Summary.
The encapsulation process welded in pipe; It is the result of wrapping a metal pipe with a diameter (Example 4” Ø) with another metal pipe (6” Ø); using welding for the fixing and sealing of the envelope or capsule according to the procedure and engineering design.
This practice is generally applied in plants or process units in services and when critical low thicknesses are detected; Its application is recommended in sections of pipes, sometimes reaching even complete circuits. This for the purpose of:
- Temporarily remove a hazardous condition; while planning its permanent repair.
- Avoid a fire accident that would cause material damage and human loss with great loss of money.
- Extend the useful life of the asset.
- Do not make an unplanned stop.
- Continue to operate the refinery safely and reliably
Developing.
The American Society of Mechanical Engineers (ASME) developed the ASME PCC-2 (Repair of Pressure Equipment and Piping) standard, which provides methods for repairing equipment and piping within the scope of the ASME Pressure Technology Codes and Standards after having been placed in service. These repair methods include relevant design, manufacturing, examination, and testing practices and may be temporary or permanent, depending on the circumstances.
Generally when handling on-the-go inspection systems for the oil & gas industry (see Figure.1); In order to prevent potential failures in time, this temporary repair method is used and that is where the methodological analysis of the reliability engineer or equipment inspector begins and with their experience achieve a successful end to the project; However, the application of this practice is very risky and each case must be analyzed in its entirety as a project. This article presents a description of this practice, the risks and benefits that its application implies during the repair of equipment and pressure pipes in service.
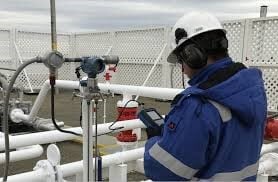
Figure 1. equipment inspector measuring the thickness of the pipe with the plant in service.
The detection of low thicknesses in a pipe that is in service due to the action of any deviation in the process (operational variables out of control) or due to implicit damage mechanisms in the material, lead to the taking of immediate actions such as: extended inspection of thickness measurements to the rest of the circuit and other similar ones in process and with the results obtained from said measurements analyze the calculations of corrosion rates, useful life, remaining thickness and next inspection date; which, serve the analyst to take the action of:
- Continue monitoring the pipeline circuit.
- Continue measuring the most critical points, under a special measurement system.
- Expand the inspection in the controlled circuit and in others with similar process and material characteristics.
- Replace the section of pipe without stopping the process unit.
- Encapsulate the stretch of pipe with the plant in service (see Figure. 2)
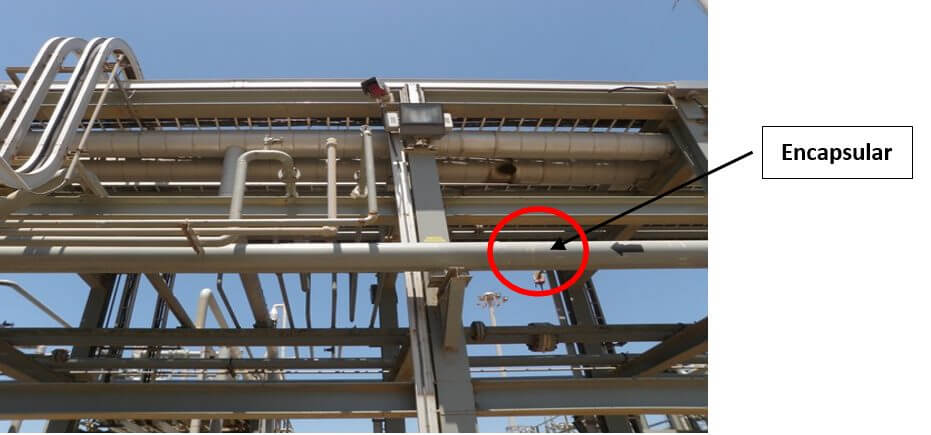
Risks and benefits of encapsulating a section of pipe.
The decision to encapsulate a section of pipe with the plant in service, a series of variables must be considered due to the risk that this represents and it is advisable to follow a procedure with responsibility signatures, which guarantee the functionality of the process. Some of these variables are:
- Process plant where the section of pipe is located. This for safety and strategy to carry out the activity. It is different to encapsulate in a plant where naphtha is processed, than another where steam is processed.
- The length of the section to be encapsulated is determined by the equipment inspector based on the results obtained in the thickness measurement activity. The ends for the circumferential fillet welds should be defined, sweeping the circumference of the tube to be encapsulated to avoid any defects when welding. (key information for capsule design)
- The reliability engineer designs the capsule and gives it the technical specifications for manufacturing and the appropriate welding procedure for this activity. Likewise, it performs a flexibility analysis of the circuit if the case warrants it, due to the new weight of the circuit.
- The manufacture of the sections of the capsule must be carried out in workshops, using manufacturing molds taken from the section of pipe to be encapsulated and guaranteeing that there are no deviations during installation. (See Figure. 3).
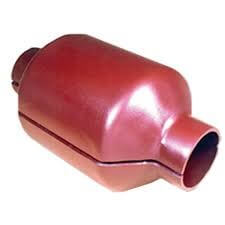
Figure. 3. Pipe capsule manufactured in the workshop.
- There must be a security protocol according to the case, which must include the use of a fire truck on site the day of the installation of the capsule with its operators; as prevention of any fire outbreak that could put human lives and the facilities of the plant in question at risk.
- The follow-up format for this activity must be in writing with the different signatures of responsibility for the role fulfilled and thus guarantee the success of the activity.
Once the capsule installation project is finished (see Figure 4), a recommendation should be made to replace the encapsulated section of pipe and eliminate this temporary condition. From the date of installation of the capsule, the operator can act more safely within his plant and these are the benefits obtained by the action carried out:
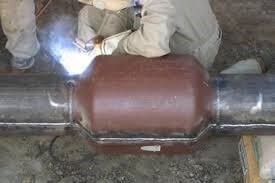
- Eliminate a risk condition
- Avoid a fire accident that would cause material damage and human loss with great loss of money.
- Extends the useful life of the asset.
- Avoid an unplanned stop.
- Operation of the refinery in a safe and reliable way, to continue producing its refined products; which will generate the benefit of the business according to its profit plan and meeting the production goals as a reliable company in the delivery of products.
Conclution.
The application of this temporary repair practice in the oil & gas industry has provided many benefits to companies, since it has been possible to keep the units operating and producing their derivatives according to their business plan. Although it is an activity that implies a certain risk, having qualified personnel, adequate tools and safe methods and procedures that serve as a guide; this activity becomes a usual practice.
The operators of these large industries have their great ally in this practice, as a preventive solution to keep the availability indicator of plants in service under control with an operational reliability at the level of the objectives and goals of large companies.
References.
[1] ASME PCC2 Standard for the repair of in-service pressure piping and equipment.
[1] API – 570 Piping Inspection Code: In-Service Inspection,
classification, repair and alteration of piping systems.
[1] API RP-574 Inspection Practices for piping system components.
About the Author. ing Mario J, Toyo. Inspfalca Technical Advisor, with more than 40 years of experience in Equipment Inspection for the Oil and Gas Industries
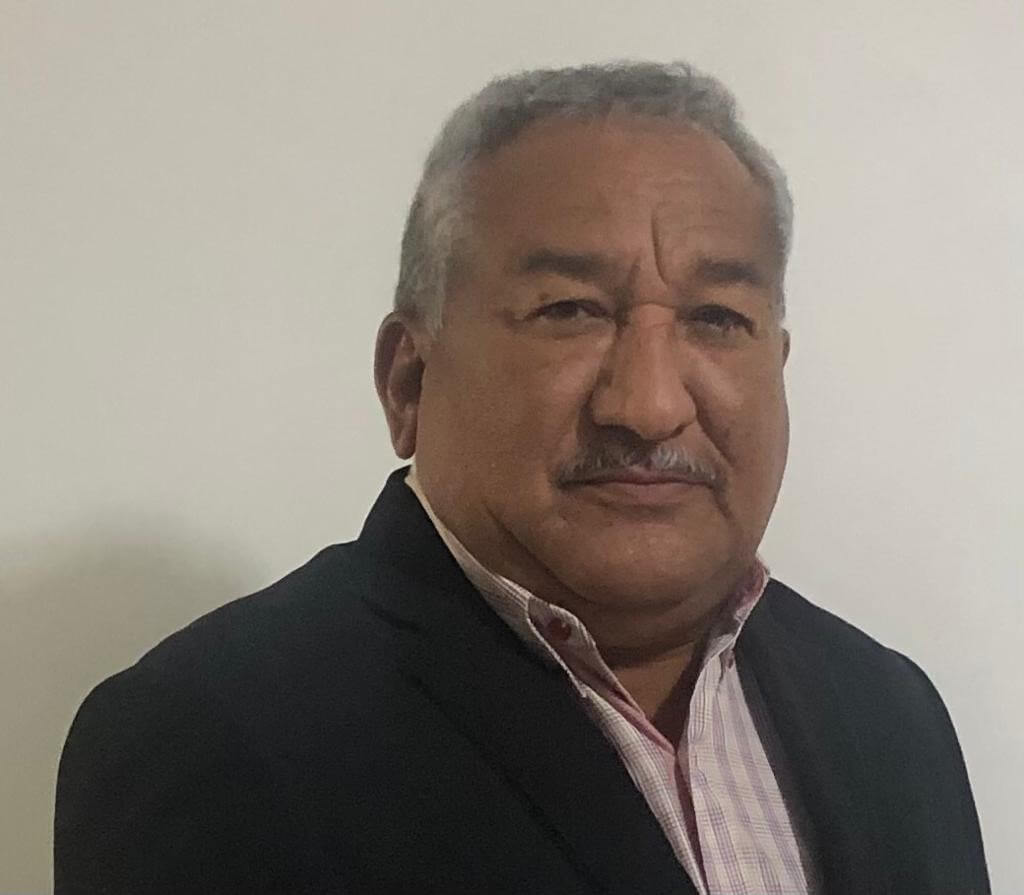