Weld inspection is a fundamental process in ensuring the integrity and quality of welded joints, which are fundamental in various industries, from construction to aerospace. Proper inspection helps detect defects and imperfections that could compromise the structural integrity of a welded component, potentially leading to catastrophic failures.
Visual inspection tools are the first line of defense in weld inspection, allowing inspectors to identify surface defects such as cracks, porosity, and grinding. These tools, ranging from simple magnifiers to advanced endoscopes, provide a clear view of the weld area, ensuring that any visible defects are addressed immediately.
Measuring tools, such as calipers, fillet weld gauges, and weld size gauges, are essential for verifying weld dimensions and tolerances. These tools ensure that welds meet specified standards and criteria, maintaining the overall quality and safety of the structures they support.
The role of inspection tools in manufacturing
Inspection tools play a vital role in various areas of manufacturing, ensuring that welded joints meet stringent quality and safety standards. In the automotive industry, inspection tools are used to verify the integrity of welds in vehicle frames and components, crucial for passenger safety.
In aerospace, precise weld, inspection is critical due to the extreme conditions aircraft endure; even minor weld defects can lead to catastrophic failures. Shipbuilding relies heavily on weld inspection to ensure the durability and safety of vessels operating in harsh marine environments. In construction, inspection tools help maintain the structural integrity of buildings and infrastructure, preventing potential collapses and ensuring public safety.
Calibrating inspection tools is essential in these sectors to maintain accuracy and reliability. Regular calibration ensures that tools provide consistent measurements, preventing errors that could compromise weld quality. Inaccurate tools can lead to undetected defects, posing significant risks to product integrity and safety.
Accurate weld inspection directly affects product quality and safety. It helps identify defects early in the manufacturing process, allowing for timely corrections and preventing defective products from reaching the market. This not only enhances the durability and performance of products but also reduces the risk of accidents and failures, protecting both users and manufacturers from potential liabilities.
Types of weld inspection tools
Weld inspection involves various tools designed to ensure the quality and integrity of welds. Visual inspection tools, such as magnifying glasses and borescopes, help identify surface defects. Measurement tools, including calipers, fillet weld gauges, and weld size gauges, verify the dimensions and compliance of welds with specified standards. These tools collectively ensure that welded joints meet the necessary quality and safety criteria.
Visual inspection tools
Visual inspection tools are fundamental for assessing weld quality and detecting defects. These tools aid inspectors in achieving thorough examinations of welds, ensuring structural integrity and compliance with standards.
- Flashlights and magnifiers: Inspectors utilize handheld flashlights to illuminate weld joints, revealing surface irregularities and discontinuities. Magnifiers, such as magnifying lenses or loupes, enhance visibility for detailed scrutiny of weld profiles and defect identification.
- Mirrors for hard-to-reach areas: Mirrors with adjustable handles allow inspectors to view obscured or inaccessible weld joints. These tools facilitate inspection in confined spaces or behind obstacles, ensuring comprehensive examination without disassembly or relocation of components.
- Weld size gauges: Weld size gauges, including fillet weld gauges and bridge cam gauges, ensure weld dimensions comply with specified tolerances. These tools measure throat thickness, leg lengths, and other critical dimensions, confirming adherence to design requirements and welding procedures.
Common measurement tools
Accurate measurement tools are indispensable in weld inspection, enabling precise assessment of weld dimensions and geometrical characteristics essential for structural integrity and performance.
- Calipers and micrometers: Precision calipers and micrometers measure weld bead thickness, depth of penetration, and groove dimensions. These tools provide accurate readings, ensuring weld conformity to specified tolerances and dimensional requirements.
- Measuring tapes and rulers: Measuring tapes and rulers are versatile tools used for assessing weld length, spacing, and overall dimensions. Inspectors rely on these instruments for quick measurements during preliminary inspections and final checks, ensuring alignment with design specifications and welding standards.
In summary, visual inspection, tools, and measurement instruments are essential for weld quality assessment. They enable inspectors to detect defects, verify weld dimensions, and ensure compliance with regulatory and industry standards, thereby enhancing the reliability and safety of welded structures and components.
Specialized weld inspection gauges
Specialized weld inspection gauges are critical for accurate measurement and evaluation of welds. These tools ensure that welds meet specified standards and tolerances, playing a crucial role in maintaining structural integrity and quality. Below are detailed explanations of various welding measuring gauges commonly used in the industry.
Bridge Cam Gauge
The Bridge Cam Gauge is a versatile tool used to measure various aspects of a weld. It is primarily designed to assess the angle of the weld bevel, throat size, and leg length of fillet welds. The gauge features a cam mechanism that allows precise measurement of these dimensions by aligning with the weld profile.
This tool is particularly valuable in multi-pass weld inspections, where accurate measurements are essential to ensure that each pass conforms to the required specifications. Its ability to provide precise readings makes it indispensable for achieving high-quality welds and ensuring compliance with welding standards.
The following video provides a quick demonstration of how to use a Bridge Cam Gauge to assist with weld inspection: Verify undercut depth, butt weld reinforcement, external misalignment, fillet leg length and weld prep angle. Source: Technoweld Training.

How to use a Bridge Cam Gauge?
HI-LO Welding Gauge
The HI-LO Welding Gauge is used to measure internal alignment and fit-up in welds. It features adjustable components to accurately assess the height and alignment of a weld relative to adjacent materials. This gauge is crucial in pipe welding to ensure proper alignment, which is essential for achieving a strong, leak-proof joint. Proper use of the HI-LO Welding Gauge helps prevent alignment issues and ensures that welds meet structural and functional requirements.
Weld Gauge 0-20 MM
The Weld Gauge 0-20 mm is designed for measuring small welds with precision. It covers a range from 0 to 20 millimeters, making it ideal for tasks that require accurate measurement of minor weld dimensions. This gauge is crucial in precision welding tasks where small welds must meet stringent specifications. Its accuracy ensures that even the smallest welds conform to design requirements, contributing to the overall quality and integrity of the welded structure.
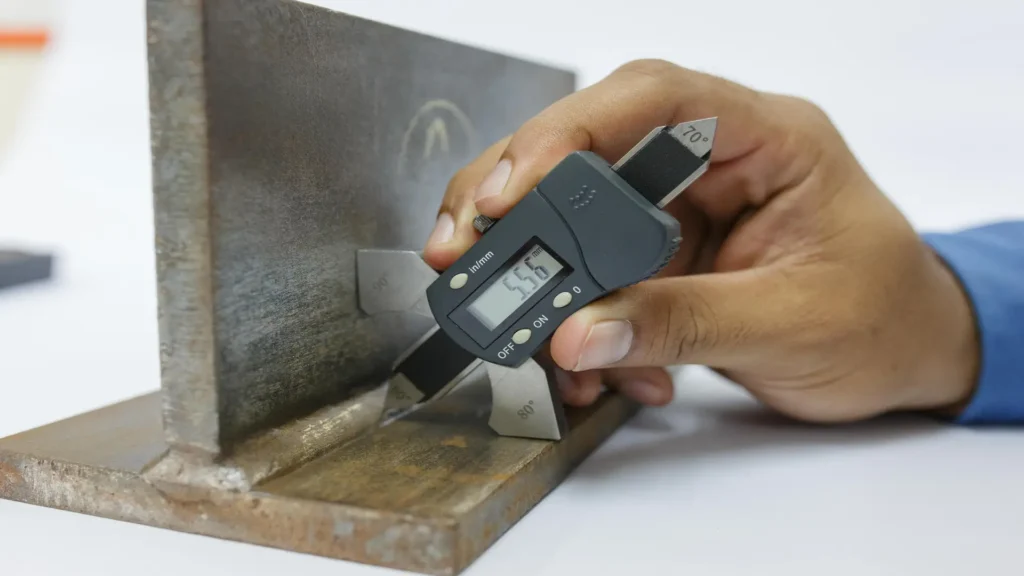
Taper Weld Gauge
The Taper Weld Gauge is used to measure the depth of undercut and pitting in welds. It features a tapered design that allows for precise measurement of these critical defects. This gauge is particularly useful in critical weld inspections where detecting minor imperfections is essential for maintaining structural integrity. By accurately measuring undercuts and pitting, the Taper Weld Gauge helps ensure that welds meet required standards and perform reliably under operational conditions.
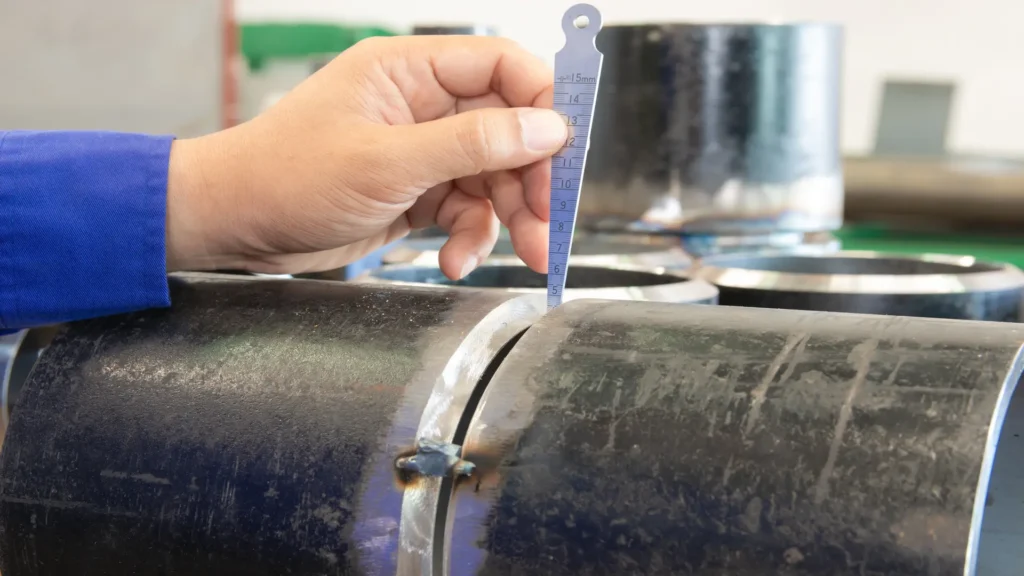
V-WAC Gauge
The V-WAC Gauge is a specialized tool used to measure undercut depth, weld reinforcement, and excess weld metal. It features a unique design to assess these aspects of a weld accurately. The gauge is essential for ensuring compliance with welding standards, as it helps inspectors verify that welds are within specified tolerances for undercuts, reinforcement, and excess metal. This ensures that welds are not only visually acceptable but also meet structural performance criteria.
Additional tools
In addition to specialized gauges, several other essential tools are used in weld inspection to ensure quality and precision.
- Fillet Weld Gauges: These gauges measure the leg length and throat thickness of fillet welds, ensuring they meet design specifications. They are critical for verifying that welds conform to required geometries.
- Contour Gauges: These are used to replicate the profile of welds and other surfaces, allowing for precise measurements and inspections. They are particularly useful for assessing complex weld shapes and contours.
- Digital Weld inspection Gauges: These advanced gauges provide digital readouts for precise measurements, enhancing accuracy and ease of use in inspections.
Calibrating inspection tools
Calibrating inspection tools is very important for maintaining measurement accuracy and ensuring the reliability of weld inspections. Regular calibration ensures that tools provide precise and consistent readings, which is crucial for meeting industry standards and avoiding costly errors.
- Procedures and standards for calibration: Calibration procedures typically involve comparing the tool’s measurements against known standards or reference gauges. This process must follow specific standards, such as those outlined by organizations like the American Society for Testing and Materials (ASTM) or the International Organization for Standardization (ISO).
- Frequency of calibration: The frequency of calibration varies by industry and application. In high-precision manufacturing sectors, tools may need calibration before each use or at regular intervals (e.g., monthly). In less critical applications, calibration might be required less frequently, such as annually. Adhering to these schedules helps maintain tool accuracy and reliability over time.
Best practices for using weld inspection tools
To ensure effective use of weld inspection tools and accurate results, follow these best practices:
- Proper handling and maintenance: Handle tools with care to avoid damage. Regular maintenance, such as cleaning and checking for wear, helps prolong tool life and accuracy. Store tools in protective cases when not in use.
- Common mistakes to avoid: Avoid using damaged or miscalibrated tools, as they can lead to incorrect measurements and compromised weld quality. Ensure that tools are appropriate for the specific inspection task and calibrated according to manufacturer recommendations.
- Ensuring accurate and reliable measurements: Follow proper measurement techniques, including proper alignment and positioning of tools. Double-check measurements and use multiple tools if necessary to confirm results. Adhering to these practices helps ensure that inspections are thorough and that welds meet quality and safety standards.
Conclusions
The use of the right weld inspection tools is fundamental for maintaining the integrity and quality of welded joints across various industries. Accurate weld inspection ensures that welds meet specified standards and tolerances, thereby preventing potential failures that could compromise structural safety and reliability. This vigilance directly impacts manufacturing quality, reducing the risk of defects and enhancing the durability of products, which is crucial in sectors like aerospace, automotive, and construction.
Looking to the future, advancements in technology promise to further revolutionize weld inspection. Innovations such as automated inspection systems, real-time data analysis, and enhanced digital tools are set to improve accuracy, efficiency, and ease of use. These developments will provide even greater precision and reliability in weld inspections, helping to meet increasingly stringent industry standards and drive continuous improvements in manufacturing quality and safety.
References
Own source