Author: Mathieu Bouchard, Eddyfi Technologies
Technological advancements in non-destructive testing are closely dependent on other fields of research surrounding it such as optics, acoustics, or tomography. One such field that plays a crucial role in enabling innovation in eddy current array (ECA) is that of flexible printed circuit boards (PCB), or more specifically, printing copper traces into a thin flexible substrate, commonly referred to as lithography. Recent advances in flexible PCB printing techniques over the past five years have ECA flexing its strength and paving the way for the development of coil sensors of higher quality, ultimately transforming the range of capabilities of eddy current testing. It’s time to stop bending over backwards for complex inspections; take a closer look at Eddyfi Technologies’ new family of ECA probes: P-Flex.
The ability to print coil sensors into flexible boards has been around for some time, but recent advancements have significantly improved the performance of these probes. The reachable density of printed copper traces has increased, resulting in higher numbers of turns in each coil, and thus a stronger magnetic field and more energy transferred
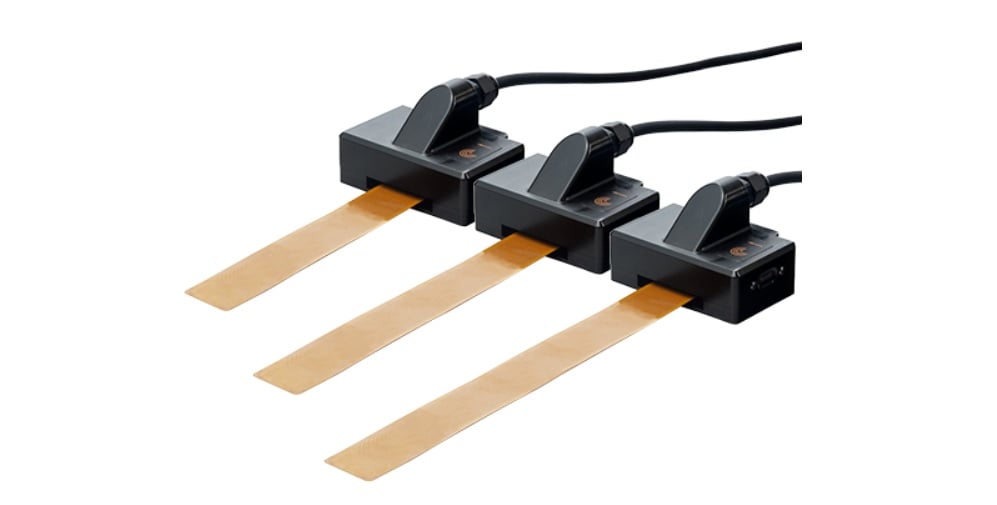
Concretely, this results in a lower level of noise, stronger indication signals, and an improved probability of detection for small flaws, making printed ECA more effective than ever before. Combined with the market-leading Reddy™ instrument, P-Flex technology surpasses other existing printed probes in terms of signal quality.
P-Flex probes are made of an array of 32 coils printed onto a paper-thin, 0.2-millimeter (0.008-inch), flexible board that can be bent with a minimum curvature radius of only 2 millimeters (0.08 inches). This allows inspection of surfaces with highly complex geometries by wrapping or inserting these thin probes into curved surfaces and tight corners, grooves, or gaps.
The P-Flex probe comes in three models that have the same number of coils; the difference lies in their size. For example, the large probe (coil size: 5 mm/0.19 in) provides greater coverage but has reduced resolution compared to the small model (coil size: 2 mm/0.078 in). The choice of probe model should therefore be based on the required coverage and the size of the smallest flaw to detect. One key feature of the P-Flex probe is its modular design. The probe can be detached from its cable adapter, allowing for easy replacement in the case of one component getting damaged. Speaking of wear and tear… a thin layer of a robust, rigid, thermoplastic PEEK (Polyether ether ketone) is installed on the probe to create a protective barrier between the sensors and the surface under inspection. This significantly increases the probe’s durability and allows for a larger volume of inspections.
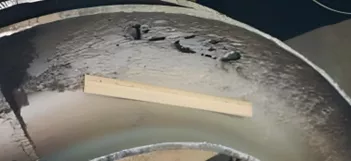
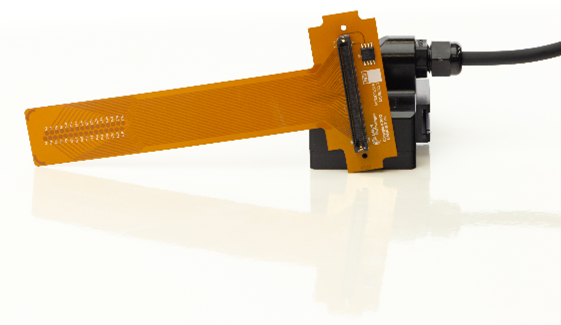
Turbine inspection
Due to its high flexibility, it’s easy to imagine how the P-Flex can become a building block that facilitates ECA probe customization for everyone. With access to a basic 3D printer, you can now manufacture a simple probe holder of any shape, attach a P-Flex and encoder to it, and proceed with your inspection. If needed, Eddyfi Technologies’ custom engineering team is always happy to tackle this part of the work and design the most optimal probe holder for specific applications.
The following images show examples of aircraft turbine components that can be inspected with P-Flex. The probes are shown here without their holder to showcase just how easy it is to ensure good contact with the surface, regardless of its curvature, complex shape, or sharp bends.
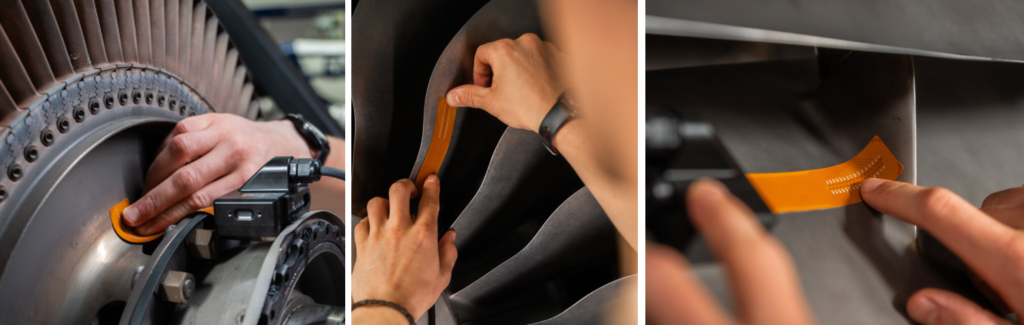
Another application that benefits from P-Flex technology is the detection of small cracks in the grooves of gas turbine discs. As shown below, Eddyfi Technologies has embedded a P-Flex probe in a dovetail-shaped keyed holder, with its sensors covering the entire side surface of the slot. A spring-loaded shoe pushes against the surface to ensure close contact during scans. From there, the probe simply slides along the slot to complete the acquisition. The modular design of this solution also allows the same cable to be reused with multiple probe heads, making it easy to inspect slots of many sizes and shapes.
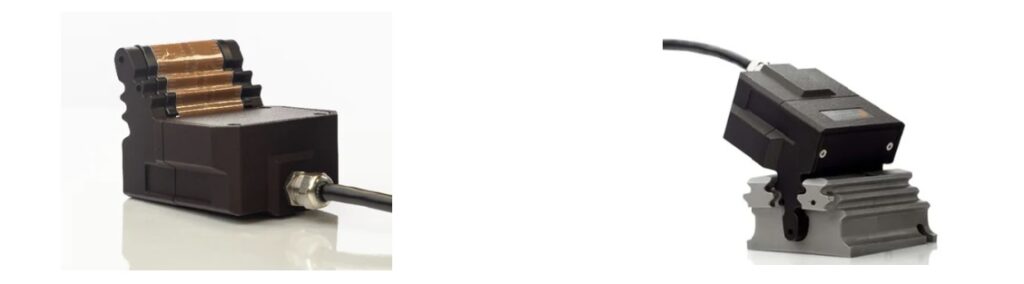
One last question remains, and it is perhaps the most important of all: how does a printed ECA probe compare to traditional ECA with real copper “pancake” coils? To answer this question, we proceeded to inspect a gas turbine disk using two nearly identical probes: one with pancake coils, and one with printed coils (P-Flex). The resulting C-scans below show several differences between the two technologies and point to the overall better performance of the P-Flex for this inspection.
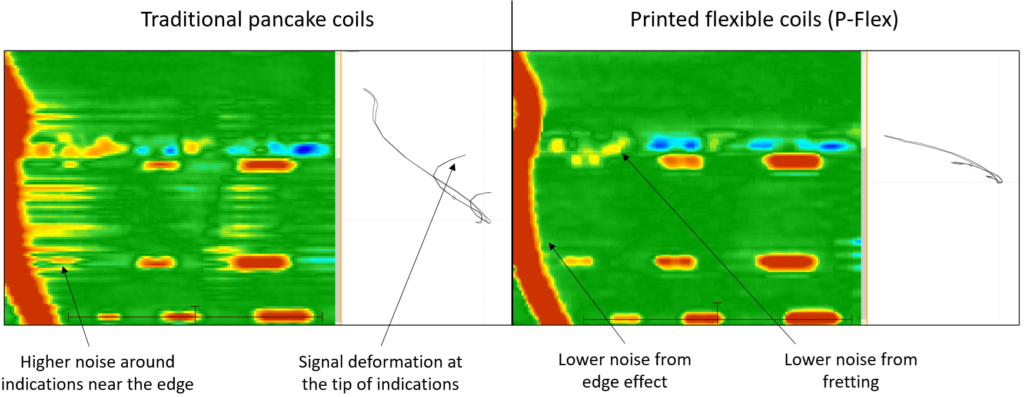
These differences can be explained by the simple fact that pancake coils must be manufactured by hand and placed one by one in the ECA probe, leading to small variations between the size, shape, position, and electric properties of each coil. On the other hand (or rather, no hands at all), the printed sensors of the P-Flex are fabricated by an automated system, making them perfectly identical, equidistant, and at the same distance from the inspected surface.
That being said, pancake sensors aren’t about to disappear completely in favor of printed coils. In fact, one important limitation of the P-Flex is its high-frequency range. While it shines for the detection of surface-breaking defects, it is much more limited for subsurface and far-side detection. Conventional ECA like the I-Flex remains the technology of choice for low-frequency sensors that can penetrate deep into non-ferrous materials.
We’re really not bending the truth when we say that P-Flex ECA probes offer excellent flexibility, customizability, and performance, making them suitable for a wide range of inspection applications. They can be used as standalone probes or integrated into simple holders for inspecting the most complex of geometries. Contact us to flex your next inspection with Eddyfi Technologies’ adaptable ECA technology!