Table of Contents
- Application standards for coated welding electrodes
- What are coated welding electrodes and their functions?
- Types of coated welding electrodes for carbon steel
- Understanding welding rod numbers for carbon steel: AWS A5.1 specifications
- Criteria for selecting the right type of coated welding electrode
- Proper storage of coated welding electrodes
- Conclusions
- References
Welding electrodes are the main component in welding processes, ensuring strong and reliable joints between materials. Selecting the right welding electrode is critical to ensure quality and safety on every project. Factors such as metal type, welding position, and operating conditions influence the choice of coated electrode, as each type offers characteristics that affect weld strength and durability.
In this article, the different types of coated electrodes, such as the popular E7018 welding rod, are detailed. It also offers a guide to understanding their coding and provides tips on their proper use and storage, which is necessary to ensure optimum, long-lasting performance in industrial applications.
Application standards for coated welding electrodes
The American Welding Society (AWS) and the American Society of Mechanical Engineers (ASME) are the foremost authorities in the field of welding, setting internationally accepted standards. AWS A5.1 provides a detailed framework for coated carbon steel electrodes, defining variables such as coating composition, tensile strength, and suitability for various welding positions. This standard ensures that coated electrodes meet quality, performance, and safety requirements.
What are coated welding electrodes and their functions?
Coated welding electrodes consist of a metallic core that acts as a filler material and a high-quality chemical coating applied in a layer 1 to 3 mm thick, which represents 15 to 30% of the total weight of the electrode. The metal core, composed of the same material as the part to be welded, melts during the welding process, providing the material necessary to form the weld bead and generates the electric arc to join the materials.
The stick welding technique, also known as manual arc welding or SMAW, is a welding process widely used in various industrial applications due to its portability and versatility.
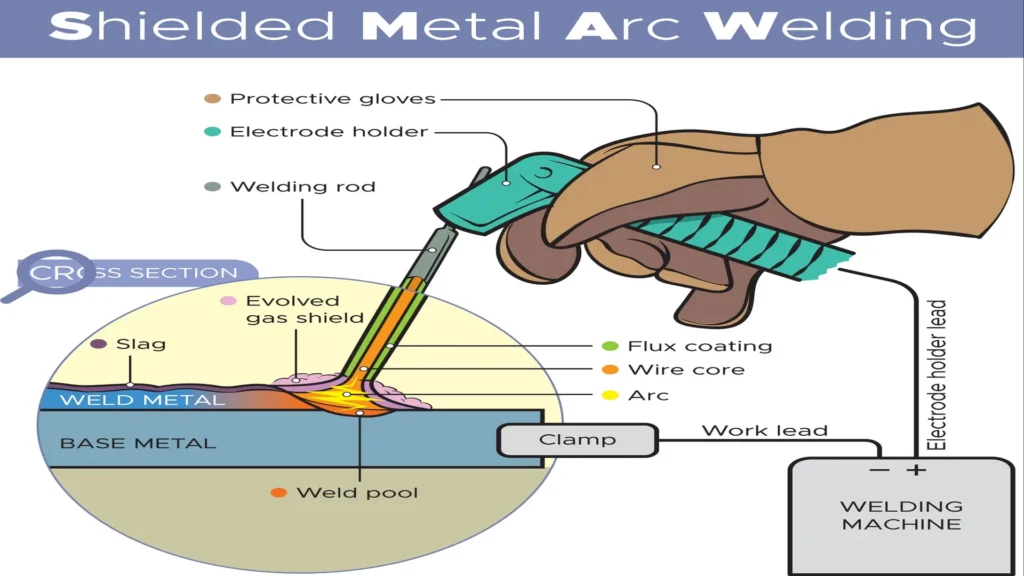
Figure 1. Basic principles of Shielded Metal Arc Welding (SMAW).
Main functions of coated welding electrodes
- Directs the arc, providing balanced and uniform melting.
- Protects the molten metal by creating a gaseous atmosphere to prevent absorption of oxygen, hydrogen, and nitrogen.
- Produces a slag that covers the metal, preventing sudden cooling and contact of oxygen and nitrogen.
- Reduces spatter, when the cladding burns slower than the core, weld metal spatter is reduced.
- Acts as a deoxidizer in the welding process.
- Acts as electrical insulation, coatings are normally electrically insulating.
Types of coated welding electrodes for carbon steel
Many SMAW electrodes maintain similarities with each other, but certain characteristics make specific electrodes more commonly used for particular applications. SMAW welding electrodes for carbon steel can be divided into four groups according to their usage characteristics1.
- Cellulosic (C) electrodes (E6010, E6011): characterized by being coated with organic compounds (cellulose), often with additional ingredients such as sodium and potassium carbonate. It is a high-penetration consumable electrode, ideal for root welding. Due to its high penetration capability and the gaseous arc that helps protect the molten metal puddle, its main applications are: piping, tanks, structures, repairs and on rusty base materials or with oil or paint residues.
- Rutile (R) electrodes (E6013, E7012): The name they receive is related to their coating; rutile is a mineral with a chemical composition based on titanium oxide and their coating contains high amounts of this compound; the slag generated from these electrodes is dense and viscous, likewise they possess excellent ease of handling. Due to its low penetration capacity it is mostly used in common steels and thin plates, mainly in welds that are not of great responsibility.
- Basic electrodes (B) (E7018): They are a type of electrode coated with calcium carbonate and fluorspar, with low hydrogen content. They possess excellent crack resistance and require preheating (baking) before use to remove moisture from the low hydrogen flux. 7018 welding rod is generally used for welding moderate to high grade and low alloy metals, such as steel, as well as in major constructions such as storage tanks and pipelines.
- Acid (A) electrodes (E7024, E7014): They are characterized by having the coating composed of iron oxide, manganese and silica. Through them, good penetration is achieved, especially in thick materials and in smooth or perpendicular environments. 7024 electrodes are widely used in heavy fabrication, storage tank and bridge construction, and transportation.
Understanding welding rod numbers for carbon steel: AWS A5.1 specifications
When welding with coated electrodes, it is necessary to differentiate between the types of electrodes, as each has specific characteristics. Some are effective on rusty metal, while others require clean steel. Also, some are suitable for any welding position, while others are limited to specific positions. Identifying a coated electrode is easier when you know how to decipher its five-digit alphanumeric code marked on its base. The following is a breakdown of the A.W.S A5.1 nomenclature system for E 7018 welding rod2:
- The first letter or prefix “E” indicates that this is an electrode designed for hand or arc welding, E7018.
- The first two digits E7018 of this electrode classification, designates the minimum tensile strength without post weld heat treatment of the deposited metal in thousands of pounds per square inch (psi); in this case it indicates that the electrode possesses a tensile strength of 70,000 psi; where this variable in a material is defined as the maximum amount of stress it can withstand before failure.
- The third digit E7018 determines the position at which the electrode can be successfully welded (in this case, the 1 refers to all positions). Table 1 describes the welding positions for this type of electrode:
Table 1. Classification of welding positions
N° | Welding position |
1 | Electrodes for welding in all positions (flat, vertical and overhead and horizontal) |
2 | Electrodes are only applicable for flat and horizontal fillet positions |
4 | Electrodes for welding in all positions, but better in vertical upwards position |
4. While the last digit E7018 indicates the type of coating and the correct polarity of the current required for the process; (in this case, the 8 refers to a low hydrogen electrode) at the same time, the type of coating is classified according to the highest percentage of raw material it contains, as identified in table 2.
Table 2. Electrode classification by and welding current
N° | Type of coating | Welding current |
0 | High cellulose sodium | CC+ |
1 | High cellulose potassium | AC, CC+ o CC- |
2 | High Titanium Sodium | AC, CC- |
3 | High Titanium Potassium | AC, CC+ |
4 | Titanium Iron Powder | AC, CC+ o CC- |
5 | Low Hydrogen Sodium | CC+ |
6 | Low Potassium Low Hydrogen Potassium | AC, CC+ |
7 | High Iron Oxide, Iron Powder | AC, CC+ o CC- |
8 | Low Potassium Low Hydrogen Potassium, Iron Powder | AC, CC+ o CC- |
In summary, the electrode classification according to AWS A5.1 for carbon steels (SMAW process) is represented as follows:
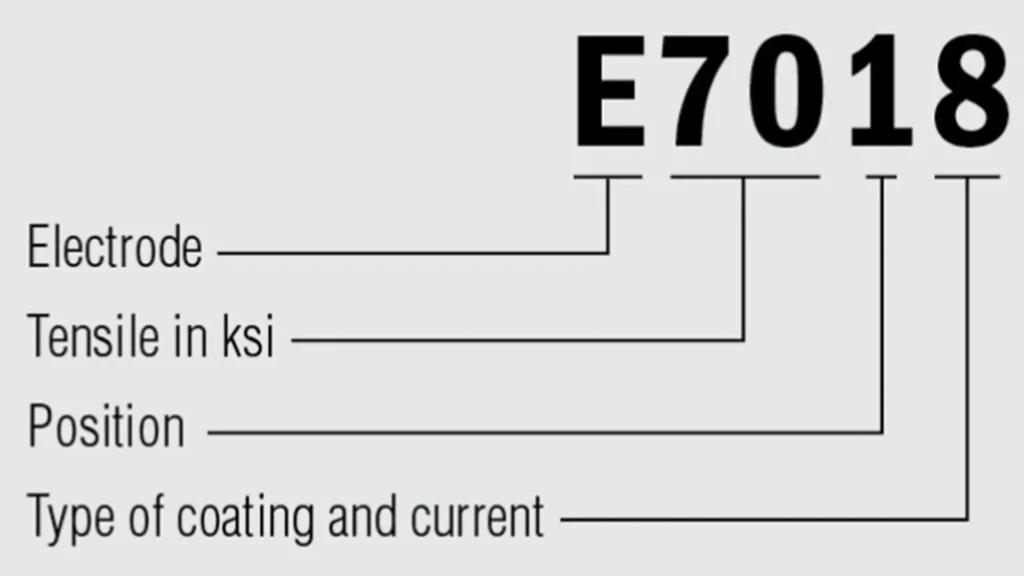
Criteria for selecting the right type of coated welding electrode
The most important thing in the welding process is to select the right electrode. Any welding activity, whether simple or major, requires knowledge of the main variables such as: tensile strength and ductility, base metal, welding position, and polarity, as well as welding current. The following is a summary of a series of criteria that, in combination, will tell you which electrode is the most suitable for a good welding job:
- Type of base metal: Each type of material has specific mechanical and chemical characteristics, being very important to use the right type of electrode for the material to be welded.
- Material thickness: Choose the electrode diameter based on the thickness of the material; thicker materials generally require larger diameter electrodes to ensure adequate penetration.
- Type of weld and position: Determine if the weld will be in flat, horizontal, vertical or overhead positions. Not all electrodes are suitable for all positions.
- Type of joint to be welded: Consider whether you will be working on butt joints, corner joints, overlap joints, etc., as some electrodes are more suitable for certain types of joints.
- Stress to withstand: Evaluate the mechanical load the weld needs to withstand. Basic electrodes are ideal for high-demanding applications, while rutile electrodes are preferred for less critical applications.
- Power of the welding machine: Ensure that the welding machine can handle the selected electrode, especially in terms of amperage required. As a rule of thumb, it is explained that:
- Welder’s skill: Opt for electrodes that match the welder’s skill level. Rutile electrodes, for example, are recommended for beginners because of their ease of use.
Proper storage of coated welding electrodes
How should electrodes be maintained and stored to prolong their service life? To ensure high-quality welds, stick electrodes used in metal arc welding (SMAW) must be stored properly to prevent moisture absorption, which can cause porosity and cracking. Here are some simple handling and storage techniques for electrodes that help maintain their quality and prolong their service life:
- Storage in airtight containers: store electrodes in their original sealed containers until use. If the containers are open, store them in an airtight container to protect them from moisture.
- Temperature and humidity control: Keep electrodes in a temperature and humidity controlled area. For low hydrogenation electrodes (7018 welding rod) for example, it is ideal to use a temperature controlled cabinet or oven between 250 and 300°F (120 to 150°C).The following video presents the due process storage and conditioning of electrodes, mainly low hydrogen electrodes. Source: CWB Group.

CSA W59 Storage and conditioning of electrodes.
3. Avoid exposure to air: Limit exposure of the electrodes to open air. If electrodes are exposed, use them as soon as possible to minimize moisture absorption.
4. Drying and re-drying: If the electrodes absorb moisture, they should be dried in an oven at the temperature recommended by the manufacturer before use. It is critical to follow specific temperature and time guidelines to avoid damaging the electrode coating.
5. Stock rotation: Use electrodes in the order in which they were purchased. This ensures that electrodes stored for a long time do not deteriorate before use.
6. Regular inspection: Regularly check the condition of stored electrodes for deterioration, such as corrosion or damage to the coating.
Following these simple handling and storage techniques will maintain the quality and functionality of the electrodes, providing high-quality welds when they are used.
Conclusions
Selecting the right welding electrode and ensuring its proper storage are critical to achieving high-quality SMAW welds and ensuring long-lasting performance. By following established regulations and carefully considering the type of welding rod, welders can optimize both safety and efficiency in their operations.
In addition, it is necessary to understand the mechanical characteristics of the base material, tensile strength, thermal conditions, joint design, and welding machine parameters to ensure an effective process. Therefore, a thorough understanding and proper management of these elements are critical to improve efficiency and obtain successful results in these welding processes.
References
- Mechanical Engineering Site. (2021, 2 de enero). 4 Major Types of Welding Electrode Coatings. Retrieved June 25, 2024 from https://mechanicalengineeringsite.com/4-major-types-of-welding-electrode-coatings/
- BFMexico. Clasificación de electrodos de la A.W.S. Retrieved June 25, 2024 from https://bfmx.com/mejora-continua/clasificacion-de-electrodos-aws/