Table of Contents
- Properties of ferrous and non-ferrous metals
- Corrosion in ferrous metals
- Corrosion in non-ferrous metals
- Examples of ferrous and non-ferrous metals
- Corrosion differences: ferrous vs. non-ferrous metals
- Which metals are more resistant to saline environments?
- Conclusions
- References
- (FAQs) on corrosion in ferrous and non-ferrous metals
Corrosion, although often underestimated, remains one of the most critical silent enemies to operational integrity in strategic industrial sectors. Every rust spot represents a potential threat to the reliability of multi-billion dollar assets, from refineries to offshore platforms.
From structural failures on offshore platforms to economic losses in refineries and marine terminals, the progressive deterioration of metallic materials compromises the safety, reliability and efficiency of assets. Understanding the nature of this degradation is not only a technical issue, but a strategic necessity for industrial asset management.
In this context, differentiating between ferrous and non-ferrous alloys is particularly important. On the other hand, both groups have different behaviors in corrosive environments and, particularly in marine environments, differentiating between ferrous and non-ferrous metals becomes especially relevant. Both groups have different behaviors in corrosive environments and, in particular, in marine environments, which directly influences design, maintenance and material selection decisions.
For professionals in Oil & Gas, wind energy, petrochemical or offshore production, knowing these differences allows them to anticipate risks, optimize life cycles and improve operational sustainability. This article provides a rigorous comparative analysis with technical, regulatory and applied basis.
Properties of ferrous and non-ferrous metals
The fundamental characteristics of ferrous and non-ferrous metals define not only their mechanical performance but also their behavior in corrosive environments. Structurally, ferrous metals such as carbon steel and cast iron contain a significant amount of iron, which makes them magnetic and denser. Their microstructure, if not properly treated or protected, tends to promote oxide formation when exposed to moisture and oxygen.
In contrast, non-ferrous metals like aluminum, copper, and titanium contain little to no iron. This makes them non-magnetic and generally lighter, offering a better strength-to-weight ratio, especially beneficial in offshore and aerospace applications.
When facing aggressive environments, their response diverges significantly. Ferrous metals are prone to rapid oxidation, while non-ferrous metals often develop passive oxide layers, such as alumina or copper patina, that naturally shield the material from further degradation. This self-protective behavior, particularly in alloys like anodized aluminum, provides key advantages in durability and reduced maintenance needs. In offshore energy projects, anodized aluminum is often selected for structural elements or paneling due to its enhanced corrosion resistance and low weight.
Comparative analysis of ferrous and non-ferrous netals
Choosing between ferrous and non-ferrous metals requires a multi-criteria evaluation of technical and economic factors, particularly in industries where corrosion severely impacts asset reliability.
Below is a general comparison:
Parameter | Ferrous metals | Non-ferrous metals |
Cost | Generally lower | Higher, especially in high-performance alloys |
Corrosion resistance | Low without surface treatment | Often high, even without coatings |
Weight | Higher density | Lower weight: ideal for structural optimization |
Maintenance | Requires frequent protection and monitoring | Less frequent and more predictable maintenance |
Conductivity | Low (except some stainless steels) | High (notably copper and its alloys) |
Applications | Piping, pressure vessels, structural supports | Aerospace, heat exchangers, chemical plants |
In the energy sector, for instance, ferrous metals remain widely used for onshore pipelines due to their mechanical strength and cost-effectiveness. However, in marine or acidic environments, non-ferrous options like titanium or anodized aluminum offer significantly longer service lives, minimizing interventions and enhancing operational continuity.
This brief video (1 min 55 s) by Patriot Coin Rings explains the difference between ferrous and non-ferrous metals in a clear, concise way—covering composition, properties, and typical applications:

Corrosion in ferrous metals
Ferrous metals are well known for their vulnerability to corrosion, a persistent issue that continues to cause structural failures across industrial facilities. Common mechanisms include direct oxidation, pitting corrosion, particularly in chloride-rich environments, and galvanic corrosion, which occurs when dissimilar metals are electrically connected in a conductive medium like seawater.
Salinity, temperature, and humidity significantly accelerate corrosion rates, especially in coastal and offshore environments. High concentrations of dissolved salts, combined with thermal cycling and condensation, create highly aggressive conditions for carbon steel and other iron-based alloys.
Iron-based materials undergo accelerated oxidation without natural passivation, meaning they fail to develop stable, self-protective oxide layers. For this reason, protective strategies such as coatings, inhibitors, or cathodic protection systems are essential to extend their service life, particularly in pipelines, tanks, and offshore structures where cathodic protection is widely applied.
Such corrosive deterioration is frequently observed in assets like storage tanks, marine terminal infrastructure, and pipeline systems, particularly those operating in harsh, high salinity environments. The ISO 9223:2012 standard offers a technical framework for evaluating environmental corrosivity and anticipating degradation rates in ferrous materials.
Corrosion in non-ferrous metals
Non-ferrous metals exhibit a different response to corrosion due to their ability to form protective oxide layers naturally. However, they are not entirely immune. Forms of attack such as intergranular corrosion, pitting, and stress corrosion cracking may still occur, depending on the alloy composition, microstructure, and operational environment.
For instance, aluminum develops a thin layer of alumina that acts as a barrier, but this layer can be compromised in chloride-rich environments like marine atmospheres. Copper and its alloys form a stable patina that protects the surface, although selective leaching may occur in the presence of ammonia or certain acids. Titanium, widely used in chemical plants, is remarkably resistant even in highly oxidizing or chlorinated environments.
Non-ferrous metals can better withstand marine or acidic environments, an advantage engineers have long relied upon, particularly when properly selected and supported by appropriate operational controls.
Typical applications include offshore structures made from aluminum, HVAC piping in copper, and reactors or heat exchangers in titanium. For more in-depth analysis, the Journal of Corrosion Science and Engineering by the American Chemical Society (ACS) offers valuable insights and peer-reviewed research on these mechanisms.
Examples of ferrous and non-ferrous metals
In the context of engineering and industrial applications, understanding the typical ferrous and non-ferrous metals is essential for selecting materials aligned with performance and durability requirements.
Among ferrous metals, carbon steel remains the most widely used due to its strength and affordability, particularly in pipelines, tanks, and structural frames. Cast iron, with its excellent vibration damping properties, is common in machinery bases and valve bodies. Martensitic stainless steels, on the other hand, offer moderate corrosion resistance and are often employed in turbine components and high-wear applications.
For non-ferrous options, aluminum is favored in offshore and aerospace sectors for its light weight and corrosion resistance. Anodized aluminum components are common in subsea modules, riser systems, and platform enclosures. Copper plays a key role in electrical systems and HVAC piping due to its high conductivity and antimicrobial properties. Titanium, known for its exceptional chemical resistance, is used in heat exchangers and pressure vessels, while nickel-based alloys serve critical roles in high-temperature environments, such as gas turbines and chemical reactors.
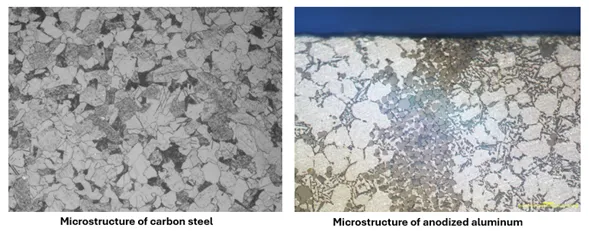
Corrosion differences: ferrous vs. non-ferrous metals
The main difference in corrosion behavior between ferrous and non-ferrous metals lies in their electrochemical response and their ability to form protective barriers.
Alloys containing iron are particularly vulnerable to oxidation when exposed to moisture and oxygen. Without adequate protection, their degradation can occur rapidly, evidenced by the formation of rust and pitting. Their service life in aggressive environments is compromised unless coatings, cathodic protection, or specific alloying strategies are applied.
In contrast, what many engineers value in non-ferrous metals is their self-protective ability: a thin oxide film that acts as a natural shield against corrosion. This advantage is critical in harsh marine environments. Aluminum, for example, forms alumina; copper develops a stable patina. These layers significantly enhance their durability in marine or acidic conditions.
However, no group is immune. Proper design, the use of targeted protective coatings, and predictive maintenance management remain essential to extend the service life of industrial assets.
Which metals are more resistant to saline environments?
When it comes to corrosion resistance in offshore or marine environments, not all metals perform equally. Salinity, combined with high humidity and fluctuating temperatures, creates one of the most aggressive corrosion scenarios in industrial operations.
Non-ferrous metals, particularly titanium, aluminum, and nickel-based alloys, are far better suited to these conditions than untreated ferrous materials. Their ability to form stable oxide layers on the surface provides a natural barrier that reduces the need for continuous maintenance. For instance, titanium is practically immune to chloride-induced corrosion, making it ideal for offshore platforms and desalination plants.
In contrast, ferrous metals like carbon steel corrode rapidly without external protection, such as coatings or cathodic protection systems, which are often mandatory in subsea and marine infrastructure to mitigate galvanic effects. Alloying elements (e.g., chromium in stainless steel), metallurgical treatments, and protective linings are necessary to enhance their performance in saline environments.
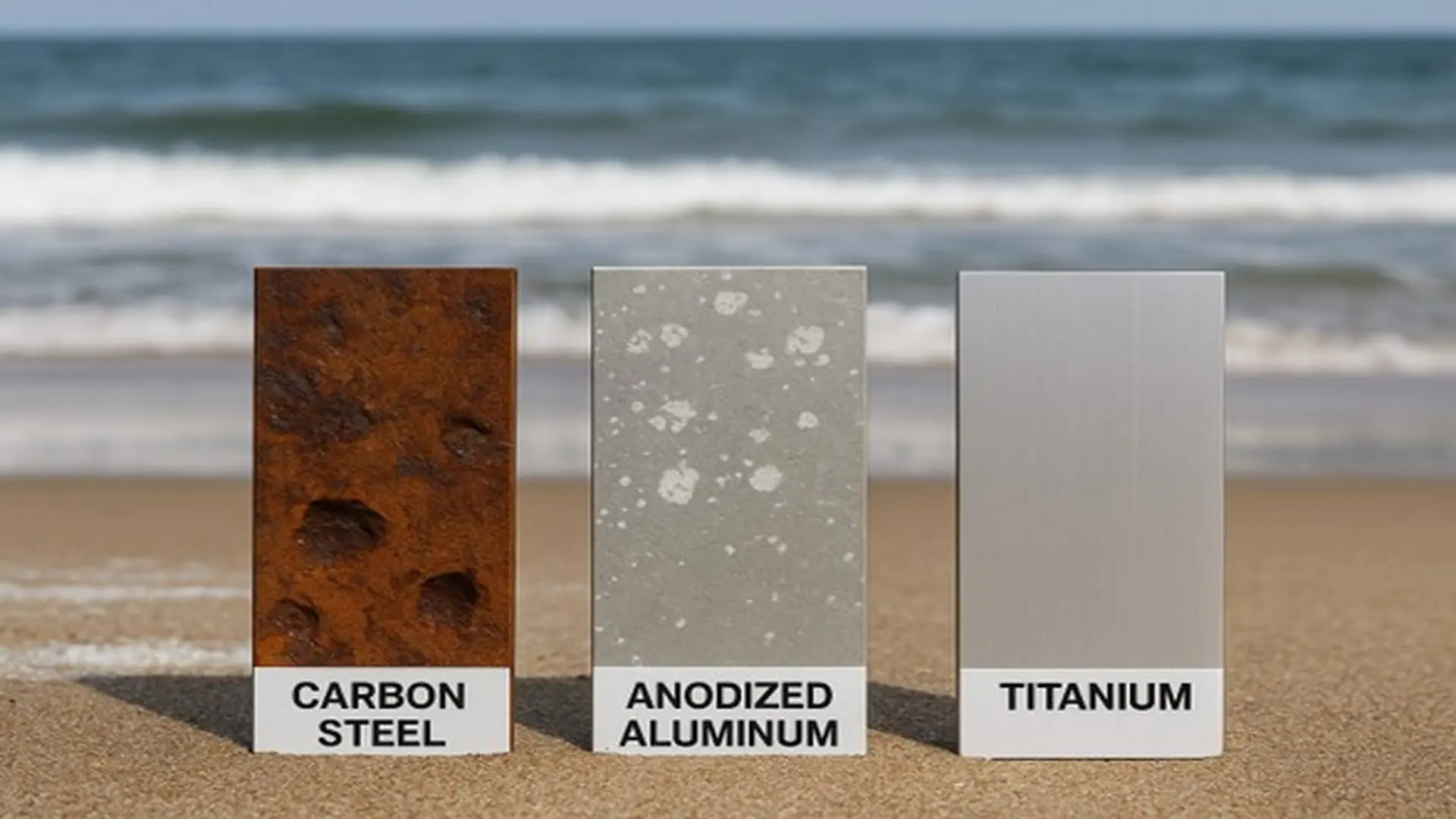
Conclusions
The corrosive behavior of ferrous and non-ferrous metals is not a minor design variable—it is a central consideration for anyone involved in the engineering, maintenance, or management of industrial assets. Selecting the right material for each operating environment can determine the success or failure of long-term operations.
Understanding the mechanisms of corrosion, the role of passivation, and the impact of environmental conditions empowers engineers and asset managers to make smarter decisions. In high-stakes sectors like Oil & Gas, offshore energy, and petrochemicals, this knowledge translates directly into cost savings, enhanced safety, and longer asset life.
While corrosion can never be fully eliminated, it can be anticipated and managed with the right strategy. Solutions like cathodic protection, predictive maintenance, and proper material selection allow engineers to protect infrastructure, safeguarding lives, investments, and the sustainability of entire operations.
To explore effective strategies for corrosion control, monitoring, and material selection across various industrial settings, we invite you to read Inspenet’s article: “Challenges in the Protection of Materials from Corrosion”, which dives into applied solutions for sectors such as Oil & Gas, petrochemicals, and offshore operations.
References
- ISO 9223:2012 – Corrosion of metals and alloys — Corrosivity of atmospheres
- https://www.sciencedirect.com/science/article/pii/S0010938X24000252
- https://pubs.acs.org/doi/10.1021/acscatal.3c00000
- AWS D3.6M:2017 – Underwater Welding
- NACE International – Corrosion Basics: An Introduction
- IUPAC – Standard Definitions for Metal Classification
- ASTM G1 – Standard Practice for Preparing and Evaluating Corrosion Test Specimens
(FAQs) on corrosion in ferrous and non-ferrous metals
What differentiates corrosion in ferrous and non-ferrous metals?
Ferrous metals contain iron, which makes them more susceptible to oxidation, especially in humid or saline conditions. Non-ferrous metals, like aluminum and copper, develop oxide layers that inhibit corrosion.
Which metals are more resistant to saltwater environments?
Non-ferrous metals such as titanium, aluminum, and certain copper alloys outperform untreated ferrous metals in marine and acidic environments, offering better longevity and lower maintenance requirements.
Can corrosion be completely prevented?
Not entirely, but it can be controlled through material selection, protective coatings, cathodic protection, and predictive maintenance protocols.
What standards guide industrial corrosion control?
Core standards include ISO 9223, ASTM G1, and comprehensive guidelines by NACE International, all of which are widely adopted in energy, petrochemical, and offshore industries.