Table of Contents
- Introduction
- Quick diagnostics for industrial power systems
- Next-generation backup power solutions
- Innovative automated switchgear for electrical maintenance
- Types of electrical preventive maintenance routines
- Resilience through design
- Expanded security measures
- Mitigating the risk of accidents by applying electrical preventive maintenance (EPM)
- Conclusion
- References
Introduction
Electrical systems are responsible for 24% of fires in industrial environments, according to the NFPA, underscoring the importance of electrical maintenance programs. These programs integrate advanced technologies such as SCADA systems and AI-driven predictive analytics to detect and manage electrical faults efficiently.
In addition, the implementation of backup power solutions and automated switchgear minimizes downtime during outages, ensuring continuous and safe operations in industries where every moment counts. This article will explore how these technologies and strategies are redefining industrial safety and efficiency.
Quick diagnostics for industrial power systems
Today’s industrial systems require fast and accurate response mechanisms to detect and reduce power failures. SCADA systems, coupled with AI-driven predictive analytics, provide advanced monitoring and predictive capabilities. The integration of intelligent sensors within the power infrastructure enables real-time fault detection, instantly signaling anomalies such as voltage sags, frequency imbalances, or equipment wear and tear.
In addition, AI diagnostics can predict the condition of key components such as transformers and distribution boards, enabling preventive maintenance before problems escalate. This fusion of monitoring, prediction, and immediate feedback is the backbone of an agile emergency response strategy.
Next-generation backup power solutions
In industries where downtime generates significant losses, backup power solutions are critical. Hybrid systems that combine traditional generators with renewable energy sources (solar, wind) provide a sustainable yet reliable power source.
Fuel cell technologies, such as solid oxide cells, are increasingly viable for extended backup durations, providing longer and cleaner operating times during power outages.
Energy storage systems, including advanced flow batteries or compressed air energy storage (CAES), provide another layer of redundancy, maintaining power for critical operations and avoiding the emissions and fuel costs associated with conventional generators.
Innovative automated switchgear for electrical maintenance
High-speed static transfer switches (STS) allow immediate transitions between power sources, ensuring minimal downtime during power outages.
By combining these technologies, facilities can ensure uninterrupted operations and optimize emergency responses, leveraging automation to overcome traditional manual responses.
Types of electrical preventive maintenance routines
Electrical preventive maintenance encompasses a variety of activities that ensure the safe and continuous operation of systems. These routines are divided into three main categories: inspection, testing, and service, and should be implemented systematically to address different operational aspects of each piece of equipment.
The key elements and other critical topics for an efficient program are detailed below:
1. Inventory and risk classification: It is essential to maintain a detailed inventory of all electrical equipment within the facility. This inventory should not only catalog the assets but also classify them according to the level of potential damage if they fail.
Ranking criteria can be based on operational criticality, costs associated with downtime, and safety risks. To facilitate inspections and testing, a detailed checklist should be generated that addresses each piece of equipment, prioritizing those whose failure would have the greatest consequences.
2. Periodic inspection: Each piece of equipment in the inventory should have a predetermined inspection cycle according to its criticality, year of manufacture, and the operating conditions to which it is subjected. Equipment working under variable loads, harsh environments, or high temperatures should be inspected more frequently. Inspections should include a complete visual inspection, looking for signs of wear, overheating, corrosion, and other indicators of deterioration.
Diagnostic and functional testing: In addition to visual and auditory observations, extensive testing should be performed. These include insulation resistance measurements, leakage current tests, power factor analysis, and infrared thermography to detect hot spots. Power quality analysis (harmonics, phase unbalance) is also recommended to detect problems that can reduce equipment life and increase operating costs. Functional tests should verify the operating capacity under simulated loads.
4. On-line monitoring and electrical predictive maintenance: A modern approach includes the use of on-line monitoring technologies for continuous monitoring of critical parameters such as temperature, vibration, and operating voltage. These systems enable a predictive approach, identifying impending failures before they occur. IoT-based monitoring systems can automatically alert electrical maintenance teams to deviations that require immediate intervention, reducing the need for frequent manual inspections.
5. Meticulous record keeping: Keeping meticulous records of every action is essential for traceability and continuous improvement of electrical maintenance. Not only failures and corrections should be recorded, but also critical measurements of tests performed, operating conditions, and even information on preventive maintenance performed.
A computerized maintenance management system (CMMS) can facilitate this process, allowing real-time tracking and reporting for trend analysis and optimization of electrical maintenance cycles.
6. Scheduled repair, adjustment, and replacement: Electrical preventive maintenance is not limited to inspection and diagnosis; it also involves carrying out corrective repairs and adjustments as problems are identified. Faulty or underperforming components should be repaired or replaced immediately to avoid major failures.
Additionally, there should be a replacement plan for parts with determined life cycles, based on the data collected and the manufacturer’s recommendations. This step includes planning for the availability of critical spare parts.
7. Regulatory compliance and auditing: Facilities must comply with applicable electrical safety regulations and standards, such as the National Electrical Code (NEC) or OSHA regulations. In addition, periodic audits are recommended to ensure that electrical maintenance routines comply with industry best practices and legal requirements. Failure to comply can result in penalties or serious safety hazards.
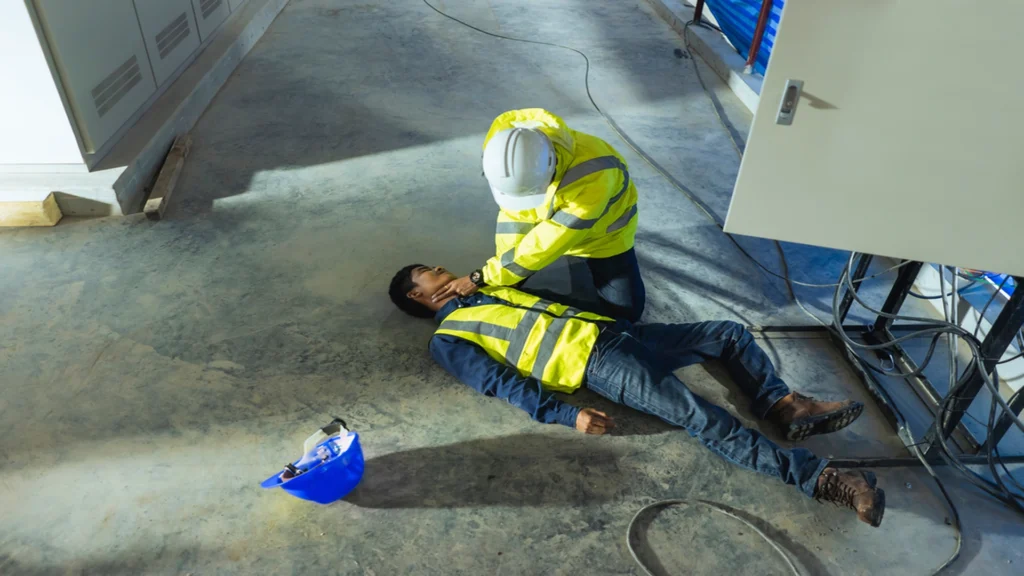
Resilience through design
To prepare industrial facilities for the future, self-repairing networks that can autonomously isolate and repair faults are needed. Modular power distribution systems also offer flexibility, allowing sections of the network to be isolated during failures while maintaining operations in unaffected areas.
Advanced materials, such as high-temperature superconductors, can further enhance the resilience of electrical equipment, improving durability and performance.
The term resilience is not only applied to human behavior; in the field of engineering and industrial systems, it is also used to describe the ability of a system, equipment, or asset to adapt and recover from disturbances or adverse conditions, such as mechanical failure, fluctuations in demand or extreme environmental conditions.
In industrial asset design, resilience refers to creating equipment and systems that are robust and adaptable, able to withstand failure or recover quickly to minimize downtime.
This involves integrating features such as:
- Redundancy: Having duplicate components or parallel systems that take over in case of failure.
- Modularity: Facilitate electrical maintenance or replacement of equipment parts without interrupting the entire operation.
- Fault tolerance: Designing systems that can operate safely, even if some components fail.
- Monitoring and diagnostics: Implement sensors and predictive maintenance algorithms to anticipate problems before they affect operation.
Thus, resilience in industrial design ensures that assets can meet unforeseen challenges without compromising overall operation, improving both system reliability and efficiency.
Expanded security measures
Quick hazard identification allows immediate implementation of safety protocols, reducing risk to personnel and assets. Handheld devices can monitor the physical condition of emergency response equipment. In this context, “physical condition” refers to the structural and operational status of the equipment, i.e., its mechanical and electrical integrity, which ensures its safety during operations.
Efficient deployment of resources: These diagnostics help determine the exact location and nature of an emergency, allowing for more targeted and efficient deployment of response assets and equipment. Geographic information systems (GIS) integrated with diagnostic data can provide spatial context for better resource allocation.
Uninterrupted communication and coordination: Fast and accurate diagnostics facilitate better communication between different teams and stakeholders involved in the emergency response. Integrated communication systems can quickly disseminate diagnostic information to all relevant parties.
Continuous monitoring and adaptation: Continuous diagnostic data allows real-time adjustment of response strategies as the situation evolves. This adaptive approach ensures that the response remains effective throughout the duration of the emergency.
Mitigating the risk of accidents by applying electrical preventive maintenance (EPM)
Electrical preventive maintenance (EPM) is an essential strategy to ensure the reliability and continuous performance of electrical systems in industrial facilities. Through regular inspections and evaluations, this approach allows problems to be detected and corrected before they become critical failures.
By identifying potential failures early, constant uptime is ensured, avoiding unplanned outages that can affect both the operation and productivity of a plant.
Another crucial aspect of EPM is its direct impact on safety. Maintenance programs include detailed tests that identify electrical hazards such as possible electrical arcing or insulation failures, thus mitigating the risk of accidents that can endanger both personnel and the facility’s infrastructure.
Preventive maintenance also extends the life of electrical equipment by ensuring that it operates within its design specifications. Properly maintained electrical components suffer less wear and tear, which delays the need for replacements and allows for better utilization of equipment investments.
Conclusion
From a regulatory standpoint, the EPM is a tool that ensures compliance with applicable industry electrical codes and standards. Many regulations require periodic inspections to ensure that systems are operating safely and efficiently, and failure to comply with these requirements can result in sanctions or penalties. A preventive maintenance program ensures that facilities remain within regulatory parameters, thus avoiding legal or financial consequences.
In addition, this approach allows the energy efficiency of electrical systems to be improved. Problems such as low power factor or load imbalances can be identified and corrected, reducing energy waste and optimizing consumption. This not only implies a reduction in utility costs but also a lower environmental impact, which is increasingly relevant in industrial sectors where sustainability is a priority.
References
- https://www.hanover.com/businesses/business-customer-resources/hanover-risk-solutions/electrical-preventive-maintenance-epm
- https://www.kazarselectric.com/how-a-transfer-switch-protects-your-home-during-power-outages/
- https://www.emersonautomationexperts.com/2019/control-safety-systems/controlling-surge-centrifugal-compressors/
- https://www.lembergelectric.com/blog/3-ways-electrical-preventative-maintenance-can-improve-your-operatives/