Table of Contents
Introduction
Corrosion prevention in dock pipelines is a matter of safety, efficiency, and environmental responsibility. These steel arteries, or other resilient materials, carry essential fluids like water, fuel, and chemicals, or serve as links connecting ships and land, facing a relentless enemy: corrosion in marine environments. The combination of saltwater, humid air, vibrations, and abrupt temperature changes accelerates metal deterioration, leading to leaks, breaks, and other severe issues with consequences such as high costs, safety risks, environmental damage, and operational disruptions.
For these reasons, the following article presents the most effective strategies in preventing corrosion in dock pipelines. Focusing on the root causes, commonly used advanced solutions, and the importance or benefits of corrosion control systems, and highlighting the latest innovations making a difference.
What are dock pipelines?
These are structures extending from the shore that serve as mooring and boarding points for vessels. They are crucial for maritime commerce, facilitating the transport of goods and people. Dock pipelines play a significant role in this dynamic, carrying fluids necessary for ship operation and cargo handling.
What is corrosion in dock pipelines?
Corrosion is a natural electrochemical process that degrades metals when interacting with the marine environment, leading to corrosion in marine settings. In the case of dock pipelines, the primary factors accelerating corrosion are:
- Saltwater: Sodium chloride in seawater is highly corrosive to metals.
- Moist Air: Air humidity promotes oxide formation on the pipe surface.
- Vibrations: Ship movements and wave action can weaken welds and cause cracks.
- Sudden Temperature Changes: Temperature fluctuations between water and air create material stress that promotes corrosion.
Main causes or factors of corrosion in marine environments
Corrosion in marine environments is a complex process influenced by various environmental and metallurgical factors. Below are the primary factors:
Environmental factors
- Salinity: seawater contains a high concentration of dissolved salts, primarily sodium chloride (NaCl). These salts act as electrolytes, facilitating the flow of electric current and thus accelerating corrosion.
- Dissolved oxygen: Oxygen dissolved in seawater also contributes to corrosion, acting as an oxidizing agent.
- Temperature: The rate of chemical reactions, including corrosion, increases with temperature. Therefore, warmer seawater generally leads to accelerated corrosion.
- pH: Seawater has an alkaline pH (around 8.2), making it more corrosive to certain metals.
- Biofouling: The growth of marine organisms, such as algae and barnacles, on metal surfaces, can create anaerobic microenvironments that promote corrosion.
- Water velocity: Water movement, such as waves or currents, can erode the protective oxide layer that forms on some metals, exposing fresh metal to corrosion.
Metallographic factors
- Metal composition: The chemical composition of the metal plays a significant role in its corrosion resistance. Metals like iron, steel, and aluminum are more prone to corrosion in marine environments than others such as copper or titanium.
- Metal microstructure: Grain size and distribution can also affect corrosion resistance.
- Mechanical stress: Mechanical stresses, such as tension or compression, can damage certain metals.
Other factors
- Structural type: The shape and design of a structure can lead to water stagnation and deposit accumulation, which in turn may influence the corrosion rate.
- Maintenance: Lack of proper maintenance, such as cleaning and painting.
The image shows pipes and fittings in poor condition, with corrosion crust formation, likely due to inadequate maintenance, protective coatings unsuitable for the conditions, or other factors mentioned in this article. This is what should be avoided, as it leads to failures and subsequent losses from inefficient industrial pipeline management.
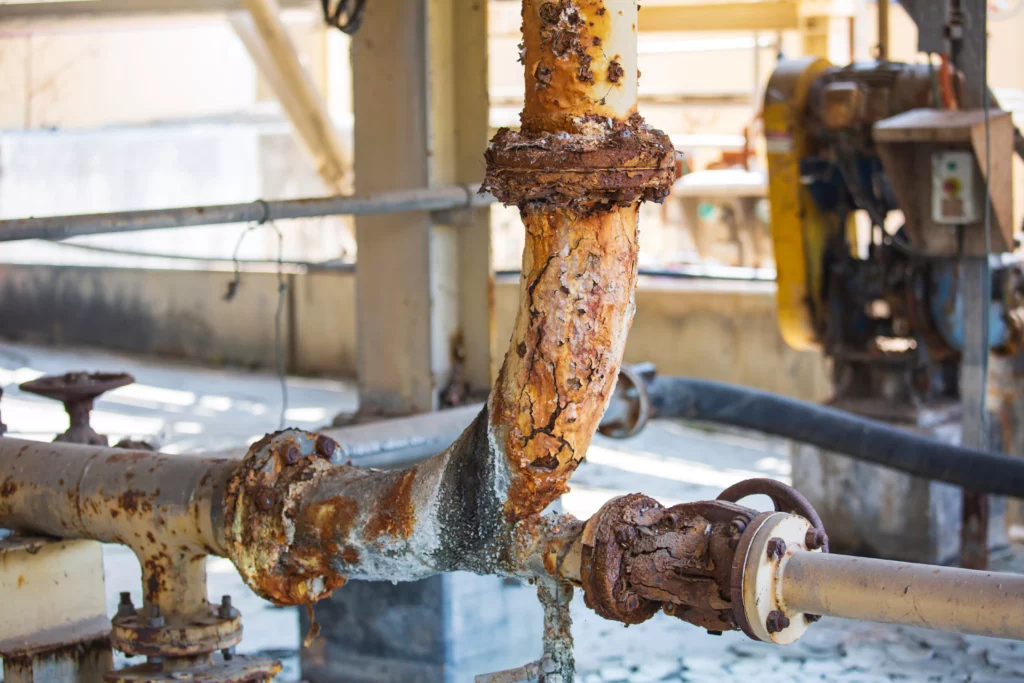
Combining these factors can result in different types of corrosion in marine environments, such as generalized corrosion, pitting corrosion, galvanic corrosion, and erosion-corrosion. It is important to understand the factors causing corrosion in marine environments to select suitable protection methods for structures exposed to this type of environment.
Advanced strategies or solutions for corrosion prevention in dock pipelines
While traditional strategies like selecting resistant materials and protective coatings remain essential, preventing corrosion in dock pipelines requires a more sophisticated approach in an increasingly challenging marine environment. This is where advanced strategies emerge, offering innovative solutions to protect these critical structures and ensure their longevity.
Use of corrosion-resistant materials
The selection of corrosion-resistant materials is a fundamental first step. Commonly used materials include:
- Stainless steel: Offers excellent resistance to chloride corrosion and is a popular choice for dock pipelines.
- Nickel alloys: Alloys like Monel and Hastelloy are highly resistant to corrosion from acids, salts, and other aggressive agents.
- Composites: Composite materials like fiberglass-reinforced plastic (FRP) are lightweight, corrosion-resistant, and offer good durability.
Protective coatings
In addition to material selection, advanced marine coatings can provide an additional layer of corrosion protection. These coatings include:
- Epoxy marine coatings: Resistant to saltwater, chemicals, and abrasion, and offer good adhesion to various materials.
- Zinc coatings: Provide sacrificial cathodic protection, slowly sacrificing themselves to protect the underlying metal.
Maintenance and regular monitoring
Regular inspections and monitoring of dock pipelines are essential to detect early signs of corrosion and take timely preventive measures. These periodic inspections and monitoring techniques include:
- Visual inspections: Identify physical damage such as cracks, pitting, and scaling.
- Ultrasonic testing: Measure remaining pipe thickness, determine corrosion rate, calculate remaining service life, and determine maintenance actions.
- Guided Wave Testing: Assess overall pipeline integrity.
- Cathodic current monitoring: Evaluate the effectiveness of the CP system and make adjustments as needed.
Innovations in anti-corrosion technology
The corrosion prevention industry is constantly evolving, with new technologies offering more effective and durable solutions. Some highly recommended innovations include:
- Nanotechnology coatings: These ultra-thin coatings provide superior corrosion protection and are more resistant to wear.
- Printed cathodic protectors: These compact, cost-effective CP systems integrate easily into existing pipelines.
The following video shows the cathodic protection process, courtesy of: The Professionals.
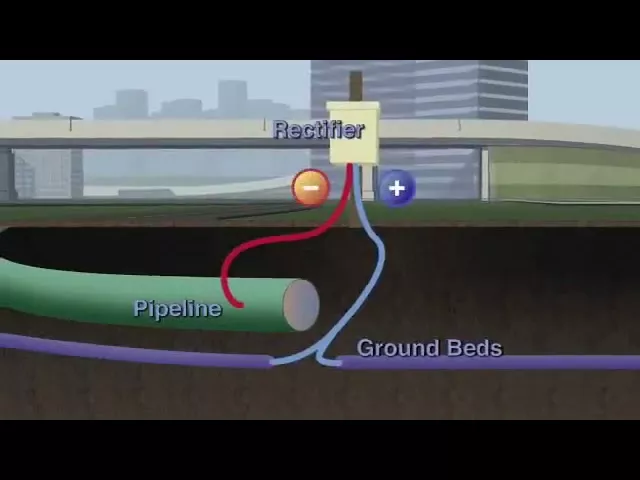
Cathodic protection for pipelines.
- Real-time remote monitoring: Smart sensors enable remote and real-time monitoring of pipeline conditions, facilitating a quick response to any signs of corrosion.
What is the importance or benefits of corrosion control systems in docks?
Preventing corrosion in dock pipeline systems is not a trivial matter, nor is it limited to aesthetic or functional concerns. Its importance lies in protecting critical assets, ensuring safety for people and the environment, and optimizing operational efficiency. The consequences of corrosion in this environment are severe and far-reaching.
- Reduced costs: Minimizes expenses associated with repairs, replacements, and product losses. It’s estimated that corrosion costs the global economy around $2.5 trillion annually, equivalent to about 3.4% of the world’s GDP.
- Improved safety: Reduces risks of accidents related to leaks of hazardous substances. Corrosion is responsible for numerous industrial accidents, including chemical leaks, fires, and explosions.
- Environmental protection: Prevents water and soil pollution caused by spills. Corrosion generates significant greenhouse gas emissions, contributing to climate change.
- Enhanced operational Efficiency: Reduces disruptions in port operations and the supply chain.
- Extended pipeline lifespan: Allows pipelines to operate longer before replacement is needed. Implementing effective corrosion prevention strategies can significantly extend the lifespan of dock pipelines, reducing maintenance and replacement costs.
Conclusions
Preventing corrosion in dock pipelines is not just a technical challenge but a crucial responsibility for the safety, efficiency, and sustainability of energy infrastructure.
By implementing comprehensive strategies that combine the use of corrosion-resistant materials, protective marine coatings, rigorous pipeline maintenance, and continuous monitoring with scheduled periodic inspections, port, and energy companies can protect their assets. They can also reduce operating costs and ensure the safe and reliable operation of their facilities.
Ensure the integrity of your marine infrastructure now!
References
- Prometal: “Types of Corrosion in Metal Pipes and Their Mitigation: Complete Guide”
- Cenosco: “Pipe Corrosion: Prevention and Management