Table of Contents
- The role of drones in corrosion inspection
- Benefits of Drones and Robotics in the detection of corrosion in different environments
- Limitations of Drones and Robotics in Corrosion Detection
- Examples of application of Drones and Robotics in the detection of corrosion
- Job opportunities and training in corrosion inspections with Drones and Robotics
- Challenges and Ethical Considerations in Corrosion Inspection with Drones and Robotics
- Conclusions
- Bibliographic references
Corrosion is a recurring problem in the oil industry, with the potential to have serious consequences if not properly addressed. However, in recent years, advances in technology have provided promising solutions to combat this problem.
Drones and robotics have emerged as fundamental tools in corrosion inspection, allowing constant monitoring and early detection of anomalies.
This phenomenon can seriously affect the integrity of the structures and pipelines used in the extraction, transportation and refining of oil, which can result in dangerous leaks and costly interruptions in production.
Traditionally, inspection is performed by human personnel, which carries significant security risks and limitations in terms of scope and efficiency. However, in recent years, advances in drone and robotics technology have provided promising new solutions to more effectively address this challenge.
In this article, a summary is made about corrosion in the oil industry, about the application and benefits that new technologies provide to mitigate it, such as the integration of drones and robotics in corrosion inspection as a promising solution to overcome the limitations of the traditional inspection methodologies.
Corrosion in the oil industry
Corrosion is a natural process that affects metal components used in the oil industry. Infrastructures, piping, and equipment are exposed to aggressive environments that accelerate deterioration and generate potential risks such as leaks, structural failures, and decreased operating efficiency. Addressing corrosion effectively is important to avoid costly downtime and ensure the safety of workers and the environment.
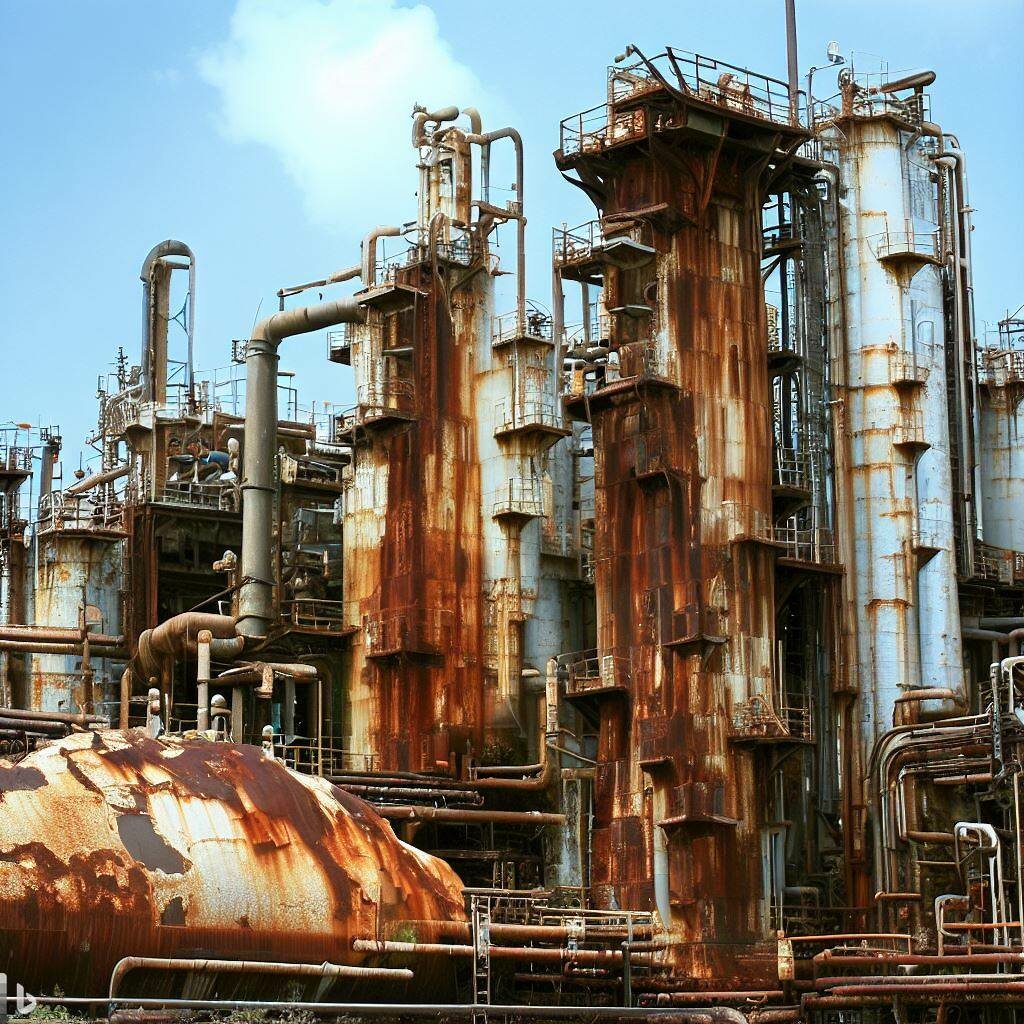
Constant exposure to corrosive environments, such as contact with aggressive chemicals, the presence of acid gases and humidity, can lead to degradation and deterioration of the metallic materials used in this industry. The phenomenon of corrosion is one of the main causes of failures in oil facilities and half of these failures are linked to corrosion due to the presence of gases such as CO2 and H2yes1,2; which dissolve in the aqueous phase of the fluid, producing different forms of corrosion.
Corrosion inside storage tanks depends on the nature of the stored product and on roofs it is mainly due to the combination of sulphurous gases, humidity and oxygen present inside the equipment 3 . The types and the degree of corrosion of the refining units have a great relationship with the material and the quality of the crude oil 4 .
Corrosion in seawater depends on specific factors such as water temperature, salinity, chlorinity, water depth and current speed, as well as the different areas to which they are exposed 5 .
The role of drones in corrosion inspection
Drones have emerged as a valuable tool in corrosion inspections in the oil industry. Equipped with high-resolution cameras and specialized sensors, these devices can fly over large, hard-to-reach areas to capture detailed images of structures and equipment; which are analyzed by artificial intelligence algorithms and automated systems to detect anomalies and areas prone to corrosion. Drones allow constant monitoring and detection of failures and the implementation of corrective measures.
Benefits of Drones and Robotics in the detection of corrosion in different environments
1. Confined spaces
The adoption of drones and robotics in corrosion inspections offers a number of significant benefits. It allows non-destructive inspections to be carried out, avoiding interruptions in production and reducing risks for workers. Additionally, the constant monitoring provided allows discontinuities to be detected before they become failures, helping to prevent further damage and minimize associated costs.
Integration of collected data with asset management and predictive maintenance systems facilitates more efficient and data-driven planning of maintenance activities, extending equipment life and reducing costs associated with unscheduled downtime. One of the main advantages of drones is their ability to access areas that are dangerous or inaccessible to human operators.
Confined spaces, such as storage tanks, pipelines, or industrial structures, often present hazardous conditions, such as toxic gases, high temperatures, lack of oxygen, or narrow passages. By using drones, the need for operators to physically enter these dangerous spaces is eliminated, drastically reducing the risk of accidents and injuries.
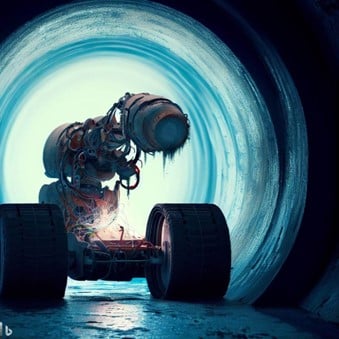
2. Submarine spaces in the detection of corrosion
Pipes submerged in seawater are exposed to aggressive environmental conditions that increase the risk of corrosion. Seawater, with its high salinity and the presence of chloride ions, together with marine currents and biological activity, creates an environment conducive to the deterioration of metal pipes.
The application of underwater drones in the detection of corrosion of pipelines submerged in seawater has opened up new possibilities for the marine and oil industry. These innovative tools allow detailed and precise inspections in subsea environments, facilitating the detection of corrosion problems to prevent and control possible failures in the pipelines.
Previously, the inspection of subsea pipelines was carried out by traditional methods, such as the use of divers or Remotely Operated Vehicles (ROVs). These methods are expensive, time consuming, and posed risks to divers and ROV technical personnel.
The advent of underwater drones has revolutionized this process, allowing a more efficient, safe and accurate inspection of pipelines submerged in seawater. These drones, also known as AUVs (Autonomous Underwater Vehicles), are specifically designed to operate underwater and feature advanced navigation systems, high-resolution cameras, and specialized sensors.
3. Airspaces with difficult access
In the oil industry, there are various structures that are exposed to challenging weather conditions, such as drilling rigs, production rigs, and elevated pipe and tank systems. These structures are critical to the extraction, processing, storage and transportation of oil, and their integrity and important to ensure safe and continuous operations.
Unmanned aerial systems provide NDT experts from all industry sectors with a unique aerial perspective. This methodology enables easy access to remote or inaccessible areas without compromising the safety of the inspector.
Previously, the inspection of these structures was carried out using traditional methods that involved risks and were costly in terms of time and resources. The use of scaffolding, cranes or personnel at height presented obvious hazards, while manual inspection methods did not always provide a thorough and accurate assessment of corrosion in all inspection areas.
Currently, the use of aerial drones in the oil industry allows access to areas that are difficult to access quickly and safely. These devices can fly close to structures and capture detailed images of exposed surfaces. High-resolution cameras provide a clear and precise view of areas affected by corrosion, erosion or other types of damage.
Additionally, some aerial drones are equipped with thermal imaging technology, allowing them to detect discontinuities that are not visible to the naked eye. This is especially useful in detecting corrosion under protective coatings or in areas where corrosion is in its early stages and not readily noticeable.
Limitations of Drones and Robotics in Corrosion Detection
Despite the significant benefits that drones and robotics offer in corrosion inspections, there are also some important limitations to consider. Here are some of the common limitations of these technologies:
Limited coverage: Although drones can cover large areas and provide detailed images, there are still limitations in terms of flight range and range. Drones have limited flight times and may require frequent battery recharges, which can affect efficiency and inspection coverage.
Adverse Weather Conditions: Adverse weather conditions, such as high winds, heavy rain, or fog, can affect the operation of drones and limit their ability to safely and effectively conduct inspections. These conditions can reduce the quality of captured images and make it difficult to accurately detect corrosion.
Access to hard-to-reach areas: Although drones and robots on land or underwater can access many hard-to-reach areas, there are still limitations in certain complex environments. Some confined areas, such as tight spaces or small diameter pipes, may be inaccessible to conventional robotic tools.
Data interpretation: Interpretation of data collected by drones and robots can be challenging. While these technologies can capture images and collect accurate data, the analysis and interpretation of this data often requires human experts to make informed decisions.
Costs: The implementation of drones and robotics in corrosion inspections implies significant investments in the acquisition of equipment, personnel training and maintenance. These costs can be expensive for some businesses, especially smaller ones or those with limited budgets.
It is important to be aware of these limitations and consider how to address them when implementing drones and robotics in corrosion inspections. While these technologies offer numerous benefits, it is critical to understand their limitations and work on solutions to maximize their effectiveness and overcome technical and operational challenges that may arise.
Examples of application of Drones and Robotics in the detection of corrosion
Various companies 6 leaders in the oil industry have successfully adopted the use of drones and robotics in corrosion inspections, obtaining positive results. For example, there are companies that have implemented a fleet of drones equipped with thermal imaging cameras to monitor their oil structures. Thanks to this technology, they were able to detect hot spots that indicated areas of incipient corrosion, allowing them to intervene quickly and prevent further damage.
Another example is incorporating underwater robots to inspect your underwater pipelines . These robots, equipped with magnetic and ultrasonic sensors, detected corroded areas and precisely measured the thickness of the metal. As a result, the company was able to schedule preventative maintenance and avoid costly repairs.
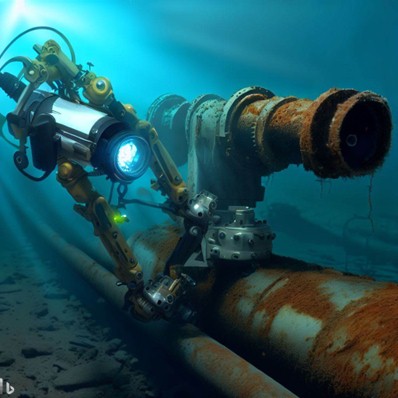
These cases demonstrate how companies are harnessing the potential of drones and robotics to improve corrosion detection and optimize their operations.
Job opportunities and training in corrosion inspections with Drones and Robotics
The advancement of drone and robot technology in corrosion inspections creates new employment and training opportunities. Corrosion inspectors can be trained in the use of this equipment, expanding their job prospects. In addition, the implementation of these technologies promotes the development of new companies specialized in drones and robotics, generating additional jobs and contributing to economic growth.
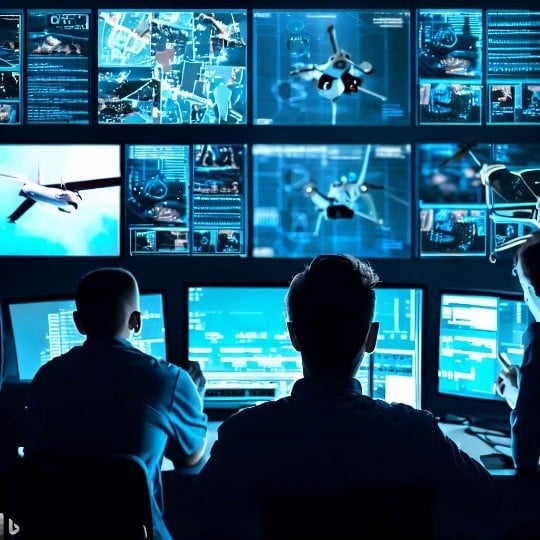
Challenges and Ethical Considerations in Corrosion Inspection with Drones and Robotics
Although drones and robots offer numerous advantages, there are challenges and ethical considerations to take into account. It is necessary to establish clear regulations and safety standards to guarantee a responsible use of these technologies in corrosion inspections. Furthermore, it is crucial to ensure that the algorithms used are unbiased and avoid algorithmic bias, guaranteeing ethical and accurate results.
Conclusions
These technologies allow constant monitoring and early detection of anomalies, facilitating the implementation of preventive measures and reducing the risks associated with corrosion. They offer a detailed view of structures and equipment, while ground and underwater robots can access hard-to-reach areas. This improves the efficiency of inspections, reduces costs and extends the useful life of assets.
Leading companies in the oil industry have adopted these technologies with successful results, managing to detect and address corrosion problems in a timely manner. As technology continues to advance, drones and robotics are expected to play an even larger role in corrosion detection and prevention, improving the safety and efficiency of the oil industry.
Ultimately, the era of robotics and drone-powered corrosion hunters is transforming the way we approach this persistent challenge. Thanks to these technologies, the oil industry is prepared to keep its assets in optimal conditions, prevent costly interruptions and promote a safe and efficient operation.
Bibliographic references
1. Kermany MB, D. Harrop. SPE Prod Facil, 1996; 11: 186-190.
2. Ikeda A., Ueda M., Mukai S. Influence of Environmental Factors on Corrosion in CO 2 Source Well. In: Advances in CO 2 Corrosion, ed. Houston, TX (USA): NACE International, 1986, (Vol. II): 1-22.
3. Groysman, A. (2014); Corrosion in Systems for Storage and Transportation of Petroleum Products and Biofuels: Identification, Monitoring and Solutions. Chap. 1, p. 1-21. 1st ed.
4. Peiyang Chemical Equipment Co., Ltd. (PCC) (2017). Consulted on 06-06-2023 from:
5. S. Price and R. Figueira, “Corrosion Protection Systems and Fatigue Corrosion in Offshore Wind Structures: Current Status and Future Perspectives”, Coatings. Vol. 7, No. 2, p. 25 (2017).
6. Murray, J. (2020); Seven major oil and gas firms using drones in their operations; NS Energy. Accessed on date of: https://www.nsenergybusiness.com/news/oil-and-gas-drones/