Table of Contents
- What are steel alloys?
- Types of steel alloys
- Carbon steel: strength and hardness
- Stainless steel: Durability and corrosion resistance
- Factors affecting the strength, hardness, and durability of steel
- Statistics in the development of steel alloys
- Industrial applications for alloys
- Expert opinions on the impact of steel alloys
- Future of Alloy Steels: Innovation and Sustainability
- Conclusions
- References
Since ancient times, alloy types have been the secret behind the creation of stronger and more durable materials. Today, choosing the right alloy is more important than ever, especially in sectors such as construction and automotive. But what makes steel so special? The answer lies in the steel alloys that make it up.
In this article, an analysis is made on how different alloy components significantly impact the mechanical properties of steel (strength, steel hardness, and durability), in order to provide clear information on how these decisions influence sectors such as industrial, construction, and energy.
What are steel alloys?
Steel is an alloy composed mainly of iron and carbon, but its strength comes from the other elements that are added during its production, such as nickel, chromium, or molybdenum. These components modify the mechanical and chemical properties of steel, allowing it to be adapted to specific applications.
Main alloying elements and their effect on steel properties
Carbon steels are generally composed of five main elements: carbon, silicon, manganese, phosphorus, and sulfur. In addition to these elements, other metals or compounds are added, such as nickel, chromium, vanadium, tungsten, molybdenum, cobalt, copper, titanium, among others, called alloy steels. These additional elements, known as alloying elements, improve the properties of the steel for specific applications.
These alloying elements can dissolve in ferrite, form solid solutions with alpha iron, or tend to form carbides. In addition, some of these elements alter the critical temperatures in the equilibrium diagrams, such as the Ac and Ar points in the iron-carbon diagram, rising or falling as the case may be.
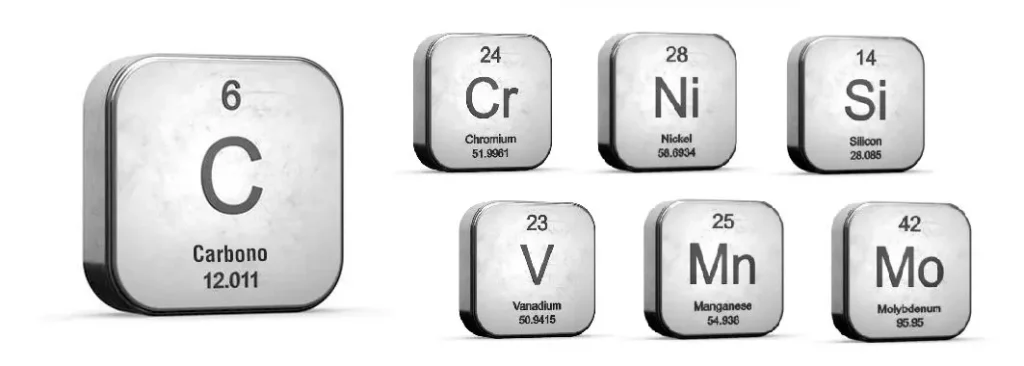
The influence of the alloying elements varies significantly, and by adjusting their percentages appropriately, steels with very diverse characteristics can be obtained. This makes it possible to manufacture thick parts with high internal strength, tools that effectively resist corrosion, mechanical components with high hardness and toughness, and mechanisms that maintain high strength even at high temperatures. It is also possible to create complex molds that do not deform or crack during hardening.
Influence of nickel and chromium alloying elements in the energy industry
1. Nickel (Ni): It plays a key role in heat treatments by preventing grain growth, which helps to increase the toughness of the steel. In addition, nickel reduces the critical point Ac, which allows treatments to be carried out at slightly lower temperatures than those required for conventional steels.
Steels alloyed with nickel achieve greater elasticity, elongation, and strength compared to carbon or low-alloy steels, while maintaining the same hardness. Nickel is essential in the manufacture of stainless steels and steels resistant to high temperatures, where it is combined with chromium in percentages varying between 8% and 20%. Example: stainless steel type 316L.
Nickel dissolves in ferrite and does not have a great tendency to form carbides. Its presence increases toughness and strength in annealed steels, and in steels with high chromium content, it tends to retain austenite, which improves their mechanical properties.
2. Chromium (Cr): It is one of the most widely used alloying elements in alloy steels, and is widely used in construction steels, tools, stainless steels, and heat-resistant steels. Its main effects are:
- Increases the hardness and tensile strength of steel.
- Improved hardenability.
- Reduces deformations during hardening.
- Increases wear and abrasion resistance.
- Improves resistance to high temperatures.
- It provides corrosion resistance, converting the steel into stainless steel.
Chromium dissolves in ferrite and has a strong tendency to form chromium carbides and complex carbides, which further enhances the strength and durability of the steel. Example: tubes and coatings for cracking furnaces.
Types of steel alloys
Alloy types vary according to the elements added and their proportions. There are two main categories: carbon steel and stainless steel. Each has distinctive properties that make it more suitable for certain uses.
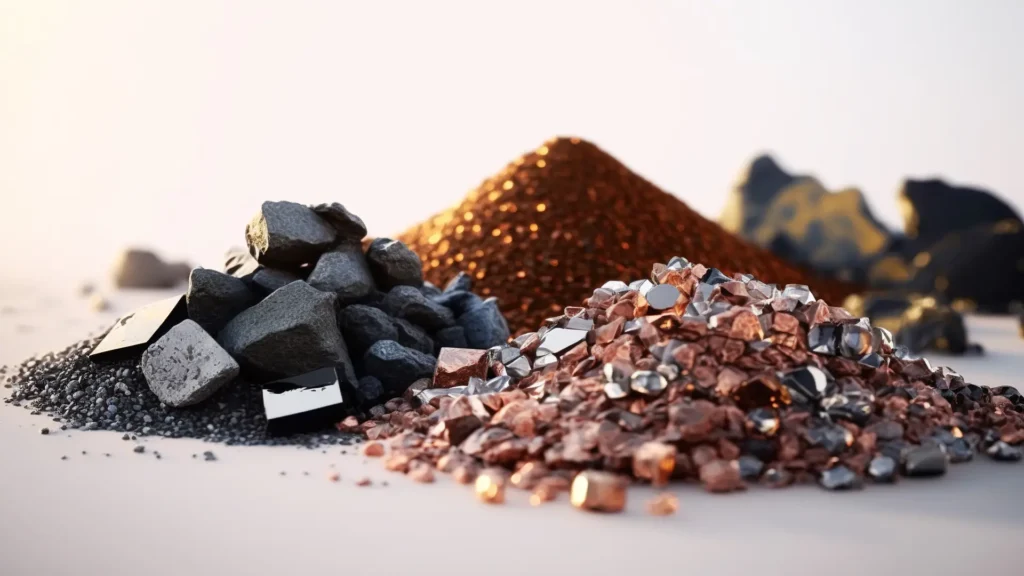
Carbon steel: strength and hardness
Carbon steels, as a general rule, contain: carbon, silicon, manganese, phosphorus, and sulfur. It is one of the most common alloys in the industry and its carbon percentage can vary depending on the application. It is classified into three types according to its carbon content: low, medium, and high.
- Low carbon steel: It is the most malleable, which makes it easier to work and weld. However, its steel hardness is relatively low.
- Medium carbon steel: It has higher strength and is more wear-resistant, suitable for mechanical parts such as gears.
- High carbon steel: This type is extremely hard and is used in cutting tools and blades.
Carbon steel stands out for its hardness, which makes it an ideal choice for applications that require it to withstand loads and mechanical wear. However, its low content of other elements makes it more susceptible to corrosion.
Stainless steel: Durability and corrosion resistance
Stainless steel is a steel alloy containing at least 10.5% chromium, which gives it extraordinary resistance to corrosion. This type of steel is essential in industries where the material is exposed to aggressive environments or chemicals.
Stainless steels are not only highly resistant to corrosion but also offer excellent durability. There are several types of stainless steel, including:
- Austenitic: This is the most common type of stainless steel, characterized by good corrosion resistance and high ductility. It is widely used in food processing equipment, refineries, and medical products. In the manufacture of components with this material, it is essential to comply with specific design and manufacturing standards, norms, and codes, which also include the rigorous inspection of austenitic stainless steel welds.
- Ferritic: Offers good hardness and is more economical than austenitic, used in automotive parts.
- Martensitic: It is harder and is used in cutting tools, although its resistance to corrosion is lower.
The following is a video courtesy of James Sword Engineering on “Types of steel: stainless steel vs. carbon steel”, as supplementary material to this article.
Factors affecting the strength, hardness, and durability of steel
The properties of steel, such as strength, hardness, and durability, are affected not only by the alloying elements, but also by the manufacturing processes. Here are some key factors:
- Alloy composition: The amount of carbon, chromium, nickel, and other elements plays a crucial role. A higher carbon content increases the hardness of the steel but also makes it more brittle. An example of an application for this type of material is in the manufacture of cutting tools, such as drills, industrial blades, and milling cutters.
- Heat treatments: Hardening and tempering are processes that improve strength and hardness. Proper heat treatment can make steel more resistant to wear and less prone to deformation.
- Manufacturing processes: Hot or cold rolling and welding can alter its properties, making it more suitable for certain applications.
Statistics in the development of steel alloys
Recent industry studies have shown that steel continues to be one of the most widely used materials in construction and heavy machinery manufacturing, with a projected 4.2% annual growth in the use of these alloys in sectors such as energy and automotive.
Additionally, new alloys, such as high entropy steels, are beginning to gain relevance. These combine multiple elements in equimolar proportions, showing 30% higher strength compared to conventional steels, although they are not yet widely available in commercial applications.
Industrial applications for alloys
Thanks to their versatility, the different alloys are used in a wide range of industrial applications. From construction to heavy machinery manufacturing, the properties of the alloy types allow their use in demanding environments where strength, toughness, and durability are essential.
- Construction: Carbon steels are widely used in the fabrication of beams and bridges because of their strength.
- Tool manufacturing: Cutting tools are manufactured from high-carbon steel because of its extreme hardness.
- Automotive industry: Engine components require durable and fatigue-resistant steels.
- Energy and petroleum: Stainless steel alloys are essential in corrosive environments and high temperatures. Hence, the manufacture of special alloy pipes for critical services.
Expert opinions on the impact of steel alloys
Metallurgy experts stress that the design of new alloy steels must balance strength, hardness, and ductility, since optimizing one property can compromise others. They also emphasize the importance of sustainability, promoting efficient processes and recyclable materials. An example of the application of these new alloy steels that balance strength, hardness, ductility, and sustainability is in the aerospace industry, particularly in the manufacture of aircraft structural components.
Future of Alloy Steels: Innovation and Sustainability
With technological advances and the growing demand for more efficient and sustainable materials, new alloys are evolving. Types of alloys are being developed that not only improve the mechanical properties of steel, but also reduce the environmental impact. One example of the application of these new alloys that improve the mechanical properties of steel and reduce environmental impact is in the construction of sustainable infrastructure, such as bridges and high-rise buildings.
Low-carbon alloys that maintain high strength and hardness are gaining popularity, as they minimize CO2 emissions during their manufacture. In addition, efforts are being made to recycle and reuse steel to reduce the consumption of natural resources. One example of the application of low-carbon alloys that maintain high strength and hardness is in the automotive industry, specifically in the manufacture of light vehicle bodies.
Conclusions
The impact of steel alloys on strength, toughness, and durability is undeniable. Proper selection of alloy types not only ensures optimum performance but also improves efficiency and extends service life in a wide range of industrial applications, from construction to machinery and specialized tooling.
Current research is focused on creating more sustainable steels, reducing environmental impact, and encouraging recycling. Thus, steel continues to be fundamental in the industry, driving innovations to meet the production and sustainability challenges of the future.
Learn about new developments in steel alloys and their impact on the design of industrial structures.