The aerospace industry has always evolved hand in hand with technological developments, which has allowed it to improve its competitiveness and research capacity, while acting as a promoter of advances in other disciplines. The high growth and investment in R&D is leading to the emergence of digital capabilities in fields such as materials composition, fuels, communications or security, whose implementation and adaptation to space projects will have a full impact in the coming years.
The aerospace industry is a field where safety, durability and reliability are critical. Corrosion is one of the most critical challenges facing this sector, as it can compromise the structural integrity of aircraft and components, which could have catastrophic consequences. To address this problem, a number of technological advances have been developed in corrosion protection in the aerospace industry. In this article, we will explore some of these developments and how they are improving corrosion resistance in the aerospace industry.
Corrosion in the aerospace industry
In this industry there are various topics of interest for the development of research, innovation and technological support projects; But an issue that is pressing for this industry is when metallic materials stop being functional and its manifestation is electrochemical degradation or oxidation at high temperatures due to the operating conditions of the aircraft.
Corrosion control in the aeronautical industry is an issue that has always been important, but it is increasingly a function of the aging of the aircraft fleet. Corrosion can lead to aircraft deterioration (Figure 1), aircraft unavailability and in extreme cases to catastrophic failure.
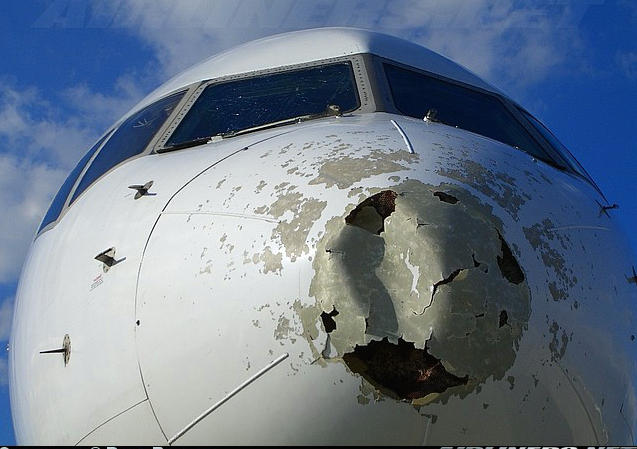
One of the challenges for space exploration is that equipment must withstand extreme conditions of heat, rocket exhaust and extreme cold in space. Surprisingly, one of the most destructive factors is the corrosive effect of salt-laden ocean fog that causes corrosion of launch structures and equipment at the Kennedy Space Center.
What are the types of aircraft corrosion?
It can be divided into several different categories depending on the cause, its location, and its appearance. Different types of aircraft corrosion to consider include:
Surface corrosion: The most common type in aircraft, it occurs when the metal on the surface of an aircraft rusts, such as when paint wears off. Typically, it can be recognized by the roughness, pitting or etching of the metal surface and the presence of grayish-white powder deposits on the aluminum.
However, another type called filiform corrosion can look like tiny worms beneath the paint surface, eventually causing bubbles and cracks.
Corrosion of dissimilar metals: Appears when dissimilar metal parts come into contact with each other in the presence of a conductor. This type of electrochemical corrosion can cause extensive pitting damage. It often occurs out of sight, making it particularly dangerous.
This is a very expensive and dangerous type of wear that can go unnoticed for long periods of time. In fact, most of the time the only way to determine if this type of corrosion is occurring is to disassemble and inspect the various parts.
Intergranular corrosion: Affects the grain boundaries of an alloy, so it is often related to a lack of uniformity in the alloy structure. Although it often exists without surface evidence, over time it can cause the surface metal to lift and flake. Extruded components may be particularly susceptible.
This form can occur when the crystallite boundaries found in the materials make them more susceptible to corrosion than their internal parts. Fortunately, most grains are not affected by the process because this type affects only small sections of the plane.
Alloys that have been improperly treated, but subsequently exposed to a corrosive environment, are particularly vulnerable and lack of uniformity in the alloy structure is one of the main reasons why this occurs.
Stress corrosion: As the name suggests, it develops when parts such as engine landing gear and crankshafts are subjected to sustained tensile stress in corrosive environments, sometimes leading to cracks and failures.
It can be caused by certain environments, including seawater and salt solutions which can crack certain steels and alloys, humid air which can corrode magnesium alloys, and titanium alloys which can corrode due to methyl alcohol solutions and hydrochloric acid.
Protective coatings, shot peening of a metal surface, and stress relieving heat treatments can be used to reduce the chances of this type of corrosion occurring.
Friction corrosion: It is caused by the slight relative movement of two mating surfaces on an aircraft. Characterized by significant pitting and fine debris, this type of aircraft corrosion is greatly accelerated when water vapor is present.
Technology trends
- Innovation in alloys and materials: The development of new metal alloys will continue at a rapid pace. The demand for stronger, lighter and more heat resistant materials will drive innovation in this field. Aluminum alloys, lithium, titanium and polymer plastics will continue to be areas of intense research and development.
- Composite materials: are a class of materials manufactured by combining two or more different components to obtain properties superior to those of the individual materials. Carbon fiber, glass fiber and epoxy resins are the most used compounds in this sector. They are interlocked and bonded in layers to form a strong, lightweight structure, optimized to withstand the rigorous conditions that aircraft are subjected to during flight.
- Advances in additive manufacturing: Also known as 3D printing, it is revolutionizing the way aerospace components are manufactured. This technology allows for unprecedented design flexibility and can reduce manufacturing costs and lead times. The future is likely to see greater adoption of additive manufacturing in the aerospace industry, as well as advances in 3D printing techniques for metals and composites.
- Automation and robotics: They will play an increasingly important role in the metalworking industry because the adoption of robots and automated systems can increase efficiency, improve precision and reduce costs in the manufacturing of aerospace components. This includes not only the automation of production processes, but also the adoption of automated inspection technologies to improve quality control.
- Sustainability and energy efficiency: With the increasing focus on sustainability and energy efficiency, it is likely that there will be greater emphasis on ‘green’ metalworking production, this may include the use of recycled materials, the optimization of production processes to reduce energy consumption and minimize waste.
- Artificial intelligence and machine learning: AI and machine learning will play an increasingly important role in the metalworking industry and can be used to optimize production, improve product quality and accelerate the development of new materials and alloys. Additionally, machine learning can also help predict and prevent failures of aerospace components, thereby improving safety and reliability.
Conclusion
In conclusion, the aerospace industry is driving technological development, not only to improve the safety and durability of aircraft, but also to influence other fields. Advances in corrosion protection are just one part of a broader narrative of constant innovation in this critical sector.