Introduction
In the field of heat exchanger engineering and design , the API 660 standard has emerged as an indisputable standard. This document has been the compass for professionals and companies in the manufacture of tube and shell heat exchangers, guaranteeing quality, safety and efficiency. This article delves into the historical development of API 660, breaking down its key features and the implications of its latest updates.
Origins of API 660
The API 660 standard, also known as shell-and-tube heat exchangers, has its roots in the 1950s and 1960s, a period that saw exponential growth in the oil and gas industry. Originated by the American Petroleum Institute (API), this standard emerged in response to the critical need to standardize the manufacturing and design of shell and tube heat exchangers, essential components in numerous industrial processes. Prior to its implementation, the industry faced significant challenges due to a lack of uniformity in standards, often resulting in efficiency, security, and compatibility issues.
API 660 was designed to address these issues by providing a consistent and detailed set of guidelines to ensure the quality and performance of heat exchangers. Since its first edition, it has focused on promoting design and manufacturing practices that not only meet operational demands, but also improve safety and efficiency. Over the years, the standard has evolved, but its origins remain a testament to the industry’s commitment to standardization and continuous improvement, ensuring that heat exchangers are manufactured to the highest quality standards.
Fundamental characteristics of the API 660 standard
The API 660 standard, recognized for its rigor and comprehensiveness, establishes a comprehensive framework for the design, manufacture and operation of shell and tube heat exchangers. Its fundamental characteristics are the pillar on which the reliability and efficiency of these critical equipment in the oil and gas industry is built. Below we delve deeper into these essential features:
- Design and construction: The standard specifies detailed criteria for thermal and mechanical design. On the thermal side, it establishes how loads, heat transfer and pressure drop should be calculated, ensuring that the exchanger meets specific operating requirements and efficiently handles temperature and pressure variations. Regarding mechanical design, API 660 provides guidelines on dimensions, tolerances and construction methods, ensuring that each component can withstand operating conditions without failure. This includes specifications for tubesheets, housings, headers and other critical components, considering factors such as thermal expansion and vibration.
- Material selection: Proper choice of materials is crucial to ensure the durability and safety of heat exchangers. API 660 provides detailed guidance on materials suitable for different operating environments, taking into account factors such as corrosion resistance, ability to withstand high temperatures and pressures, and compatibility with processed fluids. This ensures that the materials selected will not only extend the life of the exchanger, but will also maintain its structural integrity under adverse conditions.
- Inspection and testing: To ensure that heat exchangers meet quality and safety standards, API 660 establishes rigorous inspection and testing protocols. This includes non-destructive testing to detect hidden defects, hydrostatic testing to verify strength under pressure, and performance testing to ensure that the exchanger meets design criteria. These inspections and tests are essential to identify and correct any problems before the equipment is placed in service, thus minimizing the risk of operational failures and accidents.
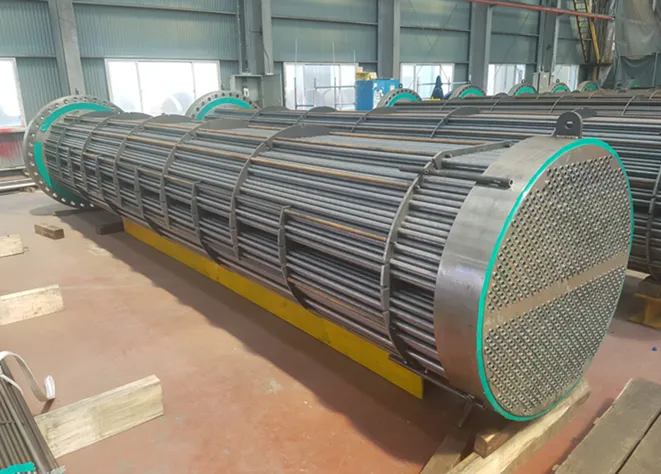
Types of inspection and testing
The API 660 standard establishes a series of rigorous inspections and tests to ensure the quality, safety and performance of shell and tube heat exchangers. These inspections and tests are crucial to verify that exchangers meet established standards and operate safely and efficiently in their operating environments. Below are some of the most relevant types of inspection and testing according to the API 660 standard:
Visual and dimensional inspection
- Visual: A detailed visual inspection of all parts of the heat exchanger is performed to identify any surface defects such as cracks, corrosion or deformation.
- Dimensional: All heat exchanger dimensions are verified to meet design specifications. This includes the length, diameter, thickness of plates and tubes, and alignment of components.
Non-destructive testing (NDT)
- Radiography or ultrasound: Used to detect internal defects, such as cracks or inclusions in welds and materials. These tests are essential to ensure the structural integrity of the exchanger.
- Magnetic Particle Test: Applied to ferromagnetic materials to identify surface and subsurface discontinuities.
- Liquid Penetrant Test: Used to detect cracks and defects on the surface of non-porous materials.
- Eddy Current Testing (ECT): Especially useful for inspecting heat exchanger tubes, this test detects cracks, corrosion, and other surface and subsurface defects in conductive materials. It works by inducing a magnetic field in the material and then measuring the response, allowing anomalies to be identified.
- Infrared thermography: Uses infrared cameras to detect and measure thermal radiation from a surface. Differences in heat output may indicate problems such as leaks, blockages, or areas of degradation.
- Phased array ultrasound testing: An advanced version of traditional ultrasound testing that uses multiple piezoelectric elements to control the direction and focus of the sound beam. This allows for more detailed inspection and the ability to map and size defects with high precision.
- Remote Visual Inspection (RVI): Uses devices such as endoscopes or miniature cameras to visually inspect areas that are inaccessible or difficult to reach. It is useful for internally checking tubes, welds and components.
- Acoustic emission: Detects high-frequency sound waves emitted by the structure under stress. Acoustic emissions may indicate the presence of developing cracks or fractures.
- Microwave inspection: Uses radio frequency waves to detect changes in material properties, such as the presence of corrosion, delaminations or trapped water.
- Metallographic replication testing: Involves taking impressions of the microstructure of the material at the site. These prints are then analyzed under a microscope to evaluate degradation, such as corrosion, fatigue, or microstructural changes.
- Optical emission spectroscopy: Analyzes the light emitted by a sample when excited by an energy source. It is useful to determine the chemical composition and, therefore, the quality and type of material.
- Ultrasound by IRIS (internal rotary inspection system): It is an advanced non-destructive testing technique that uses a rotating ultrasonic transducer to inspect the internal integrity of tubes in heat exchangers and boilers. During the inspection, the tubes are filled with water as a medium for ultrasonic waves, and the transducer, as it rotates and moves along the tube, emits waves that penetrate the tube wall and are reflected back, allowing defects to be detected and quantified. such as corrosion, erosion, pitting and cracks with high precision. This technique offers a detailed and accurate evaluation, being able to identify a wide range of deteriorations and provide visual and quantitative records for monitoring over time, although it requires clean tubes and may have limitations in tubes with sharp bends or complex configurations.

Hydrostatic tests
- Casing and tube pressure test: Performed to check the strength and absence of leaks in the casing and tubes. It consists of filling the exchanger with a liquid, generally water, and pressurizing it to a value higher than the operating value to ensure that there are no leaks or deformations.
Test of performance
- Heat transfer test: Verify that the heat transfer rate of the exchanger meets the design specifications.
- Pressure drop test: Ensures that the pressure drop across the exchanger does not exceed established limits, which could indicate obstructions or design problems.
Material inspection
- Chemical analysis and mechanical tests: These are carried out to confirm that the materials used in the construction of the exchanger meet the specifications of the standard in terms of chemical composition and mechanical properties.
Cleaning tests
- Cleaning inspection: The exchangers are verified to be free of contaminants, manufacturing residues or corrosion before commissioning.
Each of these tests and inspections is vital to ensuring that heat exchangers not only meet design and manufacturing standards, but also operate safely and efficiently throughout their useful life. The API 660 standard provides detailed guidelines on how these tests should be performed, the acceptance criteria, and the qualifications that the inspectors and technicians who perform them must have.
Evolution and detailed updates of the API 660 standard
API 660 has undergone significant transformations, adapting to technological advances and changing industry needs.
Design improvements
- Advanced thermal design: Revisions have integrated advanced thermal design methods, using simulation software to predict performance and allowing more efficient designs tailored to specific needs.
- Innovative mechanical design: The adoption of finite element analysis (FEA) has improved the evaluation of strength and durability, optimizing structural integrity and extending the useful life of the equipment.
Focus on sustainability
- Energy efficiency: The standard now places special emphasis on energy efficiency, promoting the optimization of thermal exchange and the reduction of heat loss.
- Reduction of emissions: Guidelines have been incorporated to minimize harmful emissions, aligning with environmental regulations and promoting sustainable practices.
Advances in materials
- New materials and alloys: The inclusion of advanced materials has been crucial, offering greater resistance to adverse conditions and prolonging the useful life of the exchangers.
- Long Life: These materials not only improve corrosion resistance, but also reduce the need for costly maintenance and replacements.
Integration of digital technologies
- Simulation and Modeling: Computational modeling and simulation tools have been integrated to optimize the design, allowing detailed analysis and performance improvements.
- Computer Aided Design (CAD): The use of CAD software makes it easy to create detailed models, streamlining the design process and allowing for efficient adjustments.
Implications of the latest updates
The latest updates to the API 660 standard have profound and transformative implications for the oil and gas industry, reflecting technological advances and a renewed commitment to efficiency, sustainability and safety.
These revisions not only incorporate more sophisticated design methods and advanced materials that improve resistance to extreme conditions and extend the life of heat exchangers, but also emphasize the importance of energy efficiency and reduction of harmful emissions, aligning with global environmental regulations and sustainability initiatives.
The integration of digital technologies such as computational modeling and computer-aided design (CAD) enables unprecedented precision in design and manufacturing, facilitating early detection of potential problems and customization to specific operational needs.
These upgrades not only raise the bar for quality and safety in heat exchangers, but also prepare companies to meet future challenges, ensuring their products and practices not only meet current demands, but are also ahead of the curve. of innovation and environmental responsibility.
Conclusion
The API 660 standard is a living testimony of the evolution of engineering and technology in the industrial sector. Their continuous updating not only ensures that heat exchangers meet current demands, but are also prepared for the challenges of the future. As professionals in this field, it is our responsibility to stay informed and adapt to these regulations, thus guaranteeing excellence and safety in our projects.
References
Own source