Table of Contents
- What is dezincification?
- Conditions favoring each type
- Relevance for early detection and material design
- What Causes Dezincification of brass?
- Signs and consequences of dezincification
- Early detection methods for dezincification
- How to prevent dezincification of brass?
- Common design or maintenance errors that promote dezincification
- How to reverse or repair dezincification
- Real-world applications and case studies
- International standards and regulations
- Conclusions
- References
Corrosion is a critical concern in the durability and reliability of metallic components, especially those exposed to aggressive environments. One particularly insidious form of corrosion affecting copper-zinc alloys is dezincification. This phenomenon leads to the premature degradation of brass, a widely used material in plumbing systems, industrial piping, marine hardware, and various mechanical fittings.
Dezincification, a type of galvanic corrosion, can cause significant structural and functional failures, often going unnoticed until visible damage or leakage occurs. As infrastructure ages and environmental conditions become more demanding—such as the presence of carbon dioxide, chlorides, or soft water—the risk of this localized corrosion type increases.
This article explores in depth what dezincification of brass is, its underlying mechanisms, the causes, and the strategies to prevent it, providing essential knowledge for engineers, maintenance professionals, and material specialists seeking to enhance the lifespan and performance of brass components.
What is dezincification?
Dezincification is a form of selective leaching where zinc is removed from brass alloys, leaving behind a spongy, porous matrix of copper. This process occurs when brass is exposed to certain corrosive environments, particularly those involving stagnant or mildly acidic water, high chlorides, or carbon dioxide. Over time, the loss of zinc transforms the alloy’s microstructure, severely degrading its mechanical strength and visual appearance.
I want to highlight the term stagnant water as the water that does not circulate, is retained in pipes or equipment and therefore, can increase the contact time with metal surfaces and favor corrosive environments (such as accumulation of CO₂, chlorides, or pH drop). Over time, the loss of zinc transforms the microstructure of the alloy, severely degrading its mechanical strength and visual appearance.
From a metallurgical standpoint, dezincification is a dealloying corrosion mechanism, and more specifically, a form of galvanic corrosion between zinc and copper in the brass alloy, where the more reactive element (zinc) is preferentially dissolved. The result is a weakened, brittle layer composed mostly of copper, often with a pinkish hue, which is both mechanically fragile and prone to further corrosion.
The answer to “what is dezincification?” lies not just in its chemistry, but in its impact: it compromises the integrity, conductivity, and pressure tolerance of brass components. In critical applications like dezincification brass valves or fittings in plumbing systems, this corrosion can lead to sudden failures, water contamination, or costly replacements.
Preventing dezincification brass degradation is thus essential in systems where long-term durability and corrosion resistance are vital.
Types of dezincification: Uniform vs. Localized
This form of corrosion occurs in alloys containing one metal less noble than the other. In this case the less noble element is removed from the more noble material, leaving a porous material with very low strength and ductility. The most common example of selective corrosion is the dezincification of brass (Zn-Cu), which occurs by removal of zinc from the alloy. Zn-depleted regions show a characteristic reddish color in contrast to the original yellow brass.
Brass dezincification can be classified into two main types:
a. Uniform dezincification, which occurs in the presence of high Zn content and acidic solutions. b. Localized dezincification, which occurs in the presence of lower Zn content and in neutral, alkaline and slightly acidic solutions.
Both corrosion processes can be seen in the following image.
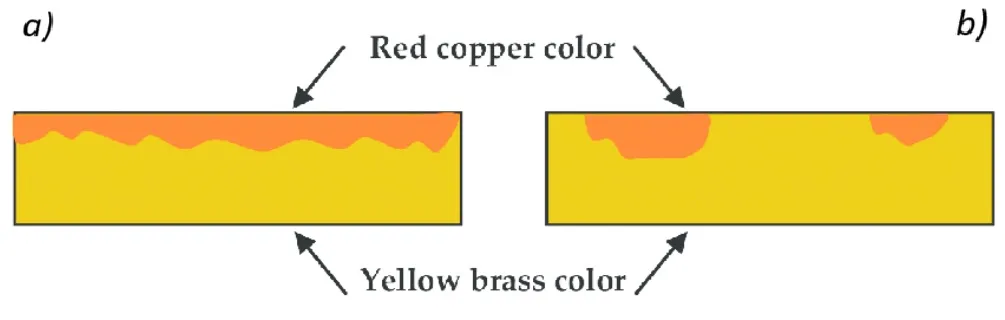
Uniform dezincification
This type of attack is characterized by a gradual and widespread loss of zinc across large surface areas of the brass component. Although the damage may appear superficial, the progressive leaching of zinc creates a weakened copper-rich microstructure with a porous and spongy texture, compromising mechanical integrity over the medium to long term.
Characteristics:
- Affects large areas evenly.
- Strength loss is progressive but less catastrophic in the short term.
- Commonly associated with prolonged exposure to soft, slightly acidic water or water with low chloride content.
Practical implication:
Although it may initially go unnoticed, uniform dezincification shortens the component’s service life and can lead to structural collapse if not detected in time.
Localized dezincification (plug-type)
In this case, the attack is severe and concentrated, forming deep cavities or “corrosion plugs” in specific areas of the component. These patches can detach, leaving critical voids in the material wall, significantly increasing the risk of sudden failures such as leaks, cracks, or rupture under pressure.
Characteristics:
- Corrosion is concentrated in isolated zones.
- Severe structural damage at specific points, even if the rest of the part appears intact.
- Often triggered by stagnant water, high chloride concentrations, or the presence of dissolved carbon dioxide.
Practical implication:
This type of attack is particularly dangerous, as it can cause unexpected and localized failures in valves, couplings, and pipes—especially in hot water systems or poorly designed hydraulic networks.
Conditions favoring each type
Type of dezincification | Favorable conditions |
Uniform | Soft water, low acidity, continuous flow, moderate temperature |
Localized | Stagnant water, high acidity, dissolved CO₂, high chlorides, low-flow zones |
Relevance for early detection and material design
Understanding the type of dezincification helps tailor the inspection methods: Uniform dezincification may require thickness measurements or sampling for metallographic analysis; localized dezincification on the other hand, calls for techniques such as indirect visual inspection (borescope inspection), radiography, or dye penetrant testing, which can detect hidden cavities.
In terms of material design, identifying the most likely type of attack allows selection of the appropriate alloy (e.g. DZR CW602N brass for critical conditions), application of protective coatings and more accurate preventive monitoring protocols.
What Causes Dezincification of brass?
Dezincification occurs due to a selective leaching mechanism, where zinc is preferentially dissolved from brass when exposed to corrosive environments. The process is electrochemical and is triggered when brass components come into contact with water containing oxygen, chlorides, carbon dioxide (CO₂), or even low pH (acidic) conditions.
The primary driver of dezincification is galvanic corrosion, causes dezincification of brass is the galvanic difference between copper and zinc in the alloy. In the presence of electrolytes—such as soft water, distilled water, or lightly acidic water—zinc ions tend to migrate out of the brass matrix, leaving behind a weakened, copper-rich layer.
Environmental contributors that accelerate dezincification include:
- Soft or demineralized water lacking buffering minerals.
- High chloride concentrations, common in marine atmospheres.
- Dissolved CO₂, which lowers pH and increases corrosion rates.
- Poor flow conditions, such as stagnant water in plumbing systems.
Real-world examples of galvanic corrosion through dezincification are often seen in domestic plumbing, especially in older homes with non DZR brass fittings, and in marine components such as valves and propellers exposed to seawater. The result is not only visual degradation but a profound loss of structural integrity, which can lead to catastrophic failures if left untreated.
The illustration shows a brass alloy pipe exposed to an aggressive aqueous environment containing chlorides (Cl⁻), carbon dioxide (CO₂), and acidic pH, which promote the leaching of zinc (Zn). As zinc ions (Zn²⁺) migrate into the surrounding environment, the brass structure transforms into a porous, copper-rich matrix, significantly weakening the material. The flow arrow indicates the movement of the corrosive medium through the component.
Signs and consequences of dezincification
Identifying dezincification early is key to preventing serious damage. Common visual and physical signs include:
- A pinkish or reddish discoloration on the brass surface due to remaining copper.
- A porous, spongy texture upon inspection or when the material is scraped.
- Noticeable loss of strength, with components becoming brittle and fragile.
In plumbing systems, these signs may indicate that a fitting or valve is at risk of leaking or bursting, especially under pressure. The risk increases in hot water circuits and stagnant sections of pipework.
The economic consequences are significant. Undetected dezincification can lead to water damage, system downtime, expensive repairs, or even health and safety hazards due to water contamination. For industries or municipalities, this translates into maintenance costs, regulatory non-compliance, and public safety concerns.
Early detection methods for dezincification
Early detection of dezincification is essential to prevent catastrophic failures, reduce maintenance costs, and ensure the operational reliability of systems. Since this type of corrosion can progress silently and internally affect the brass microstructure before becoming visible on the surface, it is necessary to apply specific inspection techniques—both destructive and non-destructive (NDT).
Visual inspection and surface evaluation
Although limited, a careful visual inspection can reveal early signs such as:
- Reddish or pink discoloration (indicates surface copper accumulation).
- Loss of luster or a matte appearance in typically polished areas.
- Presence of surface cracks or flaking material.
Advantage: Fast and low-cost method.
Limitation: Does not detect internal damage or hidden critical areas.
Destructive testing and metallography
In selected components or in laboratory settings, the following can be applied:
- Cross-sectional cutting of the material and analysis under an optical microscope.
- Chemical etching to reveal the copper-rich matrix.
- Identification of microcracks, porosity, or zinc-depleted areas.
Advantage: Allows confirmation of the type and severity of dezincification.
Limitation: Not applicable in service; requires sample extraction.
Non-Destructive Testing (NDT)
Ideal for field inspections or on components in service.
a) Ultrasonic Thickness Measurement
- Detects structural material loss in critical areas.
- Useful for comparing suspect zones with reference sections.
b) Industrial Radiography (RT)
- Enables visualization of internal cavities caused by localized dezincification.
- Requires access and compliance with radiological safety procedures.
c) Liquid Penetrant Testing (PT)
- Ideal for revealing surface cracks resulting from compromised brass integrity.
- Complements visual inspections.
d) Borescope Inspection
- Involves inserting a camera into valves, pipes, or couplings.
- Allows real-time observation of internal damage, erosion zones, or abnormal discoloration.
Advanced laboratory techniques
When a detailed diagnosis is required, elemental characterization methods can be applied:
- Scanning Electron Microscopy (SEM): Reveals corroded microstructure and associated porosity.
- Energy Dispersive X-ray Spectroscopy (EDS or EDX): Confirms zinc loss and copper enrichment.
- Elemental mapping: Evaluates the distribution of zinc and other elements to quantify damage levels.
Recommended strategy
Application | Suggested method |
Preventive field inspection | Visual + Ultrasonic + Borescope |
Detailed laboratory diagnosis | Metallographic sectioning + SEM + EDX |
Critical failure assessment | Industrial radiography + Metallographic analysis |
How to prevent dezincification of brass?
Understanding how to prevent dezincification of brass begins with material engineering. One of the most effective strategies is using dezincification-resistant brass (DZR brass), such as alloys conforming to standards like EN 12165 CW602N or ASTM B887. These alloys contain small amounts of arsenic, tin, or phosphorus, which stabilize the microstructure and reduce zinc leaching.
In this video, courtesy of Boshart Industries, you’ll find a simple explanation of what dezincification is, how to identify it, and which materials—such as stainless steel or DZR brass—can help prevent it.
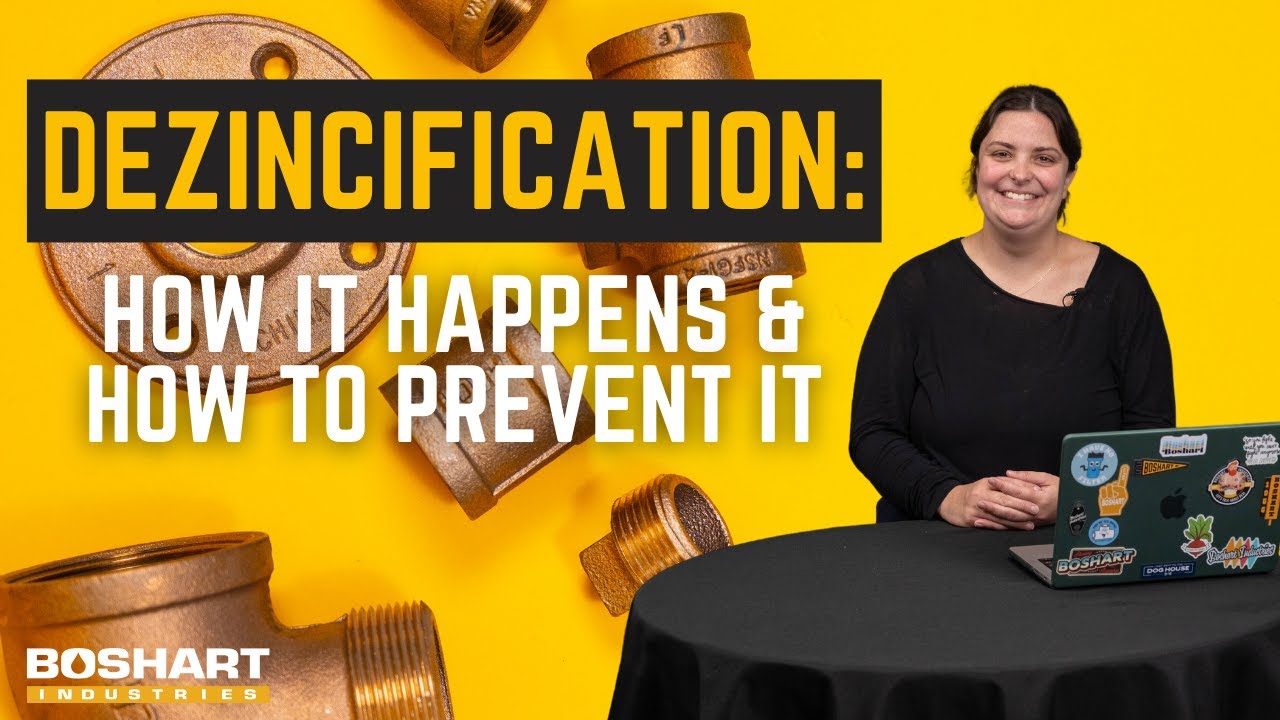
Additional prevention methods include:
- Water treatment & environmental control
- Neutralizing soft or acidic water via pH adjustment or mineral enrichment.
- Reducing chloride and CO₂ concentrations in water systems.
- Ensuring proper flow rates to avoid stagnant zones.
- Smart material selection
- Avoid using standard brass in critical applications such as marine valves, industrial pumps, or high-temperature circuits.
- Specify DZR brass for fittings in hot water plumbing systems or areas prone to galvanic corrosion.
- Surface protection
- Apply corrosion-resistant coatings such as epoxy paints or polyurethane linings.
- Use cathodic protection in large-scale industrial or marine settings.
Selecting appropriate materials and implementing preventive strategies can significantly extend the lifespan of brass components and help mitigate galvanic corrosion caused by dissimilar metal reactions in aggressive water environments. The use of innovative materials specifically designed to resist zinc leaching and galvanic corrosion represents a key advancement in the engineering of long-lasting systems
Common design or maintenance errors that promote dezincification
In both industrial and residential settings, many severe cases of dezincification are not solely caused by adverse environmental conditions, but rather by inadequate decisions in system design, material selection, or maintenance practices. Understanding these recurring mistakes is essential to prevent costly failures and ensure the durability of brass components in service.
Using standard brass in soft or chlorinated water environments
One of the most frequent mistakes is using standard (non DZR) brass in applications where the water chemistry promotes zinc leaching:
- Soft or demineralized water: lacks buffering minerals, fostering slightly acidic environments.
- Chlorinated water: chlorine and its derivatives accelerate localized corrosion.
Consequence: Standard brass is highly susceptible to dezincification under these conditions, especially when in continuous contact with stagnant or hot water.
Recommendation: Specify DZR (Dezincification Resistant Brass) certified to standards such as EN 12165 CW602N or ASTM B887 to ensure proven resistance.
Ignoring water chemistry during hydraulic design
Many systems are designed without a preliminary analysis of the water that will circulate through them, overlooking critical factors such as:
- pH
- Alkalinity
- Dissolved chlorides and sulfates
- Free CO₂
Consequence: The corrosive potential of the medium is underestimated, leading to poor material selection or insufficient protective design.
Recommendation: Include water chemical analysis as a mandatory step in the design process. This information helps define the need for corrective treatments, resistant alloys, or protective coatings.
Overlooking temperature and pressure limits of the material
Brass has a safe operational range, yet it is often used in systems that:
- Exceed 70–80 °C (temperatures that accelerate corrosion and zinc diffusion).
- Operate under high pressure without accounting for internal wall thinning due to corrosion.
Consequence: The combination of heat, pressure, and internal dezincification can lead to sudden ruptures, especially in valves, nipples, and soldered or threaded fittings.
Recommendation: Consult the manufacturer’s technical datasheets, verify pressure–temperature ratings, and avoid using standard brass in hot water or steam systems.
Lack of preventive maintenance in valves and piping
Many systems operate for years without internal inspections, cleaning, or pressure testing, allowing dezincification to progress undetected.
Commonly ignored warning signs:
- Unexplained pressure loss
- Minor intermittent leaks
- Discoloration in the water
Consequence: By the time the issue is detected, the component has already lost structural integrity and requires full replacement, increasing costs and downtime.
Recommendation: Implement a preventive maintenance program that includes:
- Internal visual inspection using a borescope
- Pressure testing
- Periodic replacement of fittings in critical areas
- Historical tracking of materials, water quality, and service life
Summary of best practices
Common error | Recommended action |
Use of standard brass in soft/chlorinated water | Use certified DZR brass |
Ignoring water chemistry | Perform water analysis during design |
Exceeding operational limits | Verify temperature/pressure specifications |
Lack of maintenance | Establish periodic inspection programs |
How to reverse or repair dezincification
A common question is how to reverse dezincification of brass, especially in domestic and industrial applications. Unfortunately, dezincification is not practically reversible. Once zinc has been leached out of the brass alloy, the resulting copper-rich structure is brittle, porous, and mechanically compromised.
In most cases, replacement of the affected component is the safest and most cost-effective solution. Attempting to reinforce or recoat a severely dezincified part is discouraged due to its loss of structural integrity.
Maintenance protocols and consumer guidance
For industrial applications, regular inspection schedules and preventive maintenance can identify early signs of dezincification, such as discoloration, surface pitting, or reduced pressure performance in plumbing systems.
For homeowners curious about how to reverse dezincification of brass at home, there is no DIY fix once the damage is advanced. However, early replacement with DZR brass fittings and filtration to control water chemistry can prevent recurrence.
Routine flushing of stagnant water lines, use of corrosion inhibitors, and water quality testing are practical preventive steps. In short, proactive replacement, not repair, remains the industry standard.
Real-world applications and case studies
Dezincification has been documented in a variety of industrial and residential contexts. In plumbing systems, it’s frequently observed in older homes with standard brass fittings exposed to soft or chlorinated water. Failures in valves and couplings can result in leaks and water damage.
In desalination plants, the high chloride content of seawater presents an aggressive environment. The use of DZR brass and polymer-coated fittings has significantly increased equipment longevity and reduced maintenance costs.
HVAC systems also face corrosion risks due to condensation, stagnant water, and high humidity. In these systems, dezincification-resistant components are used in chillers, heat exchangers, and valve assemblies to prevent mechanical failure.
Testing and verification methods
- Metallographic analysis reveals the characteristic copper-depleted structure.
- Scanning Electron Microscopy (SEM) offers detailed imaging of porosity and microcracks.
- Energy-dispersive X-ray spectroscopy (EDX) confirms zinc loss at the elemental level.
These diagnostic tools are crucial in failure analysis and in validating the effectiveness of corrosion-resistant materials in the field.
International standards and regulations
Compliance with international technical standards is a fundamental pillar in the selection, manufacturing, and application of brass components, especially in environments where dezincification poses a critical risk. These standards ensure that the alloys used meet strict requirements for chemical composition, mechanical performance, and corrosion resistance, facilitating reliable and traceable engineering decisions.
ASTM Standards (American Society for Testing and Materials)
- ASTM B858 – Standard Test Method for Determination of the Resistance of Copper Alloys to Dezincification: Specifies the procedure for accelerated testing of dezincification resistance. It is used to validate materials through immersion in controlled corrosive solutions.
- ASTM B887 – Standard Specification for Brass, High Strength, Dezincification Resistant (DZR): Defines brass alloys specifically formulated to resist zinc leaching, including those with small amounts of arsenic, tin, or phosphorus. It covers applications such as hot water systems, valves, and critical fittings.
- ASTM B927 – Standard Specification for Brass Rod, Bar, and Shapes for Forging and Extrusion (DZR): Applies to mechanically worked materials such as rods or shaped sections used in forged or extruded components. Includes quality control and composition criteria to ensure corrosion resistance.
EN Standards (European Norms)
- EN 12164 / EN 12165 / EN 12167 / EN 1982: These standards cover different forms of brass products (rods, extrusions, castings), including the CW602N alloy, which is best known for its dezincification resistance.
- CW602N: Contains arsenic as a leaching inhibitor, ideal for potable water systems and aggressive environments.
- EN ISO 6509-1 – Determination of dezincification resistance of brass: Defines the standardized method for evaluating brass resistance to dezincification, based on immersion tests and subsequent metallographic analysis.
Conclusions
Brass dezincification represents a silent yet devastating threat to the integrity of components in hydraulic, marine, and industrial systems. This phenomenon, driven by corrosive environments and poor material selection, can lead to unexpected mechanical failures, significant economic losses, and safety risks.
Although dezincification cannot be reversed, it can be prevented. The use of dezincification-resistant brass (DZR), proper water treatment, surface protection, and continuous monitoring are essential practices to extend the service life of systems and equipment. Understanding and applying these strategies not only mitigates risks but also strengthens operational reliability in sectors where every component matters.
Beyond technical performance, preventing dezincification and galvanic corrosion also contributes to sustainability. Frequent leaks and replacements result in water waste, metal scrap generation, and increased energy consumption. By using DZR materials and maintaining a proactive management approach, operational integrity is preserved while actively supporting resource efficiency, environmental impact reduction, and asset life cycle extension.
In a world where infrastructure is aging and operating conditions are increasingly demanding, preventing dezincification is not an option—it is a technical, economic, and environmental necessity.
References
- Dezincification by AMPP. https://www.ampp.org/technical-research/what-is-corrosion/forms-of-corrosion/dezincification?utm_source=chatgpt.com
- Dinnappa, R.K., and S.M. Mayanna. “The Dezincification of Brass and Its Inhibition in Acidic Chloride and Sulphate Solutions.” Corrosion Science 27,4 (1987).
- Dean, J.A. Lange’s Handbook of Chemistry, 14th ed. New York, NY: McGraw-Hill, 1992.
- Wieland Chase Explains Processes Leading to Improved Dezincification-Resistance by Larry Muller, Senior Technical Advisor, Wieland Chase, LLC