Table of Contents
- introduction
- Consequences of negative impact of corrosion in industry
- Corrosion resistant materials
- Smart Coatings: Advanced Corrosion Protection
- Real-time monitoring technologies: Detect and prevent corrosion
- Corrosion Failure Analysis: Understanding the Challenges and Advancing Solutions
- Conclusion
- Bibliographic references
introduction
Corrosion in industry can have devastating consequences that can cause problems in structures and equipment. From material degradation to costly downtime, corrosion can significantly affect the profitability and safety of businesses.
Physically, sometimes a faulty structure cannot be seen, but it may have cracks that cannot be seen with the naked eye, generating a dangerous situation; that can cause a catastrophe depending on its size, location and service.
In this context, it is exposed how current innovations in the field of prevention and treatment of corrosion in industry are revolutionizing the energy sector among others. From the use of more resistant materials to the application of intelligent coatings and the use of data detection technologies in real time, the methods and control to mitigate the advance of corrosion, protecting assets, reducing costs and strengthening resilience in the industry.
Corrosion is a destructive phenomenon that affects many industries, such as oil and gas. Its effects can be catastrophic, causing significant financial loss, prolonged downtime and, in extreme cases, serious accidents.
Consequences of negative impact of corrosion in industry
- Economic losses: According to studies, it is estimated that the losses caused by corrosion in the oil and gas industry exceed 1.4 trillion dollars annually. These costs are due to repairs, equipment replacement, lost production, and downtime.
- Reduction of the useful life of the equipment: Accelerates the process of degradation of the equipment, decreasing its useful life. Exposed to corrosive environments, such as pipelines, storage tanks, metal structures, and drilling equipment, they are subject to premature wear and require frequent replacement. This generates high maintenance costs and affects operational efficiency.
- Safety risks: Structural weakening caused by corrosion often leads to catastrophic failure of equipment and structures, increasing the risk of accidents, releases of hazardous substances, and spills. These incidents can have significant environmental and human consequences.
- Impact on production: Corrosion can disrupt production and cause costly downtime. Equipment damaged or out of service due to corrosion must be repaired or replaced, resulting in a decrease in production capacity. In addition, the need for frequent inspection and maintenance to control corrosion can also affect productivity.
- Offshore Infrastructure Challenges: In the oil and gas industry, subsea and offshore structures are exposed to highly corrosive environments. Corrosion on subsea platforms, pipelines and equipment can be especially challenging due to extreme conditions, such as the presence of salt water and exposure to marine life. These challenges require effective solutions to ensure the integrity and security of the facilities.
Corrosion resistant materials
Among the latest developments in the fight against corrosion is the improvement of more corrosion resistant materials. Industry leading companies such as Acme Industries, Inc. and Global Metals, have invested in the research and creation of special alloys that offer greater resistance to corrosion. Here are some of the most corrosion resistant materials 1 .
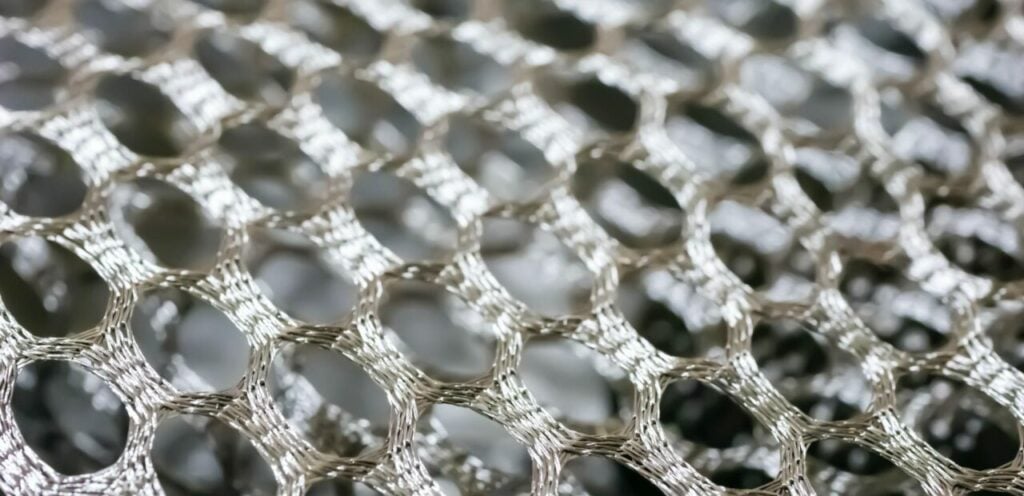
- Stainless Steel Alloys: In recent years, more corrosion resistant stainless steel alloys have been developed, such as duplex stainless steel and super duplex stainless steel, which offer higher corrosion resistance and higher mechanical strength. Its use has allowed reducing maintenance costs and prolonging the useful life of subsea structures in the oil and gas industry.
- Nickel Alloys: Nickel alloys, such as inconel and monel, are known for their high corrosion resistance in extremely corrosive environments, such as high temperatures and acidic media. These alloys are widely used in the oil and chemical industry, where they are exposed to severe corrosion conditions.
- Composite materials Composite materials, such as glass fiber reinforced polymers (GRP) and carbon fiber reinforced polymers (CFRP) 1 , offer high corrosion resistance and excellent mechanical strength. These materials are widely used in applications where high structural strength and corrosion protection are required, such as in the manufacture of pipes and tanks.
These are just some of the outstanding innovations, trends and technologies in the field of corrosion resistant materials. Research and development continue to advance in this field, with the aim of further improving the corrosion resistance of materials and ensuring greater durability in challenging environments.
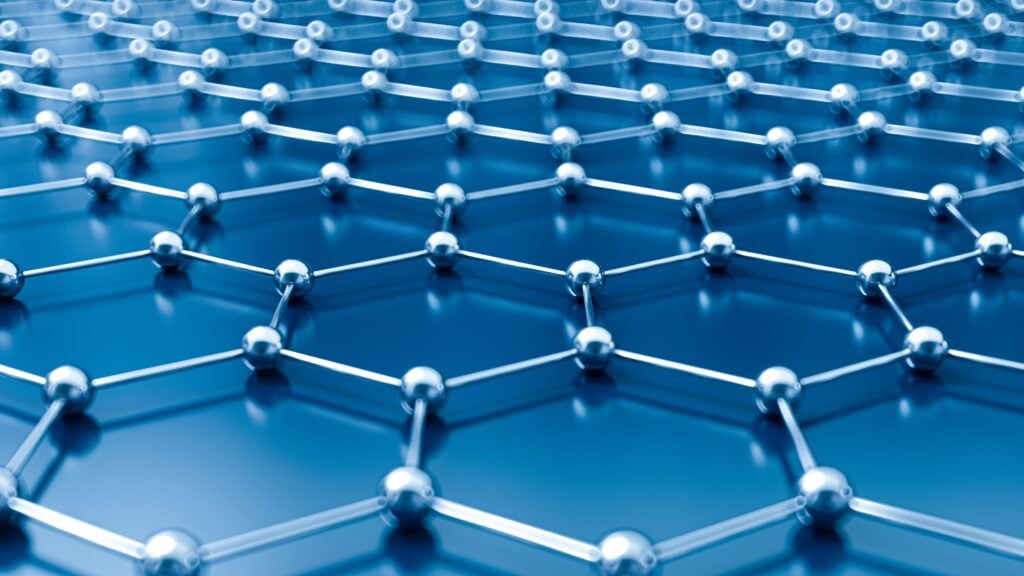
Smart Coatings: Advanced Corrosion Protection
Smart coatings have revolutionized corrosion protection in the industry. These advanced coatings offer a highly effective protective layer that adapts and responds to changing environmental conditions, providing a long-lasting barrier against corrosion. Here are some of the most prominent innovations and technologies in the field of smart coatings:
- Self-healing coatings: Self-healing coatings are capable of repairing small cracks and surface damage as they occur. These coatings contain active materials that activate when a crack occurs, filling the crack and restoring the integrity of the protective layer. This prevents corrosion from spreading and extends the life of the structure.
- Controlled Release Inhibitor Coatings: Smart coatings can release inhibitors in a controlled manner over time, ensuring continuous and effective corrosion protection. In this sense, the great development of nanotechnologies has opened up a range of possibilities in the field of anticorrosive paints, offering the possibility of integrating nanocontainers loaded with active and encapsulated components into coatings.
- By means of a suitable capsule design, the release of the corrosion inhibitor can be caused by different external or internal factors (pH changes, mechanical damage, etc.), avoiding the spontaneous leakage of the active component and thus achieving a higher efficiency. and economy in the use of the inhibitor, which is only released on demand in the affected area.
- Active coatings against pH changes: pH changes can influence the corrosion of materials. Smart coatings can adjust their chemical composition and properties in response to changes in pH, allowing them to adapt to different conditions and provide optimal corrosion protection.
- Self-cleaning coatings : The accumulation of dirt and contaminants on the surface of materials can accelerate corrosion. Self-cleaning smart coatings use technologies such as hydrophobicity and photocatalysis to autonomously remove contaminants. This helps keep the surface clean and prevents corrosive agents from adhering to and damaging the material.
- Coatings with built-in corrosion sensors: Some smart coatings are equipped with built-in corrosion sensors that monitor the corrosion status in real time. These sensors can detect changes in electrical potential, impedance, or other surface properties and send alerts when signs of corrosion are detected. This allows a quick and precise intervention to prevent the advance of corrosion.
Smart coatings are a promising innovation in corrosion prevention. Using technologies such as nanotechnology and self-healing materials, these coatings adapt to changing conditions and offer long-lasting protection against corrosion.
A prominent case is the development of polymer-based self-healing coatings at Harvard University. These coatings can automatically detect and repair small damage caused by corrosion, thus preventing it from spreading and causing further damage to structures. Companies like CoatingTech and Innovate Coatings are implementing these technologies into industrial applications.
Real-time monitoring technologies: Detect and prevent corrosion
Real-time monitoring technologies play a critical role in detecting and preventing corrosion in industry. These technologies make it possible to continuously and accurately monitor the behavior of materials and structures in corrosive environments, providing greater responsiveness and the ability to take preventive action in a timely manner. Below are some of the most prominent real-time monitoring technologies in the fight against corrosion:
- Corrosion Sensors: Corrosion sensors are devices that detect changes in the electrical potential or impedance of a metal surface, indicating the presence of corrosion. These sensors can be installed directly on structures or equipment and send signals in real time that warn of possible corrosion problems. By constantly monitoring changes in corrosion, preventative measures can be taken before damage becomes significant.
- Real-time ultrasound: The use of real-time ultrasound technology allows for early detection of corrosion in pipes, tanks, and other structures. Ultrasonic devices emit sound waves that penetrate the material and detect any changes in the wall due to corrosion. This allows affected areas to be identified and corrective action taken before serious damage or structural failure occurs.
- Electrochemical Corrosion Analysis : Electrochemical corrosion is a process that involves the flow of electrical current between different regions of a material. Electrochemical monitoring systems allow changes in current flow to be measured and analyzed, providing valuable information on the corrosion status of a structure. These systems can provide real-time data and early warnings about the occurrence of corrosion.
- Coating Thickness Monitoring: Protective coatings play a crucial role in preventing corrosion. Real-time monitoring of the thickness of the coatings makes it possible to identify any deterioration or loss of thickness that could compromise its effectiveness. This is achieved by installing sensors in the linings that measure and transmit thickness data, allowing constant assessment of their integrity and rapid action in the event of wear.
These real-time monitoring technologies are just a few of the many tools available in the fight against corrosion. Its application provides a greater understanding of corrosive processes, allows early intervention, and helps prevent structural damage and failure. By using these technologies proactively, companies in the energy sector can reduce the costs associated with corrosion, minimize downtime and ensure the safety and efficiency of their operations.
Corrosion Failure Analysis: Understanding the Challenges and Advancing Solutions
Corrosion failure analysis is a crucial process to understand the challenges and develop effective solutions in the prevention and mitigation of corrosion in industry. Below we will explore the key issues related to corrosion failure analysis and how they can be addressed:
- Corrosion Cause Investigation: Corrosion failure analysis involves identifying and understanding the underlying causes of corrosion problems. This may include factors such as the presence of corrosive substances, exposure to aggressive environments, defects in protective coatings, and deficiencies in the design or maintenance of structures. Through a thorough evaluation, the root causes of corrosion can be determined and corrective action taken.
- Assessment of extent of damage: Corrosion failure analysis involves assessing the extent of damage caused by corrosion to structures. This involves visual inspection, as well as non-destructive testing and evaluation techniques, such as ultrasound, radiography, penetration tests, among others. By understanding the extent of the damage, the best repair and prevention strategies can be determined.
- Analysis of corrosion mechanisms: It is essential to understand the corrosion mechanisms that are present in a structure to develop effective solutions. This involves analyzing the types of corrosion present, such as uniform corrosion, pitting corrosion, stress corrosion, among others. By understanding the specific mechanisms, prevention and control strategies tailored to each situation can be implemented.
- Identification of solutions and improvements: Corrosion failure analysis provides valuable information to identify necessary solutions and improvements. This may include selecting more corrosion resistant materials, improving protective coatings, adjusting design parameters, and implementing preventative maintenance programs. By addressing the identified deficiencies, recurrence of failures can be prevented and the long-term integrity of structures ensured.
- Documentation and feedback : It is essential to document all corrosion failure analysis data. This allows establishing a historical record of the problems encountered, the solutions applied and the results obtained. Feedback obtained through this process can be invaluable in improving design standards, maintenance practices, and prevention strategies in the industry.
Conclusion
Corrosion is an invisible enemy that threatens many industrial sectors, including the energy sector. According to recent studies, corrosion can represent up to 3% of a country’s gross domestic product (GDP). This degradation of materials can result in millions in losses and jeopardize the safety of operations.
The prevention and treatment of corrosion in the energy industry and other sectors has experienced significant advances in recent years. From the use of stronger materials to smart coatings and real-time monitoring technologies, we are better equipped than ever to combat this invisible enemy. However, there are still challenges that we need to overcome through failure analysis and industry collaboration.
Remember, corrosion may be invisible, but with the right knowledge and solutions, it can be managed under control and ensure a more resilient and sustainable future in the energy industry.
Bibliographic references
- REYES, Y. (2014). “Lighter than plastic and stronger than steel” Consulted on May 20, 2023 from: https://inspenet.com/articulo/materiales-livianos-y-resistentes-como-acero
- Wojciechowski, S. Boczkowska, A; “Intelligent Materials”; Archives Metallurgy and Materials, (2004), 49 (4) 723.