Welding is a fundamental technique in different industries, from construction and manufacturing to automotive and aerospace. It is the process that joins materials, usually metals or thermoplastics, by coalescence. The quality of a weld is critical to ensure the structural integrity of the parts and the safety of the people using them.
A well-executed weld provides a strong and durable joint, while a defective weld can lead to structural failure and costly repairs. Understanding the characteristics that differentiate a good weld vs. a bad weld is critical for any professional in the field.
In this article, we will explore the key aspects that define a good weld vs. bad weld, common defects to avoid, and inspection techniques that ensure the quality of welded joints, thus ensuring the reliability and safety of welded structures.
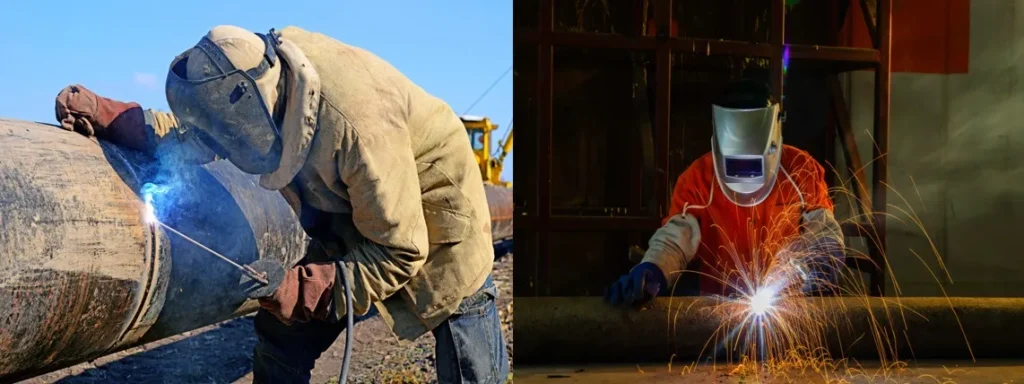
Definition of a good weld vs. bad weld
A good weld vs. a bad weld is characterized by different criteria. A good weld is known for its structural integrity and uniform appearance. General criteria for evaluating the quality of a weld include adequate penetration of the weld metal, proper fusion of the base materials and the absence of defects such as porosity, cracks, or slag inclusions. Visually, a good weld should have a uniform bead, with a smooth and consistent profile, free of undercuts or excess material. These attributes ensure that the weld can withstand the loads and stresses to which it will be subjected during its service life.
In contrast, a bad weld is flawed in one or more of these aspects. Common defects in a bad weld include lack of fusion, insufficient penetration, excessive porosity, cracking, and deformation. These defects compromise structural strength and can lead to premature failure, resulting in safety risks and increased operating costs.
Early identification and correction of these defects are essential to maintaining the quality and reliability of welded structures. Understanding the differences in good welding vs. bad welding helps professionals ensure the highest standards in their welding projects.
Characteristics of a good weld
Understanding the characteristics of a good weld vs. a bad weld is crucial. A good weld stands out for its visual appearance and structural integrity. Visually, it should have a uniform bead, free of undercuts, excess material or spatter. The profile should be smooth and consistent, with adequate weld metal penetration, ensuring complete fusion of the base materials. Uniformity and absence of visible discontinuities are key indicators of a good weld.
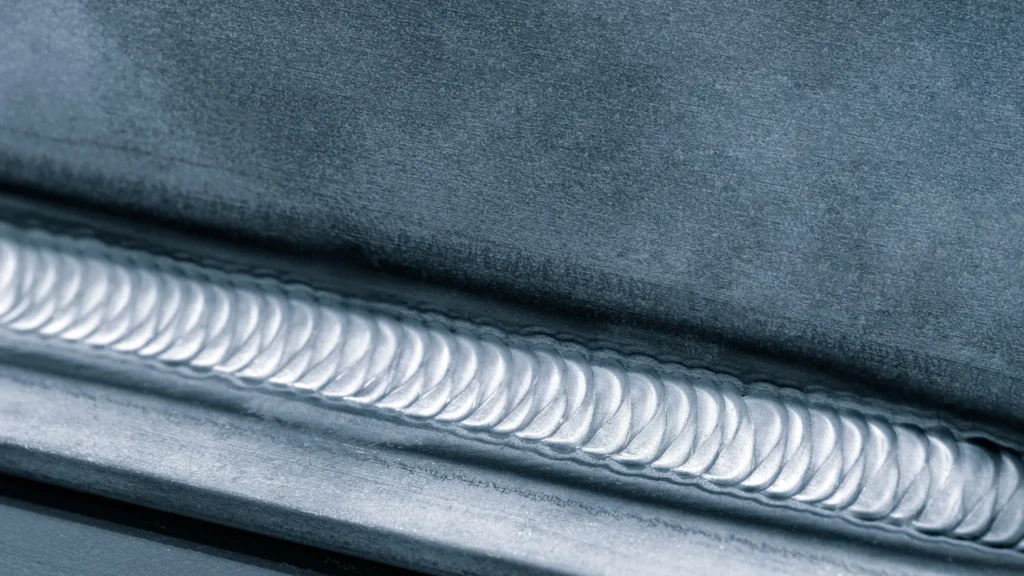
Welding parameters that influence quality include temperature, welding speed and materials used. The temperature should be high enough to melt the base materials and weld metal, but not so high as to cause deformation or defects. The welding speed should be constant to avoid variations in penetration and defect formation. Materials should be of high quality and compatible with each other to ensure a strong joint. Using low quality materials can introduce impurities and defects into the weld, compromising its integrity.
Welding tools and equipment also play a crucial role in weld quality. Using modern, well-maintained equipment, such as MIG (Metal Inert Gas) or TIG (Tungsten Inert Gas) welders, can help ensure a high-quality weld. MIG welding uses a consumable wire electrode and a shielding gas that prevents contamination of the molten metal. It is ideal for welding thinner materials and is commonly used in automotive manufacturing and repair.
TIG welding uses a non-consumable tungsten electrode and an inert gas, such as argon or helium, to shield the weld area. It is preferred for its precision and the quality of the weld it produces, making it ideal for detailed work and thinner materials.
The use of shielding gases is essential in these processes. In MIG welding, the shielding gas (usually argon, CO2 or a mixture of both) forms a barrier that prevents oxidation and contamination of the molten metal. In TIG welding, the inert gas (mainly argon) not only protects the molten metal but also the tungsten electrode, ensuring a clean and strong weld.
An example of good vs. bad welding can be seen in the fabrication of metal structures for the aerospace industry, where integrity and accuracy are crucial. Case studies have shown that well-executed welds in these applications can withstand extreme stresses and adverse conditions without failure. The quality of the materials used, the accuracy of the welding parameters and the proper use of equipment and shielding gases are essential to achieve these results.
Characteristics of a bad weld
A bad weld is characterized by the presence of defects that compromise the integrity and safety of the structure. Understanding the characteristics of a good weld vs. a bad weld helps identify these problems. Common defects include porosity, cracks, slag inclusions, lack of fusion, and insufficient penetration. Each of these defects can have significant consequences for weld quality and durability.
- Porosity: Porosity manifests itself as small holes in the weld bead caused by gases trapped during the solidification process. This defect can weaken the weld, reducing its strength and load-bearing capacity. In addition, porosity can facilitate corrosion by allowing moisture and contaminants to enter.
- Cracks: Cracks are breaks in the weld that can occur during or after cooling. They can be superficial or internal and are caused by residual stresses, rapid cooling, or improper welding techniques. Cracks are especially dangerous because they can propagate under dynamic loads, resulting in unexpected and catastrophic failures.
- Slag inclusions: Slag inclusions are non-metallic materials trapped in the weld, usually from residues of the welding process or impurities in the base materials. These inclusions weaken the joint and can act as stress concentration points, increasing the probability of failure under load.
- Failure to fuse: This defect occurs when the weld metal does not fuse properly with the base material. It can be caused by insufficient heat input, too fast a welding speed, or improper technique. Failure to fuse results in a weak joint that cannot withstand adequate loads, compromising structural integrity.
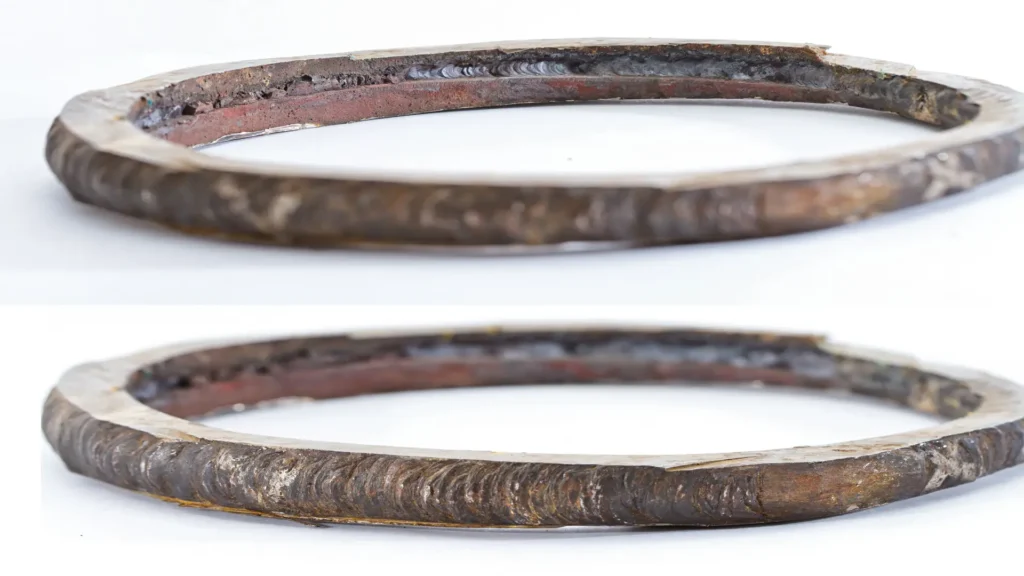
- Insufficient penetration: Insufficient penetration refers to the lack of depth of the weld metal into the base material. Similar to lack of fusion, it can be caused by incorrect weld parameter settings. Insufficient penetration reduces weld strength and increases the risk of structural failure.
The consequences of these defects can be severe. For example, in bridge or building construction, a poor weld with cracks or lack of fusion can lead to collapse under normal loading conditions, endangering lives and causing significant economic losses.
A notable case study is the collapse of an offshore platform due to weld defects. The investigation revealed that the welds exhibited cracks and lack of fusion, which compromised the integrity of the structure under normal operating conditions. This incident underscores the importance of proper welding techniques and quality control to avoid catastrophic failures.
By understanding and avoiding the common defects associated with poor welds, professionals can significantly improve the safety and durability of welded structures.
View the video showing the different defects in welds. Source: Material Welding.

Different defects in welds.
Welding inspection techniques
Inspection of welds is crucial to ensure their quality and safety. Non-destructive inspection (NDT) techniques allow the integrity of welds to be evaluated without damaging the material. Common techniques include visual inspection, ultrasound, X-ray, magnetic particle, and liquid penetrant.
Visual inspection
An essential component of inspection is visual inspection, which is performed at various stages of the welding process: during preparation, during welding, and at the end of welding.
- Visual inspection during preparation: Before welding begins, the materials and surfaces to be welded are inspected to ensure that they are clean, free of rust, grease, and other contamination. The fit-up and alignment of parts is checked and tools and equipment are checked to ensure that they are in optimum condition.
- Visual inspection during welding: While welding is in progress, the inspector observes the process to detect problems such as incorrect bead application, variations in welding speed, and the presence of spatter. Adequate lighting and magnifiers are used to improve visibility of the weld in progress.
- Visual inspection at the end of the weld: Once the weld is completed, the bead is examined for uniformity, penetration, and absence of visible defects such as cracks, porosity, and undercuts. Tools such as magnifying glasses, portable lights, profile gauges and rulers are used for this detailed inspection.
Ultrasonic
This technique uses high frequency sound waves to detect internal discontinuities in the weld. The waves are transmitted through the material and reflect off the defects, allowing them to be identified. The advantages of ultrasound are its ability to detect internal defects and its portability. However, it requires highly trained operators and can be difficult to interpret in complex materials.
The techniques for ultrasonic examination of welds described in the Standard Practice for Ultrasonic Contact Examination of Welds (ASTM- E 164- 03) are intended to provide a means of examining welds for both internal and surface discontinuities within the weld and heat-affected zone. The practice is limited to the examination of specific weld geometries in forged or wrought material.
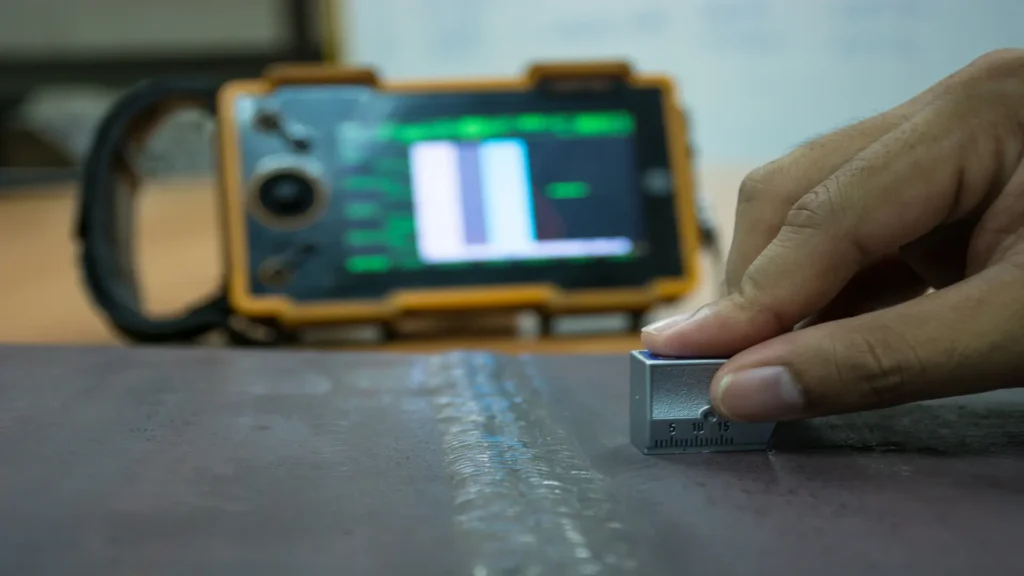
Industrial radiography
X-rays are used to image the weld and reveal internal defects such as porosity, inclusions and cracks. The main advantage is its high resolution and ability to inspect welds in hard-to-reach areas. However, it is an expensive technique and requires strict safety measures due to radiation.
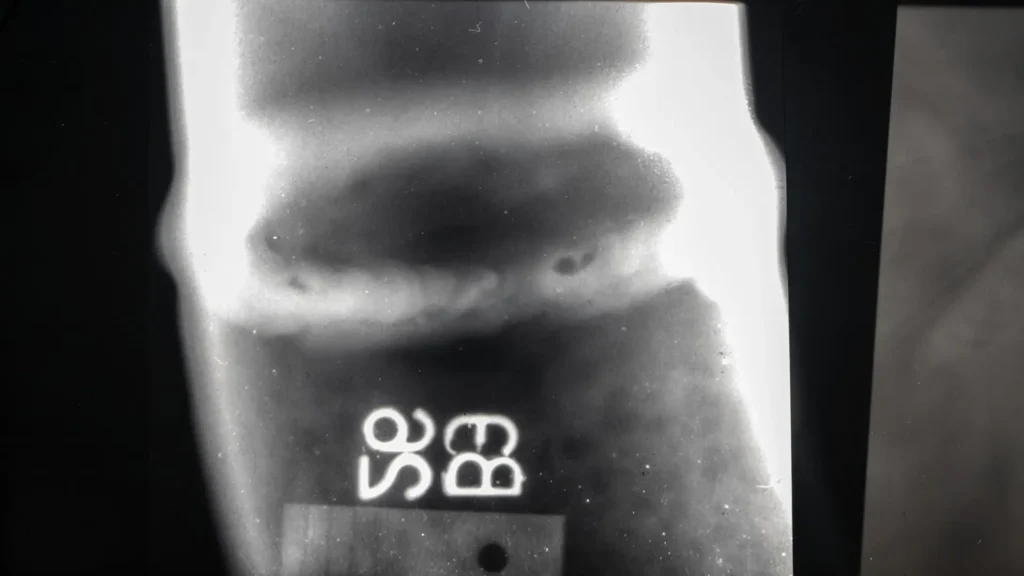
Magnetic particles
This technique is used to detect surface and subsurface defects in ferromagnetic materials. A magnetic field is applied to the weld and magnetic particles adhere to the areas with discontinuities. It is a fast and relatively inexpensive technique, but is not applicable to non-ferromagnetic materials.
Liquid penetrant
Used to detect surface defects, this technique involves the application of a penetrating liquid over the weld. After a waiting time, the excess liquid is removed and a developer is applied to visualize the discontinuities. It is a simple and inexpensive technique, but only detects open surface defects.
Each technique has its own advantages and disadvantages, and the choice of the appropriate technique depends on the nature of the weld, the type of material and the specific requirements of the project.
Welding process and key parameters
The welding process involves joining materials by applying heat and sometimes pressure to melt and fuse the base materials. Critical parameters that must be controlled during the welding process include temperature, welding speed, current type and shielding gas flow.
- Temperature: The temperature must be high enough to melt the materials without causing overheating or deformation.
- Welding speed: A constant speed ensures uniform penetration and proper weld bead formation.
- Type of current: Direct current (DC) and alternating current (AC) are used depending on the type of weld and materials. The choice of the correct type of current influences arc stability and weld quality.
- Shielding gas: In processes such as MIG and TIG welding, the use of shielding gases (such as argon, helium or CO2) is essential to prevent oxidation and contamination of the molten metal.
Welder training and certification are critical to ensure that best practices are followed and quality standards are maintained. Certified welders have the knowledge and skill to adjust parameters to project specifications and troubleshoot problems that may arise during the process.
The impact of welding equipment and tools on final quality should not be underestimated. Well-maintained, high-quality equipment ensures efficient operation and the production of consistent, high-quality welds.
Practical recommendations for identifying and preventing welding defects
How to identify a good and a bad weld?
To identify a good weld vs. a bad weld, observe the weld bead: it should be uniform, smooth and free of undercuts, spatter or excess material. The penetration should be adequate and visible, with no discontinuities. Conversely, a poor weld will show porosity, cracks, slag inclusions, lack of fusion and insufficient penetration.
Practical tips for welding professionals
- Visual inspection: Perform visual inspection at all stages of the welding process. Use tools such as magnifying glasses and profile gauges to detect surface defects.
- Correct parameters: Ensure that welding parameters such as temperature, speed and shielding gas flow are set correctly.
- Quality equipment: Use high-quality equipment and consumables and maintain them in good condition.
- Continuous training: Train welders in welding techniques and update their certifications regularly.
Additional questions on defect prevention
1. How to prevent porosity?
Make sure that the surfaces to be welded are clean and dry, and use a suitable shielding gas.
2. How to prevent cracking?
Control the cooling rate and use the proper welding technique.
3. What maintenance does the welding equipment require?
Periodically check and calibrate the equipment to ensure proper operation.
These practical recommendations will help professionals identify and prevent welding defects, improving the quality and safety of their projects.
Conclusions
The quality of welds is critical to ensure structural integrity and safety. A good weld is characterized by its uniformity and absence of defects, while a bad weld presents flaws such as porosity, cracks and slag inclusions, which can seriously compromise the safety and functionality of structures.
Welding parameters, welder training and the use of appropriate equipment play a fundamental role in the final quality of the weld. Understanding and preventing defects in welds, welding practices and inspection techniques will enhance the safety of people, as well as operational and economic efficiency in various industrial sectors.
References
Own source