Table of Contents
- Main factors affecting heat pump maintenance efficiency
- A heat pump with a high Coefficient of Performance (COP) offers several significant benefits
- Maintenance strategy with advanced monitoring and optimization of energy performance
- Preliminary analysis to establish the strategy
- Elements to implement for heat pump maintenance
- How does scheduled maintenance influence the efficiency of a heat pump?
- Correct operation of heat pumps
- Conclusions
- References
Heat pumps are high-efficiency thermal systems designed to provide heating and cooling by transferring thermal energy between two spaces, rather than generating heat directly through combustion processes. A prominent feature in the maintenance of heat pumps is that they do not require the combustion of fossil fuels to generate heat, making them a more sustainable and energy-efficient alternative.
Its operating principle is based on a thermodynamic cycle that allows heat to be moved from a lower temperature environment to a higher temperature environment, or vice versa, using a relatively low amount of electrical energy as an external source.
This type of rotating equipment operates by transferring thermal energy from one or more cold environments to warmer areas, even under simultaneous conditions, counteracting the natural flow of heat. To achieve this, heat pumps extract heat from a space with lower thermal energy and transfer it to a space with higher temperature. This process is made possible through the use of a mechanical system driven by an external energy source.
In addition, their implementation contributes significantly to the reduction of greenhouse gas emissions in various industrial applications, since they do not depend on processes that involve the direct burning of energy resources.
Main factors affecting heat pump maintenance efficiency
- External temperature: The operating efficiency of a heat pump is directly related to the difference between the temperature of the thermal source and the temperature of the working fluid. The smaller this difference, the higher the efficiency. During winter, when outdoor temperatures drop significantly, the efficiency of the heat pump tends to be reduced due to the increased effort required to extract heat from the cold environment.
- System design: Optimal thermal system design is essential to maximize the performance of a heat pump. This includes accurate sizing of the equipment and efficient thermal distribution to meet the energy needs of the space with minimum resource consumption.
- Insulation and ductwork: Proper thermal insulation in the building, along with an airtight and leak-free duct system, is crucial for retaining the desired internal temperature for extended periods. This reduces the operating load on the heat pump, improving both its efficiency and service life.
- Maintenance: Periodic preventive maintenance is essential to ensure that heat pump maintenance operates at high levels of efficiency over time. This includes technical inspections, component cleaning and necessary system adjustments.
- Control and configuration: Implementing advanced control and regulation systems is key to optimizing the performance of a heat pump. Correctly adjusting the heating curve and adapting the operation to external climatic conditions maximizes its energy efficiency.
- Water quality: In regions where the water used in the system contains high levels of impurities or minerals (hard water), thermal performance may be adversely affected due to build-up of deposits on the heat exchangers or internal corrosion.
- Specific pump speed: The specific speed of the compressor or pump directly influences the overall system performance. A properly adjusted speed ensures a balance between energy efficiency and operating capacity.
- System components: The overall efficiency of the system depends to a large extent on the individual performance of its main components, such as the compressor, heat exchangers and expansion valves. The quality and technical design of these elements are determinant to achieve a high Coefficient of Performance (COP).
- Distribution system temperature: Operating temperatures within the distribution system (whether for heating or cooling) have a direct impact on the Coefficient of Performance (COP) and total thermal capacity of the equipment. Systems operating at lower temperatures tend to be more efficient.
- SEER Rating: The Seasonal Energy Efficiency Ratio (SEER) is a key indicator that evaluates the average annual energy performance of a heat pump under different climatic conditions. A higher SEER value reflects a higher overall energy efficiency of the system.
A heat pump with a high Coefficient of Performance (COP) offers several significant benefits
- Higher energy efficiency: A high COP indicates that the heat pump produces more thermal energy for each unit of electrical energy consumed.
- Economic savings: By being more efficient, a heat pump with a high COP reduces operating costs and electricity bills.
- Better performance: A high COP (between 3 and 3.5 for air source heat pumps) indicates a highly efficient system, capable of providing more heating or cooling with less electricity consumption.
- Lower environmental impact: By consuming less energy to operate, these heat pumps contribute to the reduction of CO2 emissions and global warming.
ElectraTherm’s patented technology enables the sustainable production of emission-free and fuel-free electricity.
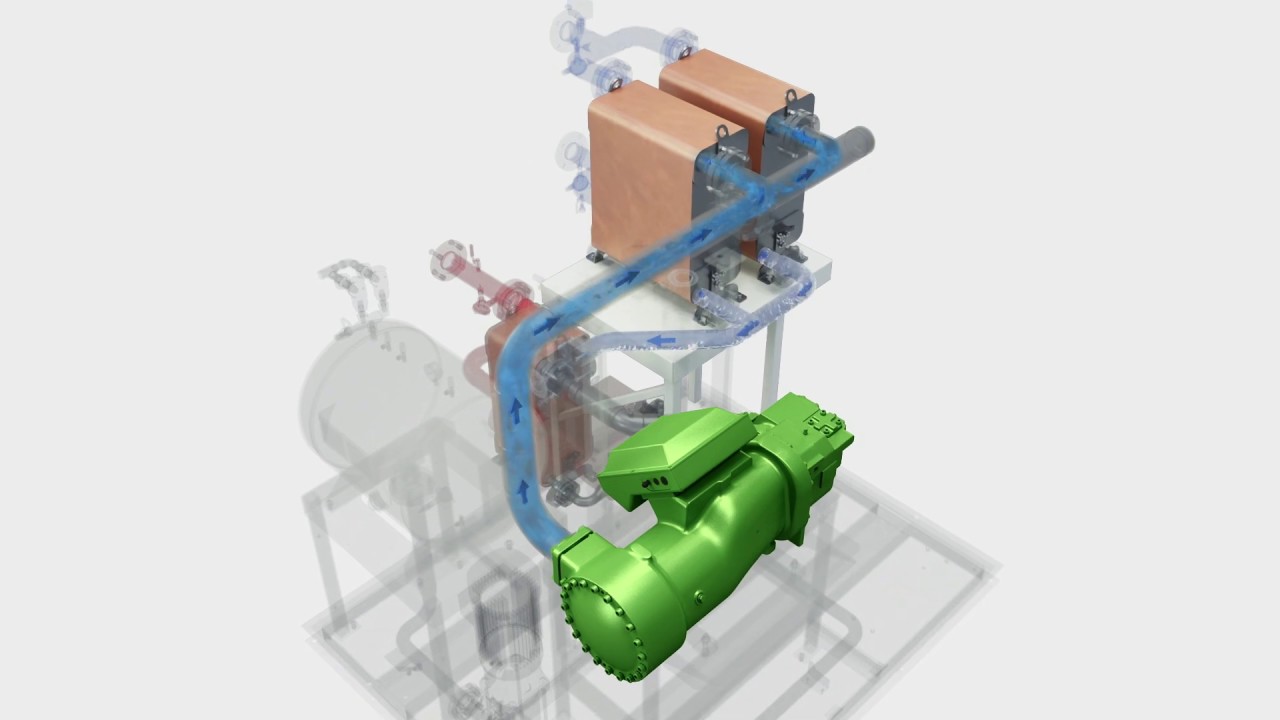
Sustainable electricity production system.
A high COP, therefore, not only benefits the user in terms of savings and comfort, but also contributes to overall energy efficiency and environmental sustainability.
Maintenance strategy with advanced monitoring and optimization of energy performance
To develop an effective industrial heat pump maintenance strategy, it is key to combine advanced monitoring and energy efficiency optimization.
Advanced monitoring
- IoT and SCADA sensors: Implement smart sensors to measure temperature, pressure, flow and power consumption in real time.
- Vibration and ultrasound analysis: Detect wear on compressor and fan components before critical failures occur.
- Infrared thermography: Identify high temperature points in heat exchangers and electrical connections.
- Oil and coolant analysis: Evaluate lubricant degradation and presence of contaminants.
Optimization of energy efficiency
- Apply automatic learning to adjust the operation according to demand and avoid unnecessary cycles.
- Adjust the thermal load and improve heat exchange through cleaning and scale control in order to improve the coefficient of performance (COP).
- Implement recovery systems to reuse thermal energy in other important processes.
- Implement strategies such as capacity modulation and frequency control in compressors to achieve efficient load management.
Predictive and preventive maintenance strategy
- Predictive maintenance models: Use artificial intelligence to predict failures and schedule maintenance before unscheduled shutdowns.
- Condition Based Maintenance (CBM): Make decisions based on data collected in real time.
- Inspection and preventive maintenance programs: Establish schedules for cleaning exchangers, checking connections and mechanical adjustments.
Preliminary analysis to establish the strategy
- Initial analysis: Conduct an inventory of the heat pumps, their current status and energy efficiency. Data collection: Install sensors to collect data on temperatures, pressures, flow and energy consumption.
- Advanced monitoring: Implement a SCADA (Supervisory Control and Data Acquisition) system to monitor performance in real time. Use machine learning algorithms to predict failures and optimize predictive maintenance.
- Optimize energy efficiency: Compare heat pump performance with industry standards and other similar installations. Evaluate the energy efficiency (COP) of each pump and adjust operating parameters (temperatures, flow rates) to improve performance.
- Proactive maintenance: Schedule interventions based on the actual condition of the pumps, not just time intervals. Train operators in the use of the monitoring system and in the analysis and interpretation of data to detect anomalies.
- Review and adjustments: Perform periodic audits of the monitoring system and energy performance, based on the results obtained, adjust the heat pump maintenance and optimization strategy.
- Documentation and reporting: Keep a detailed record of all heat pump maintenance interventions and pump performance. Generate continuous reports showing the evolution of energy performance and improvements achieved.
Elements to implement for heat pump maintenance
- Implementation of sensors and monitoring systems:
- Install temperature sensors at key points of the system.
- Install electricity consumption meters to calculate the COP in real time.
- Use pressure sensors to monitor refrigerant levels.
- Data analysis and optimization:
- Apply a data analysis system that compares actual performance with expected performance.
- Use machine learning algorithms to predict failures and optimize performance.
- Predictive maintenance:
- Schedule inspections and cleanings based on data analysis, not just at fixed intervals.
- Detect and alert on potential problems before they significantly affect performance.
- Automatic optimization:
- Implement a control system that performs automatic adjustment of the operating parameters to maximize the COP.
- Adjust the heating curve according to the climatic conditions and the thermal demand of the installation.
- Integration with energy management systems:
- Intelligent programming that adjusts the desired temperatures according to the activity in the facility.
- Refrigerant monitoring:
- Develop refrigerant leak detection systems.
- Perform constant checks of coolant levels and quality.
- Continuous performance evaluation:
- Develop refrigerant leak detection systems.
- Perform constant checks of coolant levels and quality.
Establish a system of periodic reports showing efficiency trends and areas for improvement.
Compare performance with industry benchmarks and adjust strategy as needed.
How does scheduled maintenance influence the efficiency of a heat pump?
Scheduled maintenance is significant in maximizing the efficiency and life of a heat pump. Here’s how it influences performance:
- Clean heat exchangers improve heat absorption and dissipation, ensuring that the pump operates at peak efficiency.
- A mechanically sound heat pump requires less energy to achieve the same heating output, which translates into lower energy costs.
- Regular checks of compressors, fans and refrigerant levels help prevent premature wear and costly repairs.
- Consistent heat pump maintenance reduces temperature fluctuations and ensures that the system maintains a stable and comfortable environment.
- Cleaning or replacing filters prevents clogging, allowing proper airflow and minimizing stress on the system.
- Early detection, identification and troubleshooting of problems, such as refrigerant leaks or electrical faults, prevents major system failures.
- Proper maintenance reduces stress on components, increasing the overall durability of the heat pump.
Correct operation of heat pumps
The correct operation of these equipments is important to ensure efficiency and durability over time. These units play a key role in heating and cooling systems, so ensuring their optimal performance not only improves the quality of the environment, but also contributes to reducing operating costs. Below are some basic actions that we can apply to ensure the proper operation of heat pumps:
- Periodic overhaul and maintenance: One of the fundamental practices is to perform regular inspections. This includes checking the condition of major components such as the compressor, heat exchanger and coils. Keeping them clean and operational is crucial to ensure efficient performance. Filters should be cleaned or replaced periodically to avoid blockages that affect airflow and thus system performance.
- Refrigerant quality monitoring: Refrigerant is an essential element for the heat pump operating cycle. It is important to ensure that the refrigerant level is within the manufacturer’s recommended parameters. A low level can impact the pump’s ability to transfer heat, which reduces energy efficiency. In addition, checking for leaks is essential to prevent long-term problems.
- Thermostat calibration and adjustments: An improperly calibrated thermostat can cause the heat pump to run more than necessary or not run efficiently. It is important to regularly check the thermostat calibration to ensure that temperatures are maintained within desired ranges without generating unnecessary energy consumption.
- Air duct Inspection: Air ducts should be free of obstructions to ensure iproper air circulation. Any restriction in airflow can affect both the efficiency of the system and its ability to maintain the desired temperature. Make sure ductwork is tightly sealed and undamaged.
- External temperature control: Heat pumps are most efficient when they operate within a specific external temperature range. If they are in an environment where temperatures fall too low or rise too high, their efficiency may be compromised. Ensuring that the unit is located in a suitable location free of obstructions (such as snow, leaves or debris) is vital for proper operation.
- Replacement of worn components: Components such as the fan, coils, and thermostats can wear out over time. It is important to detect any signs of deterioration and replace the necessary parts before they become a major problem. A little preventive maintenance can prevent costly failures in the long run.
- Use of advanced monitoring technologies: Today, there are technologies such as SCADA systems or IoT sensors that allow real-time monitoring of heat pump operation. Implementing these tools not only helps to detect anomalies immediately, but also optimizes system performance by making automatic adjustments based on the data collected.
To ensure the proper operation of heat pumps, it is essential to perform regular maintenance, constantly monitor their performance and make preventive adjustments. By implementing these basic actions, you not only extend the service life of your heat pumps, but also ensure efficient and sustainable performance, which translates into lower operating costs and improved energy efficiency.
Conclusions
Proper maintenance of heat pumps is necessary to ensure efficient operation over time. The preventive approach, which is based on monitoring actual system conditions rather than at fixed intervals, ensures that heat pumps operate without major interruptions. This process prevents failures, and extends the life of the system, avoiding costly replacements or unplanned repairs. Well-managed maintenance reduces the risk of failure, resulting in more reliable and efficient operation.
The use of advanced technologies, such as IoT sensors and SCADA systems for real-time monitoring, is critical to improving heat pump performance. These tools make it possible to detect problems and serious failures, which facilitates early intervention and reduces system downtime. In addition, predictive analytics help anticipate potential failures, which optimizes energy efficiency and reduces operating costs by avoiding urgent and costly repairs. Implementing these technologies transforms maintenance into a more proactive and efficient process.
Adopting a comprehensive maintenance approach, combining advanced monitoring with energy optimization, not only improves the efficiency of heat pumps, but also has a positive impact on the environment. By optimizing performance and reducing energy consumption, CO2 emissions are reduced, which contributes to environmental sustainability. The application of this type of maintenance ensures operational and economic benefits, and supports companies’ sustainability initiatives, aligning with the global goals of reducing carbon footprint and caring for the planet
References
- https://www.energy.gov/energysaver/operating-and-maintaining-your-heat-pump
- https://www.wolf.eu/es-es/guia/funcionamiento-bomba-de-calor
- https://www.viessmann.es/es/consejos/guia-para-elegir-el-sistema-de-calefaccion/eficiencia-de-la-bomba-de-calor.html
- https://servicechampions.com/blog/que-es-el-sistema-de-bomba-de-calor-necesita-reparaciones-o-mantenimiento/
- https://www.wolf.eu/es-es/guia/eficiencia-bomba-de-calor