processing into chemical products. This process involves several key stages, including the separation of crude oil components, the conversion of heavy hydrocarbons into lighter products and the improvement of the quality of these products through specialized treatments.
Crude oil is a complex mixture of different hydrocarbons, and due to its heterogeneous composition, it cannot be used directly in its original form. Therefore, it is necessary to carry out a series of industrial processes in order to separate the different components to obtain products with specific characteristics that meet the quality standards and market demand. The following are the five basic processes of oil refining:
The following image shows the main stages: distillation, conversion and finally the separation of the crude fractions.

Crude oil refining begins with atmospheric distillation, in which the oil is heated and separated into fractions according to their boiling point, obtaining products such as gases, naphtha, kerosene, and gas oil. The heavy residue from this stage is then subjected to vacuum distillation, where additional fractions such as heavy gas oils and lubricating oils are extracted.
In the conversion stage, the heavy molecules are transformed into lighter and more valuable products by processes such as catalytic cracking, which breaks long chains to generate gasoline and diesel, hydrotreating, which removes sulfur and nitrogen compounds, and catalytic reforming, which increases the octane rating of gasoline. Subsequently, the fractions obtained undergo additional treatments to desulfurize them and eliminate impurities, ensuring compliance with environmental regulations.
Finally, the different refined fractions are blended and additives are added in the finishing stage, thus obtaining finished products such as fuels, asphalt and raw materials for the petrochemical industry. This process ensures optimal use of crude oil and the production of materials that meet a variety of needs.
Crude oil preparation
The refining process begins with the receipt and storage of crude oil. The crude oil is transported through pipelines, ships, or railroads to the refinery. Before starting the process, the crude oil is dehydrated and desalted to remove water and salts, which can cause corrosion in the refinery facilities and affect the refining equipment. To summarize:
- Transport of crude oil to the refinery.
- Dehydration and desalting to eliminate water and salts.
Separation of components: Initial distillation
The first stage in the oil refining process is the separation of its components. This process is carried out through a technique called distillation, which takes advantage of the differences in the boiling points of the different hydrocarbons present in the crude oil. During this stage, the crude oil is heated to very high temperatures and then introduced into a distillation column, where the different compounds are separated into fractions according to their boiling temperature.
Atmospheric distillation
In atmospheric distillation, crude oil is heated and fed into a distillation column operating at atmospheric pressure. As the crude oil vaporizes, the lighter components (such as gases and naphtha) move up the column, while the heavier components (such as gas oil and residue) move down. Several fractions are produced in this process, including:
- Light gases (butane, propane).
- Naphtha (to produce gasoline).
- Kerosenes (used in aviation and heating).
- Gas oil (used for diesel production).
- Heavy residues (raw materials for other processes).
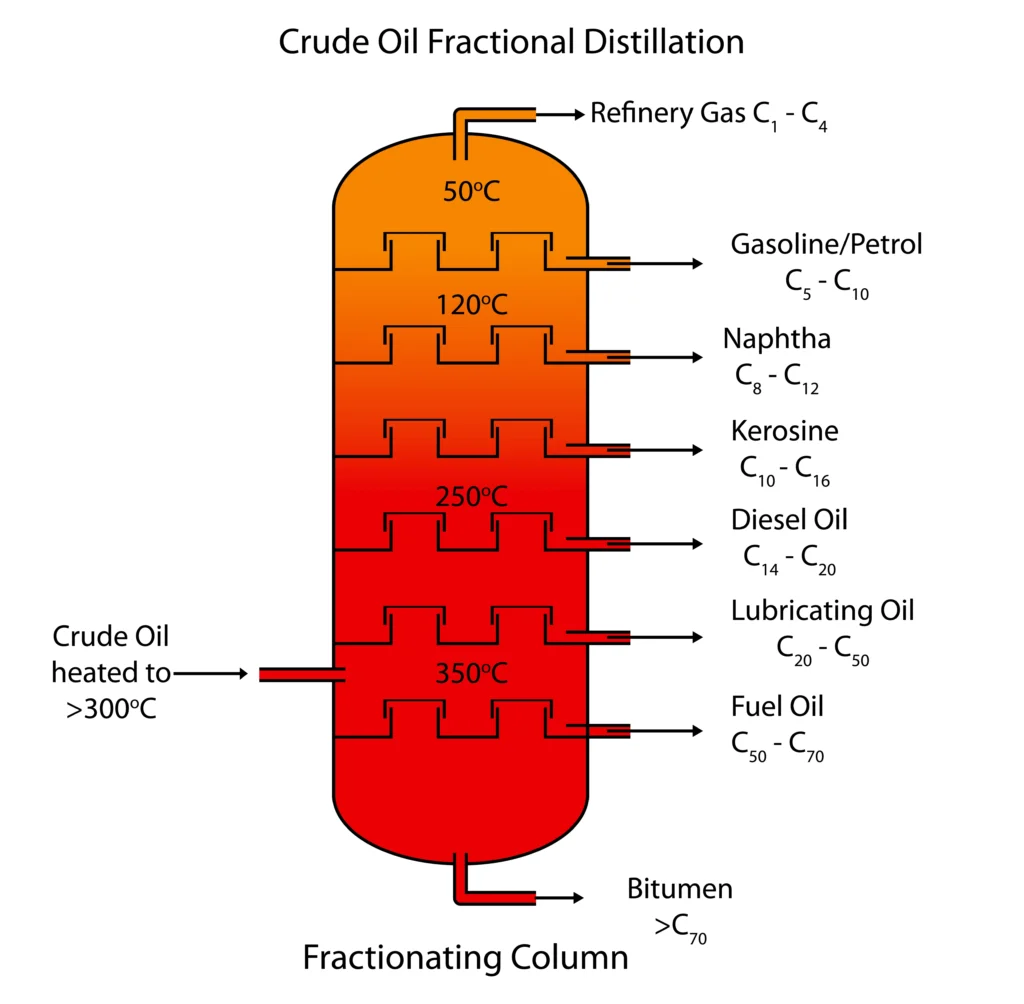
Vacuum distillation
The heavy residues generated in atmospheric distillation, such as column residue, can be distilled again, but at reduced pressures, through a process known as vacuum distillation. This produces the separation of heavier fractions, such as lubricating oils and asphalts, without decomposing the molecules due to the elevated temperature.
Hydrocarbon Conversion: Cracking, Reforming and Alkylation
Once the crude oil components have been separated, the next step in the oil refining process is to convert the heavier hydrocarbons into lighter, more valuable products through the catalytic conversion process, which includes catalytic cracking, catalytic reforming and other processes that break down the long hydrocarbon chains into smaller molecules.
Catalytic cracking
In this process, a catalyst is used to break the large molecules of heavier hydrocarbons into lighter products, such as gasoline and diesel. The process is carried out in a reactor where the hydrocarbons are mixed with a catalyst at high temperatures. The resulting products include high-octane naphtha, high-grade gasoline and diesel fuel.
According to statistics from the International Energy Agency (IEA), approximately 30% of global oil refining capacity uses the catalytic cracking process to maximize the production of gasoline and other petroleum products.
Thermal cracking
In this process, crude oil or heavy fractions are heated to very high temperatures in the absence of catalysts. The high temperature causes the large hydrocarbon molecules to break down into smaller molecules. Although less common than catalytic cracking, it is still important in some refineries.
Catalytic reforming
In this case, the process is used to transform low-octane naphtha into high-octane naphtha, thus improving the quality of the gasoline produced. Catalytic reforming not only improves the octane rating of fuels, but also produces hydrogen, which is used in other stages of the process for desulfurization and other treatments.
Alkylation
Alkylation combines butane and propane isomers to form heavier products, such as octane, used in the production of high-octane gasoline. This process is essential for improving gasoline quality without having to rely on chemical additives.
Treatment and desulfurization: Improving product quality
The next step in the oil refining process is the treatment of the products obtained to remove impurities and improve their characteristics. One of the most important treatments is hydrodesulfurization, which removes the sulfur present in petroleum products such as gasoline and diesel.
Hydrotreating
Hydrotreating is a process in which refined products, such as gasoline or diesel, are treated with hydrogen at high pressures and temperatures. This is intended to remove contaminants such as sulfur, nitrogen and heavy metals, as well as to improve the quality of the final product. It is essential to comply with environmental regulations on pollutant emissions.
According to data from the International Energy Agency (IEA), global refinery hydrotreating capacity has increased by 40% in the last decade, reflecting the growing need to meet stricter environmental standards.
Desulfurization
Desulfurization involves the removal of sulfur compounds, such as sulfur dioxide (SO₂), which is released when fuels are burned, to meet environmental standards.
Treatment of metals and other contaminants
The treatment of heavy metals, such as vanadium and nickel, is another essential process in oil refining, which can damage refinery equipment and decrease the efficiency of catalytic processes. Through various chemical and thermal processes, these contaminants are removed to ensure high quality production and prolong the life of refinery equipment.
Storage and distribution of refined products
Once the refined products have gone through the conversion and treatment processes, they are stored in tanks and distributed through various transportation networks, such as pipelines, tankers, and ships. The main products obtained are:
- Gasoline (for automobiles and other vehicles).
- Diesel (for heavy vehicles and machinery).
- Kerosene (for aviation and heating).
- Lubricating oils (for engines and industrial machinery).
- Asphalt (for road and pavement construction).
Each product requires specific storage and distribution conditions to ensure its quality and safety. The following chart provides a complete summary of the oil refining process and an explanatory video of the overall process: Source: API.

Overview of the refining process.
Environmental impact and sustainability in refining
The oil refining process has a significant impact on the environment. Refineries emit polluting gases, such as carbon dioxide, nitrogen oxides, sulfur and volatile compounds. However, current technologies, such as gas treatment and carbon capture, are helping to mitigate these impacts. Refineries are also implementing energy efficiency processes and seeking greater sustainability by integrating renewable energy sources into their operations.
Conclusions
Petroleum refining is an essential industrial process that transforms crude oil into useful and marketable products. From distillation to conversion and treatment processes, refining involves a series of complex steps that require sophisticated equipment and advanced technologies. The growing demand for high-quality products and the need to meet environmental standards have driven the development of new techniques and improvements in industrial refining processes.
By understanding the industrial processes involved in the oil refining process, we can appreciate the importance of this sector in the global economy and its crucial role in providing essential resources for energy and industry. With the advancement of technology and innovations in sustainability, petroleum refining will continue to be a fundamental pillar in meeting the energy needs of the future.
Learn more about petroleum refining and its impact on the energy industry.
References
Own source