Table of Contents
- Efficient hydrocarbon separation processes
- Optimizing Separation: Advanced innovations and technologies
- The importance of hydrocarbon separation
- What is energy efficiency?
- What are the advantages of energy efficiency?
- Data of interest
- Success stories
- Future prospects: Towards cleaner and more efficient energy
- Conclusion
- References
The Refinery is the industrial facility where crude oil is subjected to physical and chemical transformation processes for the efficient separation of hydrocarbons into chemical compounds and derivatives and other petrochemical products of greater market value, complying with technical, environmental, quality, and operational security.
What products would we be talking about? The truth is that the derivatives are very diverse, ranging from light gases, such as propane and butane, to heavier fractions, such as fuel oil and asphalt, including other products such as gasoline, diesel, and Lubricant oils.
Atmospheric and vacuum distillation processes are the two of the methods for the efficient separation of hydrocarbons. In this article, we will discuss these processes, emphasizing their importance in obtaining high-quality refined products, in order to meet international quality standards.
Efficient hydrocarbon separation processes
Atmospheric distillation process
Atmospheric distillation is an efficient hydrocarbon separation process that is carried out at atmospheric pressure. In this process, the crude oil is preheated in shell and tube heat exchangers and finishes heating in a furnace up to a certain temperature, and is sent to the fractionation tower; where the different components boil and vaporize. The vapors are then condensed in a distillation column, where they are separated into different fractions.
Crude oil refining begins with the distillation of incoming crude oil in the atmospheric distillation tower, which operates at pressures slightly above atmospheric pressure. Lighter fractions, such as gasoline and diesel, are obtained at the top of the column. The heavier fractions, such as fuel oil and asphalt, are obtained at the bottom. Figure 1 shows an image of an atmospheric distillation unit.
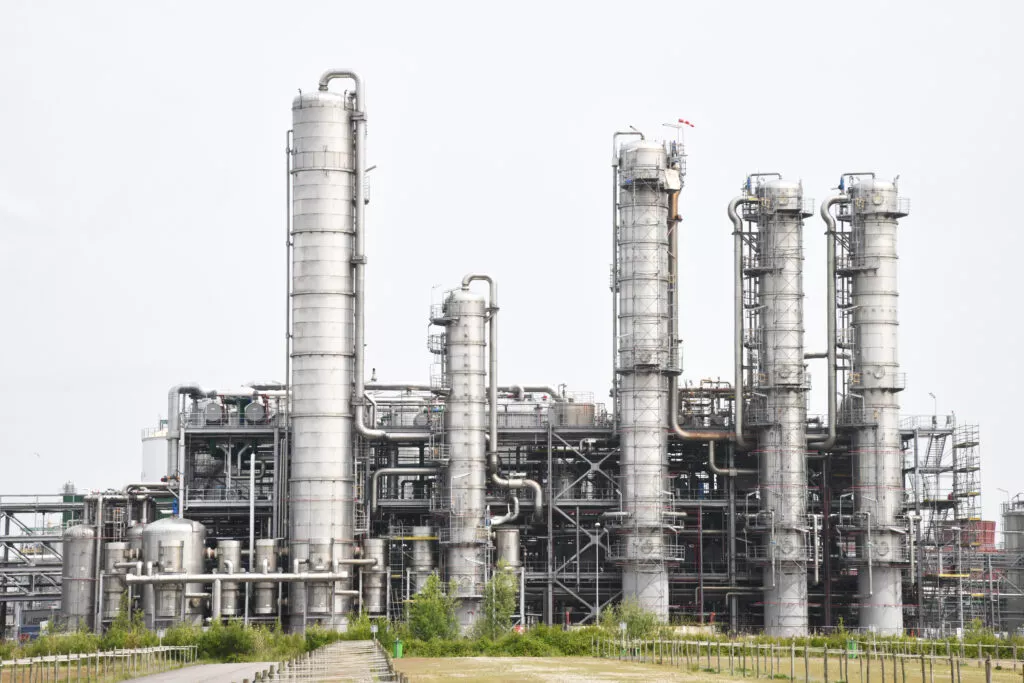
Vacuum Distillation Process
Vacuum distillation is an efficient hydrocarbon separation process that is carried out at pressures below atmospheric. In this process, the crude oil is heated until the different components boil and vaporize. However, the lower pressure causes the boiling points of the components to be lower, allowing the heavier fractions of the crude oil to be separated.
Vacuum distillation may also be referred to as “low-temperature distillation”. When distilling crude oil, it is important not to subject the crude oil to temperatures above 370 to 380°C because the high molecular weight components in the crude oil will undergo thermal cracking and form petroleum coke at temperatures above that. Heavier fractions, such as asphalt, are obtained at the bottom of the column. Lighter fractions, such as gasoline and diesel, are obtained at the top. A vacuum distillation unit is shown in figure 2.
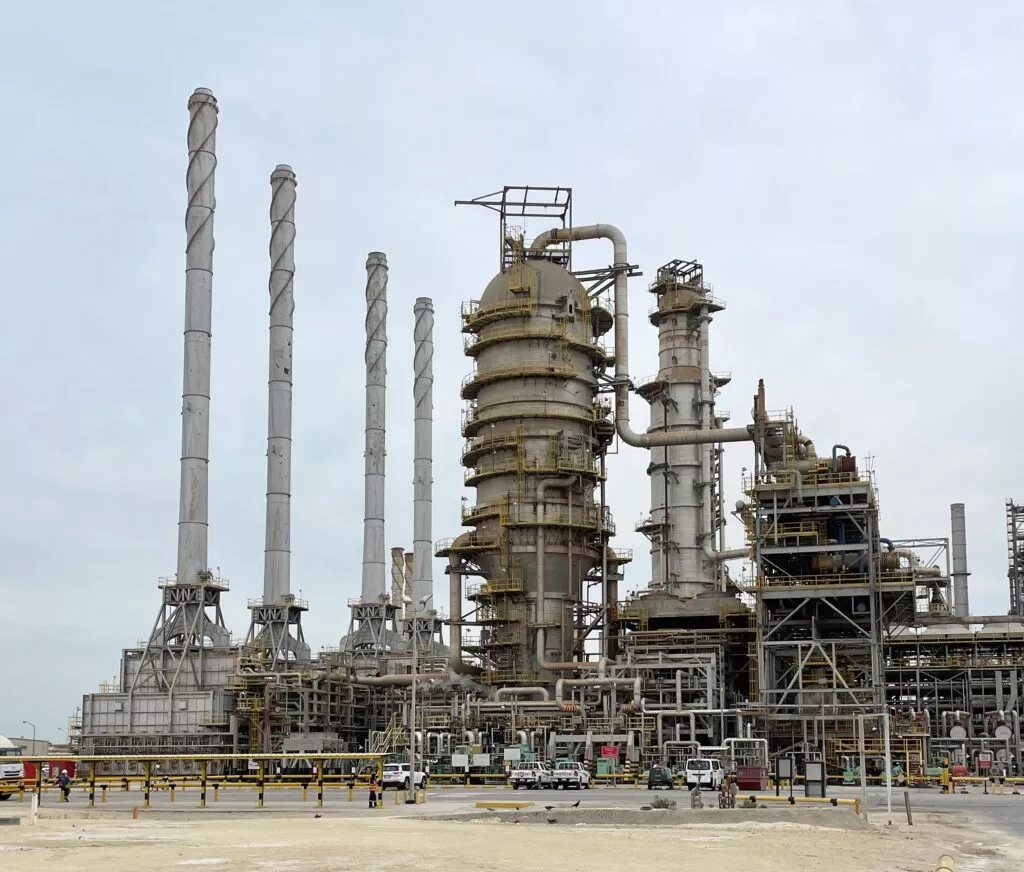
Optimizing Separation: Advanced innovations and technologies
The energy industry is constantly evolving, and distillation processes are no exception. Innovations such as perforated plate distillation columns and thin film heat exchangers are improving efficiency and product quality.
In addition, the use of selective catalysts in vacuum distillation is making it possible to obtain products with specific characteristics, satisfying the changing demands of the market.
The importance of hydrocarbon separation
The separation of hydrocarbons is a fundamental stage in oil refining. This process allows obtaining refined products with the desired characteristics and properties in accordance with international quality standards.
For example, gasoline must have a relatively low boiling point so that it can easily evaporate in the engine. Diesel, on the other hand, must have a higher boiling point so that it can withstand the higher temperatures of diesel engines.
Atmospheric and vacuum distillation processes are essential to obtain high-quality refined products. These processes make it possible to separate hydrocarbons of different molecular weights and characteristics, resulting in refined products with the desired properties and applications.
What is energy efficiency?
The concept of energy efficiency refers to the ability to obtain the best results in any activity using the least possible amount of energy resources. It allows to reduce the consumption of any type of energy and with it the possible environmental impacts associated with it. This is applicable from the generation of said energy to its final consumption.
With the efficient separation of hydrocarbons, it is therefore a question of maintaining the same performance of the activity, but incorporating a series of sustainable management models, responsible habits, and investments in technological innovation.
What are the advantages of energy efficiency?
Investing in measures that improve energy efficiency has very positive effects in all areas. These are some of the main benefits it presents:
- Energy and cost savings
Using fewer energy resources to carry out an activity saves energy. In addition, lower energy consumption translates into a reduction in the energy bill.
- Improvements for the environment
Energy efficiency lowers greenhouse gas emissions. With the responsible use of energy, fewer resources are consumed, which contributes to reducing the carbon footprint.
- Sourcing improvements
Energy efficiency allows us to optimize the use of natural resources. and create a local economy, thereby promoting responsible consumption.
Data of interest
- Atmospheric distillation is the most widely used hydrocarbon separation process in oil refineries. It is estimated that it represents around 80% of the total production of refined products.
- Vacuum distillation is used to process heavy cuts of crude oil that cannot be efficiently separated by conventional atmospheric distillation.
- Atmospheric and vacuum distillation processes are responsible for the production of most refined products, such as gasoline, diesel, jet fuel, lubricants, plastics, etc. Therefore, a reasonable estimate of the percentage that atmospheric and vacuum distillation processes represent of the total production of refined products is 95% or more.
Success stories
- In 2023, the Pemex oil refinery in Salina Cruz, Mexico, implemented a new atmospheric distillation process that improved the quality of gasoline and diesel produced at the refinery.
- In 2022, Shell’s oil refinery in Rotterdam, the Netherlands, implemented a new vacuum distillation process that reduced greenhouse gas emissions from the refinery.
- Repsol and energy efficiency. Energy efficiency is one of the ways with the greatest potential to mitigate greenhouse gas emissions.
- Repsol has a decarbonization strategy that includes all available technologies, including the so-called disruptive technologies, and whose lines of work include energy efficiency, generation and self-consumption of renewable electricity, renewable hydrogen, circular economy solutions, and synthetic or low carbon footprint fuels.
- Among its objectives to reach zero net emissions in 2050 is the integration of renewable energies in our processes and the implementation of systems and tools that improve the efficiency of industrial facilities. In this way, we will be able to make our processes more efficient and our activity less carbon-intensive.
Future prospects: Towards cleaner and more efficient energy
As the world strives for an energy transition to cleaner energy sources, efficient hydrocarbon separation remains vital. Current research is focused on greener distillation techniques and optimizing by-product recovery, such as carbon capture and waste reuse.
These advances will not only increase efficiency but also reduce the industry’s environmental footprint; Cases on this topic are promoted by the Repsol company, such as:
- RepHEN (Repsol Heat Exchanger Network). This project offers an innovative solution to the problem of fouling in heat exchangers.
- Replacement of compressors and other equipment. The implementation of new, more efficient, high-tech compressors will allow a greater reduction in CO2 emissions.
- Improvement of efficiency in furnaces. Installation of air pre-heaters equipped with the latest technology in refinery process furnaces.
In short, the refinery of the future is a key agent to continue advancing in the transition towards a low-emissions future: a complex, sophisticated, and adapted refinery, which must continue working to increase the efficiency of its operations.
All this in terms of reducing CO2 emissions by improving their energy management systems and adopting new technologies; a refinery that has to maintain its investments for the production of eco-fuels and other products with a low carbon content; and a refinery that is committed to the expansion, deepening and development of collaborative projects with other industries that allow the reduction of emissions throughout the production chain.
Conclusion
In summary, the atmospheric and vacuum distillation processes are based on the difference in boiling points of the different components of crude oil. Atmospheric distillation is carried out at atmospheric pressure, while vacuum distillation is carried out at reduced pressure. Both processes make it possible to obtain a wide range of refined products, which are essential for transport, heating, and industry.
The efficient separation of hydrocarbons through atmospheric and vacuum distillation processes is an essential pillar in oil refining. These methods have proven their ability to produce high-quality refined products that power our modern society.
As the energy industry advances, innovations continue to reshape these processes, promising a cleaner, more efficient future. The importance of these techniques in obtaining refined products with precise and adequate specifications is undeniable, and their role in the energy industry continues to be essential in a constantly changing world.
“The processes that transformed today’s society!”
References
Own source