Table of Contents
- Introduction
- Technological Improvements Brought by Industrial Robots Industrial
- Benefits of AI in industrial robotics
- Comparison between traditional robots and AI robots
- Application cases
- Practical applications of AI in industrial robotics
- Challenges and considerations in implementing AI in robotics
- Future Impact of AI on Industrial Robotics
- Enhanced Adaptability in Changing Environments
- Conclusions
- References
Introduction
The fusion of artificial intelligence (AI) and industrial robotics is generating a significant transformation in the manufacturing sector and other key areas. Thanks to AI, robots can not only perform pre-programmed tasks but also can learn, adapt and optimize their operations in real time, ushering in a new era of intelligent automation.
In manufacturing, AI-equipped robots are elevating precision in activities such as assembly, quality control, and logistics, enabling continuous operation and unprecedented efficiency. These advances make it easier for collaborative robots (cobots) to work alongside humans, providing greater flexibility and reducing costs, which is especially beneficial for small and medium-sized enterprises.
In addition, AI has boosted the perception and decision-making capabilities of robots, enabling them to adapt quickly to changes in their environment without the need for constant reprogramming. For example, machine vision-enabled cobots can identify objects and adjust their orientation during operations, improving both accuracy and safety in the workplace.
In logistics, AI has transformed the ability of mobile robots to navigate autonomously in complex environments, avoiding obstacles and optimizing routes, resulting in increased productivity and reduced downtime. These advances are also helping industries become more sustainable, minimizing waste and optimizing energy use in factories.
Industrial robots have transformed the manufacturing industry by bringing in a range of technological advancements that boost both efficiency and innovation. They enhance precision and accuracy in complex assembly tasks while automating repetitive and dangerous jobs, establishing new benchmarks for productivity and workplace safety. Moreover, the incorporation of IoT and AI into robotics has facilitated smarter operations, allowing for predictive maintenance and smooth communication between systems. These enhancements not only streamline industrial processes but also pave the way for sustainable practices and better resource management, making industrial robots essential to contemporary manufacturing.
Technological Improvements Brought by Industrial Robots Industrial
Industrial robots have introduced a range of transformative technological advancements that have changed the landscape of various industries. Below, we delve deeper into each of these improvements. Robots have made notable contributions across different sectors. Here’s a more detailed examination of these advancements, along with some ai in robotics example:
- Precision and Accuracy
Industrial robots execute tasks with remarkable precision, achieving results that are often beyond human capability. For instance: In the automotive sector, robotic arms are utilized for spot welding and painting, ensuring a consistent application and minimizing waste. In electronics manufacturing, robots assemble microchips and solder tiny components with high accuracy, leading to fewer defects in devices like smartphones and laptops.
- Automation of Repetitive Tasks
Robots are particularly effective at automating tasks that require consistent repetition, which enhances efficiency and reduces worker fatigue. Some examples include: In food packaging, robots sort, pack, and label products at speeds that far surpass human abilities. For example, robots in beverage factories can fill and seal hundreds of bottles every minute. In logistics, companies like Amazon use robots to retrieve and sort items in warehouses, improving inventory management and speeding up delivery times.
- Improved Workplace Safety
Robots take on hazardous tasks, creating a safer work environment for employees. Examples include: In chemical plants, robots manage dangerous materials, such as mixing volatile compounds, without endangering human health. In mining, autonomous robots navigate unstable tunnels to extract minerals, safeguarding workers from potential collapses. In construction, demolition robots work in areas with high debris risks, minimizing exposure to falling objects.
- Resource Efficiency
Robots assist industries in reducing waste and optimizing the use of raw materials and energy. Examples include: In textile manufacturing, robotic cutters optimize fabric layouts to minimize scraps, which decreases waste and saves costs. In agriculture, precision farming robots assess soil conditions and apply fertilizers or water as needed.
Benefits of AI in industrial robotics
Improved efficiency and productivity
Artificial Intelligence (AI) has been instrumental in increasing efficiency in manufacturing and industrial production. Together with industrial robotics, AI optimizes repetitive and high-precision tasks, allowing robots to perform work autonomously, without requiring constant human supervision. According to Duplostock, incorporating AI into industrial robots allows them to analyze data and adjust their movements in real time, which improves efficiency and reduces downtime on production lines.
For example, in factories operating under the Industry 4.0 model, AI-equipped robots can make automatic adjustments according to changing conditions in the work environment, such as detecting equipment failures or variations in assembled parts. This not only increases productivity but also optimizes the use of resources and minimizes waste. In sectors such as manufacturing, AI has facilitated significant improvements by enabling the scheduling of complex tasks without the need to stop production for manual adjustments.
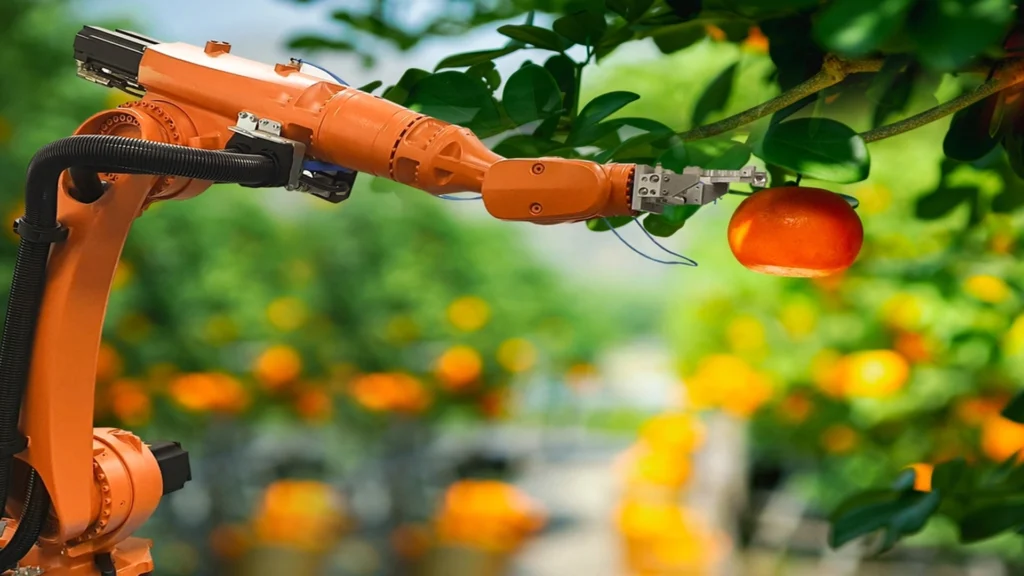
Error reduction and quality improvement
Another important benefit of AI in industrial robotics is the reduction of human error and improvement in final product quality. AI-equipped robots can carry out automatic quality inspections at every stage of production, allowing defects to be identified early and preventing defective products from progressing through the supply chain.
According to Telefónica, these robots can automatically adjust their operations by recognizing patterns in the data collected, allowing them to correct potential errors before they impact final product quality. This level of automation has proven especially useful in sectors that require a high degree of precision, such as electronics and automotive.
AI allows collaborative robots, or cobots, to modify their force and direction during delicate tasks such as welding or small component assembly, ensuring greater accuracy and reducing costs related to rework and returns. In conclusion, the automation of complex processes through AI in industrial robotics not only ensures greater consistency in product quality but also improves safety and operational efficiency.
Comparison between traditional robots and AI robots
Differences in capabilities and applications
The main difference between traditional robots and robots using Artificial Intelligence (AI) is their ability to adapt and make decisions. Traditional robots are programmed to perform specific tasks, executing them repetitively and unable to adapt to unexpected changes in their environment.
This makes them very effective tools for linear and standardized production processes, such as assembly or welding, where variability and real-time decisions are not needed. In contrast, AI robots in industrial robotics, thanks to their machine learning ability, can analyze large amounts of data in real time and adjust to new conditions without requiring manual reprogramming.
This enables them to make decisions autonomously and perform more complex tasks, such as quality inspection, warehouse logistics, or parts assembly with high precision. A clear example of the competitive advantage of AI-enabled robots is their ability to optimize factory workflow by autonomously navigating and dynamically adjusting their functions based on the data they collect.
Application cases
A clear example of these differences can be seen in collaborative robotics. Unlike traditional robots, which require rigorous programming and often operate in isolation, artificially intelligent robots can work alongside humans, sharing spaces and adjusting their actions based on interactions with operators.
In the logistics field, for example, AI-equipped robots are capable of managing inventories and planning routes autonomously, optimizing the distribution of products in large warehouses without the need for constant supervision by a human operator.
While traditional robots are effective for repetitive and defined tasks, AI-enabled robots provide greater flexibility, adaptability, and the ability to make decisions independently, giving them a considerable competitive advantage in production environments that are dynamic and complex.
Practical applications of AI in industrial robotics
Advanced manufacturing automation
Artificial intelligence (AI) has significantly changed automation in manufacturing, enabling industrial robots to perform tasks that previously required constant human intervention. This ranges from complex assembly processes to real-time quality inspection, improving both productivity and operational efficiency.
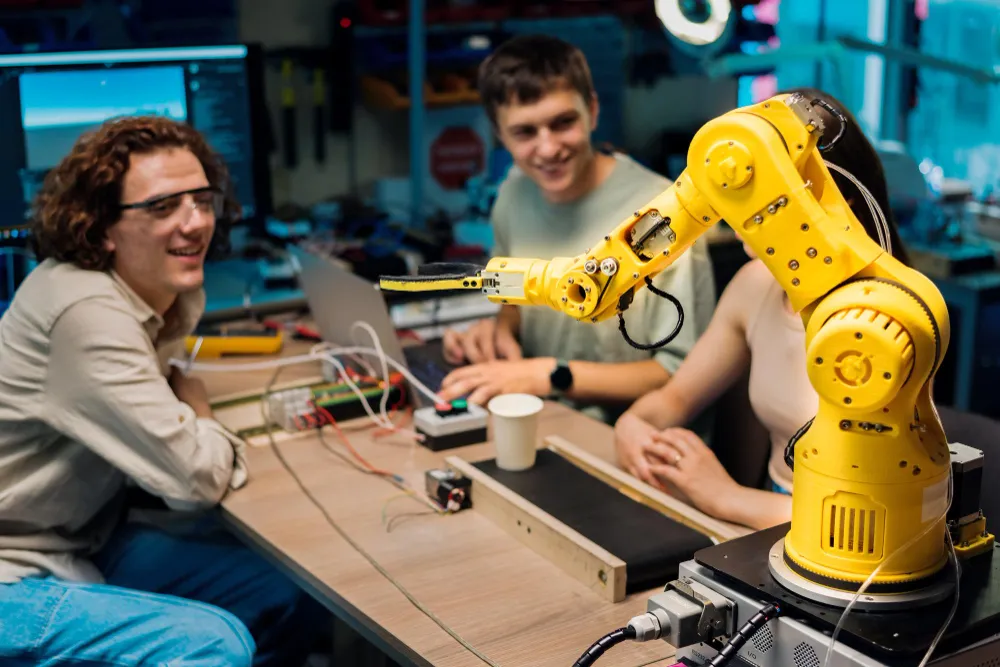
Thanks to AI, robots can analyze data and make decisions autonomously, decreasing downtime and increasing accuracy in tasks that were previously done manually.
For example, in the manufacturing industry, AI-equipped robots are able to assemble parts with high precision and adjust their movements based on real-time data analysis. This not only speeds up production but also raises the quality of the final product. In processes such as the assembly of electronic devices, where very small components are handled, the ability of robots to make automatic adjustments considerably reduces the possibility of errors.
In industries such as automotive, AI has facilitated the integration of advanced vision and machine learning systems into collaborative robots, which can now perform tasks such as precision welding or component assembly under varying conditions, without the need for constant reprogramming. The ability of robots to learn and adapt has revolutionized factories, making them more flexible and productive.
Application cases
A clear example of these industrial robotics capabilities can be seen in factories that use collaborative robotics systems (cobots). Equipped with artificial intelligence, these robots are able to work alongside human operators, adapting dynamically to environmental conditions.
In a traditional assembly line, a robot would require reprogramming to adjust to new products; however, thanks to AI, cobots can automatically switch tasks and handle different products in the same production cycle, greatly improving operational flexibility.
Advanced automation through artificial intelligence not only optimizes complex industrial processes but also enables factories to operate more flexibly and efficiently, eliminating the need for human intervention in many repetitive tasks and improving quality control.
Challenges and considerations in implementing AI in robotics
Technical and ethical challenges
The incorporation of artificial intelligence (AI) into industrial robotics presents several challenges, both technical and ethical. From the technical point of view, one of the main obstacles is the difficulty of creating AI systems that are robust and reliable in industrial environments that are dynamic and changing.
Robots using AI need large volumes of data to be trained effectively and improve their decision-making capabilities. In addition, the integration of industrial robotics with connectivity and real-time processing of this data creates challenges in terms of the infrastructure needed to support advanced automation.
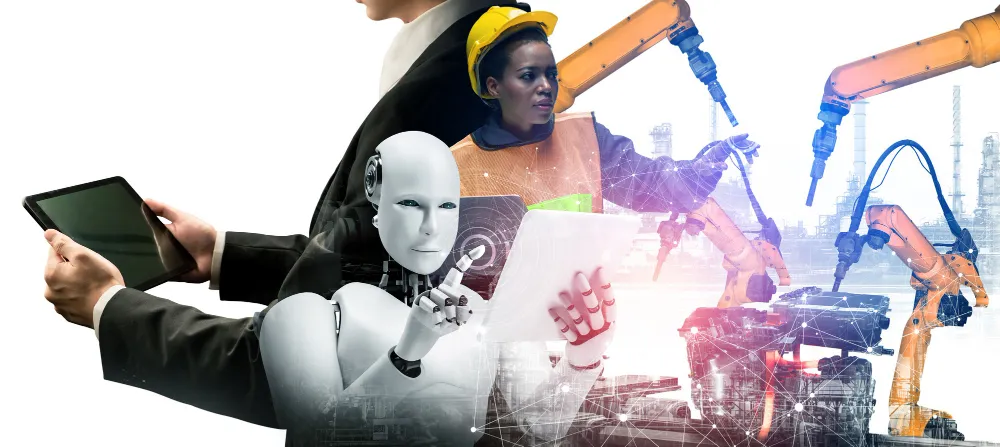
Another major technical challenge is safety. The implementation of AI robots operating autonomously in environments where human workers are also present requires sophisticated solutions to prevent accidents. AI systems must be able to detect and react to unexpected changes in the environment, such as the presence of people or machine faults. Although technologies such as machine vision already exist to help improve safety, it remains a challenge to ensure that these robots are completely safe and do not pose a danger.
From an ethical perspective, the introduction of AI in industrial robotics also raises questions about liability and automated decision-making. For example, if an AI robot makes a mistake that causes damage or injury, who assumes liability – the robot manufacturer, the programmer of the algorithm, or the company using the robot? This is an issue that is constantly discussed in the field of AI, as technology advances faster than industry regulations and standards.
The impact on employment is an important ethical issue to consider. Advanced automation may displace workers in sectors that traditionally rely on unskilled labor. While AI proponents argue that new jobs will emerge in areas such as robot maintenance and data analysis, the transition could be complicated for many workers who lack the skills necessary to adapt to these new roles. Safety and liability considerations: Safety is a critical aspect of implementing AI-enabled robots in industrial settings.
As robots take on more complex tasks and integrate with human workers, more sophisticated safety systems become necessary. Robots must be equipped with sensors and learning algorithms that enable them to react quickly to unexpected hazards or human error. For example, collaborative robots are designed to stop immediately if they detect the presence of a person too close, but it is crucial to ensure that these systems work seamlessly to avoid accidents.
In addition, accountability in autonomous decision-making represents another significant challenge. AI can make data-driven decisions, but it cannot always assess the full ethical or legal implications of those decisions. In this regard, it is critical that policymakers and businesses collaborate to develop ethical and regulatory frameworks to guide the use of AI in industry, ensuring that robots operate not only efficiently, but also safely and ethically.
Future Impact of AI on Industrial Robotics
The future of artificial intelligence (AI) in industrial robotics is poised to further revolutionize the operational and evolutionary dynamics of industries. As these technologies progress, they are anticipated to redefine the boundaries of automation and the intelligence of robotic systems.
More Intelligent Autonomous Robots
With the advancement of deep learning algorithms and neural networks, future industrial robots will be capable of making autonomous decisions in real-time. This capability will enable them to adapt to unforeseen circumstances, such as changes in the supply chain or variations in materials, without requiring human intervention. For instance, a robot on an assembly line could automatically detect and rectify a production error.
Enhanced Human-Robot Collaboration (Cobots)
AI will continue to enhance the interaction between robots and humans, fostering the development of safer and more efficient collaborative systems. Future cobots will be better equipped to interpret gestures, voice commands, and human behaviors, facilitating smoother integration in shared work environments. This will be particularly beneficial in sectors such as healthcare and logistics, where robots can serve as extensions of the human workforce.
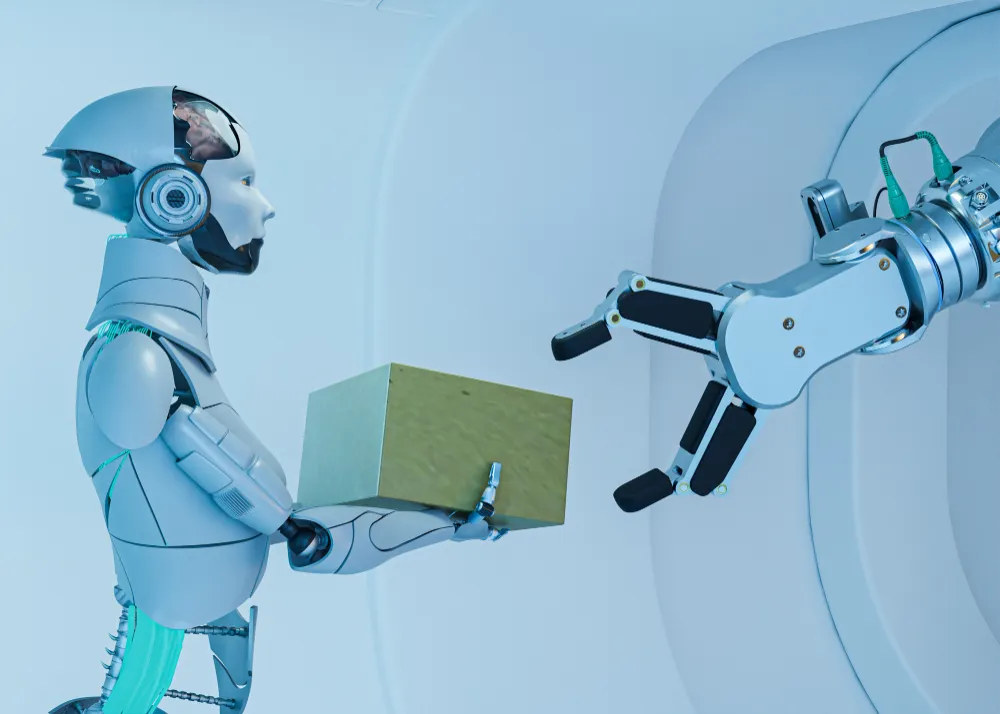
Data-Driven Automation
The extensive collection and analysis of data will enable robots to anticipate production needs with greater accuracy. For example, in smart factories, robots will leverage historical data to forecast product demand, optimize processes, and minimize waste. This approach will not only enhance efficiency but also contribute to industrial sustainability.
Integration with the Metaverse and Digital Simulations
The integration of artificial intelligence in industrial robotics will significantly benefit from its connection to the metaverse, facilitating advanced simulations and the creation of virtual testing environments. Prior to executing a new design or process, robots will be able to simulate their operations within a digital twin, aiding in the identification of potential issues and the optimization of outcomes before real-world implementation.
Contribution to Sustainability
The development of more efficient robots, coupled with optimization driven by artificial intelligence, will enable industries to reduce energy consumption and lessen their environmental impact. From efficient resource management to the establishment of automated recycling processes, industrial robotics will play a crucial role in achieving global sustainability objectives.
Expansion into New Industries
Industrial robotics is beginning to extend beyond traditional sectors such as manufacturing and automotive, moving into areas such as:
Agriculture: AI-powered robots will be able to monitor crop growth, apply fertilizers with precision, and predict agricultural yields based on meteorological data.
Renewable Energy: Intelligent robots will assist in the installation and maintenance of infrastructures like solar panels and wind turbines, thereby maximizing the efficiency of these technologies.
Healthcare: Medical robotics will leverage advanced AI to perform complex surgeries, automate diagnostic processes, and tailor treatments for patients.
Enhanced Adaptability in Changing Environments
In the future, robots will be more versatile, allowing them to quickly adapt to changes in their work environment or production conditions. For example, in the construction industry, robots will adjust their processes in real-time to respond to variations in materials, terrain, or weather. This level of adaptability will lead to greater flexibility and efficiency in industries that often face significant fluctuations.
Utilization of Neural Networks for Complex Decision-Making Sophisticated neural networks will enable robots to perform complex analyses and make independent decisions in situations with multiple variables. For instance: In inventory management, a robot will accurately predict demand and adjust production flow accordingly. In quality control, a robot will detect patterns in manufacturing defects and make necessary adjustments before problems affect large-scale production.
Conclusions
The incorporation of artificial intelligence in industrial robotics is transforming the automation landscape, moving robots beyond preprogrammed tasks to a constantly learning and adaptive approach. Advances in sensing, monitoring, and machine learning technologies have dramatically improved the efficiency, accuracy, and flexibility of industrial robots. They are able to make autonomous decisions, optimize processes in real time, and collaborate safely with humans in a variety of work environments.
In addition to revolutionizing productivity in factories and logistics chains, AI in industrial robotics is also promoting sustainability by reducing energy consumption and minimizing waste. This collaborative and automated approach is emerging as a key driver in the transition to a more efficient, flexible, and environmentally friendly industry.
Artificial intelligence-driven robotics is not only changing the way goods are produced, but is also redefining the future of work, safety, and sustainability in global industry. This conclusion reflects a strategic and professional perspective on the impact of AI on industrial robotics, highlighting its importance both now and in the future.
References
- https://robotnik.eu/es/la-inteligencia-artificial-en-la-robotica/
- https://www.universal-robots.com/es/blog/aplicaciones-inteligencia-artificial-produccion/
- https://duplostock.com/robotica-industrial-y-colaborativa-en-la-fabricacion/s/industry-5-0.html
- https://www.telefonica.com/es/sala-comunicacion/blog/usos-y-aplicaciones-de-la-inteligencia-artificial-en-robotica
- https://metaverso.pro/blog/futuro-de-la-inteligencia-artificial-y-robotica-una-nueva-era-de-innovacion/