Selecting the right risk-based inspection methodology (IBR) or software for your organization is a critical process that requires consideration of several key factors. Choosing the appropriate IBR methodology must effectively evaluate the outcome of a time-based approach, thus allowing for continuous improvement of inspection tasks and mitigation measures.
It is essential that the selected IBR technological process is robust, reliable in evaluating the risk profile of active and potential damage mechanisms. To ensure process integrity, the IBR methodology and team study process must be clearly defined, auditable, and transparent.
The IBR software used must comply with industry standards, such as API RP 580/581, and must provide a comprehensive team study method.
How to choose the IBR methodology in the industry
In the context of a continually evolving industry, companies have the ability to select risk-based inspection software from vendors that offer a wide range of tools and functions to manage calculations, records and data.
Although the calculations necessary in IBR processes could be performed manually, this option is not feasible, especially when considering the extensive volume of assets present in a typical installation.
When selecting IBR software, it is essential to keep in mind that although most programs available in the market claim to comply with standards such as API RP 580/581, the superiority in terms of capabilities may vary between them. Given the complexity of this process, it is crucial that the team’s experts conduct a thorough technical assessment of how to choose the IBR methodology.
The risk-based inspection (IBR) methodology is used to identify and understand the risk and its component factors, as well as choose the IBR methodology to determine the phase of the life cycle in which the equipment is located.
Risk-based inspection can indicate whether assessments are required; However, this implies the availability of additional data that focuses on reducing the underlying uncertainties associated with risks related to the current and expected future state of the equipment.
In situations where the risk originates from the probability of failure (POF), the IBR must indicate other mitigation alternatives, such as replacement, repair or other actions that meet the established risk criteria.
The risk-based inspection (RBI) methodology can be used to prioritize inspection-related activities, usually through non-destructive testing (NDT), with the purpose of reducing uncertainties about the true damage status of the equipment and the factors that contribute to it.
The resulting inspection plan can detail the type and frequency of inspections of an asset. In addition to ECMs, additional risk mitigation activities identified through an IBR assessment could involve modifications to material of construction, installation of corrosion-resistant coatings, adjustments to operating conditions, application of corrosion-inhibiting chemicals. corrosion, among other actions.
Factors for choosing the IBR methodology
Asset integrity management (AIM) is becoming increasingly important, especially in the context of the trend towards long-term operation.
This involves a significant effort to mitigate risks as part of the pursuit of operational excellence and compliance with rigorous security standards.
Risk-based inspection (RBI) stands out as a fundamental AIM tool that enables risk minimization and cost optimization. Typically, IBR implementation is done through software capable of modeling variables and solving complex equations.
This software may be a legacy system developed in-house by the owner-user or one of the numerous products available on the market today.
International engineering standards and best practices play a crucial role in the description, approach and application of Risk Based Assessment (IBR). These standards include ASME PCC-3, Remapping, API 580 , API 581, API 571, among others.
Each of these standards applies to specific industry sectors, such as fixed pressure equipment (ASME), the oil and gas sector (API), and power plants. Importantly, these standards provide specialized guidelines and approaches for risk assessment in their respective sectors, contributing to the safety and reliability of industrial facilities.
Risk-based inspection methodology
In the current era of digitalization, the field of IBR methodologies and software covers a wide spectrum ranging from qualitative to quantitative approaches, including all variants in between. Organizations are currently seeking to discern the differences between qualitative and quantitative risk assessments in order to determine the most appropriate approach for their business structure.
In general, risk assessment methods are classified into:
- Qualitative (expert judgment).
- Semi-quantitative (rule-based analysis).
- Quantitative (probabilistic, statistical, mathematical model).
Several international engineering standards and recommended practices have been established to address the needs, approaches and application of risk-based inspection (RBI). These include ASME PCC-3, API 580, API 581, API 571, among others.
These standards are usually aimed at specific industry sectors. For example, ASME is a US standard applicable to stationary pressure-containing equipment, while API is also a US standard designed especially for the oil and gas sector.
Practitioners often face challenges when trying to distinguish between various recommended practices.
It is feasible for IBR software packages to adopt the best practices described in API 580 without necessarily implementing the associated methodology in API 581. Standards generally do not impose a single approach, such as a strictly quantitative one.
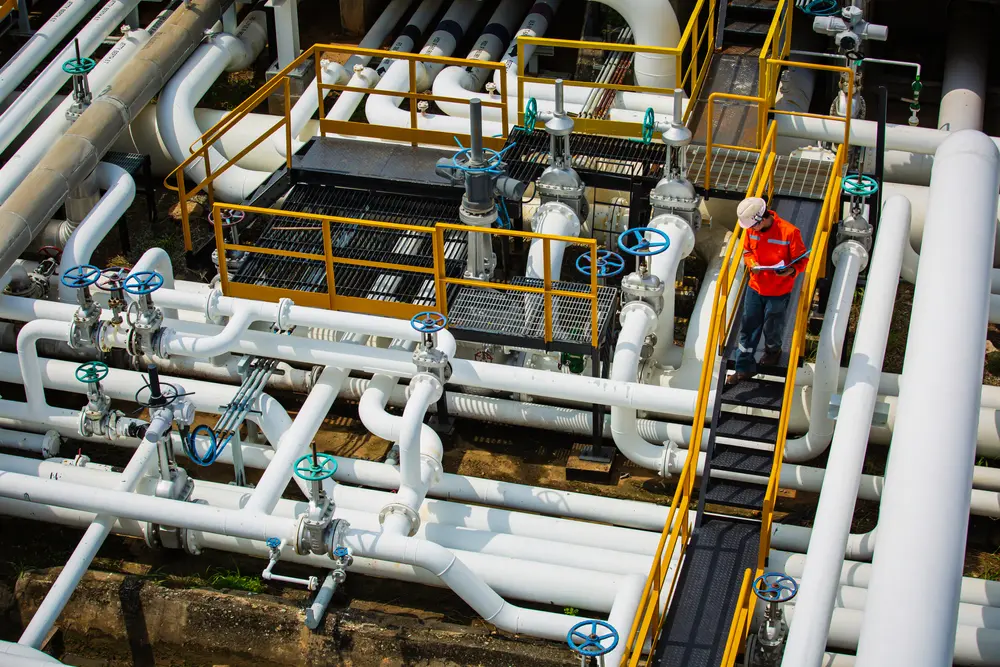
Importance of methodology and team study in IBR
It is of utmost importance that the IBR team’s methodology and study approach are reliable, transparent, auditable, detailed, user-friendly and properly documented.
To ensure compliance with API 580, the software must incorporate an IBR methodology that is understandable and familiar to plant and operations inspection engineers.
Failure to do so could result in increased risk to the team rather than reduced risk. Additionally, the IBR technology method (Level 1, Level 2, or Level 3) must be robust and capable of evaluating the failure probability and risk profiles of all applicable degradation and failure modes.
In the context of risk assessments, precision depends on the analysis methodology, data quality, and consistency of execution, while accuracy is determined by the metrics and computational methods selected.
It is essential to proceed with caution, as a result may be highly accurate, but if there is a significant amount of uncertainty in the probabilities and consequences, the result may still be inaccurate.
Approach | Advantages | Disadvantages |
Qualitative | Ease of use and transparency in the methodology | Less precision and accuracy in risk assessment |
Quantitative | Greater precision and accuracy in risk assessment | Greater complexity in implementation |
It is crucial to consider that, while the quantitative approach can offer greater precision in risk assessment, it also implies greater complexity in its implementation. On the other hand, the qualitative approach stands out for its ease of use and transparency, although it may present limitations in terms of precision and accuracy in risk assessment.
Thoroughly evaluating all the IBR software options available on the market involves a considerable investment of precious time and resources. The methodology presented in this article aims to reduce the extensive set of options to focus on a limited list, aligned with the company’s objectives.
For example, the objective of how to choose the IBR methodology and improve compliance may imply the need to comply with a specific standard or code.
Conclusions
When beginning an IBR program, common challenges are faced such as collecting and organizing the data necessary to conduct an accurate evaluation. The complexity of this effort will vary depending on the organization’s specific data load. It is essential to have a team of qualified professionals who have the necessary experience to carry out accurate assessments.
Given the commitment of time, resources and the iterative nature of the IBR process, it is crucial to employ software with the ability to effectively store, document and report on analyses, results and recommendations.
The immediate cost savings benefits of adopting risk-based inspection (RBI) for asset integrity management are driving its adoption. The ability to intelligently assess the probability of failure (POF) relative to the consequences of failure (COF) makes IBR the most prudent approach to managing critical assets.
It offers a structured, systematic and technically-defensible framework for decision making, significantly reducing equipment failures and reducing the probability of unplanned stops by more than 50%.
When using quantitative risk-based inspection methodology to assess the probability of failure and its consequences, regulated parties may choose to define the leak hole size in accordance with API RP 581, or an equivalent reference standard. or higher, with the purpose of simulating the possible consequences and quantifying the risk precisely.
References
- https://inspectioneering.com/journal/2017-10-26/7018/best-practices-for-implementing-a-risk-based-inspection-rbi-prog
- www.ndt.net/article/mendt2009/papers
- www.trinity-bridge.com/knowledge-center/blog/10-steps-to-choosing-rbi-program
- www.linkedin.com/pulse/risk-based-inspection-methodology-qualitative-quantitative-everything