Table of Contents
Contents
It is to reflect!
In the first part of this sequence of articles, reference is made to the accidents that have occurred since 2016, but in the recent year 2018, at least 6 related explosions were reported, with boilers (Figure 1), which again left 10 human losses and more than 40 injured, among these there were 13 children who attended a nearby school.
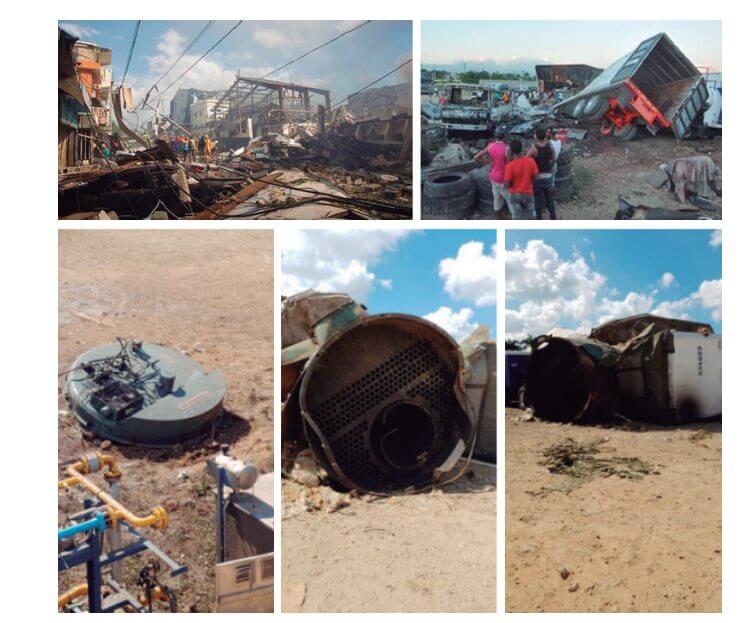
Among the press reports, it can be read, from the interviewees of the facilities, statements such as the following:
“All this was something unexpected, we thought it was like an incident of another person, but it was work and, from one moment to the next, two people died…”
“…according to unofficial sources it was learned that during Easter the company was the protagonist of a similar scenario of which they did not give more details, but that preamble could have been what triggered this explosion. (…) It will be the pertinent organisms that determine
What was the cause of the work accident?
In that way? An accident involving a boiler that is properly operated, in which key parameters are monitored, in which the operators “listen to what it is saying”, inspected and maintained by trained personnel, cannot have unexpected events! Why was action not taken at the time of the event that had already occurred? What was the boiler saying? What are we not doing?
Boilers say what they need. If we take and record the appropriate operational parameter readings, the boiler will show trends. Based on the history of operations – events, maintenance, failures and repairs, the scope of inspections and maintenance must be planned, so it is worth asking ourselves: To what extent is our staff trained to know how to listen to what the boiler says? ?
Maintenance was done on the boiler. What was this maintenance based on? What was the scope? Why was the problem that had manifested itself not resolved? Did the accident really have
what to do with the previous event?
In one of the reported events, the explosion occurred in a steam pipe associated with a new boiler that was replacing another that had been removed. In most of the Latin American regulations, the inspections are limited to the evaluation of the boilers and in very few they ask for the evaluation of the associated pipes, knowing that the condensate and feed water pipes can suffer severe corrosion damage and the steam pipes In addition to possible corrosion damage, they can age along with the boiler itself, also due to overheating. What gives us the certainty that this will not happen in our installation?
Is there a regulation for the use of boilers in your country? Do you know him?
In the first part, reference was made to inspections to guarantee reliability and mechanical integrity and to the standards and codes on which they could be based. When you have to define the scope of frequent or routine maintenance, both for the mechanical structure of the boiler itself, its auxiliary equipment and all the instrumentation and controls that guarantee its reliable, efficient and safe operation, you can find a very good guide in Section VII of the ASME Code (the new edition is coming in 2019) in Appendix “A” Non-Mandatory – Maintenance Examination Checklist, where the needs for the different types of boilers are discerned:
Article A-100 Procedures for the Care and Maintenance of Package Type Boilers.
Article A-101 Maintenance Verifications for Gas, Oil or Solid Fuel Aquatube Boilers.
Article A-102 Operational Verifications related to Maintenance for Aquatube Boilers.
Article A-103 Maintenance Verifications for Firetube Boilers.
Article A-104 Operational Verifications related to Maintenance for Firetube Boilers.
It is very important that the maintenance plan is based on several considerations such as boiler operation time, reported failures, observations in the last inspection, needs pending maintenance that have not been completed or covered in the previous maintenance; but it is definitely essential that the maintenance personnel, the planner, receive the requirements and observations of behavior of the boilers observed and recorded by the operating personnel. To which it is worth asking: Do the operators take frequent readings of the key parameters of the boilers and auxiliary equipment that allow for deterioration trends, guarantees of their good and safe operation and give the alarm voice when these values begin to move away from the control parameters established for the design of each boiler in particular?
When focusing on the instruments and control-safety system, is the service and calibration of the measurement and control instruments being considered? Maintenance staff (instrumentation
and electricity) must handle the requirements of the NFPA 85 or ASME CSD 1 Codes (depending on the capacity of the boiler) and ensure that due to operational requirements to keep the boilers running (improper fixes – bypasses) or modifications made in previous maintenance due to ignorance of these codes, the boiler is not in an unsafe condition that could cause a serious disaster.
The importance of guaranteeing the proper functioning of the supervision, control and actuation of the alarms and trips due to the level of water inside the boiler and protection to overpressures. Maintenance personnel should check to ensure that the instrumentation conforms to the requirements of the Codes and the boiler manufacturer. The codes usually indicate how often these checks should be made, if the local regulation does not indicate it or if there is no regulation on the use of boilers.
In the case of verification of pressure relief valves (safety valves), the specific precautions for these devices must be found in the National Board Inspection Code at its Part 4 “Pressure Relief Devices” and in Part 1 “Installation”, following the observation that no changes have been made against the code due to loss of the nameplate of the valves, carelessness in identifying the valves that are handled in the maintenance workshop, not having the appropriate valves in the plant or in the local market when replacing it, or due to ignorance that there are valves for gas, liquid and steam service, the requirements regarding the steam discharge capacity, where it must be verified that the pressure relief valve or valves installed in the boiler have the capacity to evacuate all the steam produced by the boiler at its maximum capacity production; and/or installation care, such as not having blocking valves between the boiler and the safety valve, reductions at the inlet and outlet of the valve and the characteristics of the steam discharge. (Figures 2).
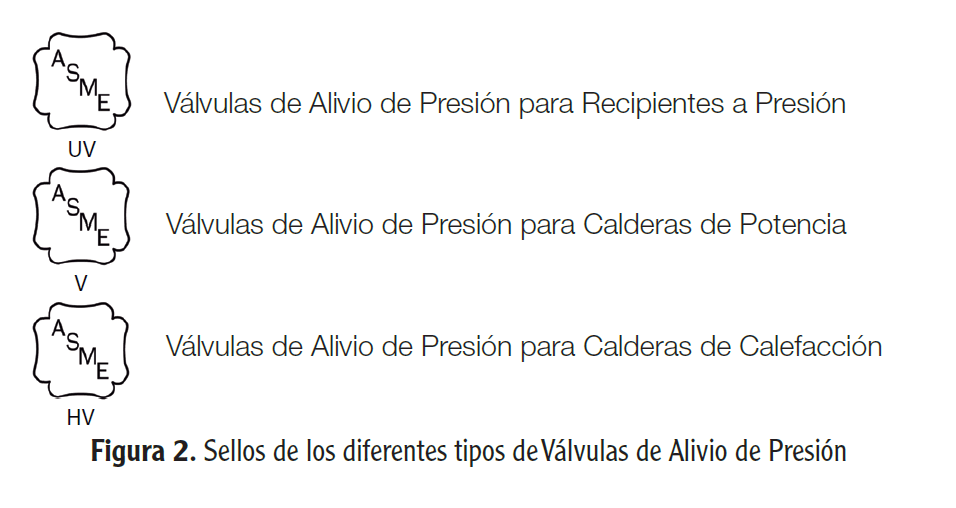
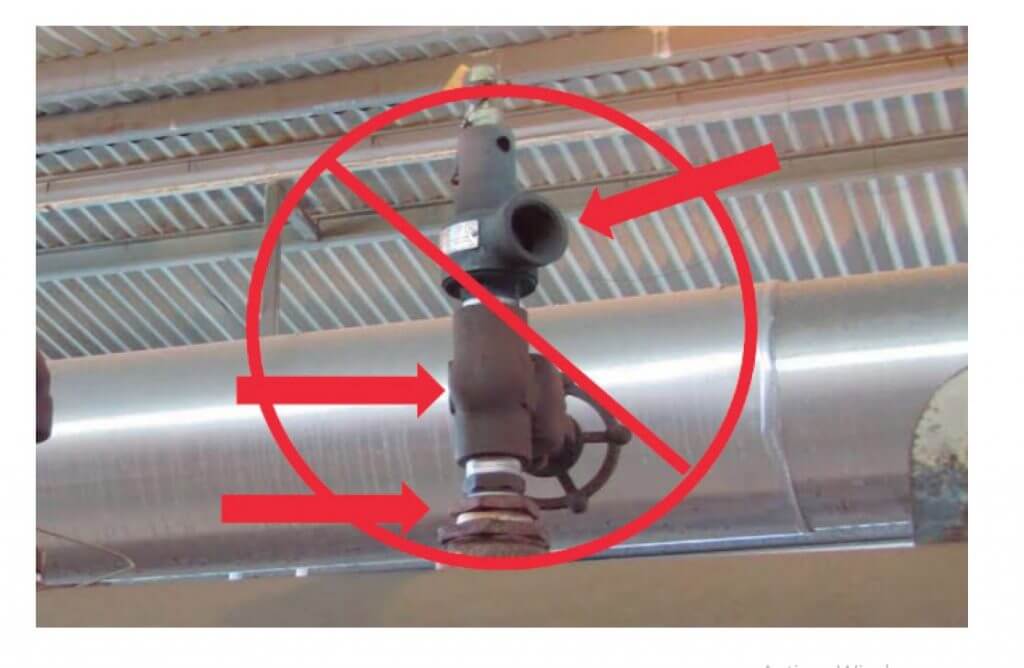
For a boiler like the following example in figure 4, with 750 square feet of heating surface and a maximum evaporation capacity of 5,175 lb/hour at maximum working pressure
admissible pressure of 150 psi, to which the image in figure 3 also corresponds, when the ASME Code in its Section I “Construction Rules for Power Boilers” (note: do not use Section VIII “Construction Rules for Pressure Vessels ” when a boiler is being evaluated) and Part 1 “Installation” of the National Board Inspection Code state that:
• A boiler with more than 500 square feet of surface area
heater must have two or more pressure relief valves and
what’s more,
• The discharge capacity of the pressure relief valve(s)
for each boiler it must be such that they dislodge all the steam
that can be generated in the boiler (it must not be less than the
maximum designed steam production capacity at MAWP
of the boiler),
• One or more pressure relief valves, in the boiler itself,
must be regulated to the maximum admissible working pressure or by
below this.
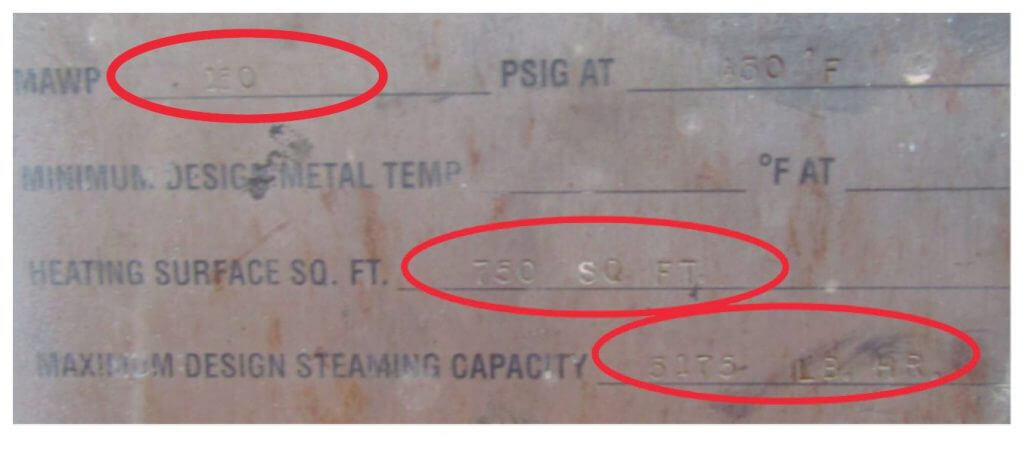
In this case, it may not be acceptable to have a single pressure relief valve, to be used in pressure vessel service, which is not able to dislodge all the steam produced and with a pressure
200 psi setting as shown in Figure 5.
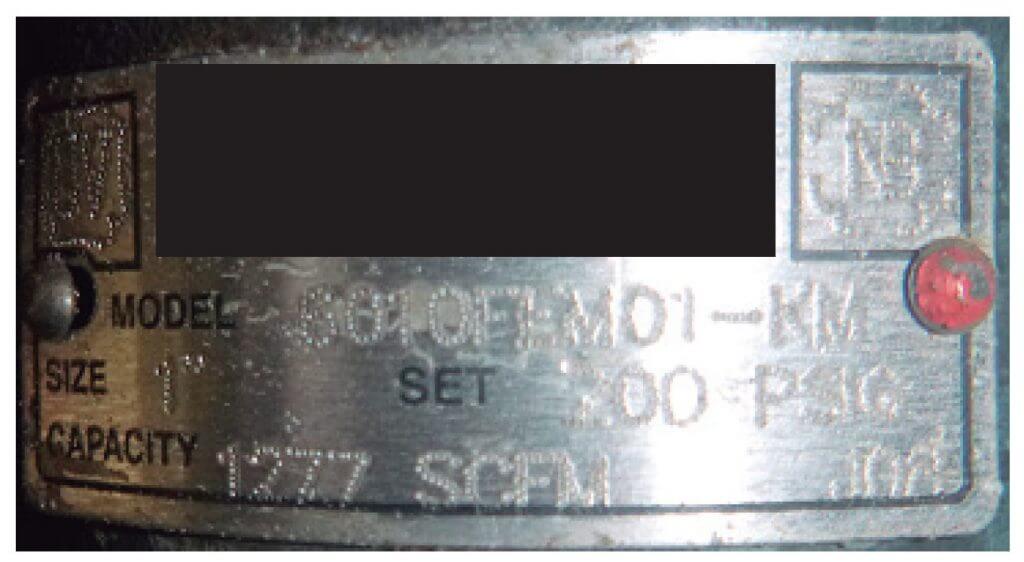
which is a UV valve for pressure vessels, set at 200 psi.
It is worth asking since when the boiler could be under an unsafe condition such as the one that could be found and possibly someone will answer that “it came like that from the factory”, so you must have the manufacturer’s manual, not a commercial brochure of that model of boiler. boiler. If the manufacturer’s manual does not exist, it must be requested by referring to the manufacturer’s serial or contract number printed on the boiler nameplate. In the meantime, it is highly recommended that maintenance personnel educate themselves on the requirements of the above codes.
Conclusion
Maintenance planning should be based on the boiler model and its years of operation, the manufacturer’s recommendations and Section VII of the ASME Code and requirements of the National Board Code and NFPA 85, and the results of inspections, but especially in the analysis of the trends of the critical operational parameters of the boilers, which the operators must record in each shift; because remember that the boilers say what they need and you should never accept or allow an accident to take you by surprise.
References
Own source.